- お役立ち記事
- Selection of Thermoelectric Modules and Their Applications in Manufacturing
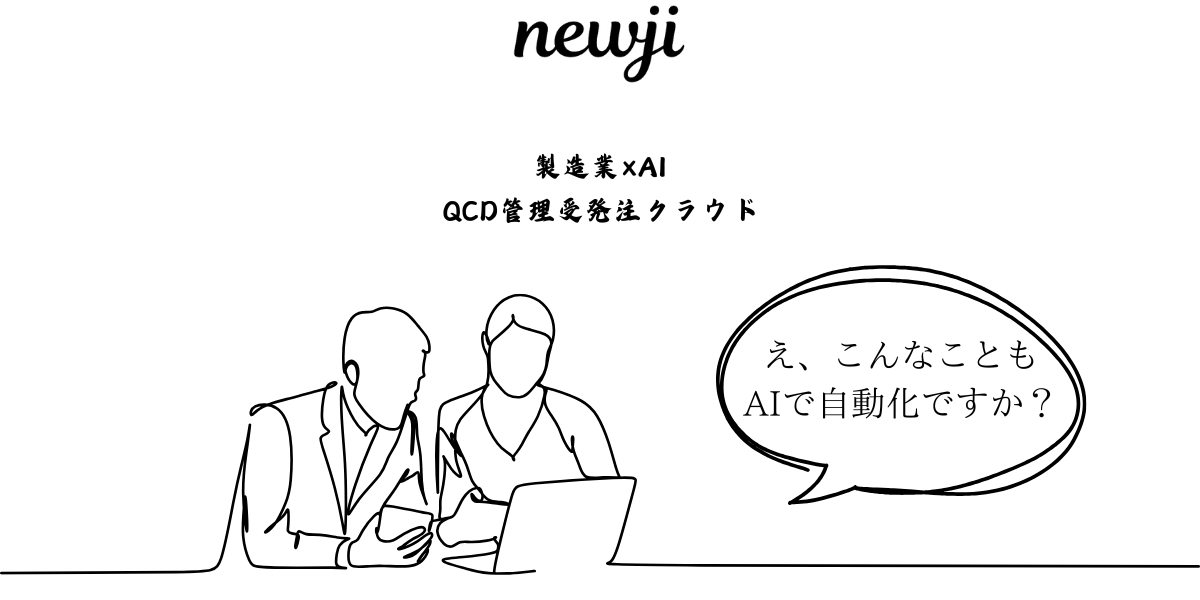
Selection of Thermoelectric Modules and Their Applications in Manufacturing
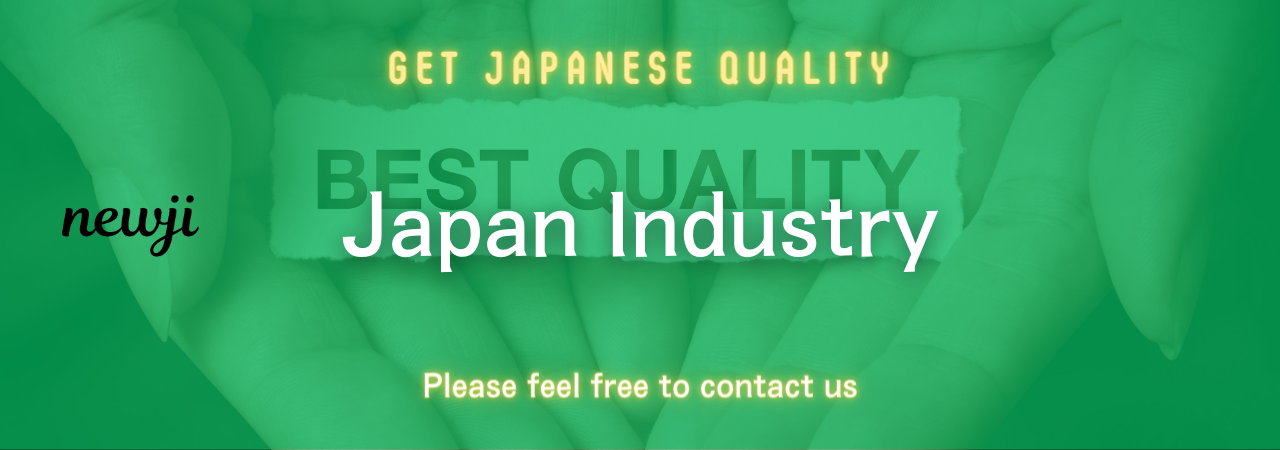
Thermoelectric modules, often referred to as thermoelectric generators (TEGs), have been gaining traction in various industries due to their ability to convert temperature differences directly into electrical energy.
This remarkable technology leverages the Seebeck effect, a phenomenon where voltage is created in the presence of temperature gradients.
The burgeoning field of thermoelectrics promises significant benefits, especially in the realm of manufacturing, where energy efficiency and sustainable practices are paramount.
Let’s delve deeper into how to select the right thermoelectric modules and explore their applications in manufacturing.
目次
Understanding Thermoelectric Modules
Thermoelectric modules are compact semiconductor devices composed of a series of p-type and n-type thermoelements, typically made from materials like bismuth telluride.
When a temperature difference is established across these elements, a voltage is generated, which can be harnessed for power.
