- お役立ち記事
- Sandwich Molding Process: A Practical Guide to Multilayer Molding
Sandwich Molding Process: A Practical Guide to Multilayer Molding
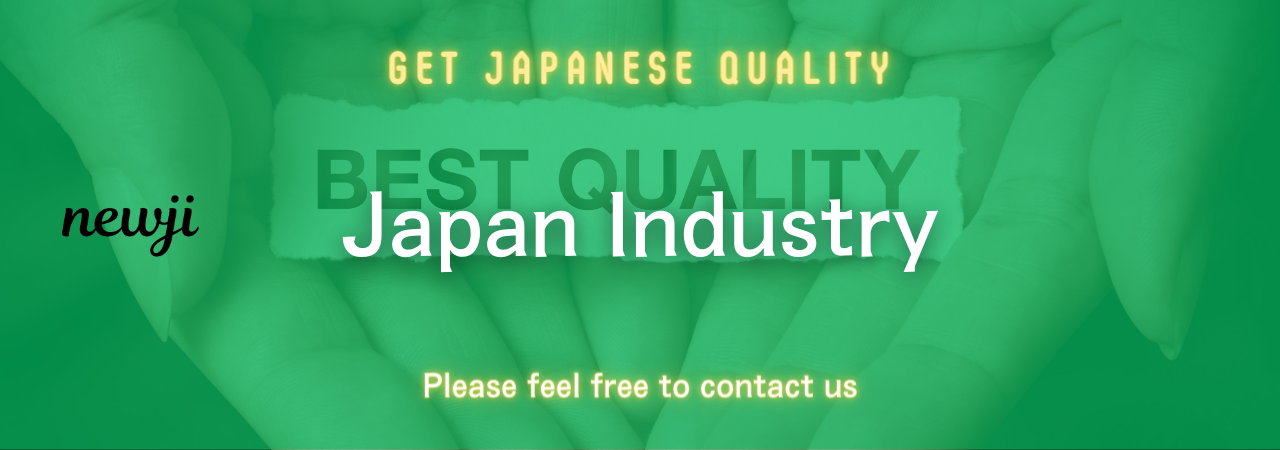
The sandwich molding process is a versatile and innovative technique used in the production of multilayer plastic parts.
It allows for the creation of components with a unique combination of properties by layering different materials within a single part.
This process is particularly useful in industries that require parts to have both aesthetic and functional characteristics.
In this article, we will dive into the intricacies of sandwich molding, its benefits, applications, and the steps involved in mastering this process.
目次
What is Sandwich Molding?
Sandwich molding, also known as co-injection molding or two-shot molding, involves the simultaneous injection of two different types of plastic materials into a mold.
These materials typically consist of an outer skin and a core material.
The skin material is usually a high-quality, aesthetically pleasing polymer, while the core material can be a less expensive or recycled plastic.
This combination helps to reduce costs and optimize the properties of the final part.
The Science Behind Sandwich Molding
During the molding process, the core material is injected first, followed closely by the skin material.
The core material flows through the center of the mold, while the skin material forms a continuous layer around it.
As the materials cool and solidify, they bond together to create a single, cohesive part.
This method ensures that the outer surface of the part has the desired appearance, while the overall part maintains the necessary structural integrity and performance.
Benefits of Sandwich Molding
The sandwich molding process offers several advantages over traditional single-material molding techniques.
Here are some key benefits:
Cost Efficiency
By using a less expensive or recycled material for the core, manufacturers can significantly reduce production costs without compromising the quality of the final product.
This is particularly beneficial for high-volume production runs, where cost savings can be substantial.
Enhanced Design Flexibility
Sandwich molding allows for greater flexibility in design, enabling the creation of complex shapes and intricate details that may be difficult or impossible to achieve with single-material molding.
This is especially important for products that require both functional and aesthetic properties.
Improved Material Properties
The combination of two different materials within a single part can enhance its overall performance.
For example, the outer skin can provide resistance to wear, UV radiation, and chemicals, while the core material can offer structural strength and impact resistance.
This results in a part that is more durable and longer-lasting.
Environmental Benefits
Using recycled materials for the core can help reduce waste and lower the environmental impact of the manufacturing process.
This is an essential consideration for companies seeking to adopt more sustainable practices and meet regulatory requirements.
