- お役立ち記事
- Unveiling the Powerhouse: How Functional Evaluation Transforms Japanese Manufacturing Excellence
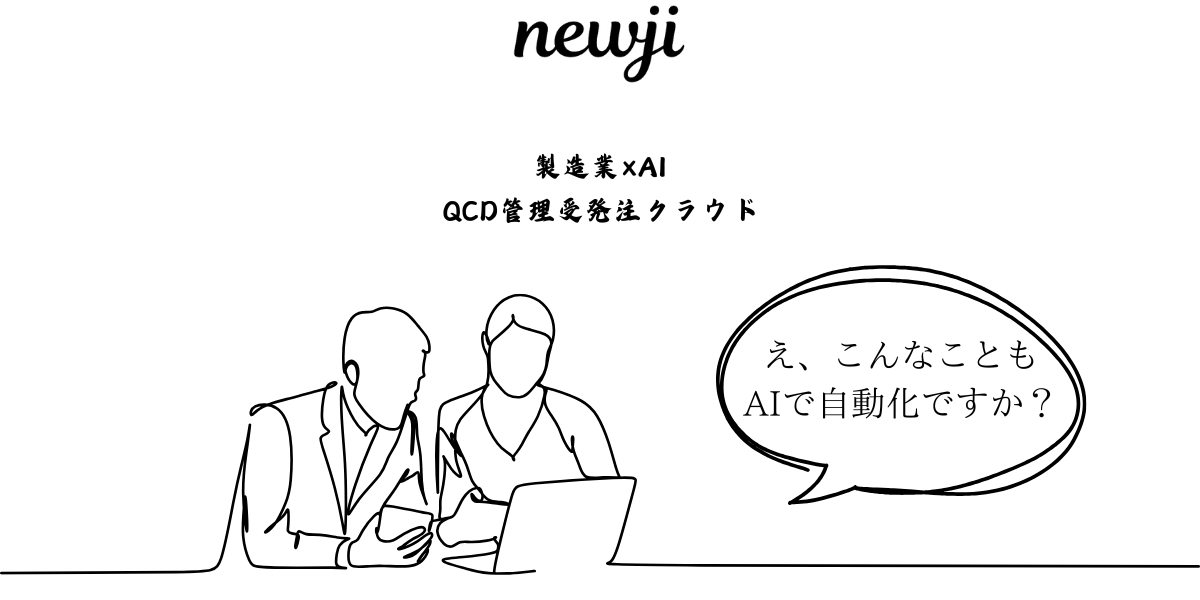
Unveiling the Powerhouse: How Functional Evaluation Transforms Japanese Manufacturing Excellence
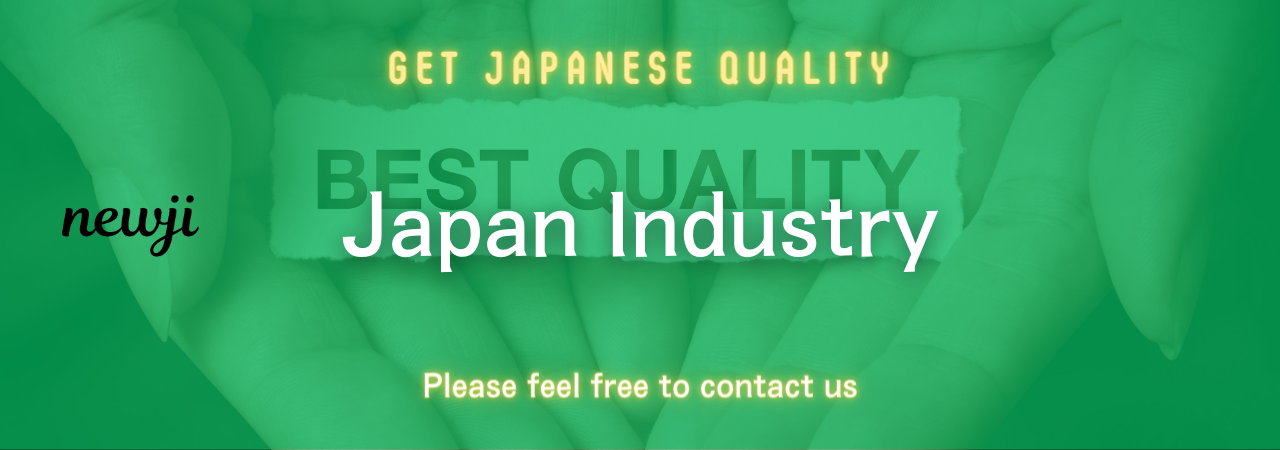
Working in international procurement and purchasing for over two decades has provided me with the opportunity to delve deeply into the nuances of global trade.
