- お役立ち記事
- Tolerance Design and Geometric Dimensioning and Tolerancing (GD&T) Techniques
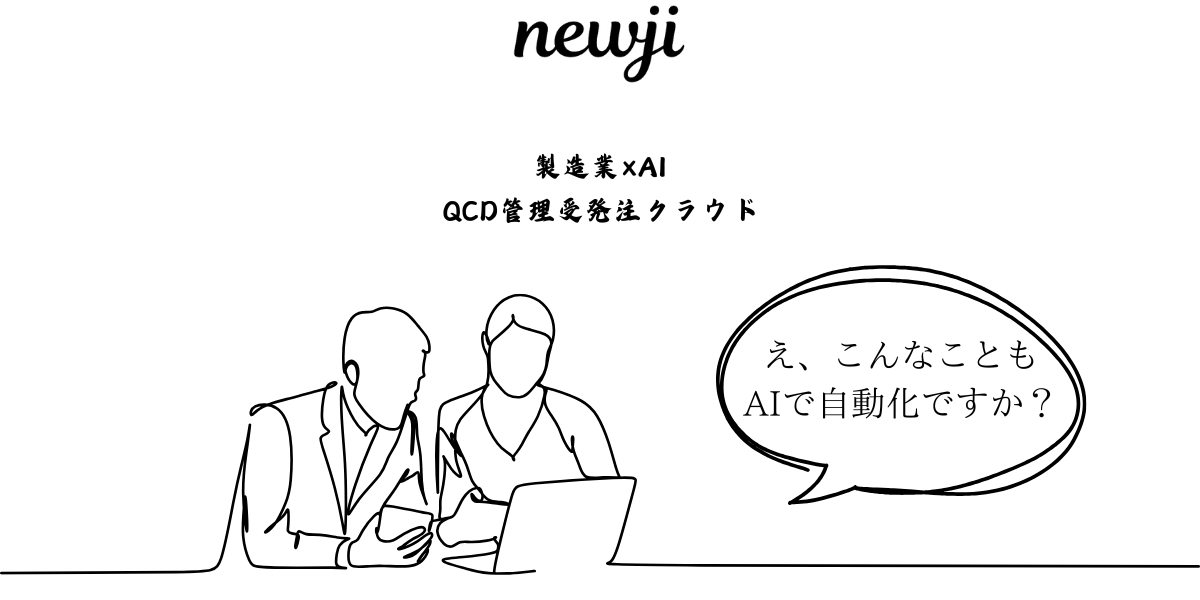
Tolerance Design and Geometric Dimensioning and Tolerancing (GD&T) Techniques
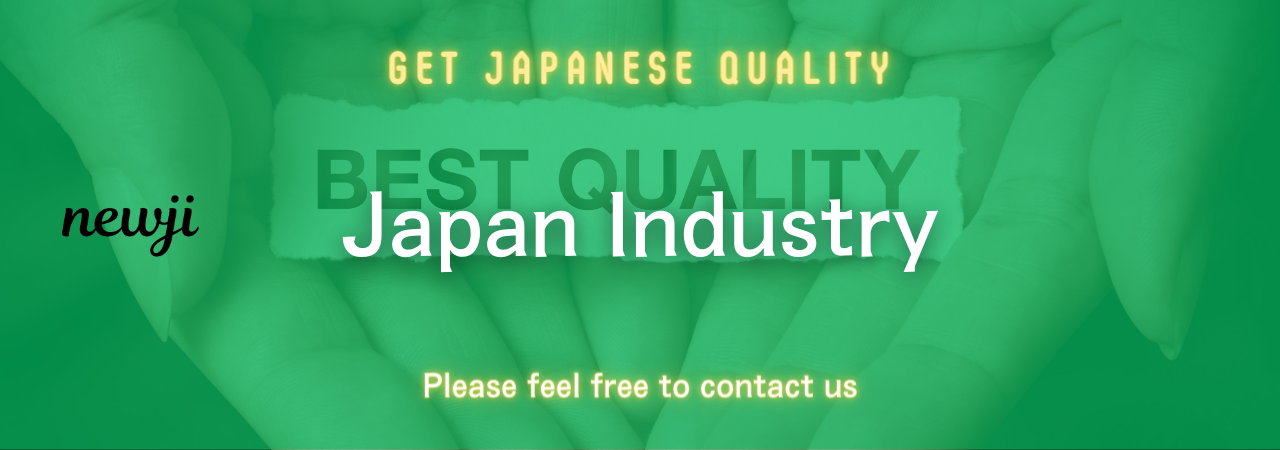
目次
Understanding Tolerance Design
Tolerance design is a crucial aspect of manufacturing and engineering.
Essentially, it refers to how much deviation from the intended dimensions of a part is acceptable.
Every manufactured part will naturally have some variation, but these variations need to be within specific limits, known as tolerances, for the part to function correctly.
Why Tolerance Design Matters
Tolerance design is significant for several reasons.
First, it ensures that parts will fit together properly in an assembly.
If tolerances are too loose, parts may be too big or too small, leading to poor fit or performance issues.
On the other hand, if tolerances are too tight, manufacturing costs can increase due to the need for more precise and expensive production processes.
Moreover, proper tolerance design can improve product quality and reliability.
When tolerances are well-defined and consistently met, it reduces the risk of parts failing prematurely or causing system malfunctions.
Geometric Dimensioning and Tolerancing (GD&T) Basics
Geometric Dimensioning and Tolerancing (GD&T) is a system that complements tolerance design.
It provides a standardized way to specify and communicate tolerances in technical drawings.