Conversely, applying a voltage can create a temperature difference, allowing for both heating and cooling applications.
Although the basic principle remains consistent, various factors influence the module’s performance, including material properties, temperature range, and module design.
Key Considerations for Selecting Thermoelectric Modules
Material Selection
The material used in thermoelectric modules is crucial as it directly impacts efficiency and durability.
Bismuth telluride is commonly used due to its excellent thermoelectric properties at room temperatures.
For applications involving higher temperatures, materials like silicon-germanium or lead telluride may be more appropriate.
Temperature Range
Each thermoelectric material has an optimal operating temperature range.
Understanding the thermal environment of your application is critical.
For instance, if you intend to recover waste heat from industrial processes, selecting a module that withstands higher temperatures without degradation is essential.
Power Output and Efficiency
Different applications require varying power outputs and efficiencies.
For low-power applications, small modules with lower output might suffice.
However, for large-scale energy recovery, modules that offer high efficiency and power output are necessary.
Module Design
The design of the thermoelectric module, including its size, shape, and electrical configuration, plays a significant role in its performance.
Custom designs might be needed to fit specific applications or to enhance energy capture and conversion.
Applications of Thermoelectric Modules in Manufacturing
Waste Heat Recovery
One of the most promising applications of thermoelectric modules in manufacturing is waste heat recovery.
Industrial processes often generate large amounts of excess heat, which is a form of energy that usually goes to waste.
Thermoelectric modules can capture this heat and convert it into electricity, which can be reused within the plant or fed back into the grid.
Temperature Control
Thermoelectric modules can be utilized for precise temperature control in manufacturing.
By applying a voltage, these modules can either heat or cool components rapidly.
This capability is particularly beneficial in processes that require strict temperature regulation, such as semiconductor manufacturing or 3D printing.
Powering Remote Sensors
In large manufacturing facilities, it can be challenging and costly to provide power to remote sensors and monitoring equipment.
Thermoelectric modules can use the temperature differential between equipment and the ambient environment to generate power for these sensors.
This not only reduces wiring complexity but also improves the reliability of data collection.
Environmental Sustainability
Sustainability is becoming a cornerstone of modern manufacturing practices.
By leveraging thermoelectric modules to tap into waste heat and optimize energy usage, manufacturers can significantly reduce their carbon footprint and energy costs.
This, in turn, supports broader environmental goals and demonstrates a commitment to sustainable practices.
Challenges in Implementing Thermoelectric Modules
Despite their potential, there are several challenges associated with the deployment of thermoelectric modules in manufacturing.
Initial Costs
The upfront costs of thermoelectric modules can be high, particularly for those made from specialized materials needed for high-temperature applications.
However, the cost can be offset over time through energy savings and enhanced efficiency.
Efficiency Levels
Thermoelectric modules are not yet as efficient as traditional methods of power generation or temperature control.
Ongoing research aims to improve these efficiency levels, making them a more competitive option for a variety of applications.
System Integration
Integrating thermoelectric modules into existing manufacturing systems can be complex.
It requires careful planning and design to ensure compatibility and efficiency.
Additionally, ongoing maintenance might be needed to keep the systems operating optimally.
Future Prospects
Research and development in the field of thermoelectrics are paving the way for new materials and designs, which promise higher efficiencies and broader application scopes.
For example, advancements in nanostructured materials and quantum dot technologies are showing great potential in enhancing the conversion efficiency of thermoelectric modules.
In the future, we might also see the integration of thermoelectric modules with other renewable energy technologies, creating hybrid systems that maximize energy capture and utilization.
Conclusion
Selecting the right thermoelectric modules for manufacturing applications involves a detailed understanding of material properties, temperature ranges, power requirements, and design considerations.
While the initial investment might be substantial, the long-term benefits in terms of energy savings, environmental sustainability, and operational efficiency are significant.
As technology continues to advance, thermoelectric modules are likely to play an increasingly crucial role in the future of manufacturing, helping industries transition towards more sustainable and energy-efficient practices.
資料ダウンロード
QCD調達購買管理クラウド「newji」は、調達購買部門で必要なQCD管理全てを備えた、現場特化型兼クラウド型の今世紀最高の購買管理システムとなります。
ユーザー登録
調達購買業務の効率化だけでなく、システムを導入することで、コスト削減や製品・資材のステータス可視化のほか、属人化していた購買情報の共有化による内部不正防止や統制にも役立ちます。
NEWJI DX
製造業に特化したデジタルトランスフォーメーション(DX)の実現を目指す請負開発型のコンサルティングサービスです。AI、iPaaS、および先端の技術を駆使して、製造プロセスの効率化、業務効率化、チームワーク強化、コスト削減、品質向上を実現します。このサービスは、製造業の課題を深く理解し、それに対する最適なデジタルソリューションを提供することで、企業が持続的な成長とイノベーションを達成できるようサポートします。
オンライン講座
製造業、主に購買・調達部門にお勤めの方々に向けた情報を配信しております。
新任の方やベテランの方、管理職を対象とした幅広いコンテンツをご用意しております。
お問い合わせ
コストダウンが利益に直結する術だと理解していても、なかなか前に進めることができない状況。そんな時は、newjiのコストダウン自動化機能で大きく利益貢献しよう!
(Β版非公開)