- お役立ち記事
- Eliminating Work Errors and Halving “Motion and Transport Waste” Through Workbench Kaizen
Eliminating Work Errors and Halving “Motion and Transport Waste” Through Workbench Kaizen
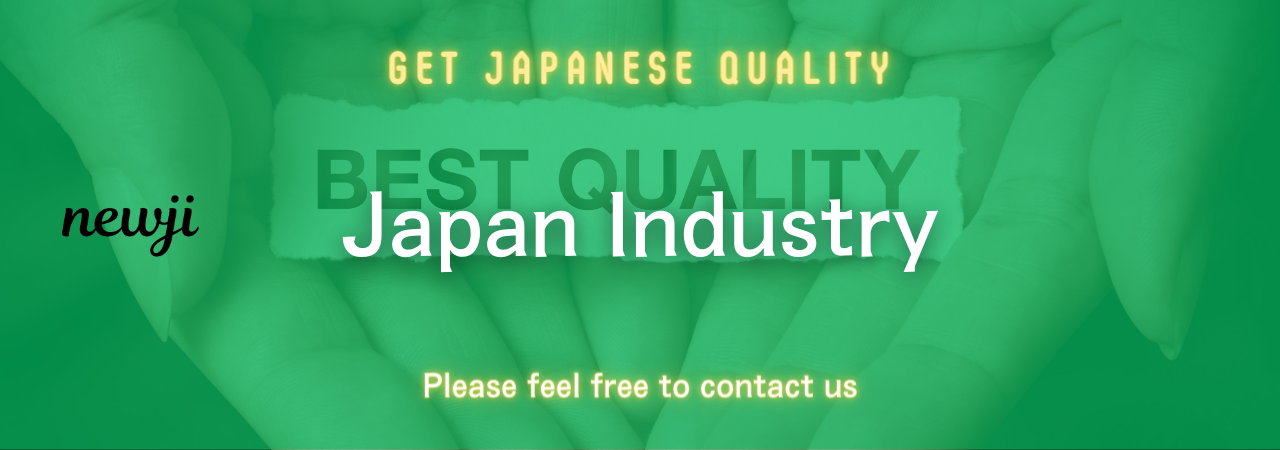
Improving productivity and efficiency in workplaces is crucial for the success of any business.
One strategy that stands out in achieving this is workbench kaizen.
Kaizen, a Japanese term meaning “change for better,” involves making continuous improvements to processes to eliminate waste and optimize performance.
By focusing on workbench kaizen, you can reduce work errors and significantly cut down on motion and transport waste.
This article delves into how implementing workbench kaizen can transform your workspace and boost efficiency.
目次
Understanding Workbench Kaizen
Workbench kaizen specifically targets the immediate work environment of employees.
It aims to streamline activities performed at the workbench by making small, incremental adjustments.
These tweaks can involve rearranging tools, optimizing workflows, and improving ergonomic conditions.
The goal is not to overhaul the entire system in one go, but to continuously search for better ways of doing things.
The Importance of Workbench Kaizen
The concept of kaizen has been used in manufacturing and various industries for decades.
However, its principles are universally applicable.
When applied to workbenches, kaizen can make significant improvements in productivity and efficiency.
Small changes can lead to substantial benefits, such as reducing work errors and minimizing waste.
This, in turn, can lead to happier employees and a more profitable business.
Eliminating Work Errors
Work errors are detrimental because they can slow down production, increase costs, and frustrate employees.
One of the key aspects of workbench kaizen is standardizing tasks to prevent mistakes.
When tasks are standardized, there’s less room for error because everyone knows exactly what is expected of them.
Organizing Tools and Materials
Having tools and materials organized and within easy reach can drastically reduce the chances of errors.
Workers shouldn’t have to search for what they need.
Implementing a designated place for each tool and ensuring it is returned to its place after use is essential.
Labeling shelves and drawers can also make it easier for workers to find what they need quickly.
Streamlining Workflow
Identifying redundant steps in your workflow can significantly reduce errors.
For example, if a task involves multiple handoffs between workers, there’s a higher chance for miscommunication and mistakes.
Reducing these handoffs or simplifying them can streamline operations and decrease errors.
Cutting Down on Motion and Transport Waste
Motion and transport waste refer to unnecessary movements made by workers and the inefficient transport of materials within the workspace.
These types of waste don’t add value to the final product and should be minimized.
Workbench kaizen can help achieve this by optimizing the layout and workflow.
Optimizing Workspace Layout
A well-arranged workspace can minimize unnecessary movement.
