- お役立ち記事
- Mastering Corrosion Tests in Japanese Manufacturing: An In-Depth Guide
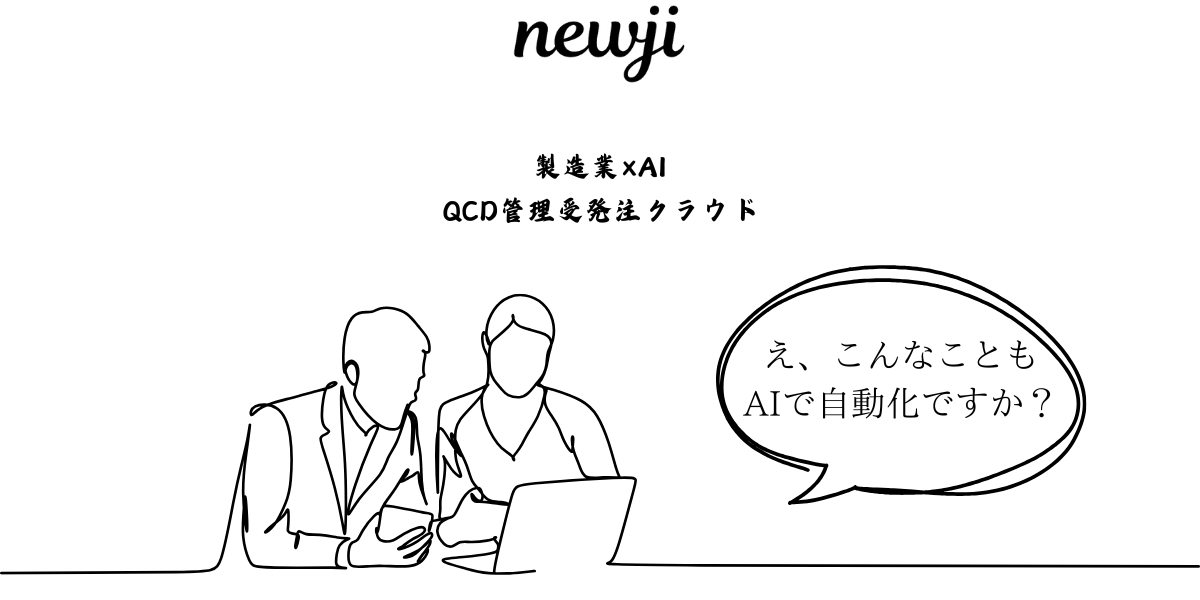
Mastering Corrosion Tests in Japanese Manufacturing: An In-Depth Guide
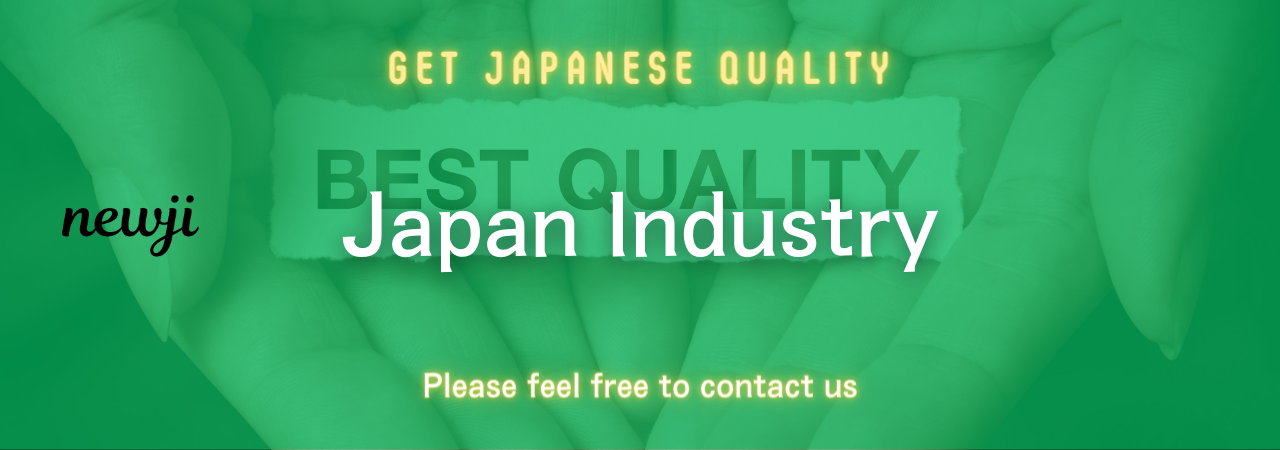
目次
Introduction to Corrosion Testing in Japanese Manufacturing
Corrosion poses a significant threat to the longevity and performance of manufactured products.
