- お役立ち記事
- How to Utilize QFD to Enhance Manufacturing Competitiveness: From Basics to Applications
How to Utilize QFD to Enhance Manufacturing Competitiveness: From Basics to Applications
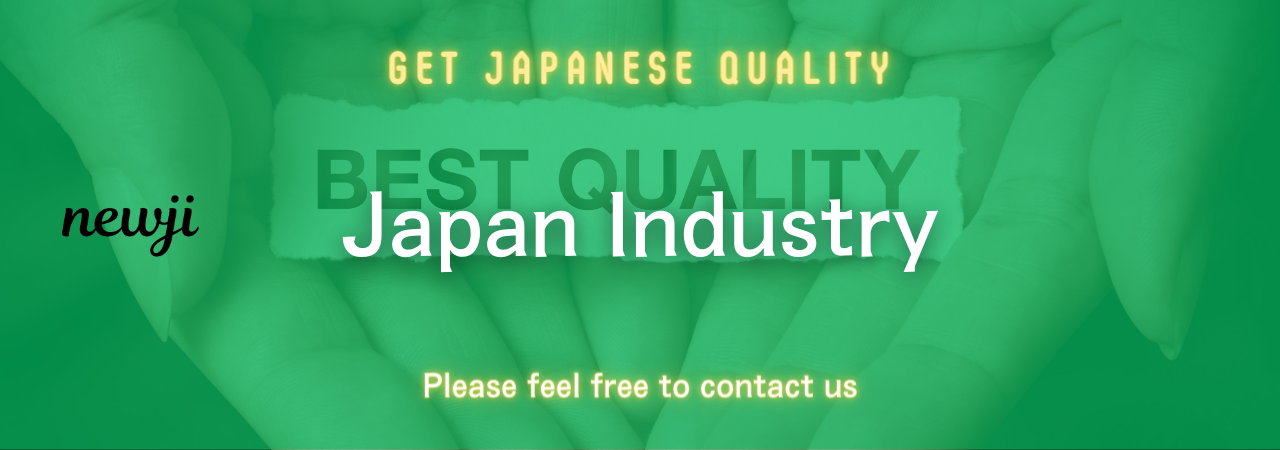
Quality Function Deployment (QFD) is a powerful methodology that can significantly enhance manufacturing competitiveness.
It systematically transforms customer needs into detailed design specifications.
In simple terms, QFD ensures that the voice of the customer is heard and addressed throughout the product development process.
By integrating QFD, manufacturers can produce high-quality products that meet or exceed customer expectations, ensuring market success.
目次
Understanding the Basics of QFD
Quality Function Deployment is often visualized through a tool known as the “House of Quality.”
The House of Quality is a matrix that helps teams translate customer requirements (what the customer wants) into engineering characteristics (how the company can provide it).
This structured approach ensures that every stage of product development aligns with customer needs, ensuring quality and satisfaction.
The House of Quality Explained
Imagine a house-like diagram.
On the left side, you list customer requirements.
On the top, you list technical requirements—specific features or characteristics of the product.
By mapping customer needs to technical specifications, you can clearly see how different requirements relate to one another.
This graphical representation fosters cross-functional teamwork and communication.
Benefits of QFD
Implementing QFD in manufacturing offers several advantages:
1. **Enhanced Communication**: QFD requires input from various departments, fostering better communication and collaboration.
2. **Customer-Centric Products**: By prioritizing customer needs, companies can ensure that their products are better aligned with market demands.
3. **Reduced Costs**: By identifying potential issues early in the process, manufacturers can avoid costly design changes down the line.
4. **Improved Quality**: With clear specifications and requirements, the chance of producing high-quality products increases.
Steps to Implement QFD in Manufacturing
Successfully integrating QFD into your manufacturing process involves several critical steps.
Understanding these steps will help you seamlessly incorporate QFD into your existing workflows.
Step 1: Establish a Cross-Functional Team
QFD thrives on collaboration.
Assemble a team that includes members from various departments: marketing, design, engineering, and production.
