- お役立ち記事
- Technology of Cold Forging and Its Applications in Manufacturing
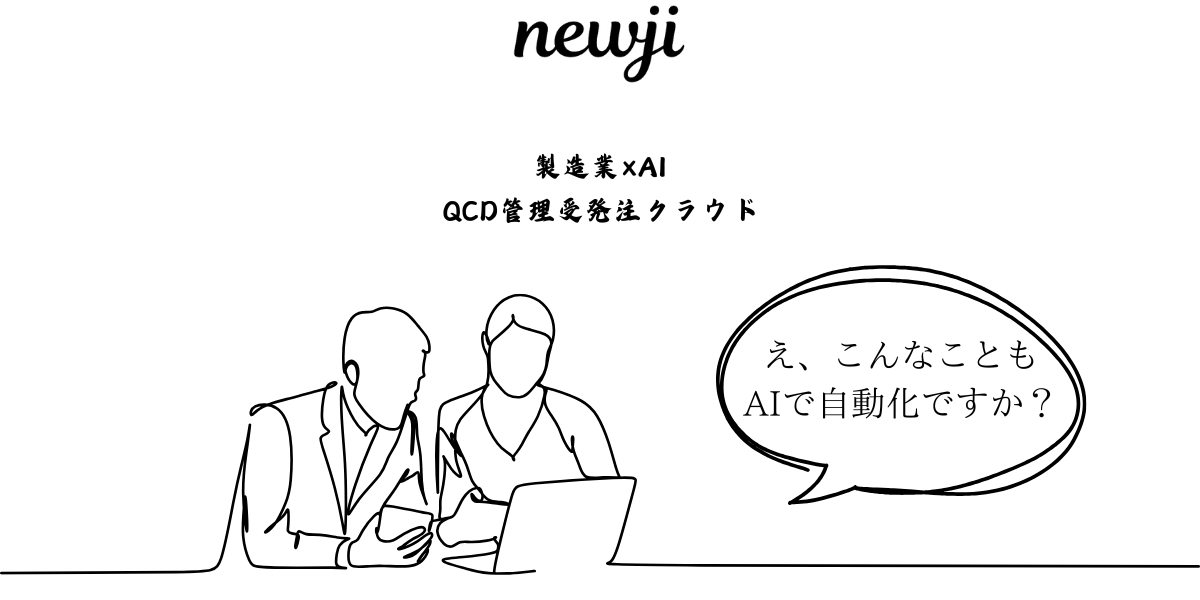
Technology of Cold Forging and Its Applications in Manufacturing
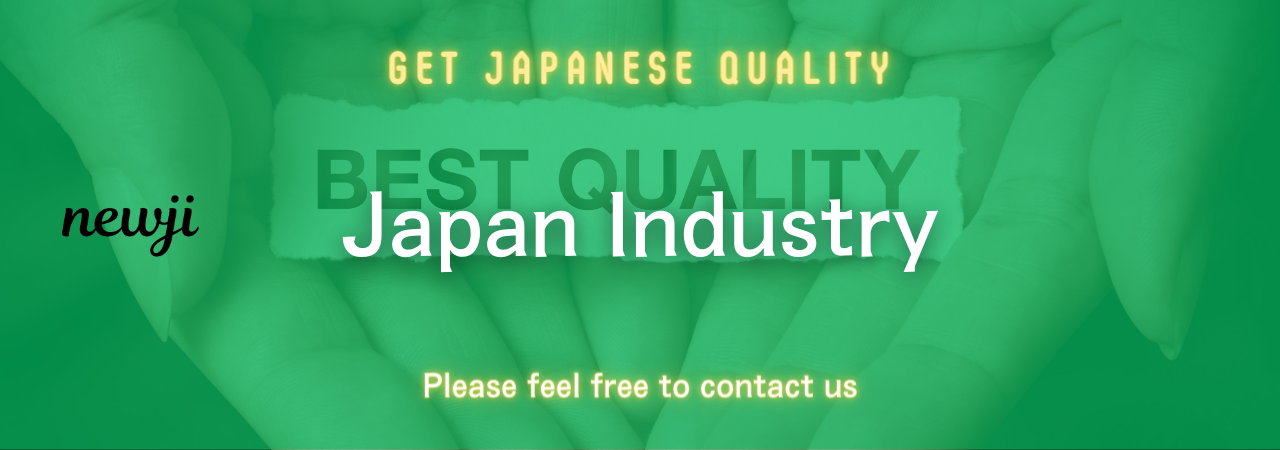
Cold forging is a manufacturing process that shapes metal materials at or near room temperature to create various industrial components.
This process is popular due to its cost-effectiveness, high strength of finished products, and minimal waste production.
目次
Understanding Cold Forging
Cold forging, also known as cold forming, involves deforming metal to a finished shape without heating the material above its recrystallization temperature.
Unlike traditional hot forging, cold forging is performed at room temperature.
This process usually includes operations like bending, coining, extruding, heading, punching, and thread rolling.
Materials Used in Cold Forging
Various metals can be used in cold forging, with the most common being aluminum, brass, copper, and steel.
Aluminum’s high malleability makes it a favorite choice, while steel is often chosen for its strength and durability.
