- お役立ち記事
- Optimizing Manufacturing Techniques to Compete Globally
Optimizing Manufacturing Techniques to Compete Globally
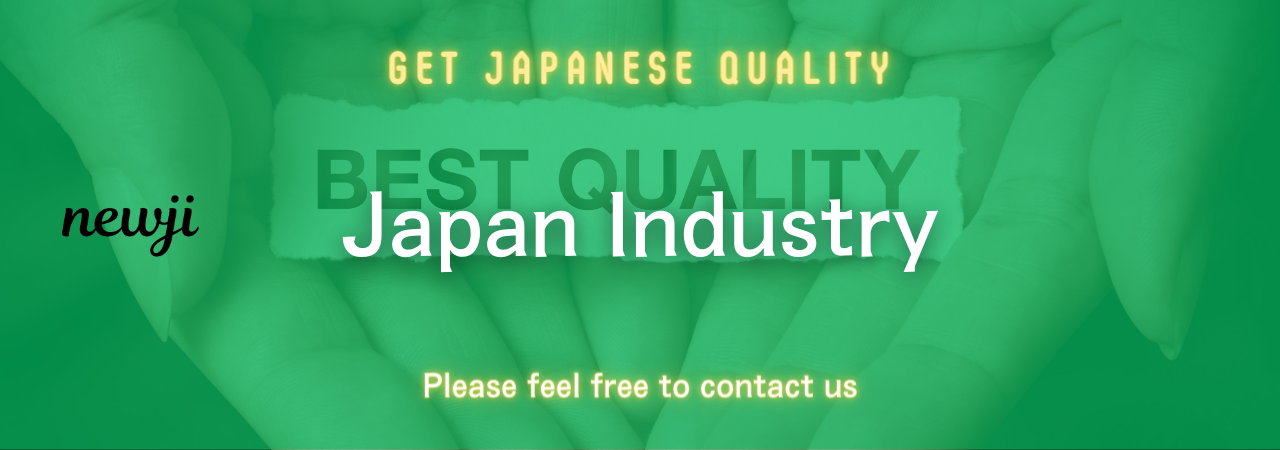
In today’s fast-paced world, industries are continually evolving.
Companies in the manufacturing sector must stay ahead of the curve to remain competitive on a global scale.
Optimizing manufacturing techniques is not just about sustaining growth; it also involves making processes more efficient, reducing costs, and boosting quality.
By focusing on these aspects, manufacturers can create a sustainable competitive advantage.
Here, we will explore various ways in which this optimization can be achieved.
目次
Embracing Automation and Technology
Automation is no longer the future; it’s the present.
Incorporating advanced technologies in your manufacturing processes can drastically improve efficiency.
From robotics to artificial intelligence (AI), technology provides a quicker, more accurate, and reliable way to perform tasks.
Factories using automated assembly lines often see increased output and decreased error rates.
AI can help in predictive maintenance, lowering downtime by anticipating when a machine needs servicing before a failure occurs.
Benefits of Robotics
Robots can work tirelessly, speeding up tasks that would take humans much longer to complete.
These machines can perform repetitive tasks with consistent quality, reducing human error.
Moreover, they can work in hazardous conditions where human safety could be compromised.
Robots not only execute jobs faster but can also work round the clock, improving production schedules and meeting customer demands efficiently.
Leveraging AI
Artificial Intelligence offers numerous applications in manufacturing.
One essential function is predictive maintenance.
Using sensors and data analytics, AI systems can foresee when equipment is likely to fail and schedule timely maintenance.
This approach not only reduces downtime but also extends the lifespan of machinery.
AI algorithms can also enhance quality control by automatically identifying defects in products during the production process.
Adopting Lean Manufacturing Principles
Lean manufacturing is a methodology aimed at creating more value with fewer resources.
It focuses on minimizing waste within the manufacturing system.
By adopting lean principles, companies can streamline production processes, reduce waste, and improve overall efficiency.
Value Stream Mapping
Value stream mapping is a lean-management method used to depict and analyze the flow of materials and information required to bring a product to the customer.
By examining each step in the process, manufacturers can identify and eliminate inefficiencies.
Streamlining these processes results in faster production times, lower costs, and enhanced product quality.
5S Methodology
The 5S methodology stands for Sort, Set in order, Shine, Standardize, and Sustain.
This approach aims to organize the workplace efficiently, reduce waste, and maintain high levels of cleanliness and efficiency.
