- お役立ち記事
- Optimizing Production Planning with AI Production Schedulers
Optimizing Production Planning with AI Production Schedulers
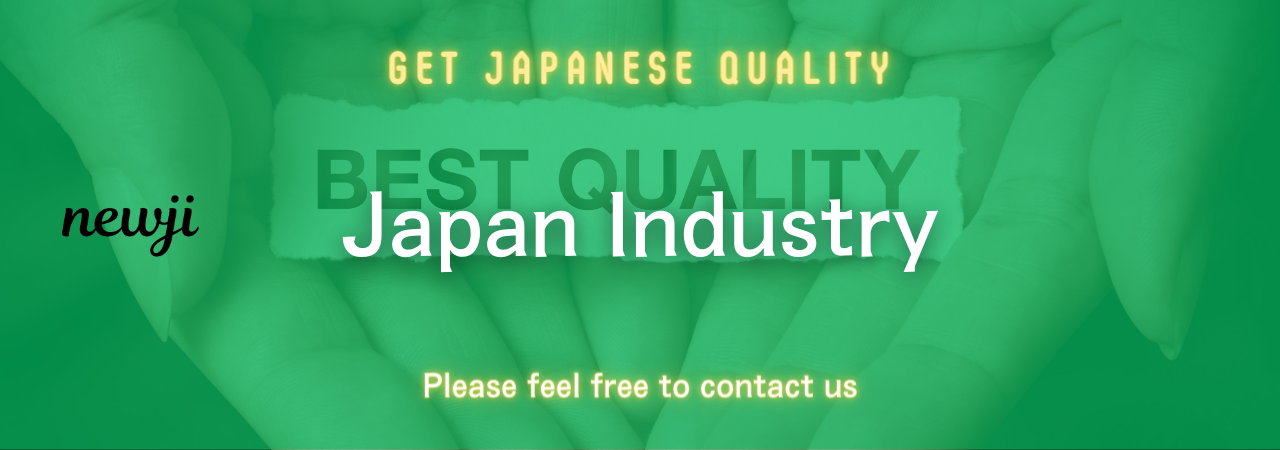
In today’s fast-paced manufacturing environment, optimizing production planning is vital to stay competitive.
Manufacturers are constantly seeking ways to enhance efficiency, reduce costs, and meet customer demands.
One of the most powerful tools now available to help achieve these goals is the AI production scheduler.
目次
What is an AI Production Scheduler?
An AI production scheduler is a software program that uses artificial intelligence to manage and optimize the production planning process.
It can analyze vast amounts of data, identify patterns, and make recommendations for scheduling production tasks.
By doing so, it helps manufacturers improve efficiency, reduce downtime, and minimize waste.
Benefits of Using AI in Production Scheduling
Increased Efficiency
AI production schedulers can process complex data much faster than human planners.
They can quickly analyze various factors such as resource availability, machine performance, and workforce capacity to create the most efficient production schedule.
This means less time spent on planning and more time focused on production.
Cost Reduction
By optimizing schedules, AI production schedulers help minimize production costs.
They can identify the most cost-effective way to allocate resources, reduce material waste, and minimize energy consumption.
This leads to significant savings for manufacturers.
Improved Product Quality
AI can help ensure that the right resources are available at the right time, reducing the chances of errors and bottlenecks in the production process.
This can lead to higher-quality products and fewer defects, which is crucial for maintaining customer satisfaction.
Better Decision Making
AI production schedulers provide detailed insights and real-time data, enabling manufacturers to make informed decisions.
They can simulate different scenarios and predict outcomes, helping planners choose the best course of action.
This leads to smarter, data-driven decisions.
How AI Production Schedulers Work
Data Collection
The first step in AI production scheduling is data collection.
The system gathers information from various sources, such as ERP systems, machine sensors, and workforce management tools.
This data provides a comprehensive view of the production environment.
Data Analysis
Once the data is collected, the AI system analyzes it to identify patterns and trends.
It uses advanced algorithms to process the data and generate insights.
These insights are used to create the most efficient production schedule.
