- お役立ち記事
- Achieving Automation in Manufacturing with PLC (Programmable Logic Controller) Implementation
Achieving Automation in Manufacturing with PLC (Programmable Logic Controller) Implementation
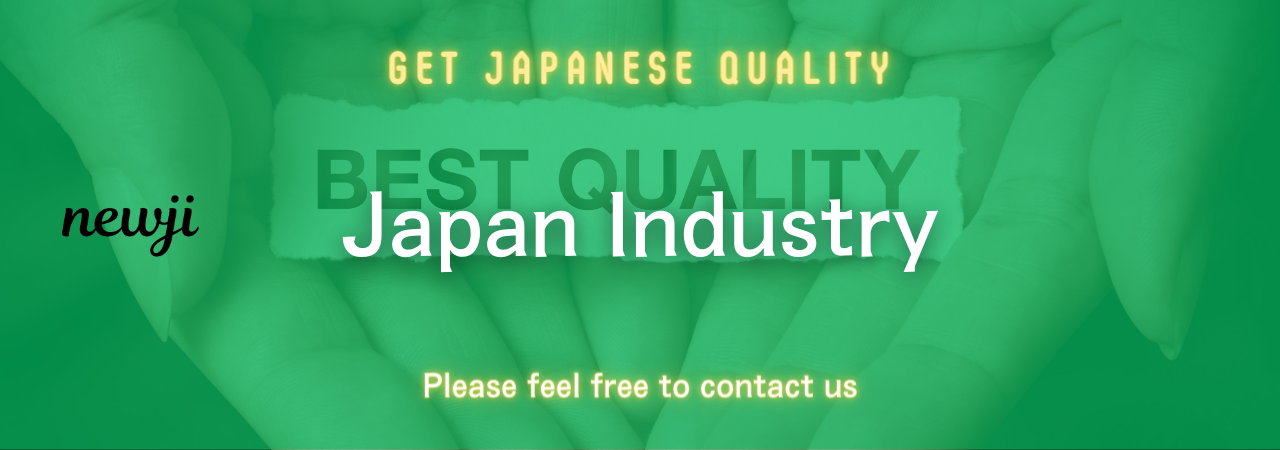
In today’s fast-paced world, efficiency in manufacturing processes has become more critical than ever. One key player in achieving this efficiency is the Programmable Logic Controller (PLC).
PLCs have revolutionized the manufacturing industry by automating operations that were once carried out manually. This article will dive into how PLCs are used in manufacturing to achieve automation and the many benefits they bring to the table.
目次
Understanding Programmable Logic Controllers
PLCs, or Programmable Logic Controllers, are industrial digital computers designed to manage manufacturing processes.
They are used to control machinery, assembly lines, and other equipment through automated systems. Unlike ordinary computers, PLCs are built to withstand the harsh conditions often found in industrial environments.
The History of PLCs
PLCs were first developed in the late 1960s to replace relay logic systems in the automotive industry.
Traditional relay systems were bulky, complex, and required frequent maintenance.
PLCs offered a more flexible, reliable, and space-saving solution, and it didn’t take long for other industries to take notice. Today, PLCs are an integral part of modern manufacturing processes across multiple sectors.
The Role of PLCs in Automation
Automation in manufacturing means using control systems, like PLCs, to operate machinery, processes, or even entire factories with minimal human intervention.
Here are several ways in which PLCs play a crucial role in automation:
Streamlining Processes
By automating repetitive tasks, PLCs help streamline manufacturing processes.
For example, in an automotive assembly line, a PLC can manage the timing and precise movement of robotic arms to assemble parts.
This increases productivity and ensures that each part is assembled with consistent quality.
Ensuring Safety
PLCs also contribute significantly to workplace safety.
They can be programmed to shut down machinery quickly if an error or malfunction is detected.
This minimizes the risk of accidents and injuries, protecting workers and reducing downtime.
Improving Quality Control
Quality control is another area where PLCs shine.
They can be programmed to monitor production processes continuously. Any deviations from set parameters trigger alerts, ensuring products meet the required standards.
This leads to fewer defects and higher customer satisfaction.
