- お役立ち記事
- 5S and Visualization for Management and Indirect Operations
5S and Visualization for Management and Indirect Operations
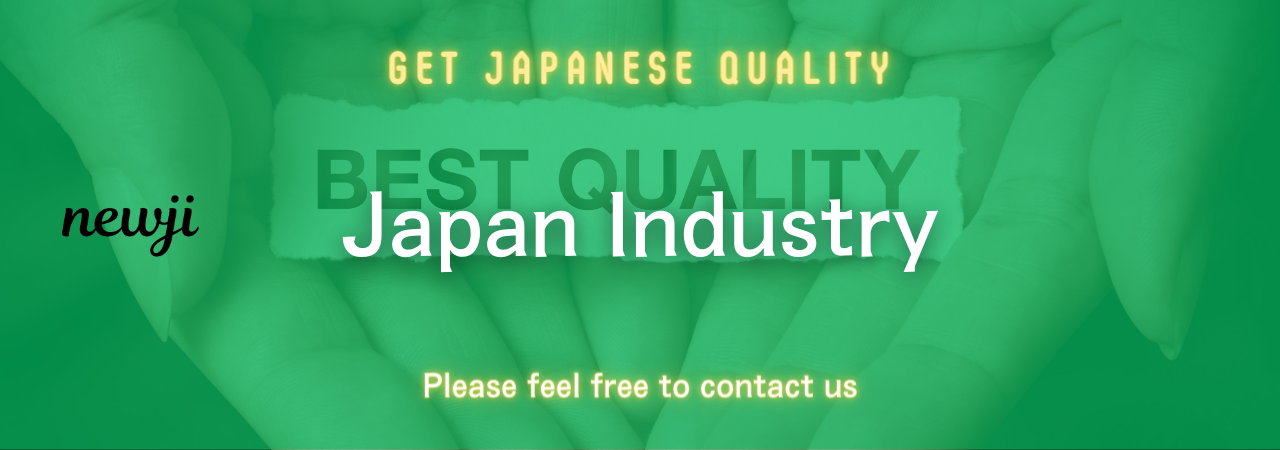
目次
What is 5S and Why is it Important?
The 5S methodology is a vital tool used in various industries to improve efficiency and organization.
It consists of five Japanese words: Seiri, Seiton, Seiso, Seiketsu, and Shitsuke which translate to Sort, Set in Order, Shine, Standardize, and Sustain, respectively.
Together, these principles help create a clean, efficient, and organized workplace.
Sort means removing unnecessary items from the workspace.
Set in Order involves organizing the necessary items in a way that they are easily accessible.
Shine entails cleaning the workspace and ensuring it stays clean.
Standardize means creating standards and protocols to maintain the achieved organization and cleanliness.
Lastly, Sustain focuses on making the 5S practices a habit within the workplace.
Benefits of 5S in Management
Implementing 5S in management brings numerous advantages.
First, it maximizes workplace efficiency by eliminating wasted time searching for items.
This leads to faster execution of tasks and ultimately increases productivity.
Next, it improves communication within teams by creating a structured and organized environment.
Clear labeling and systematic storage reduce the likelihood of misunderstandings and errors.
This fosters better teamwork and morale, enhancing overall job satisfaction.
Additionally, 5S practices play a crucial role in maintaining workplace safety.
Clean and well-organized environments significantly reduce the risk of accidents, such as trips and falls.
These practices also help in identifying potential hazards promptly, ensuring swift corrective actions.
Lastly, by sustaining a clean and organized workspace, management can minimize equipment wear and tear.
Properly maintained equipment functions efficiently and lasts longer, reducing costs for repairs and replacements.
Benefits of 5S in Indirect Operations
5S is not limited to direct production areas; it is equally effective in indirect operations such as office environments, warehousing, and logistics.
In offices, the 5S methodology helps organize files, documents, and digital data systematically.
This organized approach reduces time spent searching for information, leading to increased efficiency and better use of resources.
In warehousing and logistics, 5S principles ensure that inventory items are well-organized and stored in easily accessible locations.
This orderliness simplifies stocktaking, accelerates order fulfillment, and reduces the chances of misplaced inventory.
Consequently, this minimizes downtime and increases customer satisfaction.