Arranging tools and materials in an ergonomic and logical manner ensures that workers can reach what they need with minimal effort.
This can also prevent fatigue and reduce the likelihood of mistakes.
For example, frequently used tools should be placed within arm’s reach, while items used less often can be stored further away.
Improving Ergonomics
Ergonomics is another critical aspect.
Poor ergonomic conditions can lead to physical strain and long-term injuries, which can impact productivity.
Adjusting workbenches to the proper height and ensuring that workers have comfortable seating can improve their efficiency and reduce motion waste.
Investing in ergonomic tools and equipment can have substantial long-term benefits.
Implementing 5S Methodology
The 5S methodology is another tool often used in kaizen efforts:
Sort, Set in order, Shine, Standardize, and Sustain.
Applying this method to workbenches can help in organizing and maintaining a clean and efficient workspace.
Sort involves removing unnecessary items.
Set in order focuses on organizing tools and materials.
Shine means keeping the workspace clean.
Standardize entails maintaining consistency in organizing and cleaning.
Sustain requires regular audits to ensure ongoing compliance.
Case Studies and Examples
Real-life examples can offer valuable insights into how workbench kaizen can lead to significant improvements.
For instance, a manufacturing company implemented workbench kaizen and reduced motion waste by 50%.
They achieved this by reorganizing the layout and standardizing tasks, which also led to a significant decrease in work errors.
Case Study: Manufacturing Excellence
ABC Manufacturing, a medium-sized company, decided to implement workbench kaizen in their assembly line.
By involving employees in the kaizen process, they identified several areas for improvement.
Tools and materials were rearranged to optimize workflow.
Employees were trained to follow standardized procedures.
As a result, the company saw a 30% increase in productivity and a 40% reduction in errors within just three months.
Case Study: Boosting Employee Morale
XYZ Electronics decided to try kaizen to improve their production process.
Employees were encouraged to suggest improvements to their workstations.
One of the suggestions was to install easily accessible tool racks.
This small adjustment reduced motion waste and improved morale, as workers felt their contributions were valued.
In six months, XYZ saw a 20% reduction in production time and reported higher job satisfaction among employees.
Getting Started with Workbench Kaizen
Starting with workbench kaizen doesn’t require a significant investment.
Involve your employees in the process and encourage them to suggest improvements.
Begin with small changes and monitor their impact.
Regularly review and adjust the changes based on feedback and observed outcomes.
Employee Involvement
For workbench kaizen to be successful, it is crucial to involve employees.
They are the ones who understand the nuances of their daily tasks and can provide valuable insights.
Encourage them to voice their suggestions and create a culture of continuous improvement.
Monitor and Measure
Track the impact of the changes you implement.
Use performance metrics and employee feedback to assess the effectiveness of the kaizen efforts.
Regularly review these metrics and make necessary adjustments to ensure ongoing improvements.
Conclusion
Workbench kaizen offers a practical and cost-effective strategy for improving efficiency and reducing errors in the workplace.
By involving employees, standardizing tasks, organizing tools, and optimizing workflows, you can significantly cut down on motion and transport waste.
The result is a more streamlined, productive, and happy workspace.
Start small, encourage continuous improvement, and watch your productivity soar.
資料ダウンロード
QCD調達購買管理クラウド「newji」は、調達購買部門で必要なQCD管理全てを備えた、現場特化型兼クラウド型の今世紀最高の購買管理システムとなります。
ユーザー登録
調達購買業務の効率化だけでなく、システムを導入することで、コスト削減や製品・資材のステータス可視化のほか、属人化していた購買情報の共有化による内部不正防止や統制にも役立ちます。
NEWJI DX
製造業に特化したデジタルトランスフォーメーション(DX)の実現を目指す請負開発型のコンサルティングサービスです。AI、iPaaS、および先端の技術を駆使して、製造プロセスの効率化、業務効率化、チームワーク強化、コスト削減、品質向上を実現します。このサービスは、製造業の課題を深く理解し、それに対する最適なデジタルソリューションを提供することで、企業が持続的な成長とイノベーションを達成できるようサポートします。
オンライン講座
製造業、主に購買・調達部門にお勤めの方々に向けた情報を配信しております。
新任の方やベテランの方、管理職を対象とした幅広いコンテンツをご用意しております。
お問い合わせ
コストダウンが利益に直結する術だと理解していても、なかなか前に進めることができない状況。そんな時は、newjiのコストダウン自動化機能で大きく利益貢献しよう!
(Β版非公開)