Key Components of a PLC System
To understand how PLCs achieve automation, it’s essential to know their key components:
Central Processing Unit (CPU)
The CPU is the brain of the PLC.
It processes instructions and performs decision-making tasks based on the program loaded into it.
Think of it as the conductor of an orchestra, directing all the components to work in harmony.
Input/Output (I/O) Modules
I/O modules connect the PLC to machinery and sensors.
Input modules receive signals from sensors, such as temperature or pressure sensors, and feed them to the CPU.
Output modules send commands from the CPU to control devices like motors or actuators.
Power Supply
A reliable power supply is crucial for PLC operation.
It provides the necessary electrical power to run the CPU and I/O modules.
How PLCs Work in a Manufacturing Plant
Let’s see how a PLC functions in a typical manufacturing setup from start to finish:
Programming the PLC
First, the engineer programs the PLC using specialized software.
The program outlines the sequence of operations the machinery should follow. Once the program is loaded into the CPU, the PLC is ready to automate tasks.
Receiving Input Signals
Next, the sensors on the production line collect data and send signals to the PLC’s input modules.
The CPU processes these signals and makes decisions based on the pre-loaded program.
Executing Commands
After processing the input signals, the CPU sends commands through the output modules to control devices.
This action drives motors, controls valves, and more, orchestrating the entire manufacturing process seamlessly.
Challenges and Solutions in Implementing PLCs
Although PLCs are incredibly beneficial, implementing them can pose some challenges.
Initial Costs
The initial investment in PLCs can be substantial, especially for small to medium-sized enterprises.
However, the long-term benefits, such as increased productivity and reduced labor costs, often outweigh the initial expenditure.
Complexity in Programming
Programming PLCs requires specialized skills.
Fortunately, many training programs are available to help engineers learn to program and maintain PLC systems effectively.
Integration with Existing Systems
Integrating PLCs with existing systems can be complex.
However, modern PLCs are designed with versatile communication capabilities, making integration easier than in the past.
The Future of PLCs in Manufacturing
The future looks bright for PLC technology.
With advancements in artificial intelligence and machine learning, PLCs are becoming even more powerful. Smart PLCs can now analyze data in real time, making more accurate decisions and further optimizing manufacturing processes.
IoT and Connectivity
The Internet of Things (IoT) is another frontier where PLCs are making strides.
Connected PLCs can communicate over the internet, enabling remote monitoring and control of manufacturing processes.
Sustainability
Sustainability is becoming increasingly important in modern manufacturing.
PLCs can be programmed to optimize energy use, reducing the carbon footprint of manufacturing plants.
In conclusion, PLCs have become indispensable tools in modern manufacturing.
They streamline processes, ensure safety, improve quality control, and contribute to sustainability efforts.
As technology continues to advance, the role of PLCs in achieving automation will only become more critical.
Whether you’re an industry veteran or just starting, understanding PLCs and their capabilities is essential to staying competitive in the ever-evolving manufacturing landscape.
資料ダウンロード
QCD調達購買管理クラウド「newji」は、調達購買部門で必要なQCD管理全てを備えた、現場特化型兼クラウド型の今世紀最高の購買管理システムとなります。
ユーザー登録
調達購買業務の効率化だけでなく、システムを導入することで、コスト削減や製品・資材のステータス可視化のほか、属人化していた購買情報の共有化による内部不正防止や統制にも役立ちます。
NEWJI DX
製造業に特化したデジタルトランスフォーメーション(DX)の実現を目指す請負開発型のコンサルティングサービスです。AI、iPaaS、および先端の技術を駆使して、製造プロセスの効率化、業務効率化、チームワーク強化、コスト削減、品質向上を実現します。このサービスは、製造業の課題を深く理解し、それに対する最適なデジタルソリューションを提供することで、企業が持続的な成長とイノベーションを達成できるようサポートします。
オンライン講座
製造業、主に購買・調達部門にお勤めの方々に向けた情報を配信しております。
新任の方やベテランの方、管理職を対象とした幅広いコンテンツをご用意しております。
お問い合わせ
コストダウンが利益に直結する術だと理解していても、なかなか前に進めることができない状況。そんな時は、newjiのコストダウン自動化機能で大きく利益貢献しよう!
(Β版非公開)