- お役立ち記事
- What is Industry 4.0? Decoding the Digital Revolution in Manufacturing
What is Industry 4.0? Decoding the Digital Revolution in Manufacturing
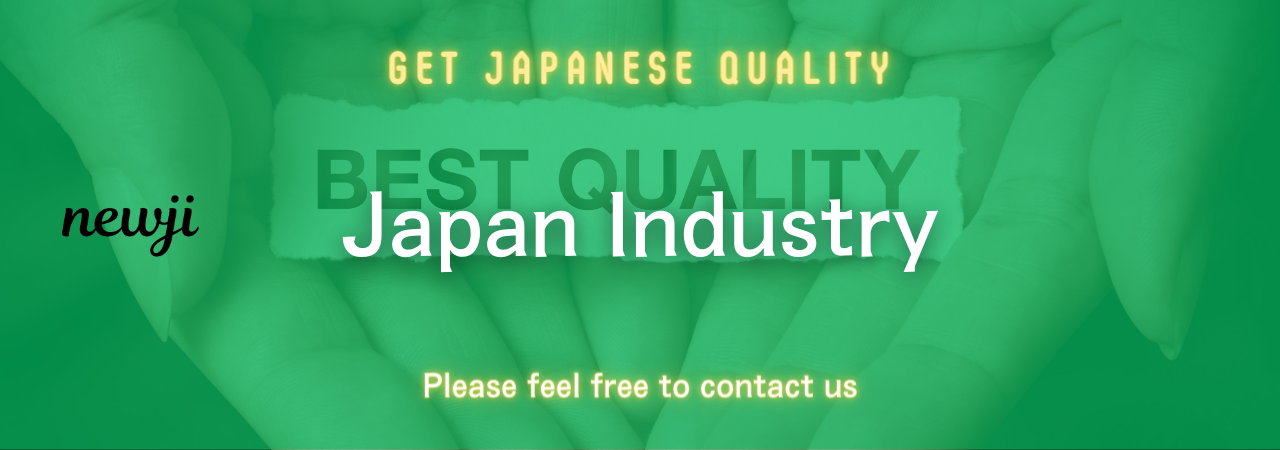
Industry 4.0 represents the fourth industrial revolution, a paradigm shift in manufacturing driven by digital transformation technologies.
From steam engines to electric power and digital computing, each industrial revolution has escalated productivity and efficiency, redefining how the world works.
With Industry 4.0, the manufacturing sector is experiencing a massive overhaul, characterized by smart factories and interconnected systems.
目次
The Core Components of Industry 4.0
Industry 4.0 is built on several key pillars.
Understanding these components is crucial to grasp the magnitude of the transformation happening in manufacturing.
Internet of Things (IoT)
IoT refers to the network of physical objects embedded with sensors, software, and other technologies to communicate and exchange data with other devices and systems over the internet.
In manufacturing, IoT enables machines to collect and share data, leading to improved efficiency, reduced downtime, and predictive maintenance.
Big Data and Analytics
With the proliferation of sensors and connected devices, immense volumes of data are generated.
Big Data analytics helps in extracting actionable insights from this data.
Manufacturers can optimize processes, enhance product quality, and predict equipment failures before they occur through data-driven decision-making.
Artificial Intelligence (AI) and Machine Learning (ML)
AI and ML are critical to Industry 4.0 as they enable machines to perform tasks that typically require human intelligence.
By analyzing data patterns, AI and ML can make autonomous decisions, improving operational efficiencies and enabling personalized manufacturing.
Cyber-Physical Systems (CPS)
Cyber-physical systems are integrations of computation, networking, and physical processes.
In a CPS, mechanisms are controlled or monitored by algorithms tightly integrated with the internet and its users.
These systems enhance real-time control and automation in manufacturing environments.
Robotics and Automation
Advanced robotics and automation play a significant role in Industry 4.0.
Robots are now more intelligent, versatile, and collaborative.
They can work alongside human workers, adapting to new tasks and environments, thus increasing productivity and safety.
Benefits of Industry 4.0
The adoption of Industry 4.0 brings numerous benefits to manufacturing.
Increased Efficiency
By integrating advanced technologies, manufacturers can streamline operations and reduce waste.
Automation and IoT systems ensure machines operate at optimal levels, minimizing downtime and maximizing productivity.
