- お役立ち記事
- Techniques for Measuring Limit Performance Through Destructive Testing
Techniques for Measuring Limit Performance Through Destructive Testing
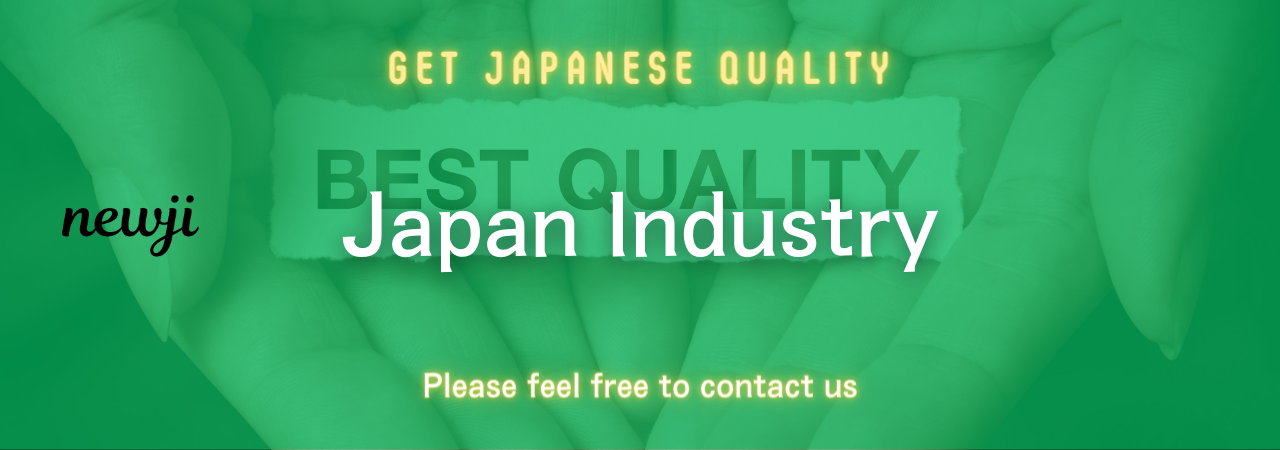
When it comes to understanding how strong or durable a material is, one of the most effective methods is through destructive testing.
This type of testing pushes a material until it breaks to determine its limit performance.
By examining how and when a material fails, engineers can design safer and more reliable products.
Here, we delve into various techniques used for measuring limit performance through destructive testing.
目次
What is Destructive Testing?
Destructive testing involves testing materials to their breaking points.
As the name implies, the material will be destroyed in the process, but the data obtained is invaluable.
This kind of testing helps to understand the mechanical strength, ductility, fracture toughness, and fatigue resistance of a material.
It allows engineers to learn how a material will perform under extreme conditions, providing a comprehensive insight into its limitations.
Common Techniques in Destructive Testing
There are several techniques used in destructive testing to evaluate the limit performance of materials.
Each method has its distinct purpose and application.
Here’s a closer look at some of the most widely-used techniques.
Tensile Testing
Tensile testing, also known as tension testing, measures a material’s resistance to being pulled apart.
During this test, a sample is stretched until it breaks, providing data on its strength and ductility.
Tensile testing is crucial for understanding how a material will perform when subjected to pulling or stretching forces.
Compression Testing
In contrast to tensile testing, compression testing measures a material’s resistance to being crushed.
A sample is compressed until it fails, offering insights into its behavior under compressive forces.
This type of testing is particularly useful for materials used in construction and manufacturing, where they often face compressive stresses.
Bending Testing
Bending testing involves applying a force to a material in a way that bends it until it fractures.
This test helps to assess the flexibility and toughness of the material.
It is commonly used for materials that will experience bending or flexing in their applications, such as beams and structural components.
Impact Testing
Impact testing evaluates a material’s toughness and its ability to absorb energy during a high-speed impact.
This test typically involves striking a test sample with a pendulum or hammer and measuring the energy required to break it.
Charpy and Izod tests are two common types of impact testing.
They are essential for materials used in environments where sudden impacts may occur.
Hardness Testing
Hardness testing measures a material’s resistance to deformation.
