- お役立ち記事
- Case Studies of Quality Assurance Department Initiatives to Prevent Defective Products from Reaching Customers
Case Studies of Quality Assurance Department Initiatives to Prevent Defective Products from Reaching Customers
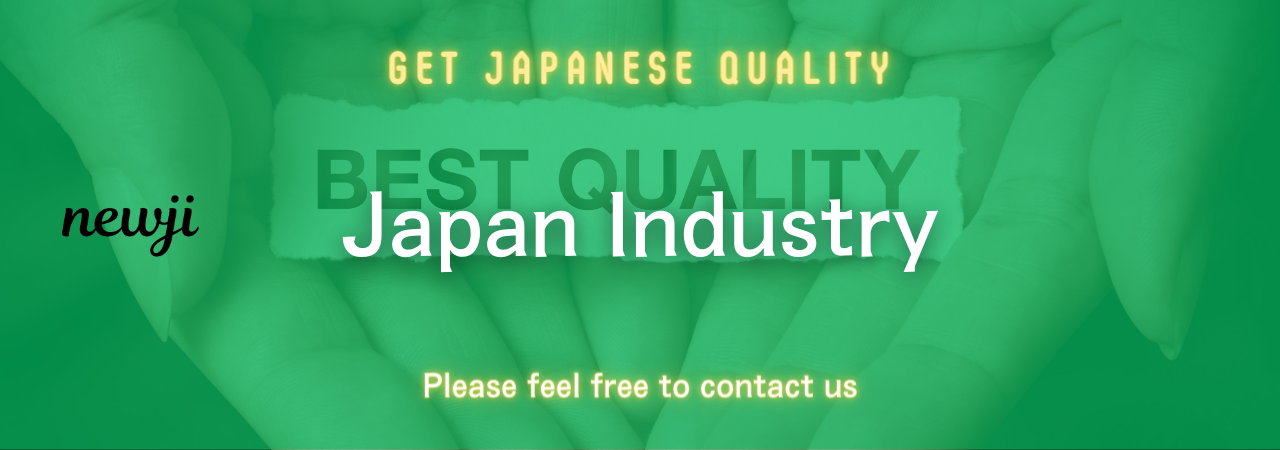
In any business, maintaining the quality of products is paramount.
The Quality Assurance (QA) department plays a crucial role in ensuring that products meet the specified requirements and customer expectations.
In this article, we will explore a few case studies of QA department initiatives that have successfully prevented defective products from reaching customers.
目次
Implementing Rigorous Testing Protocols
One successful initiative comes from a leading electronics manufacturing company.
Their QA department implemented a series of rigorous testing protocols at every stage of the production process.
Each product went through multiple quality checks, starting from the raw material inspection to the final product evaluation.
Raw Material Inspection
Inspecting raw materials is the first step in ensuring product quality.
By using advanced analytical tools and techniques, the QA department identified any potential defects before the materials entered the manufacturing process.
This proactive approach significantly reduced the chances of product defects caused by substandard raw materials.
In-Process Quality Control
The next phase involved real-time monitoring and testing during the manufacturing process.
Sensor-based technologies and machine learning algorithms were employed to detect anomalies or deviations from set standards.
Whenever an issue was detected, the production line was immediately halted and corrections were made, ensuring only defect-free products moved forward.
Final Inspection
At the final stage, a thorough inspection was conducted to catch any remaining defects.
Both human inspectors and automated systems worked in tandem to scrutinize the finished products.
This multi-layered inspection system ensured that only high-quality products were shipped to customers.
Employee Training and Engagement
Another case study shows the importance of employee training and engagement in maintaining product quality.
A pharmaceutical company invested in regular training programs for their staff, focusing on quality control procedures, compliance, and new technologies.
Comprehensive Training Programs
The training programs covered various aspects of quality assurance, including the importance of adhering to standard operating procedures (SOPs) and identifying potential defects.
Employees were also trained in the latest testing technologies and regulatory requirements, making them more adept at ensuring product quality.
Employee Engagement Initiatives
The company introduced several initiatives to keep employees engaged and motivated in their roles.