Historically, Japan has been at the forefront of industrial progress, with Japanese manufacturing companies setting global standards in quality and innovation.
This leadership extends to their expertise in corrosion testing methods, which are indispensable for ensuring the durability and reliability of materials and products.
In this article, we delve into the various aspects of mastering corrosion tests in Japanese manufacturing, including practical insights from the field, advantages and disadvantages, supplier negotiation techniques, market conditions, and best practices.
The Importance of Corrosion Testing in Manufacturing
Corrosion can lead to catastrophic failures in a variety of industries, from automotive to aerospace and electronics to infrastructure.
Therefore, it is crucial to implement comprehensive corrosion testing processes to preemptively identify potential risks.
In Japanese manufacturing, the emphasis on meticulous quality control and continuous improvement (Kaizen) underscores the importance of advanced corrosion testing.
Types of Corrosion and Corresponding Tests
Different types of corrosion require specific testing methods to accurately assess their impact.
Here are some of the most common types of corrosion and the corresponding tests:
1. **Uniform Corrosion**:
– **Salt Spray Test**: This accelerated corrosion test exposes samples to a salt-laden spray, simulating harsh marine environments.
It provides an indication of materials’ resistance to uniform corrosion.
– **Immersion Test**: Samples are submerged in corrosive solutions to observe the rate and nature of corrosion over a specified period.
2. **Pitting Corrosion**:
– **Potentiodynamic Polarization Test**: This electrochemical method evaluates the susceptibility of materials to localized pitting by monitoring their response to an applied potential.
3. **Galvanic Corrosion**:
– **Galvanic Corrosion Test**: It involves connecting two dissimilar metals in a corrosive environment and measuring the resulting corrosion rates.
4. **Stress Corrosion Cracking**:
– **Slow Strain Rate Testing (SSRT)**: This test measures the resistance of materials to cracking under stress and corrosive conditions.
Advantages and Disadvantages of Corrosion Testing in Japan
Engaging with Japanese suppliers for corrosion testing brings several benefits, though it also presents certain challenges.
Advantages
1. **Technological Expertise**:
Japanese manufacturing companies are known for their cutting-edge technology and rigorous testing protocols.
Their expertise ensures high accuracy and reliability in test results.
2. **Quality Assurance**:
The principles of Total Quality Management (TQM) are deeply ingrained in Japanese manufacturing culture.
This commitment guarantees that corrosion tests are part of a broader quality assurance framework, enhancing product reliability.
3. **Advanced Facilities**:
Japan boasts state-of-the-art laboratories equipped with the latest testing equipment.
These advanced facilities contribute to more precise and comprehensive corrosion assessments.
4. **Regulatory Compliance**:
Japanese manufacturers adhere strictly to domestic and international standards, ensuring that the test results are globally recognized and accepted.
Disadvantages
1. **Cost**:
High-quality testing often comes at a premium price.
Japanese testing services might be more expensive compared to those in other regions.
2. **Logistics**:
Coordinating shipments of samples to and from Japan may incur additional logistics costs and time delays.
3. **Language Barrier**:
Although many Japanese professionals are proficient in English, language differences can sometimes lead to miscommunication and misunderstanding of technical details.
Supplier Negotiation Techniques
Effective negotiation with Japanese suppliers can ensure favorable terms and foster long-term partnerships.
Here are some techniques to consider:
Building Relationships (Nemawashi)
In Japanese business culture, the concept of nemawashi—informal groundwork or consensus-building—is crucial.
Before formal negotiations, engage in preliminary discussions to understand the supplier’s perspective and to lay the foundation for a mutually beneficial agreement.
Building trust through consistent communication is key.