Enhanced Product Quality
Industry 4.0 enables real-time monitoring and quality control.
Manufacturers can detect defects early and take corrective actions promptly, resulting in higher-quality products and reduced scrap rates.
Cost Reduction
Automation and predictive maintenance significantly reduce operational costs.
Predictive analytics help in scheduling maintenance activities only when necessary, extending equipment lifespan and cutting down unexpected downtimes.
Flexibility and Customization
Smart factories provide the flexibility to adapt to changing market demands.
Manufacturers can switch production lines quickly, allowing for mass customization and meeting specific customer requirements efficiently.
Improved Safety
Robotic systems can undertake hazardous tasks, reducing the risk of accidents and ensuring a safer working environment for humans.
IoT devices also monitor real-time conditions, alerting workers about potential dangers.
Challenges in Implementing Industry 4.0
Despite its advantages, the transition to Industry 4.0 presents several challenges.
High Initial Investment
The implementation of advanced technologies requires substantial capital investment.
Small and medium-sized enterprises (SMEs) may struggle with the financial burden of upgrading legacy systems to smart manufacturing facilities.
Data Security and Privacy
With increased connectivity comes greater susceptibility to cyber-attacks.
Ensuring data security and safeguarding intellectual property in a highly interconnected digital ecosystem is paramount.
Skill Gap
The shift to Industry 4.0 necessitates a workforce proficient in digital skills and advanced technologies.
There is an urgent need for training and education programs to bridge the skill gap and prepare employees for the future job market.
Interoperability Issues
Integrating various systems and devices from different manufacturers can lead to interoperability problems.
Standards and protocols need to be established to ensure seamless communication and data exchange across the entire manufacturing ecosystem.
Future Trends in Industry 4.0
The journey of Industry 4.0 is continuously evolving.
Here are some emerging trends shaping its future.
5G Connectivity
5G technology promises ultra-fast data transfer speeds and low latency.
This will enhance real-time communication between IoT devices, enabling more sophisticated data analysis and decision-making processes.
Edge Computing
Edge computing brings data processing closer to the source of data generation.
By reducing the need to transfer data to centralized servers, edge computing offers faster and more efficient data analysis, crucial for real-time applications in manufacturing.
Augmented Reality (AR) and Virtual Reality (VR)
AR and VR technologies are increasingly being used in training, maintenance, and design processes.
They allow workers to visualize complex data, simulate real-life scenarios, and gain hands-on experience without physical risks.
Blockchain Technology
Blockchain offers transparent and tamper-proof record-keeping.
In manufacturing, it ensures the integrity and traceability of supply chains, helping in fraud prevention, product authenticity verification, and simplifying audits and compliance procedures.
In conclusion, Industry 4.0 is transforming the manufacturing landscape by leveraging advanced digital technologies.
While it offers tremendous benefits in terms of efficiency, quality, and customization, it also presents challenges in terms of investment, security, and skill requirements.
As technologies evolve, the future of manufacturing will undoubtedly become smarter, more connected, and highly adaptive.
資料ダウンロード
QCD調達購買管理クラウド「newji」は、調達購買部門で必要なQCD管理全てを備えた、現場特化型兼クラウド型の今世紀最高の購買管理システムとなります。
ユーザー登録
調達購買業務の効率化だけでなく、システムを導入することで、コスト削減や製品・資材のステータス可視化のほか、属人化していた購買情報の共有化による内部不正防止や統制にも役立ちます。
NEWJI DX
製造業に特化したデジタルトランスフォーメーション(DX)の実現を目指す請負開発型のコンサルティングサービスです。AI、iPaaS、および先端の技術を駆使して、製造プロセスの効率化、業務効率化、チームワーク強化、コスト削減、品質向上を実現します。このサービスは、製造業の課題を深く理解し、それに対する最適なデジタルソリューションを提供することで、企業が持続的な成長とイノベーションを達成できるようサポートします。
オンライン講座
製造業、主に購買・調達部門にお勤めの方々に向けた情報を配信しております。
新任の方やベテランの方、管理職を対象とした幅広いコンテンツをご用意しております。
お問い合わせ
コストダウンが利益に直結する術だと理解していても、なかなか前に進めることができない状況。そんな時は、newjiのコストダウン自動化機能で大きく利益貢献しよう!
(Β版非公開)