- お役立ち記事
- Transformation to a Digital Enterprise in Manufacturing: Strategies and Case Studies
Transformation to a Digital Enterprise in Manufacturing: Strategies and Case Studies
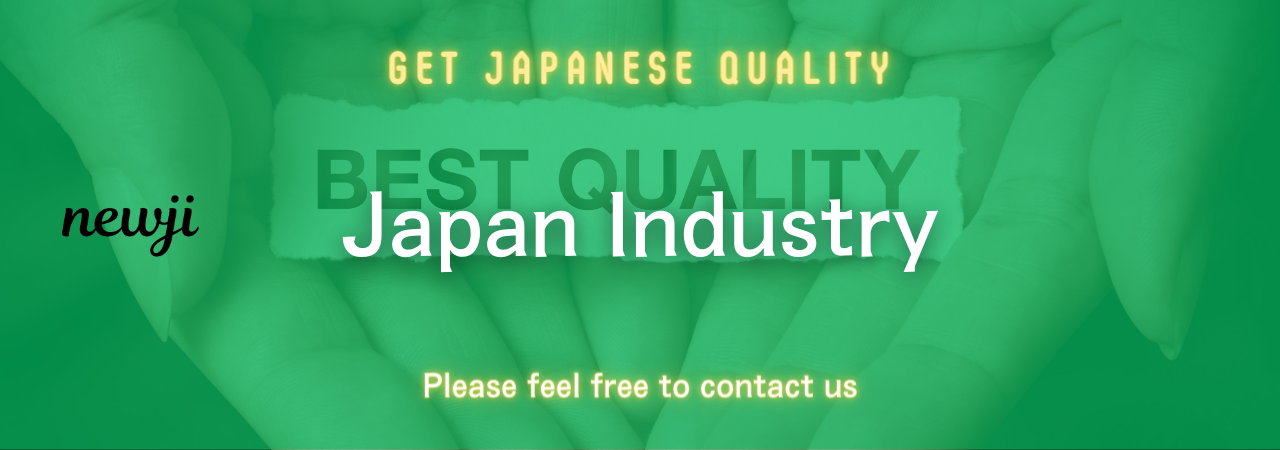
The manufacturing landscape is undergoing a significant transformation as companies shift towards becoming digital enterprises.
This shift is driven by the need to stay competitive, enhance efficiency, and meet the evolving demands of customers.
By leveraging advanced technologies, manufacturers can optimize their operations, reduce costs, and deliver better products and services.
目次
What is a Digital Enterprise in Manufacturing?
A digital enterprise in manufacturing refers to a company that uses digital technologies to improve its manufacturing processes, supply chain, and customer interactions.
It involves the integration of systems and data across the entire organization to create a seamless flow of information.
This integration enables real-time decision-making and enhances productivity.
Technologies such as the Internet of Things (IoT), artificial intelligence (AI), big data, and cloud computing are at the core of this transformation.
Key Strategies for Transforming into a Digital Enterprise
1. Implementing IoT and Smart Manufacturing
The Internet of Things (IoT) allows machines and devices to communicate with each other through the internet.
In manufacturing, IoT enables the collection of data from various sources, such as sensors and equipment.
This data can be analyzed to monitor the performance of machines, predict maintenance needs, and optimize production processes.
Smart manufacturing uses technologies like IoT to create more efficient and connected production environments.
By implementing smart manufacturing, companies can gain insights into their operations and make data-driven decisions to improve productivity and reduce downtime.
2. Utilizing Artificial Intelligence and Machine Learning
Artificial intelligence (AI) and machine learning (ML) are powerful tools that can analyze massive amounts of data and identify patterns.
In manufacturing, AI and ML can be used for quality control, predictive maintenance, and inventory management.
For example, AI-powered systems can detect defects in products during the production process, allowing for immediate corrective actions.
Predictive maintenance uses machine learning algorithms to predict when equipment is likely to fail, enabling companies to schedule maintenance before any breakdown occurs.
This approach reduces downtime and extends the lifespan of machines.
3. Embracing Big Data and Analytics
Big data refers to the vast amounts of data generated by manufacturing operations.
Analytics involves the use of statistical techniques and software tools to extract meaningful insights from this data.
By analyzing big data, manufacturers can identify trends, understand customer preferences, and optimize their supply chains.
For instance, analytics can be used to forecast demand, manage inventory levels, and balance production schedules.
This leads to better resource allocation and minimizes waste, ultimately boosting profitability.
4. Adopting Cloud Computing
Cloud computing provides a flexible and scalable platform for storing and processing data.
By moving their IT infrastructure to the cloud, manufacturers can reduce costs, increase agility, and improve collaboration.
Cloud-based solutions enable real-time data sharing and remote access to information, making it easier for teams to work together.