Schedule Generation
Based on the analysis, the AI system generates a production schedule that optimizes resource allocation, minimizes downtime, and reduces costs.
The schedule is continuously updated in real-time to adapt to changing conditions and ensure optimal performance.
Implementing AI Production Schedulers
Assessing Needs
Before implementing an AI production scheduler, manufacturers need to assess their current production processes and identify areas where AI can make the most significant impact.
This involves evaluating current scheduling methods, identifying inefficiencies, and setting clear goals for improvement.
Choosing the Right Solution
There are various AI production scheduling solutions available in the market.
Manufacturers should choose a solution that aligns with their specific needs and integrates seamlessly with their existing systems.
Factors to consider include ease of use, scalability, and the ability to provide real-time insights.
Integration and Training
Implementing an AI production scheduler requires integrating the solution with existing systems and training staff to use it effectively.
This may involve working with software vendors to ensure smooth integration and providing employees with comprehensive training on how to use the new system.
Continuous Improvement
AI production schedulers are not a one-time solution.
Manufacturers should continuously monitor the system’s performance and seek opportunities for improvement.
This involves regularly updating the AI algorithms, incorporating new data, and refining processes to achieve ongoing optimization.
Challenges and Considerations
Data Quality
The accuracy of an AI production scheduler depends on the quality of the data it receives.
Manufacturers must ensure that their data is accurate, up-to-date, and complete.
This may require investing in better data management practices and tools.
Change Management
Implementing an AI production scheduler involves significant changes to existing processes and workflows.
Manufacturers need to manage this change effectively to ensure a smooth transition.
This includes communicating the benefits of the new system to employees and addressing any concerns they may have.
Costs
While AI production schedulers can lead to significant cost savings, the initial investment can be substantial.
Manufacturers need to consider the cost of the software, integration, training, and ongoing maintenance.
However, the long-term benefits often outweigh the initial costs.
Security
AI production schedulers rely on data from various sources, making them potential targets for cyber-attacks.
Manufacturers must ensure that their data is secure and that the AI system has robust security measures in place.
This includes implementing encryption, access controls, and regular security audits.
The Future of Production Scheduling
The use of AI in production scheduling is expected to grow significantly in the coming years.
As technology advances, AI systems will become even more sophisticated, providing deeper insights and greater optimization.
In the future, AI production schedulers may integrate with other advanced technologies such as IoT, robotics, and machine learning to further enhance production efficiency.
This could lead to the development of fully autonomous production systems that can adapt to changing conditions in real-time without human intervention.
In conclusion, AI production schedulers represent a powerful tool for manufacturers looking to optimize their production planning processes.
By leveraging AI, manufacturers can increase efficiency, reduce costs, improve product quality, and make better decisions.
While there are challenges to consider, the potential benefits make AI production schedulers a worthwhile investment for the future of manufacturing.
資料ダウンロード
QCD調達購買管理クラウド「newji」は、調達購買部門で必要なQCD管理全てを備えた、現場特化型兼クラウド型の今世紀最高の購買管理システムとなります。
ユーザー登録
調達購買業務の効率化だけでなく、システムを導入することで、コスト削減や製品・資材のステータス可視化のほか、属人化していた購買情報の共有化による内部不正防止や統制にも役立ちます。
NEWJI DX
製造業に特化したデジタルトランスフォーメーション(DX)の実現を目指す請負開発型のコンサルティングサービスです。AI、iPaaS、および先端の技術を駆使して、製造プロセスの効率化、業務効率化、チームワーク強化、コスト削減、品質向上を実現します。このサービスは、製造業の課題を深く理解し、それに対する最適なデジタルソリューションを提供することで、企業が持続的な成長とイノベーションを達成できるようサポートします。
オンライン講座
製造業、主に購買・調達部門にお勤めの方々に向けた情報を配信しております。
新任の方やベテランの方、管理職を対象とした幅広いコンテンツをご用意しております。
お問い合わせ
コストダウンが利益に直結する術だと理解していても、なかなか前に進めることができない状況。そんな時は、newjiのコストダウン自動化機能で大きく利益貢献しよう!
(Β版非公開)