- お役立ち記事
- Overcoming the Digital Skills Gap in Manufacturing
Overcoming the Digital Skills Gap in Manufacturing
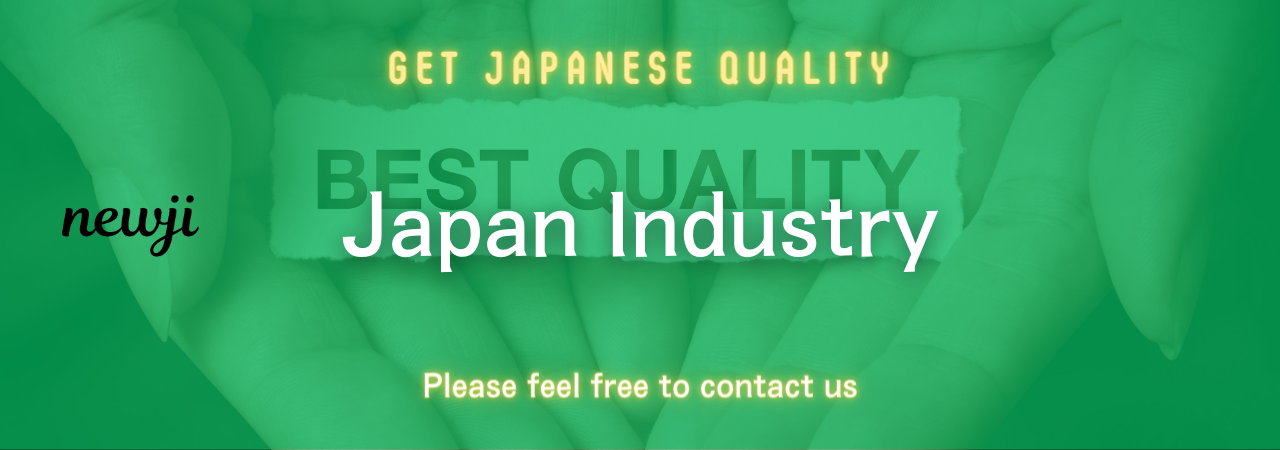
The digital age has revolutionized numerous industries, and manufacturing is no exception.
To stay competitive, manufacturers must adapt to new technologies swiftly and efficiently.
However, many companies encounter a significant challenge: the digital skills gap.
Bridging this gap is crucial for the future success of the manufacturing sector.
This article explores ways to overcome the digital skills gap in manufacturing by highlighting key strategies and best practices.
目次
Understanding the Digital Skills Gap
The digital skills gap refers to the disparity between the skills required by modern technologies and the skills possessed by the workforce.
In the manufacturing industry, this gap is often wide.
Emerging technologies such as automation, artificial intelligence, and the Internet of Things require a specialized skill set.
Many workers, especially those who have been in the industry for decades, do not have these skills.
The Importance of Bridging the Gap
Bridging the digital skills gap is not just a matter of keeping up with the times.
It is essential for staying competitive in the global market.
Advanced technologies can increase efficiency, reduce costs, and improve product quality.
Manufacturers who fail to invest in digital skills risk falling behind their competitors.
They may struggle to implement new technologies, leading to slower production times and higher operational costs.
The Economic Impact
The economic implications of the digital skills gap are significant.
Companies that invest in digital skills training will likely see a return on investment through increased productivity and innovation.
Conversely, companies that neglect this will face higher costs and may lose market share.
Bridging the gap is thus crucial not only for individual businesses but for the entire manufacturing sector.
Key Strategies for Bridging the Gap
Many strategies can be employed to overcome the digital skills gap in manufacturing.
Each company must find the methods that best suit their needs and capabilities.
Investing in Training Programs
One of the most effective ways to bridge the digital skills gap is through targeted training programs.
These programs can upskill current employees, making them proficient in new technologies.
Companies can partner with educational institutions to offer courses or utilize online platforms for flexible learning options.
Training should be ongoing, providing employees with continuous opportunities to learn and grow.
Adopting a Culture of Lifelong Learning
Creating a culture that values lifelong learning is essential.
Encourage employees to take ownership of their development by offering incentives for completing courses or obtaining certifications.