Overall, the implementation of 5S in indirect operations results in enhanced resource management and cost savings across the board.
Visualization in Management
Visualization in management involves creating visual representations of information and processes to aid in understanding and improving operations.
Common tools for visualization include Kanban boards, process flowcharts, and visual dashboards.
Kanban boards are particularly useful for project management.
They provide a visual depiction of tasks, their progress, and the responsible individuals.
This clarity helps in tracking progress, identifying bottlenecks, and ensuring timely completion of tasks.
Process flowcharts, on the other hand, map out specific processes within an organization.
These charts highlight areas where efficiency can be improved and redundancies eliminated.
By making processes transparent, teams can work collaboratively towards streamlining operations.
Visual dashboards offer real-time insights into key performance indicators (KPIs).
They consolidate various metrics into a single view, allowing managers to monitor performance and make informed decisions swiftly.
This proactive approach helps in identifying trends, addressing issues, and ultimately driving continuous improvement.
Visualization in Indirect Operations
In indirect operations, visualization tools can significantly enhance service delivery and efficiency.
For instance, customer service departments can use visual dashboards to monitor call volumes, customer satisfaction scores, and response times.
This transparency helps in balancing workloads, identifying areas needing improvement, and delivering better customer experiences.
In human resource management, visualization can aid in mapping employee performance, attendance, and training needs.
Graphical representations of these data points help HR professionals make data-driven decisions regarding promotions, training programs, and workforce planning.
Additionally, in financial management, visual tools like charts and graphs can simplify the understanding of complex financial data.
This helps in creating clear financial reports and presentations, aiding stakeholders in making informed decisions.
Integrating 5S and Visualization for Optimal Results
Integrating 5S and visualization can amplify the benefits of each methodology.
For example, visual boards can be used to track the progress of 5S implementation within an organization.
Teams can use these boards to log their sorting activities, organize items, and maintain cleaning schedules.
Additionally, visual tools can aid in the standardization and sustainability aspects of 5S.
Templates for organizing items, cleaning checklists, and visual reminders can be displayed prominently to ensure adherence to standards.
Regular visual checks can ensure sustained compliance with 5S principles.
Combining 5S with visualization ensures that both methodologies are not only implemented but also maintained effectively.
This integration leads to a highly organized, efficient, and productive workspace.
Conclusion
The 5S methodology and visualization tools are both powerful strategies for enhancing efficiency and organization in management and indirect operations.
Implementing 5S results in cleaner, safer, and more efficient work environments.
Visualization tools, on the other hand, provide clarity and transparency, helping in better decision-making and streamlined operations.
Combining these strategies leads to an organized, visually transparent, and highly productive workplace.
Ultimately, this integration fosters a culture of continuous improvement, driving long-term success and sustainability within the organization.
By embracing 5S and visualization, management teams can ensure they are not only achieving but also maintaining the highest standards of operational excellence.
資料ダウンロード
QCD調達購買管理クラウド「newji」は、調達購買部門で必要なQCD管理全てを備えた、現場特化型兼クラウド型の今世紀最高の購買管理システムとなります。
ユーザー登録
調達購買業務の効率化だけでなく、システムを導入することで、コスト削減や製品・資材のステータス可視化のほか、属人化していた購買情報の共有化による内部不正防止や統制にも役立ちます。
NEWJI DX
製造業に特化したデジタルトランスフォーメーション(DX)の実現を目指す請負開発型のコンサルティングサービスです。AI、iPaaS、および先端の技術を駆使して、製造プロセスの効率化、業務効率化、チームワーク強化、コスト削減、品質向上を実現します。このサービスは、製造業の課題を深く理解し、それに対する最適なデジタルソリューションを提供することで、企業が持続的な成長とイノベーションを達成できるようサポートします。
オンライン講座
製造業、主に購買・調達部門にお勤めの方々に向けた情報を配信しております。
新任の方やベテランの方、管理職を対象とした幅広いコンテンツをご用意しております。
お問い合わせ
コストダウンが利益に直結する術だと理解していても、なかなか前に進めることができない状況。そんな時は、newjiのコストダウン自動化機能で大きく利益貢献しよう!
(Β版非公開)