- お役立ち記事
- Mastering Delivery Time Management: The Japanese Approach to Excellence in Manufacturing
Mastering Delivery Time Management: The Japanese Approach to Excellence in Manufacturing
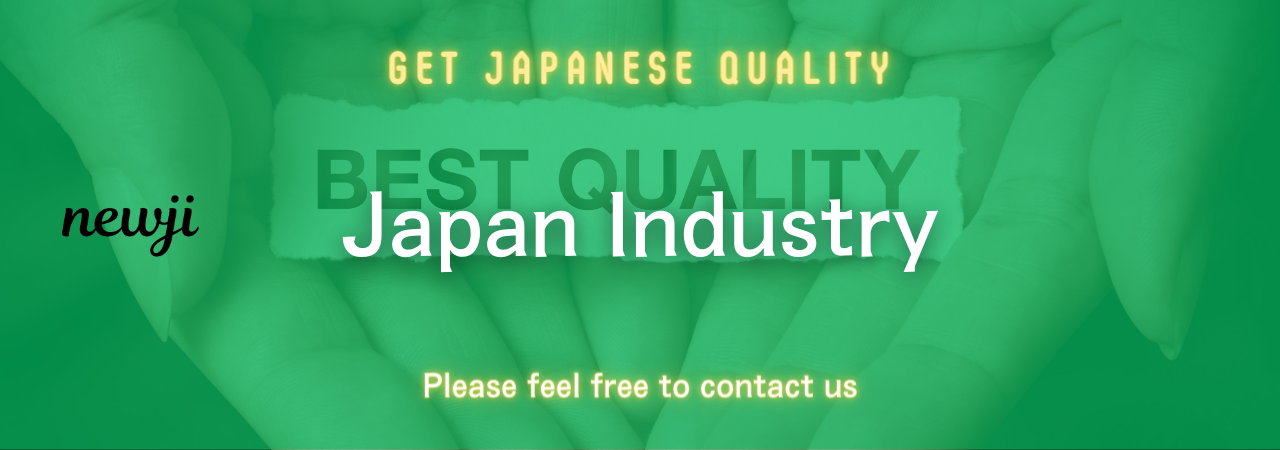
目次
Understanding the Japanese Philosophy of Time Management in Manufacturing
Japanese manufacturing companies are globally renowned for their meticulous approach to quality, efficiency, and delivery time management.
This highly disciplined methodology has catapulted them to the forefront of the global market, earning the admiration of companies worldwide.
To unlock the full potential of working with Japanese suppliers, it’s crucial to first understand their underlying philosophy and approach to time management.
The Japanese manufacturing philosophy is deeply rooted in principles derived from the Toyota Production System (TPS).
Two central tenets, Just-In-Time (JIT) and Kaizen (continuous improvement), drive their operational strategies.
JIT focuses on producing only what is needed, when it is needed, minimizing waste and inventory costs.
Kaizen, on the other hand, is a relentless pursuit of incremental improvements in every aspect of the manufacturing process.
By integrating these principles into their operations, Japanese manufacturers achieve superior coordination, efficiency, and punctuality.
Advantages and Disadvantages of Delivery Time Management with Japanese Suppliers
Advantages
Precision and Reliability
One of the biggest advantages of working with Japanese suppliers is their unwavering commitment to precision and reliability.
Their meticulously structured processes and robust quality control mechanisms ensure that delivery schedules are adhered to with minimal deviations.
Advanced Production Techniques
Japanese suppliers often employ advanced production techniques and technologies that significantly enhance their flexibility and responsiveness to changes in order volumes and delivery schedules.
This agility enables them to meet the varying demands of international clients.
Strong Relationship Building
Japanese business culture places a high value on long-term relationships.
Building a strong rapport with suppliers can lead to more favorable terms, priority treatment for urgent orders, and collaborative problem-solving.
Disadvantages
Rigidity in Processes
While Japanese manufacturing processes are highly efficient, they can sometimes be inflexible.
