- お役立ち記事
- Manufacturing in the Era of Industry 5.0: Co-Creation Between Humans and Robots
Manufacturing in the Era of Industry 5.0: Co-Creation Between Humans and Robots
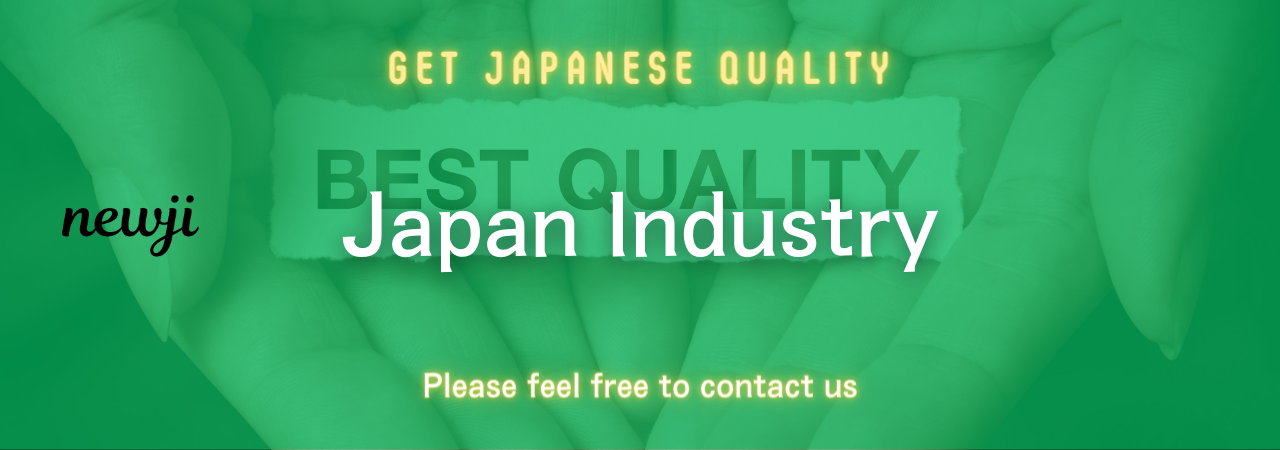
In recent years, the manufacturing industry has been going through significant changes.
From the first industrial revolution to today, each stage brought new technologies that revolutionized the way we produce goods.
We’re now standing on the brink of Industry 5.0, a new chapter that promises to transform manufacturing in ways we’ve never seen before.
This phase focuses on the collaboration between humans and robots to create smarter, more efficient, and more personalized manufacturing processes.
目次
What is Industry 5.0?
Industry 5.0 builds upon the foundations laid by Industry 4.0, which introduced the Internet of Things (IoT), big data, and automation.
While Industry 4.0 emphasized machine-driven efficiency and connectivity, Industry 5.0 places a greater focus on the synergy between human creativity and machine precision.
In this era, robots and artificial intelligence (AI) will work alongside human workers rather than replace them.
This collaboration aims to leverage the unique strengths of both, combining human ingenuity with machine efficiency.
The Key Components of Industry 5.0
Human-Robot Collaboration
The centerpiece of Industry 5.0 is the collaboration between humans and robots.
In manufacturing, this means that robots will handle repetitive and physically demanding tasks, freeing up humans to focus on more complex, creative, and strategic activities.
Collaborative robots, or cobots, are designed to work safely alongside humans, enhancing productivity and reducing workplace injuries.
Personalization and Customization
One of the most exciting aspects of Industry 5.0 is the ability to offer more personalized and customized products.
With the help of AI and advanced manufacturing techniques, businesses can cater to individual customer preferences without compromising efficiency.
This level of customization was previously unthinkable on a large scale, but Industry 5.0 makes it possible to produce unique products at the speed and cost of mass production.
Advanced AI and Machine Learning
AI and machine learning technologies are essential to Industry 5.0.
These technologies can analyze vast amounts of data, making it easier for manufacturers to optimize production processes, predict maintenance needs, and respond to changing market demands swiftly.
By learning from data, AI systems can continually improve and adapt, leading to smarter manufacturing operations over time.
Enhanced Quality Control
With the integration of advanced sensors and AI, Industry 5.0 enhances quality control measures.
