- お役立ち記事
- Ensuring Safety with AMRs Equipped with Collaborative Robots
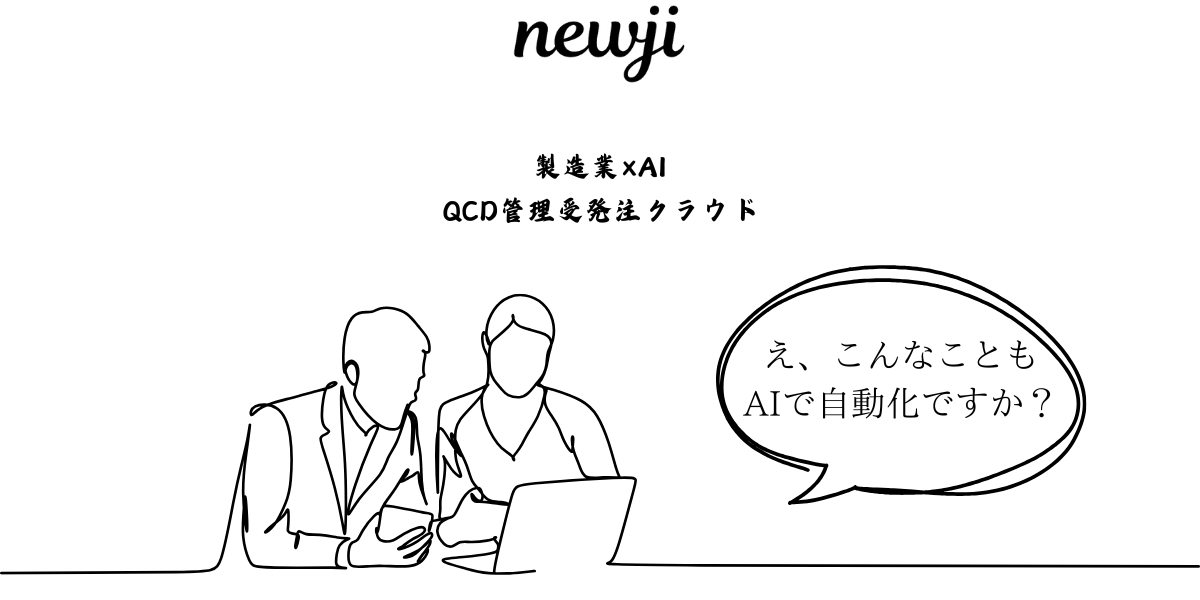
Ensuring Safety with AMRs Equipped with Collaborative Robots
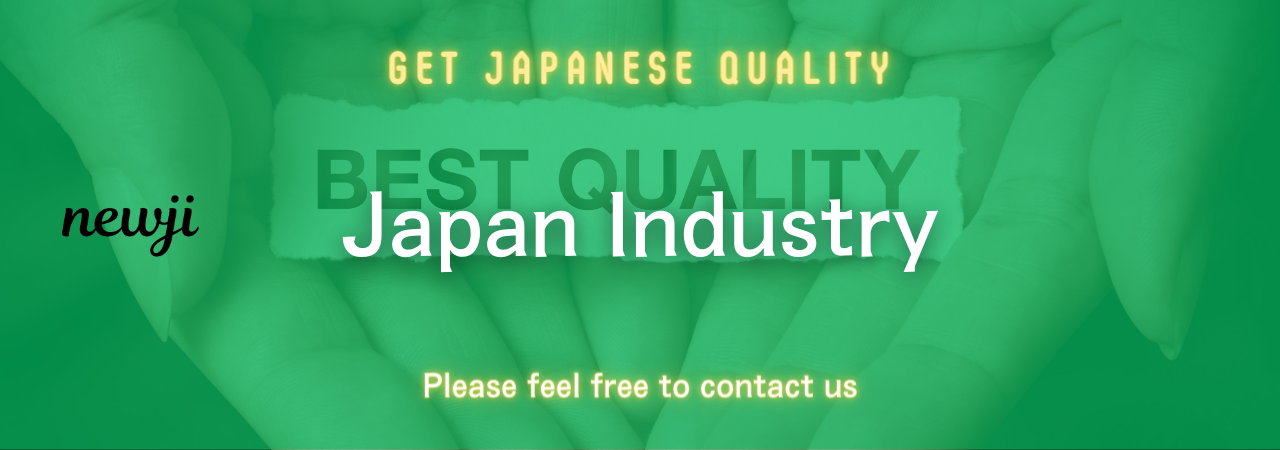
As the world of automation and robotics continues to evolve, we are witnessing the merging of two groundbreaking technologies: Autonomous Mobile Robots (AMRs) and collaborative robots (cobots).
These innovations are transforming various industries, from manufacturing to healthcare, by enhancing efficiency and productivity.
However, with these advancements comes an essential responsibility: ensuring safety.
Let’s explore how AMRs equipped with collaborative robots can be operated safely in dynamic environments.
目次
Understanding AMRs and Collaborative Robots
What are AMRs?
Autonomous Mobile Robots, or AMRs, are robots designed to navigate their environment without human intervention.
They use sensors, cameras, and complex algorithms to move around, avoiding obstacles and efficiently completing tasks.
AMRs are used in a variety of applications, including warehouse logistics, delivery services, and even healthcare.
What are Collaborative Robots?