Fostering an environment where learning is celebrated can motivate employees to embrace new technologies and improvements eagerly.
Utilizing Apprenticeships and Internships
Apprenticeships and internships can be incredibly valuable in bridging the digital skills gap.
These programs allow new talent to gain hands-on experience with the latest technologies.
It is an excellent way to build a pipeline of skilled workers who are familiar with modern manufacturing processes.
Partner with local schools and colleges to establish programs that can benefit both parties.
Leveraging Digital Tools for Training
Use digital tools and platforms to facilitate training.
Virtual reality (VR) and augmented reality (AR) can create immersive training experiences.
Simulations and digital twins can help employees practice in a virtual environment without the risk and cost associated with real-world training.
These tools make learning more engaging and effective.
Implementing a Mentorship Program
Mentorship programs can pair experienced workers with those newer to the industry.
This allows knowledge and skills to transfer seamlessly.
Mentors can provide guidance, answer questions, and offer support as less experienced employees learn to navigate new technologies.
Mentorship builds a strong community within the workplace and promotes a collaborative learning environment.
Hiring Digital Natives
Consider hiring digital natives—individuals who have grown up with technology and are inherently comfortable using it.
These employees can bring fresh perspectives and innovative ideas to the table.
Their familiarity with technology can help accelerate the adoption of new tools and systems within the company.
The Role of Leadership
Leadership plays a pivotal role in bridging the digital skills gap.
Leaders must be committed to investing in their workforce’s development.
They should communicate the importance of digital skills and support the initiatives aimed at improving them.
Setting Clear Goals and Expectations
Clear goals and expectations should be established for digital skills development.
Leaders must define what skills are needed and provide a roadmap for achieving these competencies.
Setting measurable targets can help track progress and ensure that the company’s efforts are on the right path.
Allocating Resources
Adequate resources must be allocated for training and development.
This includes financial investment, time for employees to attend training sessions, and access to learning materials.
Investing in resources is a commitment that demonstrates the company’s dedication to bridging the digital skills gap.
Encouraging Innovation and Experimentation
Leaders should cultivate an atmosphere that encourages innovation and experimentation.
Employees should feel comfortable trying new methods and technologies without fear of failure.
This openness can lead to breakthroughs and improvements in manufacturing processes.
Conclusion
Overcoming the digital skills gap in manufacturing is a multifaceted challenge that requires a comprehensive approach.
By investing in training programs, fostering a culture of lifelong learning, utilizing apprenticeships, leveraging digital tools, implementing mentorship, and hiring digital natives, companies can enhance their workforce’s skills.
Leadership commitment is crucial in driving these initiatives forward.
Bridging the digital skills gap is not just an investment in the present but a crucial step for securing the future success of the manufacturing industry.
By taking these steps, manufacturers can ensure they remain competitive and continue to innovate in an ever-evolving digital landscape.
資料ダウンロード
QCD調達購買管理クラウド「newji」は、調達購買部門で必要なQCD管理全てを備えた、現場特化型兼クラウド型の今世紀最高の購買管理システムとなります。
ユーザー登録
調達購買業務の効率化だけでなく、システムを導入することで、コスト削減や製品・資材のステータス可視化のほか、属人化していた購買情報の共有化による内部不正防止や統制にも役立ちます。
NEWJI DX
製造業に特化したデジタルトランスフォーメーション(DX)の実現を目指す請負開発型のコンサルティングサービスです。AI、iPaaS、および先端の技術を駆使して、製造プロセスの効率化、業務効率化、チームワーク強化、コスト削減、品質向上を実現します。このサービスは、製造業の課題を深く理解し、それに対する最適なデジタルソリューションを提供することで、企業が持続的な成長とイノベーションを達成できるようサポートします。
オンライン講座
製造業、主に購買・調達部門にお勤めの方々に向けた情報を配信しております。
新任の方やベテランの方、管理職を対象とした幅広いコンテンツをご用意しております。
お問い合わせ
コストダウンが利益に直結する術だと理解していても、なかなか前に進めることができない状況。そんな時は、newjiのコストダウン自動化機能で大きく利益貢献しよう!
(Β版非公開)