- お役立ち記事
- Management of Continuous Processes and Their Applications in Manufacturing
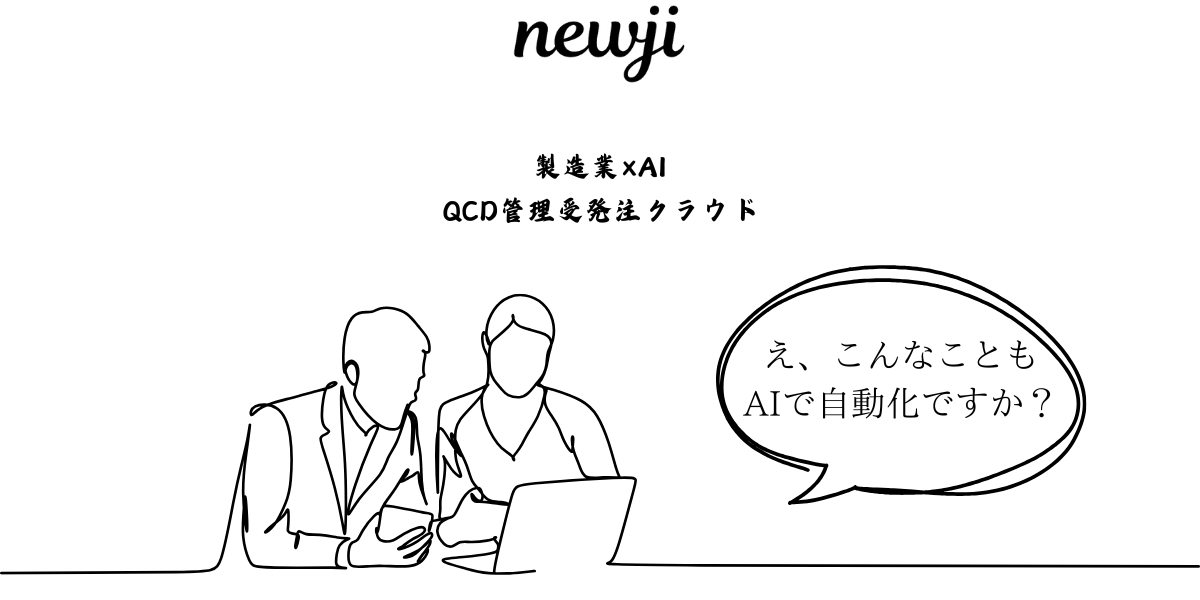
Management of Continuous Processes and Their Applications in Manufacturing
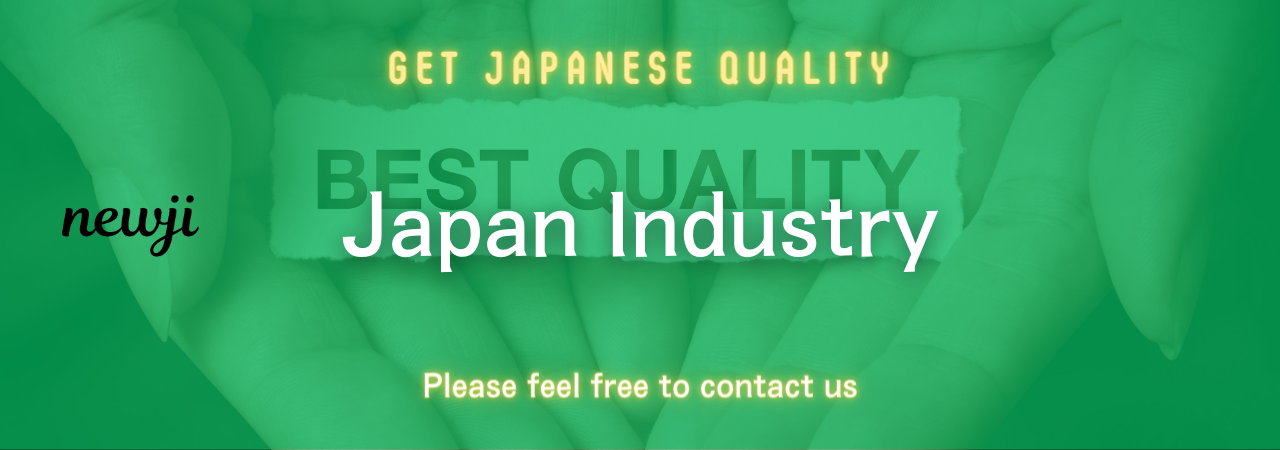
In the complex world of manufacturing, management of continuous processes is a crucial aspect that can significantly affect the efficiency and productivity of a plant.
These processes involve the ongoing production of goods without interruption, which can result in an optimized workflow and reduced production times.
Understanding the basics and benefits of managing continuous processes can provide valuable insights for anyone involved in the manufacturing industry.
目次
What are Continuous Processes?
Definition and Characteristics
Continuous processes refer to the production methods where raw materials are continuously introduced into the system, and products are continuously produced.
This is in contrast to batch processing, where production happens in discrete groups or “batches”.
Examples of continuous processes include oil refining, chemical manufacturing, and food production.
Several characteristics define continuous processes:
– The process is nonstop, which means operations run 24/7.
– They require a steady stream of raw materials.
– They often use automation technology to maintain consistency and efficiency.
