- お役立ち記事
- The Importance of Parison Control in Blow Molding and Methods for Improvement
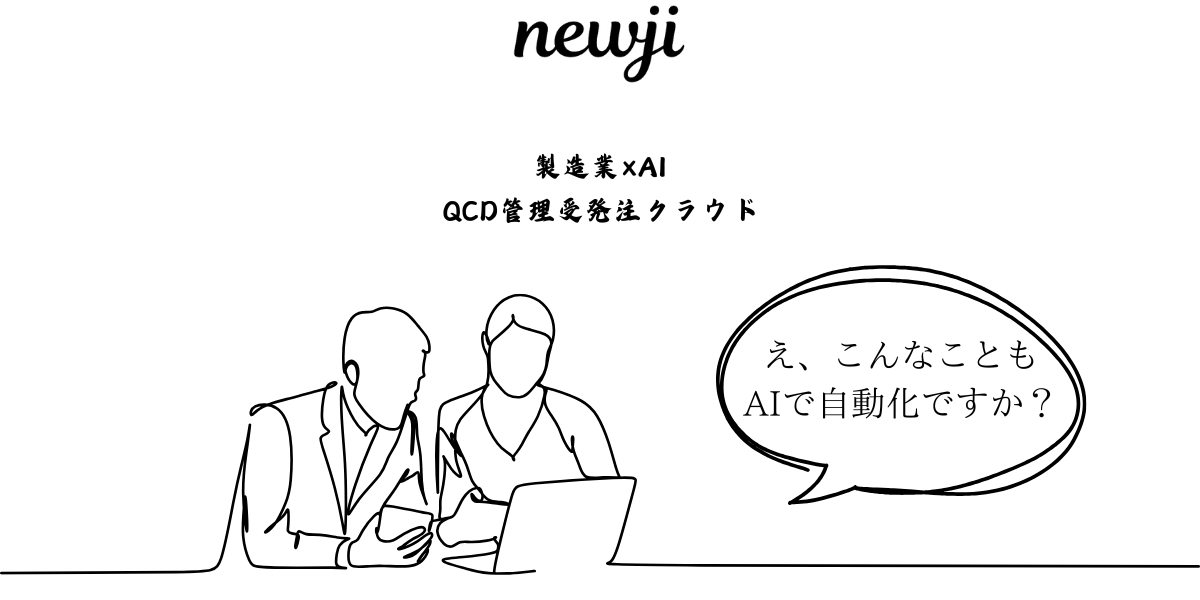
The Importance of Parison Control in Blow Molding and Methods for Improvement
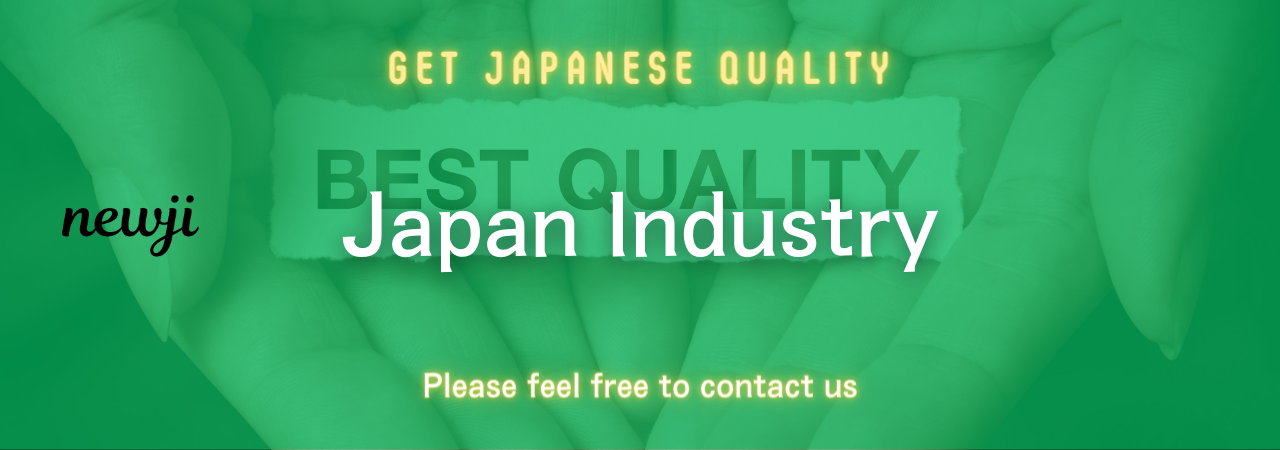
目次
Understanding Parison Control in Blow Molding
Blow molding is a manufacturing process used to create hollow plastic parts.
The term “parison” refers to the tube-like piece of plastic that is heated and then inflated into a mold to form the desired shape.
Understanding and controlling the parison is vital for producing high-quality products.
What is Parison Control?
Parison control involves adjusting the thickness and uniformity of the parison before it is inflated in the mold.
Inconsistent parisons can result in products with weak spots, uneven thickness, and other defects.
Proper parison control contributes to the strength, durability, and aesthetic quality of the finished product.
Manufacturers use a variety of techniques and technologies to achieve optimal parison control.
