- お役立ち記事
- Future-Oriented Talent Development Strategies in Manufacturing and the Importance of Digital Skills
Future-Oriented Talent Development Strategies in Manufacturing and the Importance of Digital Skills
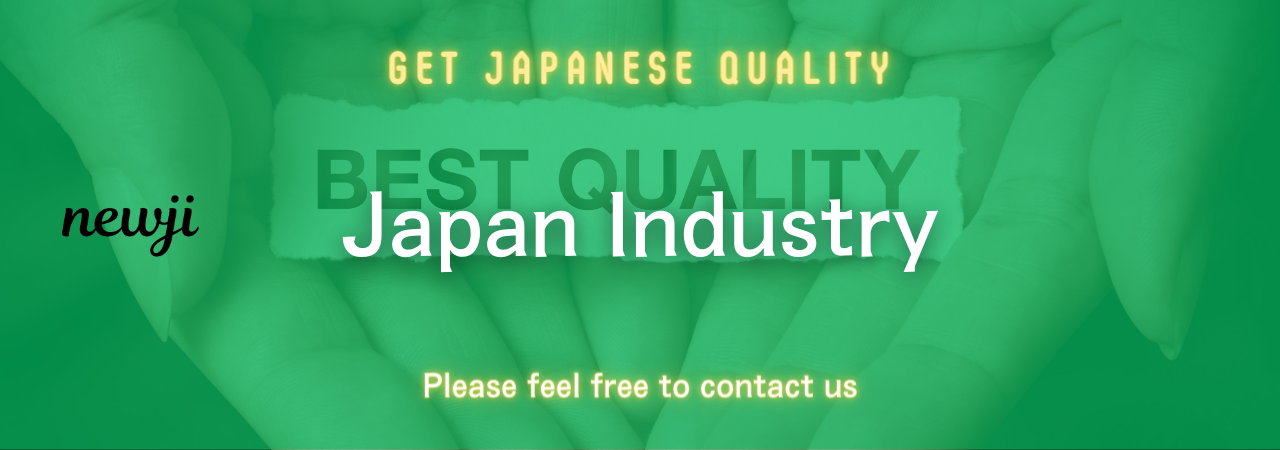
Today’s manufacturing landscape is undergoing significant changes, driven by rapid technological advancements and shifting consumer demands.
To keep pace with these transformations, businesses must focus on cultivating future-oriented talent.
In particular, digital skills have become crucial.
In this article, we’ll explore effective talent development strategies in manufacturing and emphasize the importance of digital skills.
目次
Why Talent Development is Crucial in Manufacturing
The manufacturing sector is continuously evolving.
Automation, advanced robotics, and IoT (Internet of Things) are becoming industry standards.
In such a dynamic environment, fostering talent with the right skill set is crucial for maintaining competitive advantage.
Skilled employees can adapt to new technologies and methodologies more quickly.
They can also drive innovation, leading to improved productivity and quality.
Without a focus on talent development, companies risk falling behind their competitors, missing out on efficiency gains and market opportunities.
The Changing Skill Requirements
The skills required in manufacturing today are vastly different from those needed a decade ago.
While technical skills remain important, digital literacy is becoming equally essential.
Employees need to understand and work with complex software systems, data analytics, and automated machinery.
Traditional roles are being redefined.
Maintenance technicians, for example, now often need skills in predictive maintenance technologies and data analysis.
Similarly, production managers need to understand supply chain software and real-time analytics to optimize operations.
Effective Talent Development Strategies
To nurture future-oriented talent, companies need to implement comprehensive development strategies.
Below are some effective approaches:
Continuous Learning and Development
In a fast-evolving industry, continuous learning is indispensable.
Companies should offer regular training programs to help their employees stay updated with the latest technologies and methodologies.
This could include workshops, online courses, and training seminars.
Partnering with educational institutions can also be beneficial.
Collaborations can facilitate specialized training programs tailored to industry needs.
Offering incentives for further education can motivate employees to continuously enhance their skill set.
Mentorship and Coaching Programs
Mentorship and coaching can significantly accelerate learning.
Senior employees with extensive experience can provide invaluable guidance to newer staff members.
Formal mentorship programs can help in transferring critical knowledge and skills effectively.