Applications of Sandwich Molding
The versatility of sandwich molding makes it suitable for a wide range of applications across various industries.
Here are some examples of products that can benefit from this process:
Automotive Components
In the automotive industry, sandwich molding is used to produce lightweight and durable parts such as bumpers, dashboards, and interior panels.
The outer skin provides a high-quality finish, while the core material offers strength and impact resistance.
Consumer Goods
Sandwich molding is ideal for manufacturing consumer goods like household appliances, toys, and electronic enclosures.
The process allows for intricate designs and vibrant colors, enhancing the aesthetic appeal of the products.
Packaging
In the packaging industry, sandwich molding is employed to create containers and bottles with a high-quality outer shell and a cost-effective core.
This approach ensures that the packaging is both visually appealing and functional, meeting the needs of both manufacturers and consumers.
Medical Devices
Medical device manufacturers utilize sandwich molding to produce components that require a combination of biocompatibility, durability, and precision.
Examples include surgical instruments, diagnostic equipment housings, and prosthetic devices.
The Sandwich Molding Process: Step-by-Step
To better understand how sandwich molding works, let’s break down the process into its key steps:
1. Mold Design
The first step in the sandwich molding process is designing the mold.
The mold must be engineered to accommodate the flow of both the core and skin materials, ensuring even distribution and proper bonding.
This requires careful planning and precise engineering to achieve the desired final product.
2. Material Selection
Choosing the right materials for the core and skin is crucial to the success of the sandwich molding process.
Factors such as cost, mechanical properties, and compatibility must be considered.
The core material is typically a low-cost or recycled plastic, while the skin material is a higher-quality polymer with the desired surface properties.
3. Injection and Bonding
Once the mold and materials are prepared, the injection process begins.
The core material is injected into the mold first, followed by the skin material.
This sequence ensures that the core material flows through the center, while the skin material forms a continuous outer layer.
The materials bond together as they cool and solidify, resulting in a single, cohesive part.
4. Cooling and Ejection
After the injection process is complete, the molded part is allowed to cool and solidify within the mold.
Once the part has reached the desired hardness, it is ejected from the mold and inspected for quality.
Cooling time is a critical factor in ensuring the part’s structural integrity and surface finish.
5. Quality Control
Quality control is an essential step in the sandwich molding process.
Each part must be carefully inspected to ensure that it meets the required specifications and performance standards.
This may involve visual inspections, mechanical testing, and other quality assurance measures to verify the integrity of the part.
Conclusion
The sandwich molding process is a highly effective technique for producing multilayer plastic parts with a combination of aesthetic and functional properties.
By leveraging the benefits of cost efficiency, design flexibility, improved material properties, and environmental sustainability, manufacturers can create high-quality products that meet the demands of various industries.
Understanding the step-by-step process of sandwich molding, from mold design to quality control, is essential for mastering this innovative manufacturing technique.
As industries continue to evolve, the sandwich molding process is poised to play a crucial role in the development of advanced, versatile, and sustainable plastic components.
資料ダウンロード
QCD調達購買管理クラウド「newji」は、調達購買部門で必要なQCD管理全てを備えた、現場特化型兼クラウド型の今世紀最高の購買管理システムとなります。
ユーザー登録
調達購買業務の効率化だけでなく、システムを導入することで、コスト削減や製品・資材のステータス可視化のほか、属人化していた購買情報の共有化による内部不正防止や統制にも役立ちます。
NEWJI DX
製造業に特化したデジタルトランスフォーメーション(DX)の実現を目指す請負開発型のコンサルティングサービスです。AI、iPaaS、および先端の技術を駆使して、製造プロセスの効率化、業務効率化、チームワーク強化、コスト削減、品質向上を実現します。このサービスは、製造業の課題を深く理解し、それに対する最適なデジタルソリューションを提供することで、企業が持続的な成長とイノベーションを達成できるようサポートします。
オンライン講座
製造業、主に購買・調達部門にお勤めの方々に向けた情報を配信しております。
新任の方やベテランの方、管理職を対象とした幅広いコンテンツをご用意しております。
お問い合わせ
コストダウンが利益に直結する術だと理解していても、なかなか前に進めることができない状況。そんな時は、newjiのコストダウン自動化機能で大きく利益貢献しよう!
(Β版非公開)