- お役立ち記事
- Accounting Secrets for Properly Allocating Manufacturing Expenses to Optimize Profit
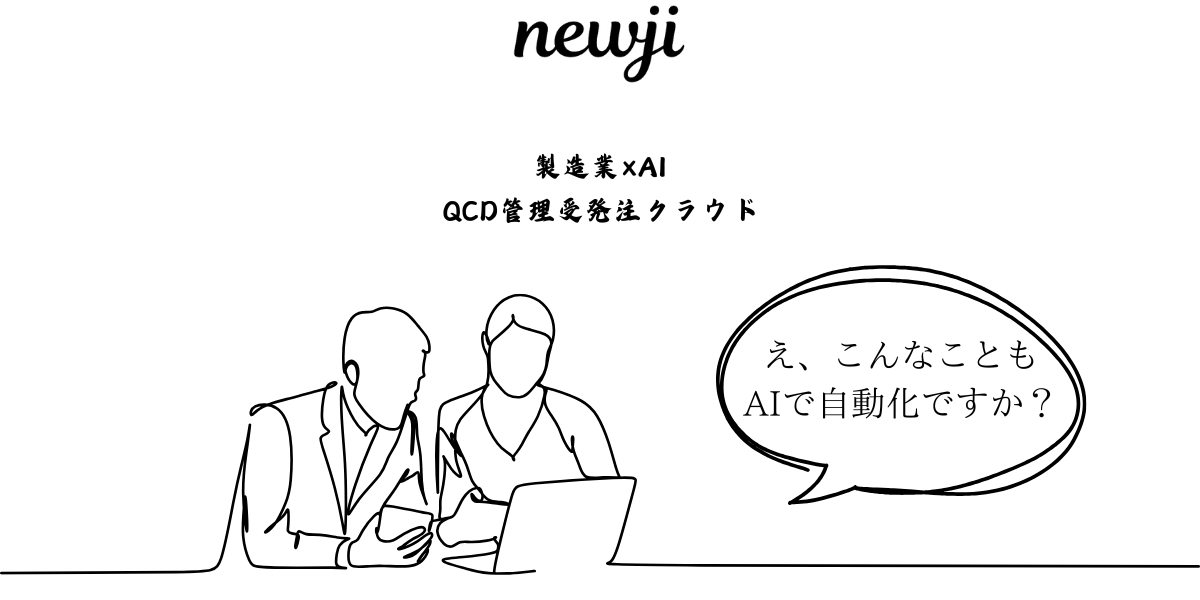
Accounting Secrets for Properly Allocating Manufacturing Expenses to Optimize Profit
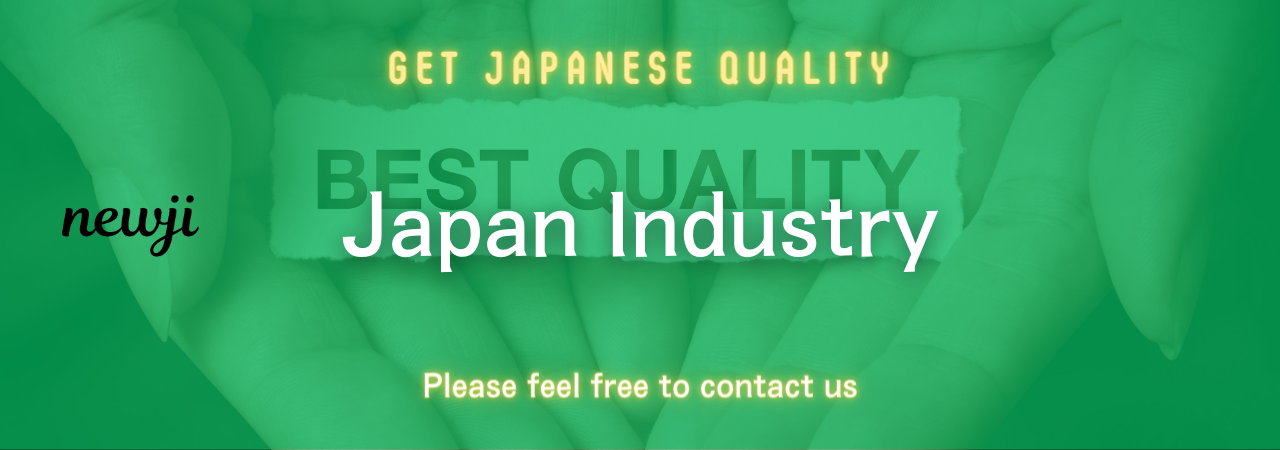
Understanding how to allocate manufacturing expenses properly can significantly impact a company’s profitability.
Manufacturing expenses include all costs directly associated with the production process, such as raw materials, labor, and overhead.
Properly managing these costs ensures that a business can price its products competitively while maintaining a healthy margin.
目次
Why Proper Allocation of Manufacturing Expenses Matters
Proper allocation of manufacturing expenses is critical for a variety of reasons.
First, it helps businesses determine the actual cost of each product they manufacture.
Knowing the exact cost per unit enables better pricing strategies, avoiding underpricing or overpricing.
Additionally, accurate allocation helps in identifying areas where cost savings can be implemented.
By understanding which processes or materials are more expensive, businesses can seek more cost-effective alternatives or streamline operations.
Finally, proper allocation is essential for financial reporting and compliance.
Accurate financial statements are crucial for investors, regulatory bodies, and internal stakeholders.
