- お役立ち記事
- Scenario Planning for Procurement Risk Management: Addressing Supply Chain Vulnerabilities
この記事は、当社の提供するお役立ち記事の一部です。詳しくは公式サイトをご覧ください。
Scenario Planning for Procurement Risk Management: Addressing Supply Chain Vulnerabilities
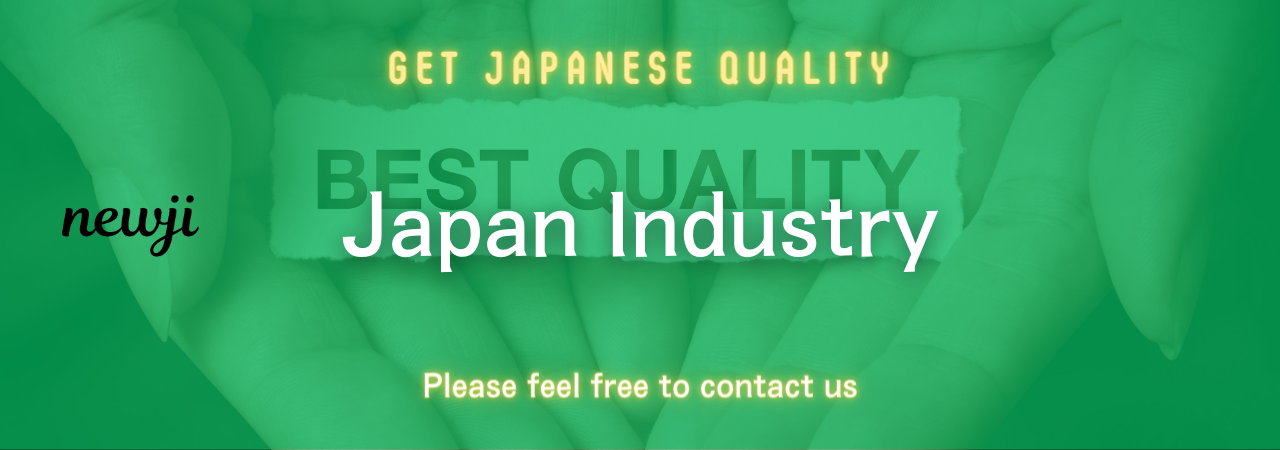
目次
Understanding Scenario Planning
Scenario planning is a strategic tool used by businesses to anticipate future challenges and opportunities.
By developing various scenarios, organizations can prepare for different possibilities and devise appropriate strategies.
In procurement, scenario planning helps identify and address supply chain vulnerabilities, ensuring a more resilient and responsive operation.
The Importance of Scenario Planning in Procurement
Procurement is the process of acquiring goods, services, or works from external sources.
With the global supply chain becoming increasingly complex, procurement faces numerous risks such as supplier failures, geopolitical tensions, and environmental disruptions.
Scenario planning enables procurement professionals to foresee these risks and develop contingency plans.
Addressing potential issues before they escalate helps maintain continuity and efficiency in the supply chain.
By anticipating disruptions, organizations can mitigate their impact, ensuring that operations run smoothly even in the face of adversity.
Steps to Implement Scenario Planning for Procurement
Identify Potential Risks
The first step in scenario planning is to identify potential risks that could affect your procurement process.
These risks can be categorized into several types:
– **Economic Risks**: Fluctuations in currency, inflation, or economic downturns.
– **Political Risks**: Changes in regulations, trade policies, or political instability.
– **Environmental Risks**: Natural disasters, climate change, or pandemics.
– **Technical Risks**: Cybersecurity threats, technological failures, or supply chain disruptions.
Conducting a thorough risk assessment helps in understanding various factors that could impact procurement.
Develop Multiple Scenarios
Once risks are identified, the next step is to develop multiple scenarios based on different combinations of these risks.
For each scenario, consider the possible outcomes and their impact on your procurement process.
This involves imagining both best-case and worst-case scenarios, as well as variations in between.
For instance, a worst-case scenario may involve a natural disaster disrupting a major supplier, whereas a best-case scenario might see uninterrupted supply chains with increased operational efficiency.
