- お役立ち記事
- Risk Assessment for Collaborative Robots and Building Safety 2.0 Systems
Risk Assessment for Collaborative Robots and Building Safety 2.0 Systems
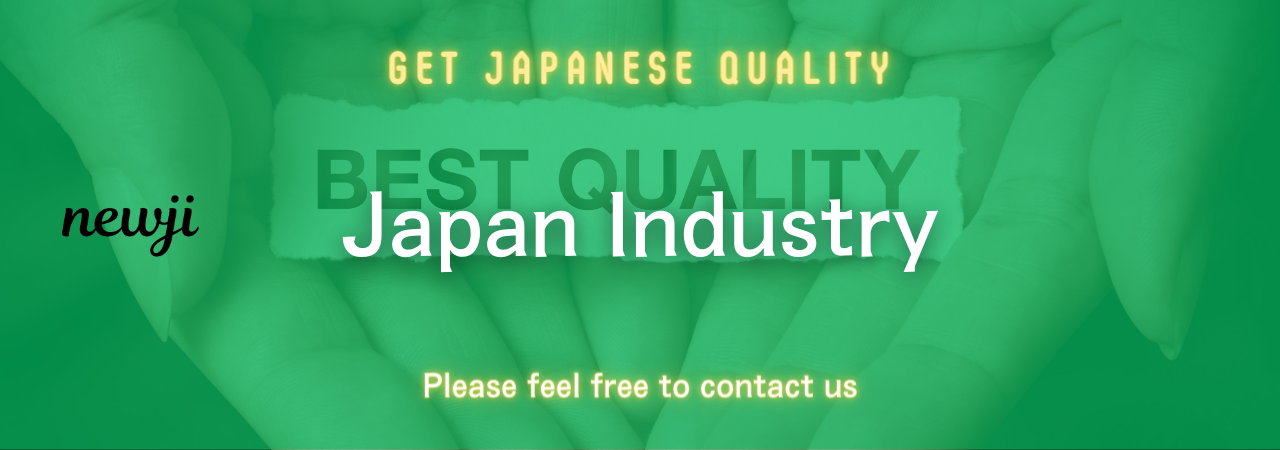
Collaborative robots, often referred to as cobots, are revolutionizing industries by working alongside human workers to enhance productivity and efficiency. While these robots bring numerous benefits, it’s essential to conduct a thorough risk assessment to ensure their safe implementation.
Simultaneously, as workplaces evolve with advanced technologies, incorporating a Safety 2.0 system provides a holistic approach to worker safety. This article delves into the importance of risk assessment for collaborative robots and the integration of Safety 2.0 systems to build safer work environments.
目次
Understanding Collaborative Robots
Collaborative robots are designed to operate in close proximity to human workers, unlike traditional industrial robots that require safety cages or barriers. These robots are equipped with sensors and advanced programming to detect human presence and navigate complex tasks safely. However, as with any machinery, cobots come with their own set of risks and challenges.
Key Features of Collaborative Robots
Collaborative robots boast several features that make them user-friendly and safe for human interaction. These include:
– **Speed and Separation Monitoring:** These robots can adjust their speed based on the proximity of human workers.
– **Power and Force Limiting Control Systems:** Advanced control systems help maintain safe interaction.
– **Hand Guiding:** Operators can easily program tasks by manually guiding the robot.
While these features enhance safety, they also present unique risks that need careful assessment.
Risk Assessment for Collaborative Robots
Conducting a risk assessment for collaborative robots involves identifying potential hazards, evaluating risks, and implementing appropriate control measures. This process is crucial for minimizing accidents and ensuring a safe working environment.
Identifying Potential Hazards
Potential hazards associated with collaborative robots include:
– **Electrical Hazards:** Possibility of electrical shocks or faults.
– **Human Errors:** Mistakes made by human workers during interaction with cobots.
– **Environmental Hazards:** Factors such as poor lighting or slippery floors that can increase risk.
Recognizing these hazards is the first step in conducting a comprehensive risk assessment.
Evaluating Risks
Once potential hazards are identified, the next step is to evaluate the associated risks. This involves assessing the likelihood of an incident occurring and the severity of its consequences. Consider factors like:
– **Proximity:** The distance between workers and the robot.
