- お役立ち記事
- Unlocking the Secrets of the Japanese Preservation System: A Game Changer for Modern Manufacturing
Unlocking the Secrets of the Japanese Preservation System: A Game Changer for Modern Manufacturing
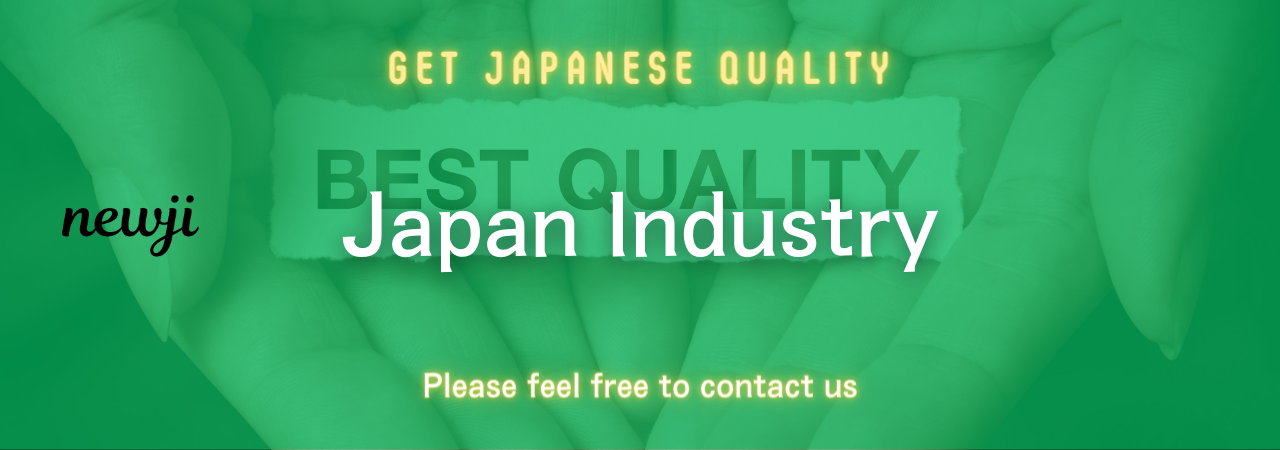
目次
Introduction
In the intricate world of modern manufacturing, the Japanese preservation system stands out as an epitome of efficiency, innovation, and meticulousness. Manufacturers worldwide continually look to Japan for inspiration, not only for cutting-edge technology but also for their disciplined approaches to procurement, quality control, and production management. This article delves into the secrets of the Japanese preservation system and explores how it can be a game changer for today’s manufacturing industry.
Understanding the Japanese Preservation System
What is the Japanese Preservation System?
The Japanese preservation system is a broad term that encompasses various methodologies and practices aimed at maintaining and enhancing the quality of production materials, finished goods, and overall manufacturing processes. Rooted in the principles of lean manufacturing, this system emphasizes minimal waste, continuous improvement (kaizen), and total quality management (TQM).
Historical Context
The Japanese preservation system traces its origins back to the post-World War II era. During this period, Japanese manufacturers like Toyota revolutionized production with the Just-In-Time (JIT) system and total quality control. These systems aimed to optimize resources, streamline workflows, and ensure the highest standards of quality.
Core Principles
Several key principles underpin the Japanese preservation system:
1. **Kaizen (Continuous Improvement):** Small, incremental changes aimed at improving efficiency and quality.
2. **5S (Sort, Set in order, Shine, Standardize, Sustain):** A workplace organization method aimed at improving efficiency and safety.
3. **Kanban:** A scheduling system for lean and JIT production.
4. **Poka-Yoke (Error Proofing):** Techniques to prevent errors by designing processes in a way that makes mistakes virtually impossible.
5. **Total Productive Maintenance (TPM):** Ensuring the longevity and efficiency of equipment.
Advantages of the Japanese Preservation System
Enhanced Quality Control
One primary benefit of the Japanese preservation system is the heightened level of quality control. By implementing stringent protocols and continuous monitoring, manufacturers can significantly minimize defects and ensure that products meet stringent standards. This commitment to quality translates into higher customer satisfaction and fewer returns or complaints.
Improved Efficiency and Reduced Waste
The principles of lean manufacturing under the Japanese preservation system are designed to eliminate waste. Whether it’s time, materials, or labor, the system seeks to optimize every aspect of the production process. This enhanced efficiency not only results in cost savings but also enables quicker turnaround times for production cycles.
Employee Empowerment and Engagement
Kaizen and other methodologies encourage employee involvement at all levels. Workers are motivated to offer suggestions for improvement, fostering a culture of continuous learning and adaptation. This empowerment leads to greater job satisfaction and often results in innovative solutions to common manufacturing challenges.
Disadvantages and Challenges
Cultural and Implementation Barriers
Implementing the Japanese preservation system can be challenging in organizations with different cultural backgrounds. The system requires a high level of commitment and discipline, which may contrast sharply with existing corporate cultures, particularly in Western countries. Overcoming these cultural barriers often requires substantial training and a shift in organizational mindset.