Machines can detect even the slightest deviations from desired specifications, ensuring higher quality and consistency in manufactured goods.
This level of precision not only reduces waste but also increases customer satisfaction.
Benefits of Industry 5.0
Increased Efficiency
Industry 5.0 aims to create more efficient manufacturing processes by combining human creativity with machine accuracy.
Tasks that once took hours or even days can now be completed in a fraction of the time, thanks to this synergy.
This increased efficiency translates to higher productivity and lower costs.
Better Working Conditions
By delegating repetitive and physically taxing tasks to robots, Industry 5.0 can improve working conditions for human employees.
This shift allows workers to engage in more meaningful and intellectually stimulating activities, leading to higher job satisfaction and reduced burnout.
Greater Innovation
With humans focusing on creativity and strategic tasks, there’s a higher potential for innovation within the manufacturing sector.
This innovation can lead to the development of new products, materials, and processes that were previously unattainable.
Environmental Sustainability
Industry 5.0 also holds promise for more sustainable manufacturing practices.
By optimizing processes and reducing waste, manufacturers can minimize their environmental footprint.
Moreover, the ability to produce customized products on-demand reduces overproduction and excess inventory, further contributing to sustainability goals.
Challenges in Implementing Industry 5.0
Technological Integration
One of the primary challenges in implementing Industry 5.0 is the integration of new technologies with existing systems.
Manufacturers need to invest in advanced technologies and ensure they work seamlessly with their current infrastructure.
This process can be time-consuming and costly, requiring careful planning and execution.
Workforce Training
As Industry 5.0 reshapes the manufacturing landscape, there’s a growing need for a skilled workforce capable of working alongside advanced technologies.
Employers must invest in training programs to equip their employees with the necessary skills to thrive in this new era.
This includes not only technical skills but also problem-solving and creative thinking abilities.
Cybersecurity
With increased connectivity and the integration of IoT devices, the risk of cyberattacks becomes more significant.
Manufacturers must prioritize cybersecurity measures to protect sensitive data and ensure the integrity of their operations.
Implementing robust security protocols and regularly updating systems are crucial steps in mitigating these risks.
The Future of Manufacturing
Industry 5.0 represents a significant leap forward in the evolution of manufacturing.
The collaboration between humans and robots has the potential to transform the industry in ways we can scarcely imagine.
From increased efficiency and innovation to better working conditions and environmental sustainability, the benefits are immense.
However, realizing these benefits requires overcoming several challenges, including technological integration, workforce training, and cybersecurity.
By addressing these issues head-on and embracing the potential of Industry 5.0, manufacturers can position themselves at the forefront of a new industrial revolution.
As we move further into this new era, the co-creation between humans and robots will become increasingly important.
This synergy will not only redefine manufacturing processes but also unlock new possibilities for growth and progress across various industries.
The future of manufacturing is bright, and Industry 5.0 is leading the way.
資料ダウンロード
QCD調達購買管理クラウド「newji」は、調達購買部門で必要なQCD管理全てを備えた、現場特化型兼クラウド型の今世紀最高の購買管理システムとなります。
ユーザー登録
調達購買業務の効率化だけでなく、システムを導入することで、コスト削減や製品・資材のステータス可視化のほか、属人化していた購買情報の共有化による内部不正防止や統制にも役立ちます。
NEWJI DX
製造業に特化したデジタルトランスフォーメーション(DX)の実現を目指す請負開発型のコンサルティングサービスです。AI、iPaaS、および先端の技術を駆使して、製造プロセスの効率化、業務効率化、チームワーク強化、コスト削減、品質向上を実現します。このサービスは、製造業の課題を深く理解し、それに対する最適なデジタルソリューションを提供することで、企業が持続的な成長とイノベーションを達成できるようサポートします。
オンライン講座
製造業、主に購買・調達部門にお勤めの方々に向けた情報を配信しております。
新任の方やベテランの方、管理職を対象とした幅広いコンテンツをご用意しております。
お問い合わせ
コストダウンが利益に直結する術だと理解していても、なかなか前に進めることができない状況。そんな時は、newjiのコストダウン自動化機能で大きく利益貢献しよう!
(Β版非公開)