- お役立ち記事
- Optimizing Japanese Manufacturing with Cutting-Edge Electromagnetic Environment and Wave Surveys
Optimizing Japanese Manufacturing with Cutting-Edge Electromagnetic Environment and Wave Surveys
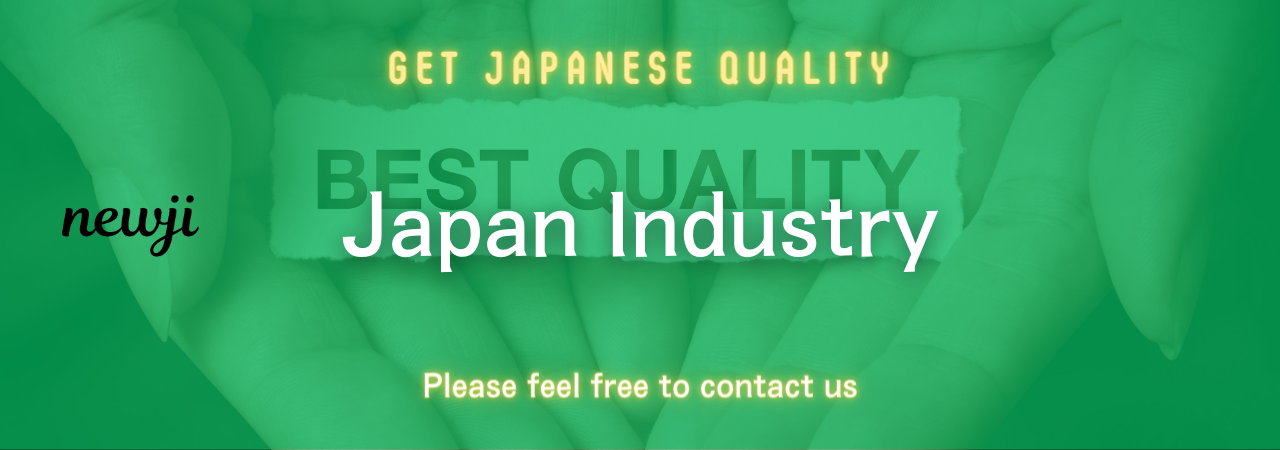
目次
Understanding the Importance of Electromagnetic Environment and Wave Surveys in Manufacturing
In the competitive landscape of global manufacturing, understanding the nuances of technological environments is paramount.
One critical, yet often overlooked, aspect is the electromagnetic environment and the associated wave surveys.
This deep dive will uncover the significance of these surveys and their impact on optimization efforts, quality control, and operational efficiency in manufacturing, especially within the context of Japanese supplier networks.
As manufacturing processes have become increasingly reliant on electronic and automated systems, interference from electromagnetic (EM) waves can lead to significant challenges.
These can range from minor disruptions to complete operational shutdowns.
Understanding and mitigating these risks is vital for maintaining the seamless flow of production and ensuring top-notch product quality.
Advantages of Conducting Electromagnetic Surveys
Enhancement of Operational Efficiency
Conducting electromagnetic environment and wave surveys can notably enhance operational efficiency within a manufacturing setup.
By identifying potential sources of EM interference, manufacturers can proactively address these issues, thereby reducing downtime and ensuring smoother workflows.
This preemptive action results in time and cost savings, contributing to overall operational excellence.
Quality Control Improvement
Precision is non-negotiable in manufacturing, particularly with Japanese suppliers known for their excellence.
Electromagnetic interference (EMI) can lead to erroneous readings and performance inconsistencies.
By conducting regular EM surveys, companies can pinpoint and rectify discrepancies early, ensuring the production maintains its high standard of quality.
Safety Assurance
Manufacturing environments are replete with sensitive equipment and personnel working in proximity.
Unregulated EM fields can pose safety hazards.
Surveys help in identifying areas with unsafe EM levels and in implementing necessary mitigations, fostering a safer working environment.
Challenges and Disadvantages
Resource Intensiveness
Implementing comprehensive EM surveys can be resource-intensive.
It demands investment in specialized equipment and skilled personnel to conduct these surveys and interpret the data accurately.
For companies operating on thin margins, this can present a significant financial burden.
Potential Operational Disruptions
Conducting thorough surveys might necessitate halting production or certain operations.
This can be difficult to manage without affecting output and delivery schedules.