Industrial Examples
Continuous processes are common in several industries due to their efficiency and ability to handle large-scale production:
1. **Oil Refining:** In the petroleum industry, crude oil is continuously fed into refineries where it is processed into various products like gasoline, diesel, and kerosene.
2. **Chemical Manufacturing:** Many chemicals, such as fertilizers and detergents, are produced through continuous processes to maintain high production rates and product consistency.
3. **Food and Beverage Production:** Items like bread, beer, and soft drinks are often produced in continuous operations to meet large consumer demands efficiently.
Benefits of Continuous Process Management
Increased Efficiency
One of the primary advantages of continuous processes is increased efficiency.
Because production is ongoing, there is less downtime compared to batch processing.
This constant operation means resources are continually being turned into products, minimizing waste and maximizing output.
Improved Quality Consistency
Since the process runs continuously, it is easier to maintain consistent quality.
Automation plays a significant role here, as it can monitor various parameters in real-time, ensuring that the product meets the specified standards throughout the production cycle.
Cost Reduction
Operating a continuous process can be more cost-effective than batch processing.
It reduces labor costs, as automation handles much of the work, and energy costs, since the system does not need to start and stop repeatedly.
Over time, these savings can be substantial.
Enhanced Scalability
Continuous processes allow for easy scalability.
As demand increases, manufacturers can adjust the speed or capacity of the system without needing significant overhauls.
This flexibility is crucial for maintaining competitiveness in fast-growing markets.
Challenges in Managing Continuous Processes
Complexity of Setup
Setting up a continuous process system is inherently complex.
It requires significant planning and investment in automation technology.
Ensuring that all components work seamlessly together to maintain the flow of materials can be challenging and time-consuming.
Maintenance Demands
Continuous processes require regular maintenance to prevent breakdowns.
Even minor issues can disrupt the entire production line, leading to costly downtimes.
Proactive maintenance and timely repairs are essential to keep the system running efficiently.
Quality Control
While automation helps maintain quality, it also requires rigorous control systems.
Any deviation in parameters can lead to significant quality issues.
Therefore, robust monitoring and control systems must be in place to detect and correct any anomalies quickly.
Applications in Modern Manufacturing
Pharmaceutical Industry
In the pharmaceutical industry, continuous processes are increasingly being adopted for the manufacture of drugs.
This approach allows for more consistent production and higher quality control.
Moreover, it helps in reducing the time from development to market, which is crucial in the pharmaceutical sector.
Automotive Industry
The automotive industry uses continuous processes in various stages of production, especially in the manufacturing of components like tires and batteries.
Continuous production ensures that the assembly line does not face delays, thus speeding up the overall manufacturing process.
Textile Industry
In textile manufacturing, continuous processes are employed to produce fabrics efficiently.
Processes like dyeing and finishing of fabrics benefit significantly from continuous operations, ensuring uniformity and high throughput.
Technological Advancements
Automation and Robotics
Advancements in automation and robotics have made continuous processes more accessible and efficient.
Robots can handle repetitive tasks with high precision, reducing the risk of human error and increasing the overall efficiency of the production line.
Advanced Monitoring Systems
State-of-the-art monitoring systems play a vital role in managing continuous processes.
These systems can provide real-time data on various parameters, enabling quick adjustments to maintain optimal performance.
IoT (Internet of Things) technology further enhances these capabilities by offering remote monitoring and control.
Artificial Intelligence (AI)
AI is increasingly being integrated into continuous processes to predict and mitigate issues before they affect production.
Through machine learning algorithms, AI can analyze historical data to forecast potential downtimes or quality issues, allowing for proactive management.
Conclusion
The management of continuous processes in manufacturing presents both opportunities and challenges.
The benefits in terms of efficiency, cost reduction, quality consistency, and scalability make it a preferred choice for many industries.
However, the complexity of setup and maintenance, along with stringent quality control demands, require careful planning and investment.
As technological advancements continue to evolve, the future of continuous process management looks promising.
Automation, advanced monitoring systems, and AI are set to further streamline these processes, making them more efficient and reliable.
For manufacturers willing to invest in the necessary infrastructure, managing continuous processes can lead to significant competitive advantages and business growth.
資料ダウンロード
QCD調達購買管理クラウド「newji」は、調達購買部門で必要なQCD管理全てを備えた、現場特化型兼クラウド型の今世紀最高の購買管理システムとなります。
ユーザー登録
調達購買業務の効率化だけでなく、システムを導入することで、コスト削減や製品・資材のステータス可視化のほか、属人化していた購買情報の共有化による内部不正防止や統制にも役立ちます。
NEWJI DX
製造業に特化したデジタルトランスフォーメーション(DX)の実現を目指す請負開発型のコンサルティングサービスです。AI、iPaaS、および先端の技術を駆使して、製造プロセスの効率化、業務効率化、チームワーク強化、コスト削減、品質向上を実現します。このサービスは、製造業の課題を深く理解し、それに対する最適なデジタルソリューションを提供することで、企業が持続的な成長とイノベーションを達成できるようサポートします。
オンライン講座
製造業、主に購買・調達部門にお勤めの方々に向けた情報を配信しております。
新任の方やベテランの方、管理職を対象とした幅広いコンテンツをご用意しております。
お問い合わせ
コストダウンが利益に直結する術だと理解していても、なかなか前に進めることができない状況。そんな時は、newjiのコストダウン自動化機能で大きく利益貢献しよう!
(Β版非公開)