- お役立ち記事
- Selection of Communication Equipment and Its Applications in Manufacturing
Selection of Communication Equipment and Its Applications in Manufacturing
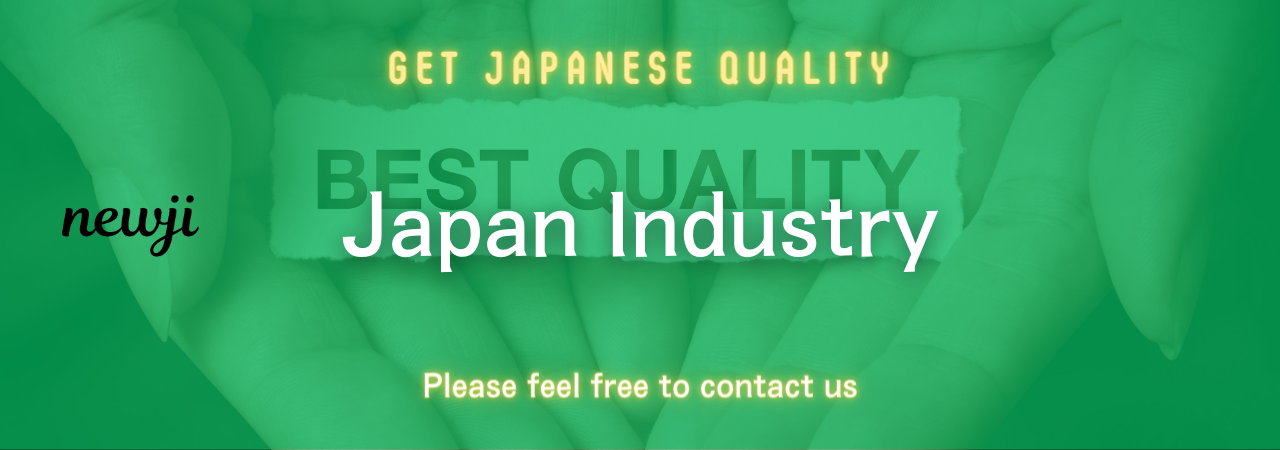
目次
Introduction to Communication Equipment in Manufacturing
In today’s fast-paced manufacturing environment, effective communication is essential for achieving operational efficiency and productivity.
The right communication equipment can streamline processes, enhance collaboration, and improve overall performance.
From walkie-talkies to advanced digital communication systems, there are various tools available.
This article explores the selection of communication equipment and its applications in the manufacturing sector.
Different Types of Communication Equipment
Walkie-Talkies
Walkie-talkies are portable devices that allow instant voice communication over short distances.
They are simple to use and require no setup, making them ideal for quick, on-the-spot communication.
In manufacturing, they are often used for coordination among team members on the shop floor.
Intercom Systems
Intercom systems are fixed communication devices that allow direct verbal interaction between different areas of a facility.
They are commonly installed in manufacturing plants to enable real-time communication between various departments or sections.
Intercoms are particularly useful for broadcasting important announcements or making emergency calls.
Digital Radio Systems
Digital radio systems offer a more advanced alternative to traditional walkie-talkies.
They provide clearer audio quality, enhanced security features, and better range.
Digital radios are equipped with multiple channels, enabling users to communicate privately or in groups.
These features make them highly suitable for complex manufacturing environments where reliable communication is crucial.
VoIP (Voice over Internet Protocol)
VoIP systems use the internet to transmit voice data, allowing for cost-effective and versatile communication.
They offer a range of features such as call forwarding, voicemail, and conferencing.
VoIP systems can be integrated with other digital tools, making them a valuable asset in modern manufacturing settings where seamless communication is key.
Factors to Consider When Selecting Communication Equipment
Range
The range of communication equipment is a critical factor.
In large manufacturing facilities, the ability to communicate over long distances is essential.
Consider whether the equipment can cover the entire area of your plant without loss of signal or quality.
Durability
Manufacturing environments can be harsh, with exposure to dust, moisture, and extreme temperatures.
