- お役立ち記事
- The Role and Strategy of Quality Assurance Departments in Achieving Zero Defects in Manufacturing
The Role and Strategy of Quality Assurance Departments in Achieving Zero Defects in Manufacturing
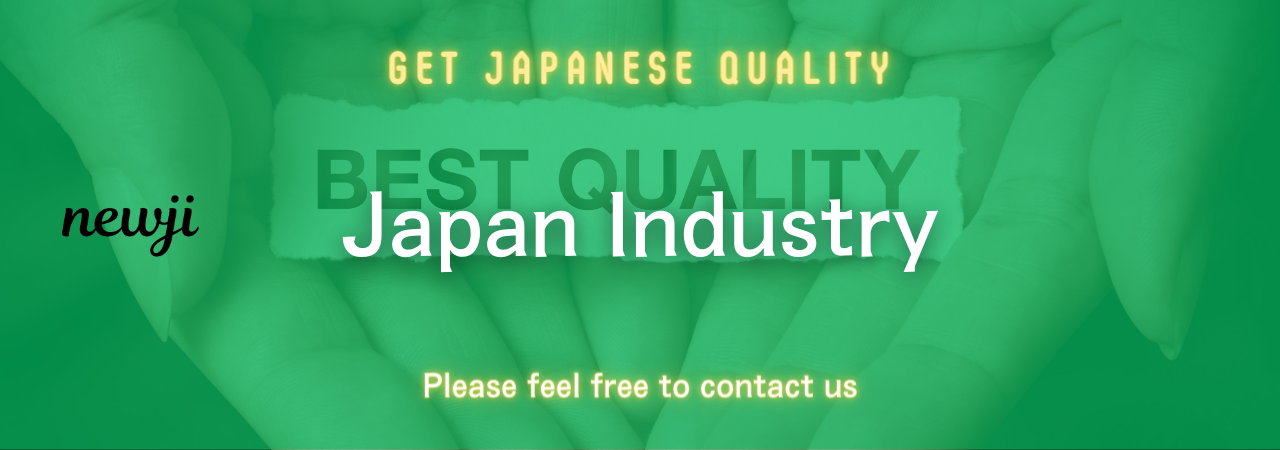
In the highly competitive world of manufacturing, ensuring product quality is paramount.
Customers demand products that are reliable, durable, and free from defects.
Achieving zero defects—an ambitious goal that signifies flawless production—is the ultimate aim of many companies.
A key player in this journey is the Quality Assurance (QA) department.
This article explores the pivotal role of QA and the strategies they employ to achieve zero defects.
目次
Understanding the QA Department’s Role
The QA department is responsible for ensuring that the products meet the required quality standards and specifications.
Their role is not just limited to catching defects at the end of the production line but involves monitoring and improving the entire manufacturing process.
Setting Quality Standards
One of the first critical roles QA plays is in setting quality standards.
These standards define the acceptable levels of product quality and identify the benchmarks against which products will be measured.
To develop these standards, QA teams often collaborate with various departments such as design, engineering, and production.
This collaborative effort ensures that quality benchmarks are realistic and achievable.
Inspection and Testing
Inspection and testing are fundamental to the QA process.
The QA team inspects raw materials, components, and finished products to detect any discrepancies or defects.
They employ various testing methodologies—such as visual inspection, measurement, and destructive or non-destructive testing—to ensure compliance with set standards.
Regular inspections and rigorous testing help in identifying potential issues early in the production cycle, reducing the likelihood of defects in the final product.
Key Strategies for Achieving Zero Defects
Achieving zero defects is a lofty goal, but several strategies can effectively steer a manufacturing company towards this ideal.
Implementing a Continuous Improvement Process
Continuous improvement is a strategy that emphasizes the ongoing effort to enhance products, services, and processes.
In the context of zero defects, it involves constantly seeking ways to reduce variability and eliminate errors in the manufacturing process.
Techniques such as Six Sigma and Total Quality Management (TQM) are often employed.
Six Sigma, for example, uses data-driven methods and statistical analysis to identify and remove the causes of defects.