– **Task Complexity:** The complexity of tasks performed by the robot and the potential for errors.
Evaluating these factors helps prioritize risks and determine which areas require immediate attention.
Implementing Control Measures
To mitigate identified risks, it’s essential to implement appropriate control measures. These may include:
– **Administrative Controls:** Establishing safe work procedures and providing training to workers.
– **Personal Protective Equipment (PPE):** Ensuring workers wear suitable protective gear.
– **Regular Maintenance:** Keeping the robot and its components in good working condition.
Effective control measures are crucial for maintaining a safe working environment and preventing accidents.
Building Safety 2.0 Systems
As workplaces become more technologically advanced, traditional safety measures may no longer suffice. Safety 2.0 systems integrate modern technologies to create comprehensive safety solutions, ensuring worker safety in dynamic environments.
The Core Components of Safety 2.0 Systems
Safety 2.0 systems encompass several core components that work together to enhance workplace safety, including:
– **Data Analytics:** Analyzing data gathered from monitoring systems to identify patterns and predict potential hazards.
– **Automation and Robotics:** Integrating automated systems and robots to perform hazardous tasks, reducing human exposure to risks.
– **Communication Systems:** Facilitating instant communication between workers, supervisors, and emergency responders.
These components help create a proactive approach to safety, allowing for swift identification and resolution of potential hazards.
Benefits of Safety 2.0 Systems
Implementing Safety 2.0 systems offers several benefits, including:
– **Enhanced Decision-Making:** Access to comprehensive data allows for informed decisions regarding safety measures.
– **Increased Compliance:** Automated systems ensure compliance with safety regulations and standards.
– **Reduced Downtime:** Quick response to incidents minimizes downtime and maintains productivity.
These benefits not only enhance worker safety but also contribute to overall operational efficiency.
Integrating Cobots with Safety 2.0 Systems
Integrating collaborative robots with Safety 2.0 systems creates a synergy that maximizes safety and productivity. Consider the following integration strategies:
– **Adaptive Safety Protocols:** Implementing protocols that adapt based on real-time data from both cobots and environmental sensors.
– **Continuous Improvement:** Regularly reviewing and updating safety measures based on data analysis and incident reports.
By combining the strengths of cobots and Safety 2.0 systems, organizations can create a safer, more efficient work environment.
Conclusion
The rise of collaborative robots presents both opportunities and challenges in workplace safety. Conducting thorough risk assessments and integrating advanced Safety 2.0 systems are crucial steps in building safer work environments.
By identifying potential hazards, evaluating risks, and implementing effective control measures, organizations can harness the benefits of cobots while ensuring the well-being of their workers. Embracing Safety 2.0 systems further enhances this commitment to safety, paving the way for a future where technology and human workers coexist harmoniously and safely.
資料ダウンロード
QCD調達購買管理クラウド「newji」は、調達購買部門で必要なQCD管理全てを備えた、現場特化型兼クラウド型の今世紀最高の購買管理システムとなります。
ユーザー登録
調達購買業務の効率化だけでなく、システムを導入することで、コスト削減や製品・資材のステータス可視化のほか、属人化していた購買情報の共有化による内部不正防止や統制にも役立ちます。
NEWJI DX
製造業に特化したデジタルトランスフォーメーション(DX)の実現を目指す請負開発型のコンサルティングサービスです。AI、iPaaS、および先端の技術を駆使して、製造プロセスの効率化、業務効率化、チームワーク強化、コスト削減、品質向上を実現します。このサービスは、製造業の課題を深く理解し、それに対する最適なデジタルソリューションを提供することで、企業が持続的な成長とイノベーションを達成できるようサポートします。
オンライン講座
製造業、主に購買・調達部門にお勤めの方々に向けた情報を配信しております。
新任の方やベテランの方、管理職を対象とした幅広いコンテンツをご用意しております。
お問い合わせ
コストダウンが利益に直結する術だと理解していても、なかなか前に進めることができない状況。そんな時は、newjiのコストダウン自動化機能で大きく利益貢献しよう!
(Β版非公開)