Incentives and recognition programs were put in place to reward employees who demonstrated a strong commitment to quality.
This fostered a culture of quality within the organization, with employees taking an active role in preventing defects.
Leveraging Technology for Quality Assurance
A third example involves a food manufacturing company that leveraged technology to enhance their QA processes.
Adopting cutting-edge technologies like predictive analytics and blockchain, they were able to minimize defects and improve overall product quality.
Predictive Analytics
By using predictive analytics, the company could anticipate potential defects even before they occurred.
Data from previous production cycles were analyzed to identify patterns and trends.
This predictive approach allowed them to make adjustments proactively, thereby preventing defects and improving yield.
Blockchain for Traceability
The use of blockchain technology ensured the traceability of products throughout the supply chain.
Each product was tagged and its journey from raw material to finished good was recorded on an immutable blockchain ledger.
This level of transparency made it easier to identify the source of defects and ensure accountability, thereby improving overall product quality.
Continuous Improvement and Feedback Loops
A consumer electronics company implemented a robust continuous improvement program to enhance their QA processes.
By establishing feedback loops and encouraging continual learning, they were able to keep their quality standards high.
Customer Feedback
One of the key components of their initiative was to actively seek and analyze customer feedback.
Surveys, reviews, and support queries were regularly reviewed to identify common issues and areas for improvement.
This customer-centric approach allowed the company to make necessary adjustments and prevent recurring defects.
Internal Audits and Reviews
Regular internal audits were conducted to assess the effectiveness of quality assurance processes.
By reviewing and analyzing the results, the company identified gaps and implemented corrective actions swiftly.
This continuous evaluation helped them refine their QA procedures and maintain high product quality.
Collaborative Supplier Management
A final case study involves an automotive parts manufacturer that achieved significant success through collaborative supplier management.
Recognizing that quality issues often stem from the supply chain, the company took a proactive approach to work closely with their suppliers.
Supplier Audits
The QA department conducted regular supplier audits to ensure that the materials and components supplied met the required standards.
These audits included on-site inspections and quality assessments, fostering a transparent and collaborative relationship with suppliers.
Joint Quality Improvement Programs
The company launched joint quality improvement programs with key suppliers.
By working together, they identified root causes of defects and implemented corrective actions.
This collaborative approach not only improved supplier quality but also strengthened the entire supply chain, ensuring the final product met high standards.
In conclusion, these case studies highlight the crucial role of the QA department in preventing defective products from reaching customers.
By implementing rigorous testing protocols, investing in employee training, leveraging technology, establishing continuous improvement programs, and collaborating with suppliers, businesses can significantly enhance their product quality.
These initiatives not only protect the company’s reputation but also ensure customer satisfaction and loyalty.
資料ダウンロード
QCD調達購買管理クラウド「newji」は、調達購買部門で必要なQCD管理全てを備えた、現場特化型兼クラウド型の今世紀最高の購買管理システムとなります。
ユーザー登録
調達購買業務の効率化だけでなく、システムを導入することで、コスト削減や製品・資材のステータス可視化のほか、属人化していた購買情報の共有化による内部不正防止や統制にも役立ちます。
NEWJI DX
製造業に特化したデジタルトランスフォーメーション(DX)の実現を目指す請負開発型のコンサルティングサービスです。AI、iPaaS、および先端の技術を駆使して、製造プロセスの効率化、業務効率化、チームワーク強化、コスト削減、品質向上を実現します。このサービスは、製造業の課題を深く理解し、それに対する最適なデジタルソリューションを提供することで、企業が持続的な成長とイノベーションを達成できるようサポートします。
オンライン講座
製造業、主に購買・調達部門にお勤めの方々に向けた情報を配信しております。
新任の方やベテランの方、管理職を対象とした幅広いコンテンツをご用意しております。
お問い合わせ
コストダウンが利益に直結する術だと理解していても、なかなか前に進めることができない状況。そんな時は、newjiのコストダウン自動化機能で大きく利益貢献しよう!
(Β版非公開)