Automating Quality Control Systems
Automation in quality control significantly reduces human error, which is a major contributor to defects.
Automated systems can perform repetitive and complex tasks with high precision and consistency.
For instance, machine vision systems can inspect products in real-time, identifying defects that might be missed by the human eye.
Automated data collection and analysis also provide QA teams with real-time insights, enabling quicker decision-making and problem resolution.
Employee Training and Engagement
Employees are at the heart of the manufacturing process, and their involvement in quality assurance is crucial.
Regular training programs ensure that employees are aware of quality standards and the importance of adhering to them.
Engagement initiatives, such as quality circles and feedback loops, encourage employees to take ownership of product quality.
When employees are well-trained and motivated, the incidence of defects significantly decreases.
Supplier Quality Management
Suppliers play a vital role in the manufacturing process, as the quality of raw materials and components directly impacts the final product.
QA departments must establish robust supplier quality management practices.
This involves selecting suppliers based on strict quality criteria, conducting regular audits, and fostering good communication.
By ensuring that suppliers meet high-quality standards, manufacturers can mitigate the risk of defects in the production line.
Advanced Quality Assurance Techniques
Innovations in technology have led to the development of advanced QA techniques that further the goal of zero defects.
Predictive Analytics
Predictive analytics uses historical data and statistical algorithms to predict future outcomes.
In quality assurance, it helps in identifying patterns and trends that may indicate potential defects.
By analyzing data from past production cycles, QA teams can forecast where and when defects are likely to occur and take proactive measures to prevent them.
Real-Time Quality Monitoring
Real-time quality monitoring involves continuously tracking the quality parameters during production.
This is often achieved through the integration of IoT (Internet of Things) devices and sensors that collect data on various aspects of the manufacturing process.
Real-time monitoring allows for immediate detection and correction of defects, minimizing their propagation through the production line.
Root Cause Analysis
When defects do occur, it is essential to identify their root cause to prevent recurrence.
Root cause analysis (RCA) is a methodical approach to pinpointing the origin of problems.
Techniques such as the Five Whys and Fishbone Diagram (Ishikawa) help in digging deep into the issue and uncovering its primary cause.
Addressing the root cause ensures that the same defect does not happen again.
Conclusion
The quest for zero defects in manufacturing is an ongoing challenge, but with the right strategies and a committed QA department, it is attainable.
Quality Assurance is not merely about inspecting finished goods; it is about fostering a culture of quality throughout the organization.
By setting high standards, leveraging advanced technologies, and engaging employees, the QA department can lead the way in producing defect-free products.
Ultimately, achieving zero defects not only enhances customer satisfaction but also boosts the overall efficiency and profitability of the manufacturing operation.
資料ダウンロード
QCD調達購買管理クラウド「newji」は、調達購買部門で必要なQCD管理全てを備えた、現場特化型兼クラウド型の今世紀最高の購買管理システムとなります。
ユーザー登録
調達購買業務の効率化だけでなく、システムを導入することで、コスト削減や製品・資材のステータス可視化のほか、属人化していた購買情報の共有化による内部不正防止や統制にも役立ちます。
NEWJI DX
製造業に特化したデジタルトランスフォーメーション(DX)の実現を目指す請負開発型のコンサルティングサービスです。AI、iPaaS、および先端の技術を駆使して、製造プロセスの効率化、業務効率化、チームワーク強化、コスト削減、品質向上を実現します。このサービスは、製造業の課題を深く理解し、それに対する最適なデジタルソリューションを提供することで、企業が持続的な成長とイノベーションを達成できるようサポートします。
オンライン講座
製造業、主に購買・調達部門にお勤めの方々に向けた情報を配信しております。
新任の方やベテランの方、管理職を対象とした幅広いコンテンツをご用意しております。
お問い合わせ
コストダウンが利益に直結する術だと理解していても、なかなか前に進めることができない状況。そんな時は、newjiのコストダウン自動化機能で大きく利益貢献しよう!
(Β版非公開)