- お役立ち記事
- Balancing Cost and Performance in Manufacturing with OEM DC Motors
Balancing Cost and Performance in Manufacturing with OEM DC Motors
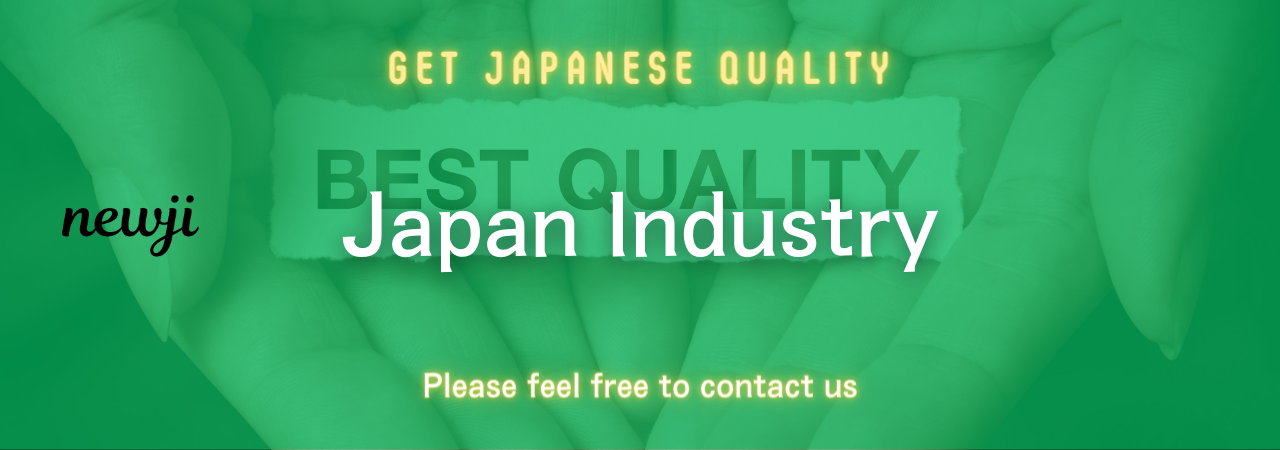
In the ever-evolving landscape of manufacturing, finding the right balance between cost and performance is key to ensuring the longevity and efficiency of your operations. One crucial component that notably affects this balance is the choice of OEM DC motors. These motors, known for their reliability and versatility, are found in a myriad of industrial applications. But how do you strike the perfect equilibrium between cost and performance when integrating OEM DC motors into your manufacturing processes? Let’s delve into the essentials.
目次
Understanding OEM DC Motors
OEM, or Original Equipment Manufacturer, DC motors are specifically designed and built to meet the unique specifications of the equipment they will power. Unlike off-the-shelf motors, OEM DC motors are tailored to ensure optimal performance for particular applications. They are often incorporated into machinery directly by the equipment manufacturer, which helps in maintaining high efficiency levels and adherence to specific requirements.
Key Characteristics of OEM DC Motors
The primary appeal of OEM DC motors lies in their customization. When a motor is designed to match the exact needs of a machine, it leads to enhanced efficiency, reduced downtime, and extended lifespan of the motor. These motors often come with specific features like optimized torque, precise speed control, and the capability to withstand rigorous operational demands.
Customization and Performance
Customization plays a pivotal role in performance. An OEM DC motor created for a particular application will always outperform a standard motor. This is because it’s built with the exact voltage, torque requirements, and operational conditions in mind. As a result, the machine runs smoother, with less wear and tear, and requires fewer maintenance interventions.
Cost Considerations
While the performance benefits of OEM DC motors are clear, cost considerations often pose a challenge. Custom-built solutions generally come with a higher upfront cost compared to generic motors. However, upon closer examination, the investment in OEM DC motors can provide significant savings over time.
Initial Investment vs. Long-Term Savings
Initially, purchasing an OEM DC motor may seem more expensive. But considering the reduced maintenance costs, lower energy consumption, and fewer replacements needed, the total cost of ownership can be considerably lower in the long run. A motor that perfectly fits its application can operate more efficiently, use less power, and have a longer operational life, which translates into cost savings over time.