Collaborative robots, or cobots, are designed to work alongside humans. Unlike traditional industrial robots, cobots are built with safety in mind, featuring sensors and programming that allow them to detect and respond to human presence, ensuring a safe and efficient collaborative environment. Cobots are used in many sectors, including assembly lines, laboratories, and customer service.
The Benefits of Combining AMRs with Cobots
When we integrate AMRs with cobots, the possibilities for automation become even more remarkable.
This combination allows for a high degree of flexibility, efficiency, and productivity in various tasks.
For instance, an AMR can transport materials within a warehouse, while a cobot performs tasks such as sorting, packaging, or assembly.
Increased Efficiency
Combining AMRs and cobots can significantly improve efficiency within a workspace.
AMRs handle the transport of materials, reducing idle time and allowing human workers or cobots to focus on tasks that require more precision or dexterity.
Enhanced Flexibility
This integration offers greater flexibility in operations.
AMRs can be deployed in different areas of a facility, and cobots can be programmed to perform various tasks, enabling businesses to adapt quickly to changing demands or workflows.
Ensuring Safety: Key Considerations
While the benefits of combining AMRs with cobots are clear, safety remains a paramount concern.
To ensure safe operation, several key considerations must be addressed.
Robust Sensor Technology
Both AMRs and cobots rely heavily on sensor technology to operate safely. For AMRs, this includes LiDAR, cameras, and ultrasonic sensors, which enable them to detect and avoid obstacles.
Cobots, on the other hand, use force sensors, proximity sensors, and vision systems to ensure they can operate safely alongside humans.
Regular maintenance and calibration of these sensors are crucial to ensure they function correctly.
Safety Standards and Compliance
Organizations must adhere to industry safety standards and regulations when deploying AMRs and cobots.
Standards such as ISO 3691-4 for AMRs and ISO/TS 15066 for cobots provide guidelines for safe design, operation, and maintenance.
Compliance with these standards helps mitigate risks and ensures a safer working environment.
Training and Education
Proper training for employees is essential when integrating AMRs and cobots into the workplace. Workers should be educated on how to interact safely with these robots, understand their capabilities and limitations, and know the protocols for reporting any issues. Regular training sessions and updates can help maintain a culture of safety.
Risk Assessment and Mitigation
Conducting thorough risk assessments before deploying AMRs and cobots is crucial.
This involves identifying potential hazards, evaluating the likelihood and severity of risks, and implementing measures to mitigate them.
Continuous monitoring and reassessment of risks can further enhance safety over time.
Real-World Examples
To better understand the safety considerations and benefits of integrating AMRs with cobots, let’s look at some real-world examples.
Warehouse Logistics
In a large warehouse, AMRs can transport pallets of goods from one area to another, while cobots handle tasks like sorting, packing, and labeling. By conducting comprehensive risk assessments and adhering to safety standards, companies can ensure that these robots operate safely alongside human workers, reducing manual labor and increasing efficiency.
Healthcare
In a hospital setting, an AMR can transport medical supplies, linens, and meals, while a cobot assists with dispensing medications or performing precise surgical procedures.
Strict adherence to safety protocols and regular maintenance of sensors ensure that these robots enhance efficiency without compromising patient or staff safety.
Manufacturing
In a manufacturing plant, AMRs can move raw materials to different assembly stations, while cobots assist with tasks such as welding, painting, or quality control. Ensuring that employees are trained in robot safety and that the robots are compliant with safety standards helps create a harmonious and productive environment.
The Future of AMRs and Cobots
As technology continues to advance, the integration of AMRs with cobots will become even more sophisticated.
We can expect to see improvements in sensor technology, artificial intelligence, and machine learning, further enhancing the safety and efficiency of these robots.
The future holds exciting possibilities, from fully automated smart factories to hospitals where robots handle routine tasks, allowing healthcare professionals to focus on patient care.
Conclusion
Ensuring safety with AMRs equipped with collaborative robots is a dynamic and ongoing process.
By leveraging robust sensor technology, adhering to safety standards, providing thorough training, and conducting regular risk assessments, organizations can create a safe and productive environment for both humans and robots.
As we continue to explore the potential of these technologies, prioritizing safety will remain essential to their successful implementation and operation.
資料ダウンロード
QCD調達購買管理クラウド「newji」は、調達購買部門で必要なQCD管理全てを備えた、現場特化型兼クラウド型の今世紀最高の購買管理システムとなります。
ユーザー登録
調達購買業務の効率化だけでなく、システムを導入することで、コスト削減や製品・資材のステータス可視化のほか、属人化していた購買情報の共有化による内部不正防止や統制にも役立ちます。
NEWJI DX
製造業に特化したデジタルトランスフォーメーション(DX)の実現を目指す請負開発型のコンサルティングサービスです。AI、iPaaS、および先端の技術を駆使して、製造プロセスの効率化、業務効率化、チームワーク強化、コスト削減、品質向上を実現します。このサービスは、製造業の課題を深く理解し、それに対する最適なデジタルソリューションを提供することで、企業が持続的な成長とイノベーションを達成できるようサポートします。
オンライン講座
製造業、主に購買・調達部門にお勤めの方々に向けた情報を配信しております。
新任の方やベテランの方、管理職を対象とした幅広いコンテンツをご用意しております。
お問い合わせ
コストダウンが利益に直結する術だと理解していても、なかなか前に進めることができない状況。そんな時は、newjiのコストダウン自動化機能で大きく利益貢献しよう!
(Β版非公開)