Key GD&T Symbols
Understanding the key GD&T symbols is fundamental to applying this technique effectively.
The most common symbols include:
1. **Feature Control Frame**: This is a rectangular box containing geometric characteristics, tolerances, and datum references.
2. **Datum**: A datum is a theoretical point, line, plane, or cylinder from which measurements are taken.
3. **Straightness**: Indicates that the element must lie within two parallel lines or planes.
4. **Flatness**: Ensures that a surface is within two parallel planes.
5. **Circularity**: Ensures that all points on a surface must lie within a concentric circle.
6. **Cylindricity**: Ensures that all points along the cylindrical surface are within two concentric cylinders.
7. **Profile**: Controls the form of a surface by defining a boundary.
8. **Parallelism**: Ensures that a surface or axis is parallel to a datum.
9. **Perpendicularity**: Ensures that a surface or axis is perpendicular to a datum.
10. **Angularity**: Controls the relationship of one surface or axis to another at a specific angle.
Advantages of Using GD&T
Implementing GD&T has several advantages.
Firstly, it provides a clear and concise way to communicate how a part should be manufactured.
This reduces misunderstandings and misinterpretations between designers and manufacturers.
Secondly, GD&T allows for more flexibility in manufacturing.
Instead of specifying exact dimensions, it defines acceptable limits, which can be more cost-effective.
Lastly, GD&T improves the functionality and reliability of products.
By controlling specific geometric features, you can ensure consistency and improve the performance of assembled products.
Applying Tolerance Design and GD&T Techniques
Integrating tolerance design and GD&T into your engineering and manufacturing processes can seem daunting.
However, following some basic steps can make the process more manageable.
Step 1: Define Critical Features
Start by identifying the critical features of the part that need tight tolerances.
These features are often related to fit, function, or performance.
For instance, holes that need to align for assembly are typically considered critical.
Step 2: Choose Appropriate Tolerances
Next, assign tolerances based on the functionality of each feature.
Consider the consequences if the part is at the high or low end of the tolerance range.
For critical features, tighter tolerances may be necessary, while non-critical features can have looser tolerances.
Step 3: Apply GD&T Symbols
Use GD&T symbols to specify the tolerances in your technical drawings.
Include feature control frames and datums to provide guidance about how the part should be measured and inspected.
Ensure that all team members understand the GD&T symbols and their implications.
Step 4: Verify and Inspect
Finally, once the part is manufactured, it’s essential to verify that the tolerances have been met.
Use precision measuring tools like calipers, micrometers, and coordinate measuring machines (CMMs) to check the dimensions and geometric features.
Challenges and Solutions in Tolerance Design and GD&T
Despite their benefits, tolerance design and GD&T also come with challenges.
For instance, over-complicating designs with unnecessary tight tolerances can drive up costs without any real benefit.
Communication gaps between design and manufacturing teams can also lead to inconsistencies and errors.
Addressing Common Issues
To overcome these challenges, consistent communication and collaboration are essential.
Ensure regular meetings between designers and manufacturers to discuss the tolerances and their impact on production.
Training is another crucial aspect.
Make sure all team members are well-versed in GD&T symbols and their applications.
Investing in training can minimize errors and improve overall efficiency.
Moreover, use simulation software to analyze tolerance stack-ups and their impact on the final assembly.
This proactive approach can save time and money by identifying potential issues early in the design phase.
The Future of Tolerance Design and GD&T
As technology evolves, so do the tools and techniques used in tolerance design and GD&T.
Advancements in 3D modeling and computer-aided design (CAD) software are making it easier to apply these principles accurately.
Emerging technologies like digital twins and augmented reality (AR) are also set to revolutionize how we approach tolerance design and GD&T.
These technologies can provide real-time feedback and alert engineers to potential issues before they become critical.
Moreover, as manufacturing moves toward more automated and smart factories, the need for precise and reliable tolerance design and GD&T will only grow.
These systems will be essential for ensuring that automated machines produce components consistently within the required tolerances.
In conclusion, understanding and implementing tolerance design and GD&T techniques can significantly improve your manufacturing processes.
By carefully defining tolerances and using standardized symbols, you can ensure that parts fit together properly, function well, and are cost-effective to produce.
While challenges exist, consistent communication, ongoing training, and the use of advanced tools can help you navigate these complexities and achieve high-quality results.
資料ダウンロード
QCD調達購買管理クラウド「newji」は、調達購買部門で必要なQCD管理全てを備えた、現場特化型兼クラウド型の今世紀最高の購買管理システムとなります。
ユーザー登録
調達購買業務の効率化だけでなく、システムを導入することで、コスト削減や製品・資材のステータス可視化のほか、属人化していた購買情報の共有化による内部不正防止や統制にも役立ちます。
NEWJI DX
製造業に特化したデジタルトランスフォーメーション(DX)の実現を目指す請負開発型のコンサルティングサービスです。AI、iPaaS、および先端の技術を駆使して、製造プロセスの効率化、業務効率化、チームワーク強化、コスト削減、品質向上を実現します。このサービスは、製造業の課題を深く理解し、それに対する最適なデジタルソリューションを提供することで、企業が持続的な成長とイノベーションを達成できるようサポートします。
オンライン講座
製造業、主に購買・調達部門にお勤めの方々に向けた情報を配信しております。
新任の方やベテランの方、管理職を対象とした幅広いコンテンツをご用意しております。
お問い合わせ
コストダウンが利益に直結する術だと理解していても、なかなか前に進めることができない状況。そんな時は、newjiのコストダウン自動化機能で大きく利益貢献しよう!
(Β版非公開)