- お役立ち記事
- Managing Manufacturing Quality with SPC (Statistical Process Control)
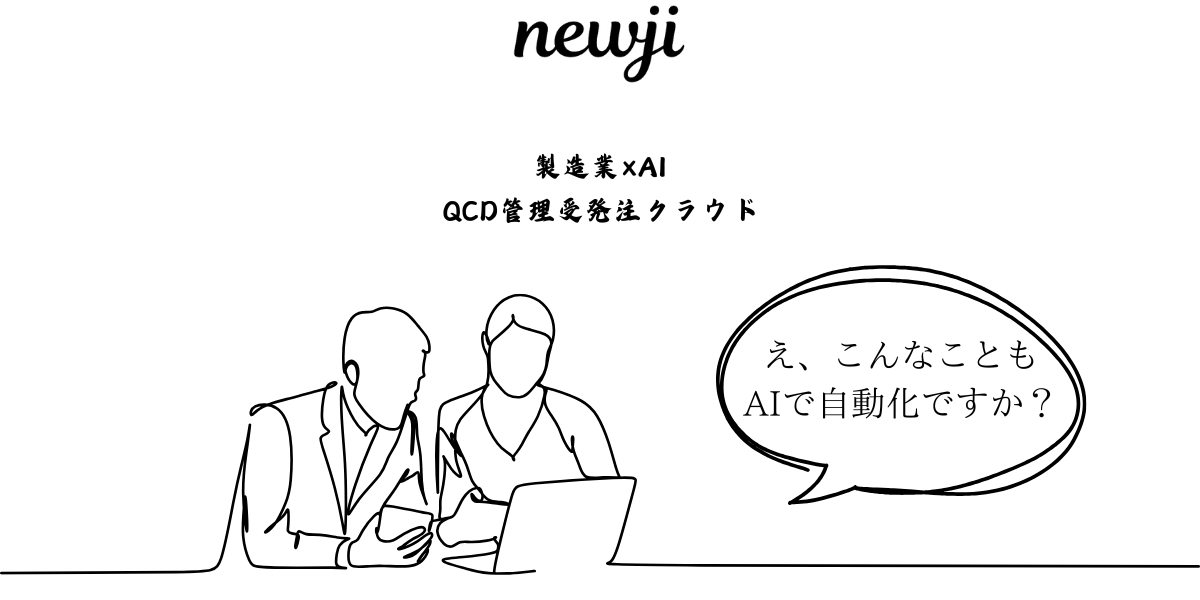
Managing Manufacturing Quality with SPC (Statistical Process Control)
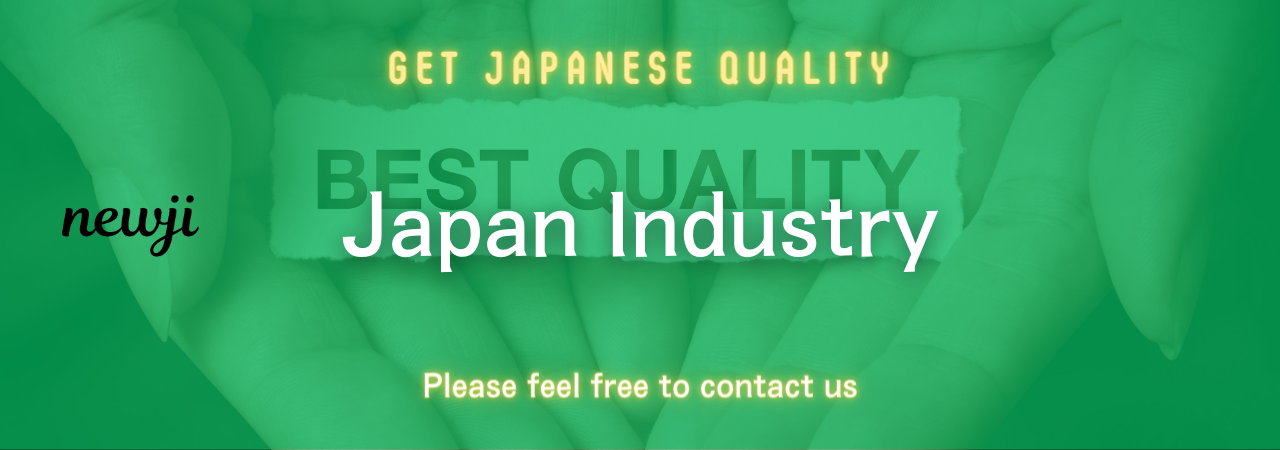
In today’s fast-paced manufacturing world, maintaining high-quality products is crucial. One way companies ensure this is through Statistical Process Control, or SPC. In this article, we’ll discuss what SPC is and how it helps manage manufacturing quality.
目次
What is Statistical Process Control?
Statistical Process Control, or SPC, is a method used in manufacturing to monitor and control processes. It uses statistical tools to track production quality and detect variations that might lead to defects. By keeping an eye on these variations, companies can fix problems before they affect the final product.