Understanding Cultural Nuances
Respecting Japanese culture and business etiquette can greatly enhance negotiation outcomes.
Punctuality, politeness, and a humble approach are highly valued.
Refrain from aggressive tactics; instead, focus on collaborative problem-solving.
Clarity and Preparation
Be clear about your requirements and expectations.
Provide detailed documentation and clearly define the standards and specifications for corrosion tests.
Demonstrating thorough preparation signals your seriousness and commitment, which is appreciated by Japanese suppliers.
Current Market Conditions
Understanding market conditions can help in making informed procurement decisions.
Here’s an overview of the current market landscape for corrosion testing in Japan:
Technological Innovations
Japanese companies are continually investing in research and development to enhance corrosion testing methodologies.
Innovations such as non-destructive testing (NDT) techniques and advanced simulation models are gaining traction.
These technologies improve the precision and efficiency of corrosion assessments.
Industry Trends
The push towards sustainability is driving the development of eco-friendly corrosion inhibitors and coatings.
Additionally, there is a growing emphasis on digitalization, with more companies adopting IoT and AI technologies to monitor and predict corrosion in real-time.
Regulatory Changes
Japan’s stringent environmental regulations influence the materials and methods used in corrosion testing.
Staying abreast of these regulatory changes ensures compliance and helps anticipate future trends.
Best Practices in Corrosion Testing
Implementing best practices can optimize the corrosion testing process and ensure reliable results.
Here are some recommendations:
Comprehensive Sample Preparation
Accurate corrosion testing begins with proper sample preparation.
Ensure that samples are clean, free of contaminants, and representative of the material to be tested.
Consistent sample preparation protocols yield more reliable and repeatable results.
Regular Calibration of Equipment
To maintain the accuracy of test results, regularly calibrate testing equipment.
Adhere to manufacturers’ guidelines for calibration frequency and procedures.
Keeping equipment in peak condition minimizes measurement errors.
Data Analysis and Interpretation
Invest time in analyzing and interpreting test data thoroughly.
Look for patterns and anomalies that could indicate potential issues.
Utilize advanced software tools to assist in data analysis and generate comprehensive reports.
Continuous Improvement
Adopt a mindset of continuous improvement in your corrosion testing processes.
Regularly review and update testing protocols based on the latest industry standards and technological advancements.
Engage in knowledge sharing and training to keep your team updated on best practices.
Conclusion
Mastering corrosion tests in Japanese manufacturing requires a combination of technical expertise, cultural understanding, and strategic negotiation.
By leveraging the technological strengths and rigorous quality standards of Japanese suppliers, businesses can significantly enhance the durability and reliability of their products.
Understanding the advantages and potential challenges, keeping abreast of market conditions, and implementing best practices are essential steps in achieving mastery in corrosion testing.
With the right approach, you can harness the full potential of Japanese manufacturing expertise, ensuring long-lasting and high-performing products.
資料ダウンロード
QCD調達購買管理クラウド「newji」は、調達購買部門で必要なQCD管理全てを備えた、現場特化型兼クラウド型の今世紀最高の購買管理システムとなります。
ユーザー登録
調達購買業務の効率化だけでなく、システムを導入することで、コスト削減や製品・資材のステータス可視化のほか、属人化していた購買情報の共有化による内部不正防止や統制にも役立ちます。
NEWJI DX
製造業に特化したデジタルトランスフォーメーション(DX)の実現を目指す請負開発型のコンサルティングサービスです。AI、iPaaS、および先端の技術を駆使して、製造プロセスの効率化、業務効率化、チームワーク強化、コスト削減、品質向上を実現します。このサービスは、製造業の課題を深く理解し、それに対する最適なデジタルソリューションを提供することで、企業が持続的な成長とイノベーションを達成できるようサポートします。
オンライン講座
製造業、主に購買・調達部門にお勤めの方々に向けた情報を配信しております。
新任の方やベテランの方、管理職を対象とした幅広いコンテンツをご用意しております。
お問い合わせ
コストダウンが利益に直結する術だと理解していても、なかなか前に進めることができない状況。そんな時は、newjiのコストダウン自動化機能で大きく利益貢献しよう!
(Β版非公開)