- お役立ち記事
- Fundamentals of Setting Up Processes to Prevent Defects and Mistake-Proofing (Poka-Yoke) and Human Error Prevention
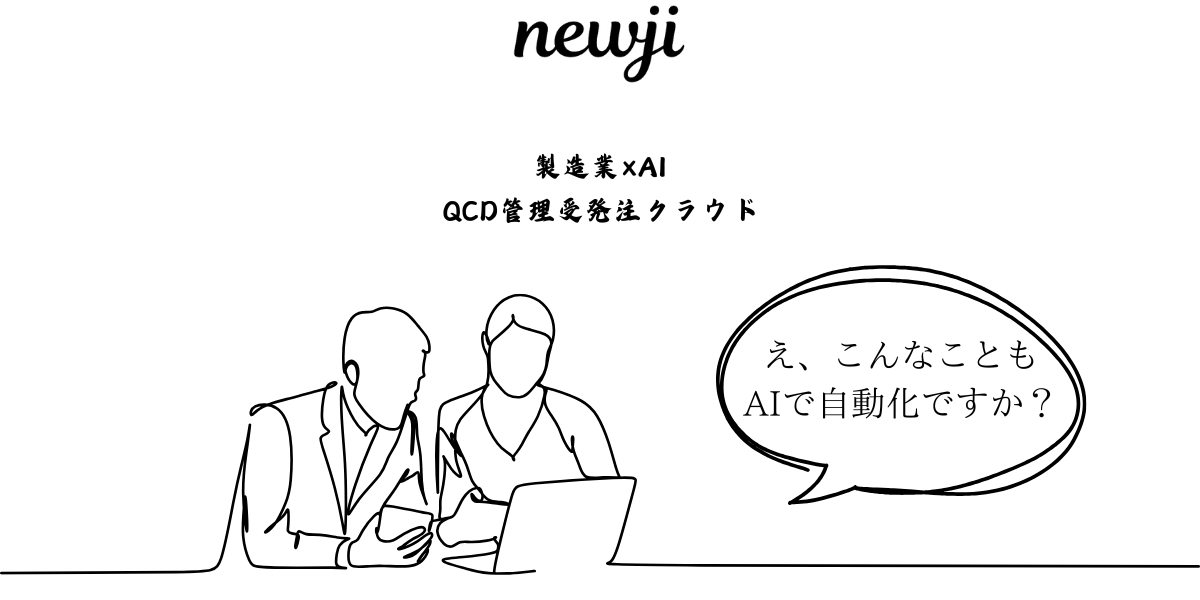
Fundamentals of Setting Up Processes to Prevent Defects and Mistake-Proofing (Poka-Yoke) and Human Error Prevention
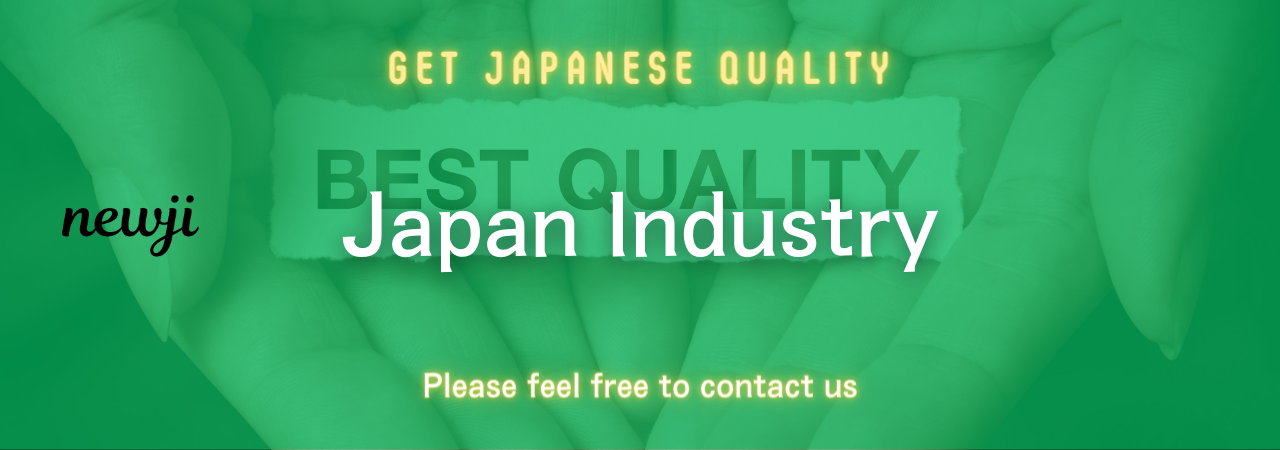
Understanding and implementing processes to prevent defects, mistake-proofing (Poka-Yoke), and avoiding human errors can significantly improve the overall quality and performance of any business operation.
The goal is to ensure that outcomes are consistent, reliable, and of high quality.
Let’s delve into the fundamentals of these concepts and explore strategies to effectively implement them in your organization.
目次
What is Defect Prevention?
Defect prevention is the strategic process of identifying and mitigating potential issues before they arise in the production or service delivery stages.
This proactive approach focuses on addressing the root causes rather than just the symptoms.
By understanding and eliminating factors that cause defects, businesses can maintain high standards and satisfy their customers consistently.