These programs should be structured with clear objectives and outcomes.
Regular feedback and progress assessments can ensure that the mentorship is productive and aligns with the company’s goals.
Cultivating a Culture of Innovation
Fostering a culture of innovation encourages employees to think creatively and adopt new technologies.
This can be achieved by promoting open communication, rewarding innovative ideas, and providing resources for experimentation.
Hackathons and innovation sprints are excellent methods to spark creativity.
These events encourage employees to collaborate across departments, share ideas, and develop innovative solutions to real-world problems.
Diverse Skill Development
Manufacturing roles are becoming increasingly interdisciplinary.
Employees benefit from having a diverse skill set that allows them to understand various aspects of the production process.
Encouraging cross-functional training can help employees develop this versatility.
Job rotation programs can also provide employees with a broader perspective of the organization’s operations.
These programs allow employees to work in different departments, gaining insights and skills that contribute to their overall development.
The Importance of Digital Skills in Manufacturing
Digital skills are no longer a luxury but a necessity in modern manufacturing.
Here’s why they are so crucial:
Automation and Robotics
Automation and robotics are transforming the manufacturing floor.
Employees need skills in programming and operating automated systems.
This includes understanding how to troubleshoot issues and optimize the performance of these systems.
Skilled workers in robotics can reduce downtime and improve efficiency.
They can also contribute to the design and implementation of automated solutions that can lead to significant cost savings.
Data-Driven Decision Making
Data analytics is becoming integral to manufacturing.
From predictive maintenance to quality control, data-driven insights can optimize operations.
Employees must be proficient in data analysis tools to interpret and use data effectively.
Training in data analytics can empower employees to identify trends, make informed decisions, and predict future outcomes.
This proactive approach can lead to improved quality, efficiency, and competitiveness.
Cybersecurity Awareness
With the increasing reliance on digital systems, cybersecurity is a major concern.
Manufacturing facilities are often targets for cyber-attacks, which can disrupt production and compromise sensitive data.
Training employees in cybersecurity best practices is essential.
Awareness programs can educate employees on recognizing threats, such as phishing attacks, and responding appropriately.
A culture of cybersecurity can safeguard the integrity of the digital infrastructure.
Digital Collaboration Tools
Digital collaboration tools are essential for efficient communication and project management.
Employees should be adept at using platforms that facilitate real-time coordination, file sharing, and workflow management.
Training on these tools can enhance teamwork, reduce misunderstandings, and streamline processes.
This becomes even more critical in the context of global supply chains and remote work scenarios.
Conclusion
Investing in future-oriented talent development strategies is imperative for the success of modern manufacturing companies.
Prioritizing digital skills alongside traditional technical skills can drive innovation and competitiveness.
By implementing comprehensive learning programs, fostering a culture of innovation, and emphasizing diverse skill development, companies can equip their workforce to meet the challenges and opportunities of the digital age.
Ultimately, the focus on digital skills and continuous development can transform manufacturing operations and secure a sustainable future.
資料ダウンロード
QCD調達購買管理クラウド「newji」は、調達購買部門で必要なQCD管理全てを備えた、現場特化型兼クラウド型の今世紀最高の購買管理システムとなります。
ユーザー登録
調達購買業務の効率化だけでなく、システムを導入することで、コスト削減や製品・資材のステータス可視化のほか、属人化していた購買情報の共有化による内部不正防止や統制にも役立ちます。
NEWJI DX
製造業に特化したデジタルトランスフォーメーション(DX)の実現を目指す請負開発型のコンサルティングサービスです。AI、iPaaS、および先端の技術を駆使して、製造プロセスの効率化、業務効率化、チームワーク強化、コスト削減、品質向上を実現します。このサービスは、製造業の課題を深く理解し、それに対する最適なデジタルソリューションを提供することで、企業が持続的な成長とイノベーションを達成できるようサポートします。
オンライン講座
製造業、主に購買・調達部門にお勤めの方々に向けた情報を配信しております。
新任の方やベテランの方、管理職を対象とした幅広いコンテンツをご用意しております。
お問い合わせ
コストダウンが利益に直結する術だと理解していても、なかなか前に進めることができない状況。そんな時は、newjiのコストダウン自動化機能で大きく利益貢献しよう!
(Β版非公開)