The Basics of SPC
SPC relies on data collection and analysis. As products are made, data on various aspects of the production process is gathered. These might include measurements like size, weight, or temperature. This data is then plotted on charts, allowing engineers to see if the process is staying within acceptable limits.
Why Use SPC?
There are several reasons why SPC is used in manufacturing.
First, it helps ensure consistent quality. By catching issues early, SPC prevents defective products from reaching customers.
Second, it reduces waste. When problems are detected early, less material is wasted on defective products.
Third, it can improve efficiency. By understanding the process better, manufacturers can make adjustments to run operations more smoothly.
SPC Tools and Techniques
Several tools and techniques are commonly used in SPC. These help manufacturers collect, analyze, and interpret data to maintain control over their processes.
Control Charts
One of the most important SPC tools is the control chart. A control chart is a graph used to study how a process changes over time. Data points are plotted in time order, with a central line showing the average and control limits indicating the acceptable range. If data points fall outside these limits, it signals that something might be wrong.
Histograms
Histograms are another key tool. They show the distribution of data points over a specified range. By looking at a histogram, engineers can see patterns and trends in the data, which can help identify potential issues.
Pareto Analysis
Pareto analysis, also known as the 80/20 rule, is used to prioritize problems. It helps identify the most significant issues affecting quality. Typically, 80% of problems are caused by 20% of the causes. By focusing on these key causes, manufacturers can make more impactful improvements.
Implementing SPC in Manufacturing
To successfully implement SPC, follow these key steps.
Identify Key Processes
Start by identifying the critical processes that impact product quality. These are the areas where SPC can make the biggest difference. Focus on processes that have a history of variability or defects.
Collect Data
Next, set up a system for collecting data on these processes. This might involve manual measurements or automated sensors. Ensure that data is collected consistently and accurately.
Analyze Data
Once you have collected data, the next step is to analyze it using SPC tools. Plot control charts to see if the process is within control limits. Look at histograms to understand data distribution. Use Pareto analysis to prioritize issues.
Make Improvements
Based on your analysis, identify areas for improvement. This might involve adjusting machine settings, retraining operators, or changing materials. Implement these improvements and continue to monitor the process.
Review and Adjust
SPC is not a one-time activity. It’s an ongoing process. Regularly review your control charts and other tools to ensure the process remains within control limits. Make adjustments as needed and continually seek ways to improve.
Benefits of SPC
Using SPC offers several benefits to manufacturers.
Improved Quality
By catching and correcting issues early, SPC helps ensure that only high-quality products leave the factory. This leads to higher customer satisfaction and fewer returns.
Reduced Costs
SPC can significantly reduce costs by minimizing waste. When fewer defective products are produced, less material is wasted. This also means fewer resources spent on rework or recalls.
Enhanced Efficiency
With a better understanding of the production process, manufacturers can streamline operations. This leads to faster production times and increased output.
Data-Driven Decisions
SPC provides valuable data that can inform decision-making. Rather than relying on guesswork, managers can use real data to make informed changes. This leads to more effective and targeted improvements.
Conclusion
Statistical Process Control, or SPC, is a powerful tool for managing manufacturing quality. By using data to monitor and control processes, manufacturers can ensure consistent quality, reduce waste, and improve efficiency.
Implementing SPC involves identifying key processes, collecting and analyzing data, making improvements, and continually reviewing and adjusting. The benefits of SPC are clear: improved product quality, reduced costs, enhanced efficiency, and data-driven decision-making.
In today’s competitive market, maintaining high quality is essential. SPC provides a proven method to help manufacturers achieve this goal. Whether you’re new to SPC or looking to enhance your current practices, embracing this approach can lead to significant benefits for your manufacturing operations.
資料ダウンロード
QCD調達購買管理クラウド「newji」は、調達購買部門で必要なQCD管理全てを備えた、現場特化型兼クラウド型の今世紀最高の購買管理システムとなります。
ユーザー登録
調達購買業務の効率化だけでなく、システムを導入することで、コスト削減や製品・資材のステータス可視化のほか、属人化していた購買情報の共有化による内部不正防止や統制にも役立ちます。
NEWJI DX
製造業に特化したデジタルトランスフォーメーション(DX)の実現を目指す請負開発型のコンサルティングサービスです。AI、iPaaS、および先端の技術を駆使して、製造プロセスの効率化、業務効率化、チームワーク強化、コスト削減、品質向上を実現します。このサービスは、製造業の課題を深く理解し、それに対する最適なデジタルソリューションを提供することで、企業が持続的な成長とイノベーションを達成できるようサポートします。
オンライン講座
製造業、主に購買・調達部門にお勤めの方々に向けた情報を配信しております。
新任の方やベテランの方、管理職を対象とした幅広いコンテンツをご用意しております。
お問い合わせ
コストダウンが利益に直結する術だと理解していても、なかなか前に進めることができない状況。そんな時は、newjiのコストダウン自動化機能で大きく利益貢献しよう!
(Β版非公開)