- お役立ち記事
- Collaboration Between Procurement and Engineering Departments: The Importance of Early Involvement in New Product Development
Collaboration Between Procurement and Engineering Departments: The Importance of Early Involvement in New Product Development
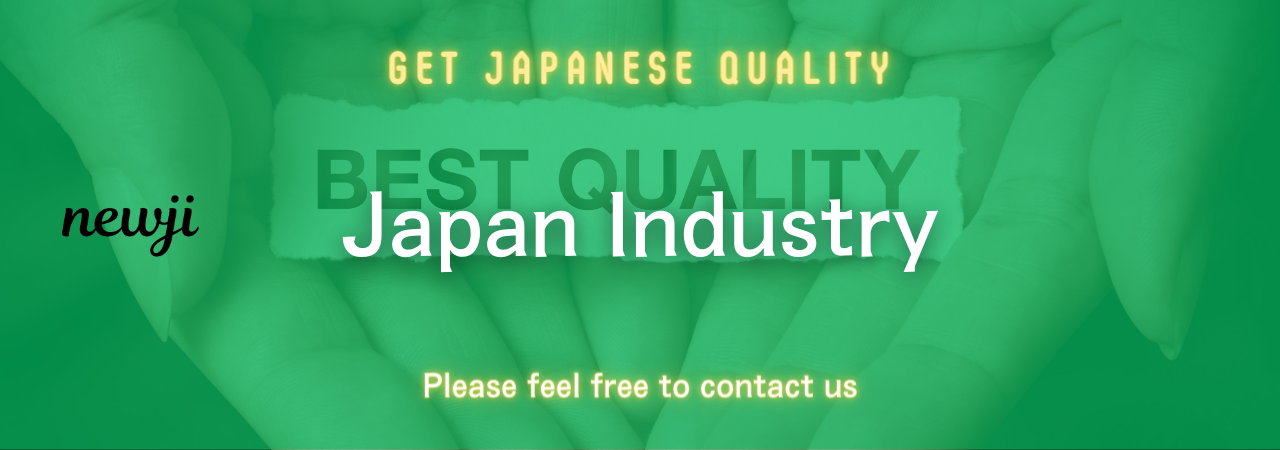
目次
Introduction
In today’s fast-paced and competitive market, the collaboration between different departments within an organization is more crucial than ever.
One of the most effective collaborations is between the procurement and engineering departments, especially in the early stages of new product development.
This collaborative effort can lead to significant benefits, including cost savings, innovation, and time efficiency.
Why Early Involvement is Critical
Cost Efficiency
One of the main reasons for involving procurement early in the new product development process is cost efficiency.
Procurement professionals have extensive knowledge of the supply market, including the best suppliers and market trends.
Involving them early ensures that the engineering team can design products with cost-effective materials and components right from the start.
Supplier Selection
Early involvement also enables better supplier selection.
Procurement teams can work closely with engineers to find suppliers who meet both the technical requirements and budget constraints.
This collaborative selection process can lead to more reliable and higher-quality supplies, ultimately affecting the product’s quality and performance.
Time Savings
When procurement and engineering teams work together from the beginning, they can develop a timeline that incorporates the sourcing and manufacturing processes.
This cohesive planning reduces delays and speeds up the time-to-market for new products.
Early collaboration also helps in anticipating potential issues, allowing for quicker resolutions without stalling the project.
The Role of Procurement in New Product Development
Market Insights
Procurement professionals bring invaluable market insights that can influence product design.
They have an eye on emerging trends, new materials, and innovative processes.
By sharing this information with the engineering team, they can contribute to more market-relevant and innovative product designs.
Risk Management
Assessing risks is a critical part of procurement’s role in new product development.
They evaluate the supply chain for potential disruptions, quality issues, and price volatility.
This risk assessment allows the engineering team to make informed decisions about materials and components, mitigating potential risks before they become problematic.
Cost Analysis
Procurement’s expertise in cost analysis provides a clear picture of the financial implications of different design choices.
They can offer alternative suppliers or materials that meet the specifications while also keeping the project within budget.
This financial acumen helps the engineering team make cost-effective decisions without compromising quality.