Analyze the Impact
After developing scenarios, analyze the impact of each one on your procurement operations.
This involves assessing how different factors such as cost, delivery time, and quality of goods could be affected.
Use data analysis and modeling tools to quantify the potential impact, making it easier to understand the severity of each scenario.
Develop Contingency Plans
Based on the analysis, develop contingency plans for each scenario.
These plans should outline specific actions to mitigate the impact of potential disruptions.
For example, if a supplier failure is identified as a significant risk, a contingency plan might include identifying alternative suppliers or increasing inventory levels.
Implement and Monitor
Once contingency plans are developed, it’s essential to implement them and continuously monitor the procurement process.
Regularly review and update these plans to ensure they remain relevant as new risks emerge.
Monitoring tools can help track the effectiveness of your plans and highlight areas that require adjustment.
Benefits of Scenario Planning in Procurement
Implementing scenario planning for procurement offers several benefits:
– **Enhanced Preparedness**: By anticipating potential disruptions, organizations can respond more effectively, minimizing downtime and maintaining efficiency.
– **Improved Decision-Making**: Scenario planning provides a structured framework for decision-making, helping procurement professionals evaluate the best course of action.
– **Cost Savings**: By identifying and mitigating risks early, businesses can avoid costly disruptions and additional expenses.
– **Increased Flexibility**: With contingency plans in place, organizations can quickly adapt to changing circumstances and maintain continuity.
– **Strengthened Supplier Relationships**: Proactive risk management fosters stronger relationships with suppliers, as it demonstrates a commitment to maintaining a stable supply chain.
Challenges in Scenario Planning
While scenario planning offers numerous benefits, it also presents certain challenges:
– **Complexity**: Developing multiple scenarios requires a thorough understanding of various risk factors and their potential combinations.
– **Uncertainty**: Predicting future risks involves a degree of uncertainty, requiring constant vigilance and adaptation.
– **Resource-Intensive**: Conducting detailed risk assessments and developing contingency plans can be resource-intensive, requiring time and effort from procurement teams.
Best Practices for Effective Scenario Planning
To maximize the effectiveness of scenario planning in procurement, consider the following best practices:
– **Collaborate Across Departments**: Involve stakeholders from different departments to ensure a comprehensive understanding of risks and potential impact.
– **Stay Informed**: Keep abreast of industry trends, technological advancements, and global events that could affect your supply chain.
– **Use Technology**: Utilize advanced data analytics and modeling tools to enhance the accuracy of your scenarios and impact analysis.
– **Regularly Review and Update Plans**: Continuously review and update your contingency plans to ensure they remain relevant and effective.
In conclusion, scenario planning is a valuable tool for procurement risk management, providing organizations with the foresight needed to navigate an increasingly complex global supply chain landscape. By anticipating potential disruptions and developing robust contingency plans, businesses can enhance their resilience, improve decision-making, and maintain a competitive edge.
資料ダウンロード
QCD調達購買管理クラウド「newji」は、調達購買部門で必要なQCD管理全てを備えた、現場特化型兼クラウド型の今世紀最高の購買管理システムとなります。
ユーザー登録
調達購買業務の効率化だけでなく、システムを導入することで、コスト削減や製品・資材のステータス可視化のほか、属人化していた購買情報の共有化による内部不正防止や統制にも役立ちます。
NEWJI DX
製造業に特化したデジタルトランスフォーメーション(DX)の実現を目指す請負開発型のコンサルティングサービスです。AI、iPaaS、および先端の技術を駆使して、製造プロセスの効率化、業務効率化、チームワーク強化、コスト削減、品質向上を実現します。このサービスは、製造業の課題を深く理解し、それに対する最適なデジタルソリューションを提供することで、企業が持続的な成長とイノベーションを達成できるようサポートします。
オンライン講座
製造業、主に購買・調達部門にお勤めの方々に向けた情報を配信しております。
新任の方やベテランの方、管理職を対象とした幅広いコンテンツをご用意しております。
お問い合わせ
コストダウンが利益に直結する術だと理解していても、なかなか前に進めることができない状況。そんな時は、newjiのコストダウン自動化機能で大きく利益貢献しよう!
(Β版非公開)