Diverse perspectives ensure that all aspects of the product are considered.
Step 2: Identify Customer Needs
The foundation of QFD lies in understanding what your customers want.
Conduct thorough market research, surveys, and interviews to gather comprehensive data.
List these customer needs clearly.
Step 3: Prioritize Customer Needs
Not all customer requirements are created equal.
Some needs will be more critical than others.
Use methods such as the Pareto principle (80/20 rule) or customer segmentation to prioritize these needs.
Focus on the most impactful requirements first.
Step 4: Develop the House of Quality
Once you have a prioritized list of customer needs, translate these into specific technical requirements.
Place these needs on the left side of your House of Quality and the technical specifications across the top.
Clearly define the relationship between customer needs and technical requirements through the matrix.
Step 5: Analyze and Optimize
With the House of Quality complete, analyze it to identify areas for improvement.
Look for opportunities to enhance product features while considering cost and feasibility.
Adjust your design and manufacturing processes accordingly.
Step 6: Monitor and Iterate
QFD is not a one-time process.
Continuous monitoring and iteration are essential.
Gather feedback from customers and use this data to refine your product.
Regularly update your House of Quality to reflect any changes in customer preferences or market trends.
Real-World Applications of QFD
Understanding how QFD applies in real-world scenarios can provide deeper insights into its practical benefits.
Case Study: Automotive Industry
One notable application of QFD is within the automotive industry.
Car manufacturers have successfully utilized QFD to improve vehicle design and production.
By integrating customer feedback, automotive companies can introduce features highly valued by drivers, such as enhanced safety systems and fuel efficiency.
This customer-centric approach has led to increased customer loyalty and market share.
Case Study: Electronics Manufacturing
Electronics manufacturers, particularly in the competitive smartphone market, have leveraged QFD to stay ahead.
By continuously addressing customer demands for better camera quality, longer battery life, and sleek designs, these companies remain competitive.
The systematic incorporation of QFD ensures they can swiftly respond to evolving market trends.
Conclusion
Quality Function Deployment is an invaluable tool for enhancing manufacturing competitiveness.
By systematically translating customer needs into tangible product specifications, manufacturers can produce goods that excel in quality and marketability.
The collaborative nature of QFD fosters better communication and teamwork across different departments.
Its continuous feedback loop allows companies to stay agile and responsive to market changes.
By implementing the steps outlined—forming cross-functional teams, identifying and prioritizing customer needs, developing the House of Quality, and continuously monitoring—the path to improved products and satisfied customers is clear.
Real-world applications, whether in the automotive or electronics industry, demonstrate QFD’s practical benefits.
Embracing QFD can be the key to achieving a competitive edge in today’s ever-evolving marketplace.
資料ダウンロード
QCD調達購買管理クラウド「newji」は、調達購買部門で必要なQCD管理全てを備えた、現場特化型兼クラウド型の今世紀最高の購買管理システムとなります。
ユーザー登録
調達購買業務の効率化だけでなく、システムを導入することで、コスト削減や製品・資材のステータス可視化のほか、属人化していた購買情報の共有化による内部不正防止や統制にも役立ちます。
NEWJI DX
製造業に特化したデジタルトランスフォーメーション(DX)の実現を目指す請負開発型のコンサルティングサービスです。AI、iPaaS、および先端の技術を駆使して、製造プロセスの効率化、業務効率化、チームワーク強化、コスト削減、品質向上を実現します。このサービスは、製造業の課題を深く理解し、それに対する最適なデジタルソリューションを提供することで、企業が持続的な成長とイノベーションを達成できるようサポートします。
オンライン講座
製造業、主に購買・調達部門にお勤めの方々に向けた情報を配信しております。
新任の方やベテランの方、管理職を対象とした幅広いコンテンツをご用意しております。
お問い合わせ
コストダウンが利益に直結する術だと理解していても、なかなか前に進めることができない状況。そんな時は、newjiのコストダウン自動化機能で大きく利益貢献しよう!
(Β版非公開)