Changes in orders or sudden requests for expedited delivery might be challenging to accommodate due to the stringent adherence to pre-set schedules.
Communication Barriers
Language and cultural nuances can occasionally result in misunderstandings.
Clear, effective communication is crucial to ensure that both parties are on the same page regarding delivery timelines and expectations.
Cost Implications
Due to the high standards of quality control and process management, products from Japanese suppliers might come at a premium.
However, these costs are often offset by the reliability and quality of the goods delivered.
Supplier Negotiation Techniques for Effective Time Management
Successful negotiation with Japanese suppliers requires a blend of cultural sensitivity, strategic planning, and clear communication.
Here are some techniques to consider:
Building Trust and Rapport
Establishing a foundation of trust is paramount when dealing with Japanese suppliers.
Demonstrating respect, integrity, and a genuine interest in building a long-term partnership can go a long way in gaining their cooperation and commitment to meeting delivery timelines.
Setting Clear Expectations
Clearly articulate your delivery expectations and requirements from the outset.
Provide detailed forecasts, share production schedules, and outline any critical deadlines.
Clarity and transparency help in aligning both parties’ goals and minimizing potential delays.
Regular Communication
Maintain regular communication with your suppliers.
Regular check-ins, status updates, and progress reviews help in identifying potential issues early and taking corrective actions promptly.
Utilize multiple communication channels, including emails, video calls, and face-to-face meetings, to ensure mutual understanding.
Incorporating Flexibility
While Japanese suppliers may have rigid processes, showing flexibility on your part can foster goodwill and cooperation.
Offer reasonable lead times for orders and accommodate their scheduling needs wherever possible.
Flexibility can lead to more favorable responses when urgent requests arise.
Understanding Market Conditions and Their Impact on Delivery Times
Japanese manufacturing operates in a dynamic market environment influenced by various factors that can impact delivery times.
Global Economic Conditions
Fluctuations in the global economy, such as changes in trade policies, tariffs, and exchange rates, can impact production costs and delivery schedules.
Staying informed about these market conditions can help in proactive planning and risk mitigation.
Technological Advancements
Continuous advancements in manufacturing technologies and automation can enhance productivity and reduce lead times.
Keeping abreast of these technological trends can offer insights into how Japanese suppliers might optimize their delivery processes.
Supply Chain Disruptions
Natural disasters, geopolitical tensions, and pandemics can disrupt supply chains, affecting raw material availability and transit times.
Collaborating with suppliers on contingency plans and diversifying sourcing options can mitigate these disruptions.
Best Practices for Effective Delivery Time Management with Japanese Suppliers
Adopting best practices tailored to the Japanese approach to manufacturing can significantly enhance your ability to manage delivery times effectively.
Invest in Relationship Building
Nurturing strong, long-term relationships with Japanese suppliers is foundational to effective delivery time management.
Regular visits to supplier facilities, participation in joint training sessions, and cultural exchange programs can strengthen mutual understanding and collaboration.
Implement Joint Planning and Forecasting
Collaborative planning and forecasting can align production schedules and delivery timelines more closely with your needs.
Sharing accurate and detailed demand forecasts helps suppliers plan better and allocate resources efficiently, reducing the risk of delays.
Leverage Technology for Real-Time Monitoring
Utilize advanced technologies such as IoT, real-time tracking systems, and supply chain management software to monitor the production and delivery processes.
Real-time data enables proactive decision-making, allowing you to address issues promptly and ensure on-time deliveries.
Foster Continuous Improvement
Encourage a culture of continuous improvement both within your organization and with your suppliers.
Regularly review performance metrics, identify areas for improvement, and implement corrective actions.
Collaborative improvement initiatives can enhance overall efficiency and delivery reliability.
Develop Contingency Plans
Proactively develop contingency plans to address potential disruptions in the supply chain.
Identify critical suppliers, assess risks, and establish backup plans for alternative sourcing and logistics.