Main Components of Manufacturing Expenses
To allocate manufacturing expenses effectively, it’s essential to understand the main components:
Direct Materials
Direct materials are the raw materials that can be directly traced to the production of a specific product.
For example, in a furniture manufacturing business, wood and nails would be considered direct materials.
These costs are usually variable, changing with the production volume.
Direct Labor
Direct labor refers to the wages of employees who are directly involved in the production process.
These include workers who operate machinery or assemble products.
Like direct materials, direct labor costs can vary depending on the volume of production.
Manufacturing Overhead
Manufacturing overhead includes all other indirect costs that are necessary for production but cannot be directly traced to a specific product.
These may include electricity for running machines, factory rental, and maintenance of equipment.
Overhead costs are often fixed, remaining constant regardless of production volume.
Methods for Allocating Manufacturing Expenses
Job-Order Costing
Job-order costing is useful when production involves customized or unique products.
It tracks the expenses for each job or order separately.
Under this method, costs are allocated to specific jobs based on the actual usage of resources.
This approach is commonly used in industries like construction and custom manufacturing where products are not standardized.
Process Costing
Process costing is suitable for businesses that produce large volumes of similar products.
Instead of tracking costs per individual job, expenses are spread across all units produced.
This method averages the total costs over the number of units, making it easier to allocate expenses uniformly.
Industries such as chemicals, petroleum, and food manufacturing commonly use process costing.
Activity-Based Costing (ABC)
Activity-based costing provides a more precise allocation by assigning costs to specific activities involved in the production process.
It identifies the activities that contribute to overhead costs and assigns these costs based on the usage of each activity.
This method helps in recognizing inefficiencies and is particularly useful for businesses with diverse products or complex production processes.
Strategies to Optimize Profit through Expense Allocation
Regular Reviewing and Updating Cost Information
Manufacturing environments are dynamic, and costs associated with production can change frequently.
Regularly reviewing and updating cost information ensures that allocations remain accurate.
Monitoring prices of raw materials, labor rates, and overhead costs helps businesses adjust their pricing strategies accordingly.
Implementing Cost-Reduction Measures
Identifying expensive components of the production process provides an opportunity to implement cost-reduction measures.
For instance, negotiating better rates with suppliers or investing in more efficient machinery can lower direct material and labor costs.
Reducing overhead expenses by streamlining processes or adopting energy-efficient practices also enhances profitability.
Investment in Technology
Leveraging advanced manufacturing technologies such as automation and data analytics can help in better allocation of expenses.
Automation reduces direct labor costs and minimizes errors, while data analytics provide deeper insights into cost drivers.
This investment not only optimizes operations but also facilitates more accurate expense tracking and allocation.
Training and Development
An often-overlooked aspect of cost management is the skill level of the workforce.
Investing in employee training and development ensures that workers perform their tasks efficiently, reducing wastage and rework.
Skilled employees are better at using resources productively, which in turn helps in reducing direct labor and material costs.
Common Challenges in Allocating Manufacturing Expenses
Complex Production Processes
When production processes are complex, allocating expenses accurately becomes challenging.
Multiple products and variable costs add layers of difficulty in tracking and assigning costs properly.
Implementing robust accounting systems and methods like activity-based costing can mitigate these challenges.
Fluctuating Costs
Raw material prices, labor rates, and overhead costs can fluctuate, making it hard to maintain consistent expense allocation.
Economic conditions, market demand, and supply chain disruptions are contributing factors.
Regular monitoring and flexible budgeting help in adapting to these changes efficiently.
Data Integrity
Accurate allocation relies on precise data collection and recording.
Inaccurate or incomplete data compromises the effectiveness of the allocation process.
Implementing stringent data management practices, regular audits, and using reliable accounting software can ensure data integrity.
Allocating manufacturing expenses properly is critical for business success.
By understanding the components of these expenses and adopting suitable allocation methods, businesses can optimize their costs and enhance profitability.
Regular reviews, cost-reduction measures, investments in technology, and workforce training are effective strategies to achieve this goal.
Despite challenges like complex production processes and fluctuating costs, businesses can overcome them with robust systems and practices.
Ultimately, efficient expense allocation creates a solid foundation for financial accuracy and competitive advantage.
資料ダウンロード
QCD調達購買管理クラウド「newji」は、調達購買部門で必要なQCD管理全てを備えた、現場特化型兼クラウド型の今世紀最高の購買管理システムとなります。
ユーザー登録
調達購買業務の効率化だけでなく、システムを導入することで、コスト削減や製品・資材のステータス可視化のほか、属人化していた購買情報の共有化による内部不正防止や統制にも役立ちます。
NEWJI DX
製造業に特化したデジタルトランスフォーメーション(DX)の実現を目指す請負開発型のコンサルティングサービスです。AI、iPaaS、および先端の技術を駆使して、製造プロセスの効率化、業務効率化、チームワーク強化、コスト削減、品質向上を実現します。このサービスは、製造業の課題を深く理解し、それに対する最適なデジタルソリューションを提供することで、企業が持続的な成長とイノベーションを達成できるようサポートします。
オンライン講座
製造業、主に購買・調達部門にお勤めの方々に向けた情報を配信しております。
新任の方やベテランの方、管理職を対象とした幅広いコンテンツをご用意しております。
お問い合わせ
コストダウンが利益に直結する術だと理解していても、なかなか前に進めることができない状況。そんな時は、newjiのコストダウン自動化機能で大きく利益貢献しよう!
(Β版非公開)