Why Parison Control is Essential
Consistent parison thickness ensures the final product will have uniform wall thickness, which is particularly crucial for containers holding liquids.
Variations in wall thickness can lead to weak points that may cause the container to leak or burst.
Additionally, uniform wall thickness is essential for meeting industry standards and regulations.
Product Quality
A well-controlled parison leads to higher quality products.
When the parison is uniform, the final product has consistent material distribution, resulting in fewer mechanical defects.
Quality control is significantly easier when the parison is consistent, which reduces waste and increases production efficiency.
Cost Efficiency
Proper parison control can help in reducing material costs.
By ensuring the parison is neither too thick nor too thin, manufacturers can minimize excess use of raw materials.
This not only reduces costs but also conserves resources, contributing to more sustainable production practices.
Methods to Improve Parison Control
Several methods are employed to ensure that the parison maintains consistent quality.
Some of these methods are technologically driven, while others focus on process improvements.
Continuous Monitoring
One of the most effective ways to improve parison control is through continuous monitoring.
Advanced sensors and computer systems can measure the thickness of the parison in real time.
These measurements help in making immediate adjustments to the process, ensuring that the parison remains as uniform as possible.
Continuous monitoring also enables manufacturers to identify any deviations quickly, reducing the risk of producing defective products.
Advanced Extrusion Equipment
Modern extrusion equipment is designed with features that enhance parison control.
For instance, variable speed drives and programmable logic controllers (PLCs) allow for precise adjustments in the parison thickness.
Some advanced machines even come with closed-loop systems that automatically adjust the extruder settings to maintain the desired parison characteristics.
Die Design
The design of the die used in the blow molding process significantly impacts the quality of the parison.
A well-designed die can help in achieving uniform material distribution.
Adjustments such as modifying the die’s contour or using streamlined flow channels can reduce irregularities in the parison.
Regular maintenance and cleaning of the die also play a crucial role in ensuring consistent performance.
Material Selection
The type of plastic material used can affect the ease of controlling the parison.
Some materials are more prone to inconsistencies due to their thermal properties.
Choosing high-quality, consistent raw materials can make it easier to achieve a uniform parison.
Moreover, additives and stabilizers can be used to enhance the flow characteristics of the plastic, contributing to better parison control.
Operator Training
Well-trained operators are essential for maintaining parison quality.
Training programs should focus on teaching operators how to recognize signs of inconsistencies and how to make necessary adjustments.
Skilled operators can identify issues that automated systems might miss and can make real-time decisions to correct any problems.
Regular update training ensures that operators stay proficient with the latest technologies and techniques.
Common Challenges in Parison Control
Despite the best efforts, achieving perfect parison control can be challenging.
Several common issues can arise, impacting the quality of the final product.
Temperature Fluctuations
Variations in temperature can lead to inconsistent parison thickness.
Ensuring that the plastic is heated uniformly and maintaining a stable extrusion temperature are crucial steps.
Using advanced heating systems and insulating materials can help mitigate temperature-related issues.
Inconsistent Material Feed
An uneven material feed can result in a parison with varying thickness.
Using automated feeding systems can help ensure a consistent material flow.
Regularly monitoring the feed and making adjustments as needed can also reduce this issue.
Mechanical Wear and Tear
Over time, the machinery used in extrusion and blow molding can experience wear and tear, affecting its performance.
Regular maintenance and timely replacement of worn parts are essential.
Preventative maintenance schedules can help in identifying potential problems before they impact production.
Conclusion
Parison control is a critical aspect of the blow molding process.
Proper control mechanisms ensure the production of high-quality, consistent products while reducing material costs and improving overall efficiency.
By employing a combination of advanced technologies, skilled operators, and effective process management, manufacturers can achieve optimal parison control.
Addressing common challenges and continuously improving the process will lead to better products and more efficient production methods.
資料ダウンロード
QCD調達購買管理クラウド「newji」は、調達購買部門で必要なQCD管理全てを備えた、現場特化型兼クラウド型の今世紀最高の購買管理システムとなります。
ユーザー登録
調達購買業務の効率化だけでなく、システムを導入することで、コスト削減や製品・資材のステータス可視化のほか、属人化していた購買情報の共有化による内部不正防止や統制にも役立ちます。
NEWJI DX
製造業に特化したデジタルトランスフォーメーション(DX)の実現を目指す請負開発型のコンサルティングサービスです。AI、iPaaS、および先端の技術を駆使して、製造プロセスの効率化、業務効率化、チームワーク強化、コスト削減、品質向上を実現します。このサービスは、製造業の課題を深く理解し、それに対する最適なデジタルソリューションを提供することで、企業が持続的な成長とイノベーションを達成できるようサポートします。
オンライン講座
製造業、主に購買・調達部門にお勤めの方々に向けた情報を配信しております。
新任の方やベテランの方、管理職を対象とした幅広いコンテンツをご用意しております。
お問い合わせ
コストダウンが利益に直結する術だと理解していても、なかなか前に進めることができない状況。そんな時は、newjiのコストダウン自動化機能で大きく利益貢献しよう!
(Β版非公開)