Among the plethora of suppliers I’ve worked with, Japanese manufacturing companies have consistently stood out for their quality, discipline, and innovation.
Understanding the importance of functional evaluation is crucial to leveraging the full potential of Japanese manufacturing.
目次
The Essence of Functional Evaluation
Functional evaluation refers to the systematic process of assessing a product or component’s performance, reliability, and efficiency.
In Japanese manufacturing, this concept extends beyond mere technical specifications to include an in-depth analysis of the practical utility and longevity of the product.
It is the cornerstone upon which Japanese manufacturers build their reputation for excellence.
Advantages of Functional Evaluation in Japanese Manufacturing
Functional evaluation offers numerous benefits, which have propelled Japanese manufacturing to the forefront of global industry.
Here are some key advantages:
1. **Enhanced Product Quality:** Japanese manufacturers employ stringent functional evaluations to ensure that every product meets high-quality standards. This focus on quality minimizes defects and customer complaints.
2. **Improved Reliability:** Through rigorous testing, Japanese companies can guarantee the reliability and durability of their products. This is crucial for industries where equipment failure is not an option.
3. **Cost-Efficiency:** While the initial costs of extensive functional evaluations can be high, they lead to long-term cost savings by reducing recalls, repairs, and replacements.
4. **Innovation:** Japanese manufacturers leverage insights from functional evaluations to drive innovation. By understanding how their products perform in real-world conditions, they can make informed decisions about design improvements and new product development.
5. **Customer Satisfaction:** Consistently delivering high-quality, reliable products fosters customer loyalty and trust, which are invaluable in maintaining long-term business relationships.
Disadvantages of Functional Evaluation
While functional evaluation has clear benefits, it’s also important to consider its potential downsides:
1. **Time-Consuming:** The thorough nature of functional evaluations means that they can be time-consuming. This can delay product launches and slow down the production process.
2. **High Initial Costs:** The resources required for comprehensive functional evaluations can be significant, including specialized equipment and skilled personnel.
3. **Complexity:** Implementing functional evaluations requires a high level of technical expertise and coordination across different departments.
4. **Risk of Over-Engineering:** There’s a risk that products may become over-engineered in pursuit of perfection, leading to unnecessary cost increases.
Supplier Negotiation Techniques with Japanese Manufacturers
Negotiating with Japanese suppliers requires a nuanced understanding of their culture and business practices.
Here are some effective techniques:
Build Strong Relationships
Japanese business culture places a high value on relationships.
Take the time to build trust and rapport with your suppliers.
Regular visits and face-to-face meetings can go a long way in strengthening these relationships.
Emphasize Quality
Japanese manufacturers pride themselves on quality.
Highlighting your company’s commitment to quality can resonate well with Japanese suppliers and facilitate smoother negotiations.
Be Patient
Japanese negotiation processes can be slower compared to Western standards.
Be patient and understand that decisions often go through multiple layers of approval.
Understand Their Needs
Take the time to understand your supplier’s needs and constraints.
This can help you propose mutually beneficial solutions and improve the likelihood of a successful negotiation.
Clear Communication
Clear and precise communication is essential.
Misunderstandings can easily arise, so ensure that all terms and conditions are explicitly stated and agreed upon.
Market Conditions and Japanese Suppliers
The global market landscape is constantly evolving, and Japanese suppliers are not immune to these changes.
Here are some current market conditions affecting Japanese suppliers:
Global Supply Chain Disruptions
The COVID-19 pandemic has caused significant disruptions to global supply chains.
Japanese manufacturers have faced challenges such as delays in raw material supplies and increased shipping costs.
However, their ability to adapt and innovate has helped them maintain a competitive edge.
Technological Advancements
Japanese manufacturers are at the forefront of adopting new technologies such as IoT, AI, and robotics.