Having contingency plans in place ensures business continuity and minimizes impact on delivery schedules.
Case Study: Successful Delivery Time Management with a Japanese Supplier
To illustrate the practical application of the principles discussed, let’s look at a real-life case study of a company that successfully managed delivery times with its Japanese supplier.
Company A, a global electronics manufacturer, needed to secure a reliable source of high-precision components for its new product line.
Understanding the advantages of Japanese manufacturing, they chose to partner with Supplier X, a reputable Japanese supplier known for its quality and punctuality.
Building a Strong Relationship
Company A invested time in building a strong relationship with Supplier X.
Senior management from both companies conducted regular face-to-face meetings to discuss strategic goals, production capabilities, and delivery expectations.
This fostered a sense of mutual respect and collaboration, laying the groundwork for effective time management.
Collaborative Planning and Forecasting
Company A shared detailed demand forecasts and production schedules with Supplier X on a quarterly basis.
They collaborated on joint planning sessions to align production timelines and resource allocation.
This proactive approach enabled Supplier X to optimize its production processes and ensure timely deliveries.
Leveraging Real-Time Tracking Technology
To monitor the production and delivery process, Company A implemented a real-time tracking system.
This allowed them to track the progress of their orders, identify potential delays, and communicate with Supplier X in real time.
By having visibility into the entire supply chain, Company A could address issues promptly and ensure on-time deliveries.
Continuous Improvement Initiatives
Both companies embraced a culture of continuous improvement.
They conducted regular performance reviews, identifying bottlenecks and areas for enhancement.
Joint improvement initiatives led to optimized production processes, reduced lead times, and improved delivery reliability.
Contingency Planning
Recognizing the potential for supply chain disruptions, Company A and Supplier X developed robust contingency plans.
They identified alternative sources for key components and established protocols for rapid response to unforeseen events.
This ensured business continuity and minimized the impact of any disruptions on delivery timelines.
Conclusion
Mastering delivery time management when working with Japanese suppliers requires a deep understanding of their manufacturing philosophy, effective negotiation techniques, and the adoption of best practices.
The principles of Just-In-Time and Kaizen, combined with a commitment to building strong relationships, clear communication, and continuous improvement, form the foundation of successful collaboration.
By leveraging advanced technologies, staying informed about market conditions, and proactively addressing risks, companies can optimize delivery times and enjoy the benefits of working with Japanese suppliers.
The case study of Company A and Supplier X exemplifies how a strategic and collaborative approach can lead to exceptional delivery time management, enhancing overall efficiency and competitiveness in the global market.
Incorporating these insights and practices into your procurement and purchasing strategies will position your organization for success in today’s dynamic manufacturing landscape.
資料ダウンロード
QCD調達購買管理クラウド「newji」は、調達購買部門で必要なQCD管理全てを備えた、現場特化型兼クラウド型の今世紀最高の購買管理システムとなります。
ユーザー登録
調達購買業務の効率化だけでなく、システムを導入することで、コスト削減や製品・資材のステータス可視化のほか、属人化していた購買情報の共有化による内部不正防止や統制にも役立ちます。
NEWJI DX
製造業に特化したデジタルトランスフォーメーション(DX)の実現を目指す請負開発型のコンサルティングサービスです。AI、iPaaS、および先端の技術を駆使して、製造プロセスの効率化、業務効率化、チームワーク強化、コスト削減、品質向上を実現します。このサービスは、製造業の課題を深く理解し、それに対する最適なデジタルソリューションを提供することで、企業が持続的な成長とイノベーションを達成できるようサポートします。
オンライン講座
製造業、主に購買・調達部門にお勤めの方々に向けた情報を配信しております。
新任の方やベテランの方、管理職を対象とした幅広いコンテンツをご用意しております。
お問い合わせ
コストダウンが利益に直結する術だと理解していても、なかなか前に進めることができない状況。そんな時は、newjiのコストダウン自動化機能で大きく利益貢献しよう!
(Β版非公開)