Copper and brass are also popular due to their excellent electrical conductivity and resistance to corrosion.
Benefits of Cold Forging
Cold forging offers numerous benefits, making it a preferred method in many industries.
Enhanced Mechanical Properties
Cold-forged components typically possess superior mechanical properties.
These parts exhibit increased tensile strength and fatigue resistance due to the work hardening that occurs during the forging process.
The grains of the metal are reoriented to produce a denser, more robust structure.
Cost-Effective Production
Cold forging is more economical than other manufacturing methods.
There is minimal material waste as metal scraps and flashes are significantly reduced.
Additionally, it usually requires less energy since there is no need for extensive heating, which minimizes production costs.
Precision and Surface Finish
Cold forging allows for greater dimensional accuracy and better surface finish.
Due to precise tooling, components can be formed with tight tolerances.
This reduces the need for additional machining, saving both time and money.
Applications of Cold Forging
Cold forging is utilized in various industries to produce a range of components.
Automotive Industry
In the automotive industry, cold forging is commonly used to manufacture parts such as gears, shafts, and fasteners.
The process creates components that are strong enough to withstand the demands of automotive applications.
Both engine and transmission components often benefit from cold forging due to their need for high durability.
Aerospace Industry
The aerospace industry takes advantage of cold forging to produce lightweight yet strong components.
Critical parts like brackets, fasteners, and panel connectors are often made through cold forging.
The process ensures that these components meet the stringent safety and performance standards required in aerospace applications.
Electrical and Electronics Industry
Cold forging is also prevalent in the electrical and electronics industry.
Components like connectors, terminals, and heat sinks benefit greatly due to the excellent electrical conductivity and precision offered by cold forging.
Copper and aluminum parts, in particular, are widely produced through this method.
Manufacturing and Industrial Equipment
Many manufacturing and industrial tools and equipment are built using cold forging.
This includes bolts, nuts, and various fasteners used in machinery.
Cold-forged parts are exceptionally durable, making them suitable for heavy-duty applications.
Challenges in Cold Forging
While cold forging offers many benefits, it also presents some challenges.
Tooling and Equipment Costs
The initial cost for tooling and equipment in cold forging can be high.
Precision tools are essential for the process, and their design and manufacture can be quite expensive.
However, the initial investment often pays off in the long run due to lower production costs and high output rates.
Material Limitations
Not all metals are suitable for cold forging.
Metals that are too brittle may crack under the pressure of cold forging.
Materials need to have adequate ductility to be successfully forged without heating.
Complexity of Dies
Creating the dies used in cold forging is a complex and precise task.
These dies must be manufactured with intricate detail to ensure the accuracy and quality of the finished product.
Any defects in the die can lead to flaws in the final components, making this an essential but challenging aspect of the process.
Future of Cold Forging
The future looks promising for cold forging due to continuous advancements in technology and processes.
Innovations in materials science, such as the development of superplastic materials, are expanding the range of materials suitable for cold forging.
Additionally, improvements in computer-aided design (CAD) and computer-aided manufacturing (CAM) are enhancing the precision and efficiency of cold forging processes.
Environmental Benefits
As industries seek more environmentally friendly manufacturing methods, cold forging stands out due to its reduced waste and lower energy consumption.
These environmental benefits make cold forging an increasingly attractive option for various industries looking to reduce their carbon footprint.
Customization and Smart Manufacturing
With the rise of smart manufacturing and Industry 4.0, cold forging processes are becoming more customizable and adaptable.
Advanced sensors and automation enable real-time monitoring and adjustments, ensuring the highest quality and efficiency in production.
These technologies also make it easier to produce small batches of customized components, further broadening the applications of cold forging.
In summary, cold forging is a highly effective and efficient manufacturing process that offers numerous advantages over other methods.
Its applications span across many industries, producing strong, precise, and cost-effective components.
With ongoing technological advancements, the future of cold forging looks bright, promising even more innovations and broader applications in the years to come.
資料ダウンロード
QCD調達購買管理クラウド「newji」は、調達購買部門で必要なQCD管理全てを備えた、現場特化型兼クラウド型の今世紀最高の購買管理システムとなります。
ユーザー登録
調達購買業務の効率化だけでなく、システムを導入することで、コスト削減や製品・資材のステータス可視化のほか、属人化していた購買情報の共有化による内部不正防止や統制にも役立ちます。
NEWJI DX
製造業に特化したデジタルトランスフォーメーション(DX)の実現を目指す請負開発型のコンサルティングサービスです。AI、iPaaS、および先端の技術を駆使して、製造プロセスの効率化、業務効率化、チームワーク強化、コスト削減、品質向上を実現します。このサービスは、製造業の課題を深く理解し、それに対する最適なデジタルソリューションを提供することで、企業が持続的な成長とイノベーションを達成できるようサポートします。
オンライン講座
製造業、主に購買・調達部門にお勤めの方々に向けた情報を配信しております。
新任の方やベテランの方、管理職を対象とした幅広いコンテンツをご用意しております。
お問い合わせ
コストダウンが利益に直結する術だと理解していても、なかなか前に進めることができない状況。そんな時は、newjiのコストダウン自動化機能で大きく利益貢献しよう!
(Β版非公開)