Strategic planning and usage of non-peak hours for surveys can help mitigate such disruptions.
Complexity of Data Interpretation
The data derived from EM surveys is complex.
Understanding and acting upon this data requires a high level of technical expertise and often collaboration with specialized consultants.
Misinterpretation can lead to either overestimating or underestimating potential EM hazards.
Techniques for Effective Supplier Negotiation
When engaging with Japanese suppliers, leveraging knowledge about the electromagnetic environment can be a powerful negotiation tool.
Here are some proven techniques:
Emphasize Compliance
Highlight the importance of compliance with international EM standards.
Suppliers are often willing to accommodate demands that align with global best practices and regulatory requirements.
Collaborate on Solutions
Instead of presenting surveys as a policing tool, approach discussions with a sense of collaboration.
Work with suppliers to develop solutions for EM issues that benefit both parties.
Leverage Historical Data
Present historical data from previous EM surveys to underline the necessity of proactive measures.
Empirical evidence can be very persuasive during negotiations.
Market Conditions and Trends
Increasing Digitalization
The trend towards digitalization and smart manufacturing is accelerating.
This increases the potential for EMI but also highlights the importance of robust EM management systems.
Regulatory Scrutiny
Global and local regulatory bodies are increasingly focusing on electromagnetic compatibility (EMC) standards.
Compliance is no longer optional, and market leaders are consistently those who preemptively align with regulatory expectations.
Tech-Driven Supplier Ecosystem
Japanese suppliers are investing heavily in advanced manufacturing technologies.
This trend signifies a growing awareness and readiness to adopt measures that mitigate EM concerns.
Best Practices for Implementation
Regular Audits
Incorporate routine EM environment audits into your operational calendar.
Frequent assessments ensure continuous monitoring and timely mitigation of potential issues.
Invest in Training
Ensure your teams are equipped with the necessary training to effectively carry out EM surveys and interpret the results accurately.
Ongoing education programs can keep your staff updated on the latest industry standards and technological advancements.
Collaborate with Experts
Engage with experts in electromagnetic fields and EMC to leverage their knowledge.
Partnerships with consultants and researchers can provide deeper insights and innovative solutions to complex EM challenges.
Utilize Advanced Tools
Invest in cutting-edge tools and technologies for EM surveys.
Advanced instruments can provide more accurate data and insights, facilitating better decision-making.
Conclusion
Optimizing manufacturing operations through comprehensive electromagnetic environment and wave surveys can significantly enhance quality, efficiency, and safety.
Despite the challenges associated with resource allocation and data management, the advantages far outweigh the downsides.
Especially when working within the robust framework of Japanese suppliers, these practices ensure that your procurement and purchasing departments can operate at peak performance.
By adopting these methods, staying updated with market trends, and engaging in collaborative negotiations, companies can harness the full potential of Japanese manufacturing excellence.
Incorporating these insights into your procurement strategies can lead to better relationships with suppliers, more efficient production processes, and a significant boost in product quality and reliability.
In turn, this positions your company as a leader in the highly competitive manufacturing industry.
資料ダウンロード
QCD調達購買管理クラウド「newji」は、調達購買部門で必要なQCD管理全てを備えた、現場特化型兼クラウド型の今世紀最高の購買管理システムとなります。
ユーザー登録
調達購買業務の効率化だけでなく、システムを導入することで、コスト削減や製品・資材のステータス可視化のほか、属人化していた購買情報の共有化による内部不正防止や統制にも役立ちます。
NEWJI DX
製造業に特化したデジタルトランスフォーメーション(DX)の実現を目指す請負開発型のコンサルティングサービスです。AI、iPaaS、および先端の技術を駆使して、製造プロセスの効率化、業務効率化、チームワーク強化、コスト削減、品質向上を実現します。このサービスは、製造業の課題を深く理解し、それに対する最適なデジタルソリューションを提供することで、企業が持続的な成長とイノベーションを達成できるようサポートします。
オンライン講座
製造業、主に購買・調達部門にお勤めの方々に向けた情報を配信しております。
新任の方やベテランの方、管理職を対象とした幅広いコンテンツをご用意しております。
お問い合わせ
コストダウンが利益に直結する術だと理解していても、なかなか前に進めることができない状況。そんな時は、newjiのコストダウン自動化機能で大きく利益貢献しよう!
(Β版非公開)