These advancements have enabled them to improve production efficiency and maintain high-quality standards.
Environmental Regulations
Stringent environmental regulations in Japan have led to a focus on sustainable manufacturing practices.
Japanese suppliers are increasingly adopting eco-friendly production methods and materials to comply with these regulations.
Best Practices for Working with Japanese Suppliers
To maximize the benefits of working with Japanese suppliers, consider the following best practices:
Conduct Thorough Research
Before engaging with a Japanese supplier, conduct thorough research to understand their capabilities, strengths, and areas for improvement.
This knowledge will enable you to make informed decisions and identify potential areas for collaboration.
Focus on Long-Term Partnerships
Japanese suppliers value long-term partnerships over short-term gains.
Demonstrating a commitment to a sustained relationship can enhance trust and result in better cooperation.
Invest in Quality Control
Investing in quality control processes is essential when working with Japanese suppliers.
Ensure that your quality standards are aligned and that both parties are committed to maintaining high-quality production.
Leverage Continuous Improvement
Adopt a culture of continuous improvement (Kaizen) to foster innovation and efficiency in your collaborations with Japanese suppliers.
Encourage regular reviews and feedback to identify areas for enhancement.
Respect Cultural Differences
Understanding and respecting cultural differences is crucial.
For example, hierarchy and formality play significant roles in Japanese business culture.
Being mindful of these nuances can facilitate smoother interactions and stronger relationships.
Case Study: Success Story with a Japanese Supplier
To illustrate the power of functional evaluation and best practices in action, let’s explore a success story involving a Japanese supplier.
Background
Our company, a global electronics manufacturer, faced challenges with the reliability of a key component used in one of our flagship products.
We decided to partner with a renowned Japanese supplier known for its meticulous functional evaluations and high-quality standards.
Implementation
We commenced with a comprehensive supplier audit to understand their processes and capabilities.
Our team collaborated closely with the supplier to define stringent quality criteria and performance metrics.
The supplier conducted extensive functional evaluations, including stress testing, environmental simulations, and real-world usage scenarios.
Outcomes
The results were remarkable.
The component’s reliability improved significantly, leading to a 50% reduction in warranty claims.
Customer satisfaction scores for the product increased, resulting in higher sales and market share.
This partnership also fostered innovation, with the supplier providing valuable insights for future product enhancements.
Conclusion
Unveiling the powerhouse of functional evaluation in Japanese manufacturing reveals a pathway to unparalleled excellence.
While there are challenges and complexities associated with this approach, the benefits far outweigh the drawbacks.
By understanding the nuances of supplier negotiation, staying attuned to market conditions, and adopting best practices, companies can harness the full potential of Japanese suppliers.
Through strong partnerships built on trust, mutual respect, and a shared commitment to quality, businesses can achieve remarkable success and drive innovation in an increasingly competitive global market.
It’s not just about procuring components; it’s about building a legacy of excellence that stands the test of time.
資料ダウンロード
QCD調達購買管理クラウド「newji」は、調達購買部門で必要なQCD管理全てを備えた、現場特化型兼クラウド型の今世紀最高の購買管理システムとなります。
ユーザー登録
調達購買業務の効率化だけでなく、システムを導入することで、コスト削減や製品・資材のステータス可視化のほか、属人化していた購買情報の共有化による内部不正防止や統制にも役立ちます。
NEWJI DX
製造業に特化したデジタルトランスフォーメーション(DX)の実現を目指す請負開発型のコンサルティングサービスです。AI、iPaaS、および先端の技術を駆使して、製造プロセスの効率化、業務効率化、チームワーク強化、コスト削減、品質向上を実現します。このサービスは、製造業の課題を深く理解し、それに対する最適なデジタルソリューションを提供することで、企業が持続的な成長とイノベーションを達成できるようサポートします。
オンライン講座
製造業、主に購買・調達部門にお勤めの方々に向けた情報を配信しております。
新任の方やベテランの方、管理職を対象とした幅広いコンテンツをご用意しております。
お問い合わせ
コストダウンが利益に直結する術だと理解していても、なかなか前に進めることができない状況。そんな時は、newjiのコストダウン自動化機能で大きく利益貢献しよう!
(Β版非公開)