Durable equipment designed to withstand such conditions will ensure uninterrupted communication.
Ease of Use
Complex systems may require extensive training, which can be time-consuming and costly.
Choosing user-friendly equipment ensures that all staff members can communicate effectively without requiring specialized knowledge.
Battery Life
For portable devices like walkie-talkies and digital radios, battery life is an important consideration.
Long battery life reduces the need for frequent recharging, ensuring that communication remains constant throughout the workday.
Applications of Communication Equipment in Manufacturing
Coordination and Collaboration
Effective communication equipment facilitates coordination and collaboration among different teams and departments.
For instance, walkie-talkies can be used by assembly line workers to communicate with supervisors, ensuring seamless operation and quick resolution of issues.
Emergency Management
In case of emergencies, such as equipment malfunctions or safety incidents, reliable communication is critical.
Intercom systems and digital radios can be used to quickly alert relevant personnel, enabling immediate response and minimizing downtime.
Quality Control
Maintaining high-quality standards is a top priority in manufacturing.
Communication equipment allows quality control teams to report issues in real-time, ensuring that defects are addressed promptly and preventing defective products from reaching the market.
Inventory Management
Accurate inventory management is essential for efficient manufacturing operations.
Communication tools can be used to coordinate stock checks, report shortages, and manage deliveries, ensuring that materials and products are available as needed.
Training and Guidance
New employees often require training and guidance from experienced staff members.
Communication equipment enables trainers to provide real-time instructions and feedback, accelerating the learning process and ensuring that new hires quickly become productive members of the team.
Benefits of Using Modern Communication Equipment
Improved Productivity
With efficient communication, tasks can be completed more quickly and accurately.
Instant access to information and the ability to coordinate activities enhances overall productivity.
Enhanced Safety
Clear and reliable communication is vital for maintaining a safe working environment.
Rapid reporting of hazards and swift response to emergencies can prevent accidents and injuries.
Cost Savings
Investing in advanced communication equipment can lead to significant cost savings.
Streamlined operations, reduced downtime, and improved efficiency translate to lower operational costs in the long term.
Better Decision-Making
Access to real-time information enables managers to make informed decisions quickly.
Effective communication ensures that all team members are on the same page, reducing misunderstandings and fostering better decision-making.
Conclusion
Selecting the right communication equipment is crucial for the success of any manufacturing operation.
From basic walkie-talkies to sophisticated digital systems, each tool offers unique benefits that can enhance productivity, safety, and efficiency.
By considering factors such as range, durability, ease of use, and battery life, manufacturers can choose the best equipment for their specific needs.
Ultimately, effective communication leads to better coordination, timely responses to issues, and overall improved performance in the manufacturing sector.
資料ダウンロード
QCD調達購買管理クラウド「newji」は、調達購買部門で必要なQCD管理全てを備えた、現場特化型兼クラウド型の今世紀最高の購買管理システムとなります。
ユーザー登録
調達購買業務の効率化だけでなく、システムを導入することで、コスト削減や製品・資材のステータス可視化のほか、属人化していた購買情報の共有化による内部不正防止や統制にも役立ちます。
NEWJI DX
製造業に特化したデジタルトランスフォーメーション(DX)の実現を目指す請負開発型のコンサルティングサービスです。AI、iPaaS、および先端の技術を駆使して、製造プロセスの効率化、業務効率化、チームワーク強化、コスト削減、品質向上を実現します。このサービスは、製造業の課題を深く理解し、それに対する最適なデジタルソリューションを提供することで、企業が持続的な成長とイノベーションを達成できるようサポートします。
オンライン講座
製造業、主に購買・調達部門にお勤めの方々に向けた情報を配信しております。
新任の方やベテランの方、管理職を対象とした幅広いコンテンツをご用意しております。
お問い合わせ
コストダウンが利益に直結する術だと理解していても、なかなか前に進めることができない状況。そんな時は、newjiのコストダウン自動化機能で大きく利益貢献しよう!
(Β版非公開)