How Engineering Benefits from Procurement
Access to Latest Technologies
When procurement and engineering teams collaborate, the engineering team gains access to the latest technologies and innovations from suppliers.
Procurement professionals, through their relationships with suppliers, can often secure early samples or demonstrations of new technologies.
This allows the engineering team to integrate cutting-edge features into their designs early on.
Streamlined Processes
Engineering teams often face tight deadlines and challenging specifications.
A collaborative effort with procurement streamlines the whole process.
Procurement can handle supplier negotiations, sample evaluations, and material verification, allowing engineers to focus more on design and development.
This division of labor ensures a smoother workflow and a more efficient development process.
Better Quality Control
Quality control is a shared responsibility.
Early involvement of procurement means that there are multiple checkpoints for quality across different stages of the supply chain.
Procurement teams work with reliable suppliers, ensuring that the materials and components used are of high quality.
This attention to detail results in a more robust and reliable final product.
Implementing Effective Collaboration
Regular Meetings
Setting up regular meetings between procurement and engineering teams is essential for effective collaboration.
These meetings provide a platform for sharing updates, discussing challenges, and brainstorming solutions.
Regular communication ensures that both teams are aligned and working towards common goals.
Integrated Project Management Tools
Using integrated project management tools can facilitate better collaboration.
These tools allow both teams to track progress, share documents, and manage tasks.
When both procurement and engineering can see the same project timeline and milestone progress, it minimizes miscommunications and enhances productivity.
Joint Training Programs
Providing joint training programs for procurement and engineering teams can help them better understand each other’s roles and responsibilities.
These programs can foster better communication and collaboration, ensuring that both teams are on the same page regarding new product development processes.
Challenges to Overcome
Cultural Differences
One of the main challenges in fostering collaboration is the cultural differences between departments.
Engineers and procurement professionals often have different priorities and working styles.
Creating a culture of mutual respect and understanding is essential for successful collaboration.
Communication Barriers
Effective communication can sometimes be a challenge, especially when technical jargon is involved.
Encouraging clear and open communication, and providing training on technical and procurement terminology, can help bridge this gap.
Resource Constraints
Both departments often face resource constraints, be it time, budget, or personnel.
Effective collaboration requires a strategic allocation of resources to ensure that neither team is stretched too thin.
Balancing resources while maintaining focus on critical tasks will lead to a more effective collaboration.
Conclusion
The early involvement of procurement in the new product development process is vital for achieving cost efficiency, quality control, and timely market entry.
By leveraging procurement’s market insights, risk management capabilities, and cost analysis expertise, engineering teams can design better products more efficiently.
Fostering effective communication, utilizing integrated tools, and overcoming cultural differences will lead to a stronger collaboration, ultimately driving innovation and business success.
Investing in collaboration between procurement and engineering departments is not just a best practice; it is a strategic advantage in today’s competitive landscape.
資料ダウンロード
QCD調達購買管理クラウド「newji」は、調達購買部門で必要なQCD管理全てを備えた、現場特化型兼クラウド型の今世紀最高の購買管理システムとなります。
ユーザー登録
調達購買業務の効率化だけでなく、システムを導入することで、コスト削減や製品・資材のステータス可視化のほか、属人化していた購買情報の共有化による内部不正防止や統制にも役立ちます。
NEWJI DX
製造業に特化したデジタルトランスフォーメーション(DX)の実現を目指す請負開発型のコンサルティングサービスです。AI、iPaaS、および先端の技術を駆使して、製造プロセスの効率化、業務効率化、チームワーク強化、コスト削減、品質向上を実現します。このサービスは、製造業の課題を深く理解し、それに対する最適なデジタルソリューションを提供することで、企業が持続的な成長とイノベーションを達成できるようサポートします。
オンライン講座
製造業、主に購買・調達部門にお勤めの方々に向けた情報を配信しております。
新任の方やベテランの方、管理職を対象とした幅広いコンテンツをご用意しております。
お問い合わせ
コストダウンが利益に直結する術だと理解していても、なかなか前に進めることができない状況。そんな時は、newjiのコストダウン自動化機能で大きく利益貢献しよう!
(Β版非公開)