Downtime and Operational Efficiency
Downtime can be a major cost factor in any manufacturing setting. Equipment failure not only halts production but also incurs repair and potential replacement costs. OEM DC motors, being tailor-made and more reliable, tend to experience fewer breakdowns. This reliability decreases the downtime and, therefore, boosts the overall operational efficiency. Over time, the increased productivity can offset the initial high cost of these motors.
Making the Right Choice
Balancing cost and performance in manufacturing requires careful consideration and analysis. The choice between a standard off-the-shelf motor and an OEM DC motor must be made based on particular needs and constraints of the manufacturing process.
Assessing Your Needs
Start by assessing the unique needs of your operation. What are the specific requirements of your machinery? Evaluate aspects like power demands, operational environments, and the criticality of the application. Understanding these requirements will help in determining whether the customization provided by an OEM DC motor justifies the cost.
Long-Term Planning
Consider the long-term implications of your decision. Analyzing factors such as operational efficiency, maintenance schedules, and energy consumption over time can provide a clearer picture of the total cost of ownership. An up-front investment in an OEM DC motor might seem steep, but the benefits reaped over the years often outweigh the initial expenditure.
Supplier Relationships
Establishing a reliable relationship with a trusted motor supplier can also play a crucial role. Suppliers with expertise in OEM DC motors can provide valuable insights and support throughout the lifecycle of your machinery. They can help in selecting the right motor specifications and provide after-sales support, ensuring the optimal performance of your systems.
Case Studies and Real-world Examples
Illustrating the balance of cost and performance through real-world examples can further solidify the understanding of OEM DC motors’ benefits.
Example 1: Automotive Industry
In the automotive industry, precision and reliability are paramount. A major automaker opted for OEM DC motors in their assembly line robots. While the initial cost was higher, the enhanced durability and precision of these motors significantly reduced maintenance intervals and improved production consistency. Over five years, the company witnessed a substantial reduction in operational costs due to fewer breakdowns and lower energy consumption.
Example 2: Packaging Industry
A packaging company integrated OEM DC motors into its high-speed conveyor systems. The customized motors offered better synchronization and speed control, which was critical for maintaining product quality. Despite the initial investment, the company saw improvements in throughput and reduction in product wastage, leading to better profitability.
Conclusion
Balancing cost and performance in manufacturing is an ongoing challenge, but OEM DC motors provide a viable solution for achieving this equilibrium. By offering customization that aligns precisely with operational requirements, these motors help enhance efficiency, reduce downtime, and optimize long-term costs.
While the initial investment might be high, the benefits accrued over the lifecycle of the machinery can far outweigh these costs. Through careful assessment of needs, long-term planning, and building strong supplier relationships, manufacturers can make informed decisions to harness the full potential of OEM DC motors. In doing so, not only do they achieve a perfect balance of cost and performance, but they also pave the way for a more reliable and efficient manufacturing process.
資料ダウンロード
QCD調達購買管理クラウド「newji」は、調達購買部門で必要なQCD管理全てを備えた、現場特化型兼クラウド型の今世紀最高の購買管理システムとなります。
ユーザー登録
調達購買業務の効率化だけでなく、システムを導入することで、コスト削減や製品・資材のステータス可視化のほか、属人化していた購買情報の共有化による内部不正防止や統制にも役立ちます。
NEWJI DX
製造業に特化したデジタルトランスフォーメーション(DX)の実現を目指す請負開発型のコンサルティングサービスです。AI、iPaaS、および先端の技術を駆使して、製造プロセスの効率化、業務効率化、チームワーク強化、コスト削減、品質向上を実現します。このサービスは、製造業の課題を深く理解し、それに対する最適なデジタルソリューションを提供することで、企業が持続的な成長とイノベーションを達成できるようサポートします。
オンライン講座
製造業、主に購買・調達部門にお勤めの方々に向けた情報を配信しております。
新任の方やベテランの方、管理職を対象とした幅広いコンテンツをご用意しております。
お問い合わせ
コストダウンが利益に直結する術だと理解していても、なかなか前に進めることができない状況。そんな時は、newjiのコストダウン自動化機能で大きく利益貢献しよう!
(Β版非公開)