Initial Cost and Time Investment
The transition to a Japanese-style preservation system often involves significant upfront costs and time commitments. Extensive training, process redesign, and often the purchase of new equipment are necessary. For smaller manufacturers, this initial investment can be a significant hurdle.
Maintenance of Standards
While continuous improvement is a core tenet, maintaining high standards consistently over time can be challenging. This is especially true as businesses scale or diversify their product offerings. Ensuring that new teams or departments adhere to the established protocols requires ongoing vigilance and effort.
Best Practices and Techniques
Supplier Selection and Negotiation Techniques
One of the foundational aspects of the Japanese preservation system is the relationship with suppliers. Selecting the right suppliers who share similar values and standards is crucial. Here are some strategies:
1. **Due Diligence:** Conduct thorough research on potential suppliers, including their manufacturing capabilities, quality control systems, and track records.
2. **Long-Term Relationships:** Focus on building long-term partnerships rather than short-term transactional relationships. This fosters mutual trust and reliability.
3. **Collaborative Negotiation:** Instead of adversarial negotiation tactics, adopt a collaborative approach. Engage in open dialogues about shared goals and expectations.
Implementing Kaizen
Integrating kaizen into your organization requires consistent effort and commitment. Begin by establishing small, cross-functional teams tasked with identifying areas for improvement. Encourage employees to take ownership of the process, and regularly review and implement their suggestions.
Adopting 5S Methodology
The 5S methodology is a practical starting point for many manufacturers. Begin by sorting and organizing the workplace. Once everything is in order, develop standardized procedures to maintain these conditions. Regular audits and sustainability initiatives will ensure long-term adherence to these practices.
Utilizing Kanban for Workflow Management
Kanban can be particularly effective for managing workflow and inventory levels. Implement visual boards to track the progress of different tasks and monitor inventory levels. This ensures a consistent flow of materials and reduces bottlenecks in the production process.
Market Conditions and Trends
Growing Demand for Quality and Efficiency
As global competition intensifies, there is an increasing demand for high-quality, efficient manufacturing processes. The Japanese preservation system’s emphasis on quality and efficiency aligns well with these market trends, providing manufacturers with a competitive edge.
Technological Advancements
The rise of Industry 4.0 and other technological advancements are shaping the manufacturing landscape. By integrating technologies such as IoT, AI, and robotics, manufacturers can enhance their preservation systems and achieve even greater efficiency and precision.
Sustainability and Environmental Concerns
With growing awareness of environmental issues, manufacturers are under pressure to adopt sustainable practices. The Japanese preservation system’s focus on reducing waste aligns with these sustainability goals, enabling companies to minimize their environmental footprint.
Case Studies and Success Stories
Toyota: The Pioneer
Toyota’s success is often attributed to its implementation of the Japanese preservation system. Their use of JIT, kanban, and kaizen has allowed them to maintain high levels of efficiency and quality, making them a global leader in the automotive industry.
Mitsubishi Electric: Leveraging Kaizen
Mitsubishi Electric has successfully implemented kaizen across its manufacturing facilities. By encouraging continuous improvement and employee involvement, they have achieved significant cost savings and quality enhancements.
Sony: Integrating Technology
Sony’s integration of the Japanese preservation system with cutting-edge technology has allowed them to remain competitive in the fast-paced electronics market. Their focus on quality control and continuous improvement has been instrumental in maintaining their reputation for high-quality products.
Conclusion
The Japanese preservation system is a comprehensive approach to manufacturing that emphasizes quality, efficiency, and continuous improvement. While there are challenges to its implementation, the benefits far outweigh the drawbacks.
By adopting these proven methodologies, manufacturers can enhance their production processes, reduce waste, and remain competitive in the global market.
As the manufacturing landscape continues to evolve, the principles of the Japanese preservation system will remain a valuable asset for companies striving for excellence.
資料ダウンロード
QCD調達購買管理クラウド「newji」は、調達購買部門で必要なQCD管理全てを備えた、現場特化型兼クラウド型の今世紀最高の購買管理システムとなります。
ユーザー登録
調達購買業務の効率化だけでなく、システムを導入することで、コスト削減や製品・資材のステータス可視化のほか、属人化していた購買情報の共有化による内部不正防止や統制にも役立ちます。
NEWJI DX
製造業に特化したデジタルトランスフォーメーション(DX)の実現を目指す請負開発型のコンサルティングサービスです。AI、iPaaS、および先端の技術を駆使して、製造プロセスの効率化、業務効率化、チームワーク強化、コスト削減、品質向上を実現します。このサービスは、製造業の課題を深く理解し、それに対する最適なデジタルソリューションを提供することで、企業が持続的な成長とイノベーションを達成できるようサポートします。
オンライン講座
製造業、主に購買・調達部門にお勤めの方々に向けた情報を配信しております。
新任の方やベテランの方、管理職を対象とした幅広いコンテンツをご用意しております。
お問い合わせ
コストダウンが利益に直結する術だと理解していても、なかなか前に進めることができない状況。そんな時は、newjiのコストダウン自動化機能で大きく利益貢献しよう!
(Β版非公開)