Identify Potential Defects
The first step in defect prevention is identifying potential areas where problems could occur.
This involves analyzing your processes and operations in detail.
You can use tools such as Failure Mode and Effects Analysis (FMEA) to systematically evaluate where and how processes might fail.
Root Cause Analysis
Once potential defects are identified, the next step is to perform a root cause analysis.
This helps to pinpoint the underlying reasons behind those defects.
Techniques like the “5 Whys” or Fishbone diagrams are commonly used to dig deeper and understand the root causes.
Implementing Solutions
After identifying the root causes, you need to develop and implement solutions to eliminate or mitigate these defects.
This often involves redesigning processes, enhancing training programs, or implementing new quality control measures.
What is Mistake-Proofing (Poka-Yoke)?
Mistake-proofing, also known as Poka-Yoke, is a Japanese term that translates to “avoid (yokeru) mistakes (poka).”
It is a lean manufacturing technique aimed at preventing errors by designing systems and processes that make it impossible or very difficult to make mistakes.
Benefits of Poka-Yoke
Poka-Yoke can significantly reduce the rate of errors and defects in any process.
By simplifying processes and removing the possibility of error, businesses can achieve higher levels of quality and efficiency.
It also reduces costs associated with rework and waste.
Design for Failure Prevention
Integrating Poka-Yoke into the design of your processes involves making changes that prevent errors from occurring.
For example, using jigs or fixtures in manufacturing can ensure precise placement of components.
In software, validation rules and error messages can guide users to enter correct information.
Detection and Warning Systems
Poka-Yoke also includes implementing detection and warning systems that identify errors before they create defects.
Automated alarms, sensors, and checklists can help operators to catch mistakes early and take corrective actions promptly.
Preventing Human Error
Human errors are a significant source of defects and failures in any operation.
By understanding and addressing the human factors in your processes, you can minimize these errors and improve overall performance.
Training and Education
One of the most effective ways to prevent human errors is through continuous training and education.
Ensure that all employees are well-trained and aware of the best practices and standards in your organization.
Periodic refresher courses can help keep skills and knowledge up-to-date.
Clear Procedures and Documentation
Having clear, well-documented procedures is essential to prevent human errors.
Ensure that instructions are easy to understand and accessible to everyone involved.
Standard Operating Procedures (SOPs) should be updated regularly to reflect new insights and improvements.
Standardization
Standardizing processes helps to reduce variability and the likelihood of errors.
By creating uniform procedures and guidelines, everyone follows the same steps, reducing the chances of mistakes.
Standardization can be achieved through checklists, templates, and regular audits.
Combining Strategies for Optimal Results
Implementing defect prevention, mistake-proofing (Poka-Yoke), and human error prevention strategies in isolation can yield positive results.
However, the true potential lies in combining these strategies to create a comprehensive quality management system.
Integrated Quality Management System
An integrated quality management system ensures that all aspects of your operations work together seamlessly.
This holistic approach enables you to identify and mitigate risks at every stage of your process, from design to delivery.
Regular reviews and continuous improvement efforts can help keep the system effective over time.
Continuous Improvement and Monitoring
Continuous improvement is the cornerstone of effective defect prevention and error-proofing strategies.
It involves regularly reviewing and refining your processes to ensure they remain effective and relevant.
Monitoring and Feedback
Establish a robust system for monitoring your processes and gathering feedback.
This can include regular audits, performance metrics, and customer feedback.
Analyzing this data helps you identify areas for improvement and take timely corrective actions.
Employee Involvement
Employees are often the best source of insights for process improvements.
Encourage a culture of continuous improvement by involving employees in identifying problems and suggesting solutions.
Regular brainstorming sessions and suggestion programs can help tap into their valuable perspectives.
By focusing on these fundamentals and integrating them into your operations, you can significantly reduce defects, improve quality, and enhance your overall business performance.
Remember, the journey towards zero defects and optimal performance is ongoing.
It requires dedication, continuous improvement, and a proactive approach to stay ahead in the competitive landscape.
資料ダウンロード
QCD調達購買管理クラウド「newji」は、調達購買部門で必要なQCD管理全てを備えた、現場特化型兼クラウド型の今世紀最高の購買管理システムとなります。
ユーザー登録
調達購買業務の効率化だけでなく、システムを導入することで、コスト削減や製品・資材のステータス可視化のほか、属人化していた購買情報の共有化による内部不正防止や統制にも役立ちます。
NEWJI DX
製造業に特化したデジタルトランスフォーメーション(DX)の実現を目指す請負開発型のコンサルティングサービスです。AI、iPaaS、および先端の技術を駆使して、製造プロセスの効率化、業務効率化、チームワーク強化、コスト削減、品質向上を実現します。このサービスは、製造業の課題を深く理解し、それに対する最適なデジタルソリューションを提供することで、企業が持続的な成長とイノベーションを達成できるようサポートします。
オンライン講座
製造業、主に購買・調達部門にお勤めの方々に向けた情報を配信しております。
新任の方やベテランの方、管理職を対象とした幅広いコンテンツをご用意しております。
お問い合わせ
コストダウンが利益に直結する術だと理解していても、なかなか前に進めることができない状況。そんな時は、newjiのコストダウン自動化機能で大きく利益貢献しよう!
(Β版非公開)