While not strictly a destructive test, it often involves making permanent indentations on the material’s surface.
Techniques such as Rockwell, Brinell, and Vickers hardness tests are commonly employed.
These tests help to determine a material’s wear resistance and its ability to endure surface indentation.
Fatigue Testing
Fatigue testing reveals how a material behaves under repeated cyclic loading.
A sample is subjected to cycles of stress, typically below its ultimate tensile strength, until it eventually fails.
This test is crucial for understanding how long a material can last in real-world conditions where it faces repetitive loads.
Fracture Toughness Testing
Fracture toughness testing determines a material’s ability to resist crack propagation.
This involves growing a crack in the sample and then subjecting it to stress until it propagates rapidly.
This test is particularly important for materials used in critical applications, such as aerospace and transportation, where failure could be catastrophic.
The Importance of Destructive Testing
Destructive testing offers several key benefits for manufacturers, engineers, and designers.
Identify Material Limits
Destructive testing allows engineers to identify the precise limits of a material, understanding exactly how much force or stress it can tolerate before failing.
This information is vital for ensuring that materials are used within their safe operational limits.
Improve Product Safety
By pushing materials to their breaking points, destructive testing helps to eliminate potential weaknesses.
Engineers can design safer products by selecting the right materials and understanding their failure mechanisms.
Enhance Reliability
Understanding how materials fail under specific conditions enhances the reliability of products.
Manufacturers can ensure that their products will perform as expected over time, even under extreme conditions.
Optimize Designs
The data from destructive testing enables engineers to optimize their designs.
They can make informed decisions on material selection, dimensions, and other critical factors, leading to more efficient and durable products.
Challenges and Considerations
While destructive testing offers numerous benefits, it also presents certain challenges and considerations.
Sample Destruction
One of the primary drawbacks of destructive testing is that it destroys the sample being tested.
This can be costly, especially when dealing with expensive or limited materials.
However, the insights gained from the testing process often justify the expense.
Test Conditions
Replicating real-world conditions precisely can be challenging.
The results of destructive testing may not always perfectly reflect how a material will behave in every possible scenario.
Engineers must carefully consider the test conditions and how they relate to the intended application.
Time-Consuming
Some destructive tests can be time-consuming, particularly fatigue testing, which requires repeated cyclic loading over extended periods.
This can slow down the overall development process, making efficient planning essential.
Conclusion
Destructive testing is an invaluable tool for understanding the limit performance of materials.
By employing techniques such as tensile, compression, bending, impact, hardness, fatigue, and fracture toughness testing, engineers can gain a comprehensive understanding of how materials will behave under extreme conditions.
This knowledge is crucial for designing safer, more reliable, and efficient products.
Despite the challenges and costs associated with destructive testing, the benefits it offers in terms of material performance and product safety make it an essential component of modern engineering and manufacturing.
資料ダウンロード
QCD調達購買管理クラウド「newji」は、調達購買部門で必要なQCD管理全てを備えた、現場特化型兼クラウド型の今世紀最高の購買管理システムとなります。
ユーザー登録
調達購買業務の効率化だけでなく、システムを導入することで、コスト削減や製品・資材のステータス可視化のほか、属人化していた購買情報の共有化による内部不正防止や統制にも役立ちます。
NEWJI DX
製造業に特化したデジタルトランスフォーメーション(DX)の実現を目指す請負開発型のコンサルティングサービスです。AI、iPaaS、および先端の技術を駆使して、製造プロセスの効率化、業務効率化、チームワーク強化、コスト削減、品質向上を実現します。このサービスは、製造業の課題を深く理解し、それに対する最適なデジタルソリューションを提供することで、企業が持続的な成長とイノベーションを達成できるようサポートします。
オンライン講座
製造業、主に購買・調達部門にお勤めの方々に向けた情報を配信しております。
新任の方やベテランの方、管理職を対象とした幅広いコンテンツをご用意しております。
お問い合わせ
コストダウンが利益に直結する術だと理解していても、なかなか前に進めることができない状況。そんな時は、newjiのコストダウン自動化機能で大きく利益貢献しよう!
(Β版非公開)