Moreover, cloud computing supports the implementation of other digital technologies, such as IoT and AI, by providing the necessary computing power and storage capabilities.
This ensures that manufacturing operations can run smoothly and efficiently.
5. Enhancing Cybersecurity
As manufacturing becomes more digitized, the importance of cybersecurity cannot be overstated.
Protecting sensitive data and systems from cyber threats is crucial for maintaining the integrity of operations.
Manufacturers must implement robust cybersecurity measures, such as encryption, firewalls, and multi-factor authentication, to safeguard their digital assets.
Regular security audits and employee training programs can also help in identifying and mitigating potential vulnerabilities.
A proactive approach to cybersecurity ensures that manufacturers can operate in a secure digital environment.
Case Studies of Successful Digital Transformation
1. Siemens
Siemens, a global leader in manufacturing, has successfully transformed into a digital enterprise.
The company implemented its own Digital Enterprise Suite, which integrates hardware, software, and services to optimize production processes.
By leveraging IoT, AI, and big data, Siemens has achieved significant improvements in efficiency and product quality.
For example, the company’s Amberg Electronics Plant operates as a fully digital factory, where machines and systems communicate with each other to enhance productivity.
This has resulted in a 50% reduction in production time and a 25% decrease in defect rates.
2. General Electric (GE)
General Electric (GE) has also embraced digital transformation through its Predix platform, designed for the industrial internet.
Predix enables GE to connect machines, data, and people to optimize manufacturing operations.
The platform uses data analytics to monitor equipment performance, identify issues, and recommend maintenance actions.
One notable success story is GE’s implementation of digital twin technology, which creates virtual replicas of physical assets.
Digital twins allow GE to simulate and analyze the performance of equipment in real-time, leading to better decision-making and operational efficiency.
This has resulted in a 20% reduction in maintenance costs and a 15% increase in equipment uptime.
3. Bosch
Bosch, a leading technology and services company, has made significant strides in digital transformation through its Industry 4.0 initiatives.
The company uses IoT, AI, and cloud computing to create smart factories and connected supply chains.
Bosch’s approach focuses on automating production processes, enhancing quality control, and improving environmental sustainability.
In its Homburg plant, Bosch has implemented an Industry 4.0 production line that uses IoT sensors and AI analytics to optimize manufacturing.
This has led to a 30% increase in productivity, a 40% reduction in maintenance costs, and a 20% decrease in energy consumption.
Challenges and Future Directions
While the benefits of digital transformation are evident, manufacturers also face several challenges in this journey.
These include high implementation costs, the need for skilled personnel, and concerns about data security.
Overcoming these challenges requires a clear strategy, investment in training, and a strong focus on cybersecurity.
Looking ahead, the future of manufacturing lies in further advancements in digital technologies.
Emerging trends such as 5G connectivity, edge computing, and blockchain will play a crucial role in shaping the next generation of digital enterprises.
Manufacturers that stay ahead of these trends and continue to innovate will be well-positioned for success in the digital age.
In conclusion, the transformation to a digital enterprise in manufacturing is a strategic imperative for staying competitive and achieving operational excellence.
By implementing IoT, AI, big data, and cloud computing, manufacturers can unlock new efficiencies, reduce costs, and deliver superior products.
Success stories from industry leaders like Siemens, GE, and Bosch demonstrate the tangible benefits of digital transformation.
While challenges remain, the continuous evolution of digital technologies promises a bright future for the manufacturing sector.
資料ダウンロード
QCD調達購買管理クラウド「newji」は、調達購買部門で必要なQCD管理全てを備えた、現場特化型兼クラウド型の今世紀最高の購買管理システムとなります。
ユーザー登録
調達購買業務の効率化だけでなく、システムを導入することで、コスト削減や製品・資材のステータス可視化のほか、属人化していた購買情報の共有化による内部不正防止や統制にも役立ちます。
NEWJI DX
製造業に特化したデジタルトランスフォーメーション(DX)の実現を目指す請負開発型のコンサルティングサービスです。AI、iPaaS、および先端の技術を駆使して、製造プロセスの効率化、業務効率化、チームワーク強化、コスト削減、品質向上を実現します。このサービスは、製造業の課題を深く理解し、それに対する最適なデジタルソリューションを提供することで、企業が持続的な成長とイノベーションを達成できるようサポートします。
オンライン講座
製造業、主に購買・調達部門にお勤めの方々に向けた情報を配信しております。
新任の方やベテランの方、管理職を対象とした幅広いコンテンツをご用意しております。
お問い合わせ
コストダウンが利益に直結する術だと理解していても、なかなか前に進めることができない状況。そんな時は、newjiのコストダウン自動化機能で大きく利益貢献しよう!
(Β版非公開)