Periodically sorting through items ensures that only necessary items are kept, reducing clutter.
Setting items in order makes tools and materials easy to find.
Shining the workplace ensures it’s clean and safe, while Standardizing maintains these practices.
Finally, Sustaining these measures keeps operations running smoothly over time.
Investing in Workforce Skills
While technology plays a critical role, human skills are equally important in manufacturing.
A well-trained workforce can efficiently operate complex machinery, adapt to technological changes, and contribute creative solutions to problems.
On-the-Job Training
On-the-job training programs are crucial for workers to get hands-on experience with new machinery and tools.
Such programs help employees understand the intricacies of equipment they’ll be working with, increasing productivity and reducing error rates.
Continuous training ensures that the workforce remains updated with the latest technological advancements and manufacturing practices.
Encouraging Innovation
Employees should be encouraged to think outside the box and come up with innovative solutions that could improve manufacturing processes.
Regular brainstorming sessions and an open-door policy for suggestions can foster a culture of innovation.
Allowing employees to contribute ideas can lead to process improvements that may not be immediately obvious to management.
Enhancing Supply Chain Management
Effective supply chain management is vital for optimizing manufacturing techniques.
A well-managed supply chain ensures timely delivery of raw materials, efficient production schedules, and on-time delivery of finished goods.
Supplier Relationships
Building strong relationships with suppliers can lead to better pricing, improved quality of raw materials, and timely deliveries.
Regular communication and collaboration can foster a partnership approach, where both parties work together to solve common problems.
Long-term relationships with reliable suppliers add stability to the supply chain, reducing unexpected disruptions.
Inventory Management
Efficient inventory management techniques like Just-in-Time (JIT) can significantly reduce waste and storage costs.
With JIT, materials are ordered and received only as they are needed, eliminating the need for large storage spaces and reducing the risk of overstocking or stockouts.
An optimized inventory system ensures that production lines keep moving without unnecessary delays or interruptions.
Implementing Sustainable Practices
Sustainability is becoming increasingly critical in the manufacturing industry.
Adopting eco-friendly practices can not only reduce environmental impact but also attract customers who are conscious of corporate social responsibility.
Energy Efficiency
Reducing energy consumption is a straightforward way to cut costs and improve sustainability.
Simple measures, such as using energy-efficient lighting and machinery, can make a significant difference.
Monitoring energy use through smart meters can help identify areas where consumption can be reduced.
Waste Management
Implementing recycling programs and minimizing waste generated during production can contribute to a company’s sustainability goals.
Waste materials can often be repurposed or recycled, reducing the need for new raw materials.
Effective waste management strategies not only benefit the environment but also contribute to cost savings.
Conclusion
Optimizing manufacturing techniques is crucial for competing on a global scale.
By embracing automation and technology, adopting lean manufacturing principles, investing in workforce skills, enhancing supply chain management, and implementing sustainable practices, companies can create a significant competitive advantage.
These strategies not only improve efficiency and reduce costs but also ensure that products meet high-quality standards.
Ultimately, a well-optimized manufacturing process leads to greater customer satisfaction and business success.
資料ダウンロード
QCD調達購買管理クラウド「newji」は、調達購買部門で必要なQCD管理全てを備えた、現場特化型兼クラウド型の今世紀最高の購買管理システムとなります。
ユーザー登録
調達購買業務の効率化だけでなく、システムを導入することで、コスト削減や製品・資材のステータス可視化のほか、属人化していた購買情報の共有化による内部不正防止や統制にも役立ちます。
NEWJI DX
製造業に特化したデジタルトランスフォーメーション(DX)の実現を目指す請負開発型のコンサルティングサービスです。AI、iPaaS、および先端の技術を駆使して、製造プロセスの効率化、業務効率化、チームワーク強化、コスト削減、品質向上を実現します。このサービスは、製造業の課題を深く理解し、それに対する最適なデジタルソリューションを提供することで、企業が持続的な成長とイノベーションを達成できるようサポートします。
オンライン講座
製造業、主に購買・調達部門にお勤めの方々に向けた情報を配信しております。
新任の方やベテランの方、管理職を対象とした幅広いコンテンツをご用意しております。
お問い合わせ
コストダウンが利益に直結する術だと理解していても、なかなか前に進めることができない状況。そんな時は、newjiのコストダウン自動化機能で大きく利益貢献しよう!
(Β版非公開)