- お役立ち記事
- Challenges and Solutions for Quality Control in Global Procurement for Manufacturing
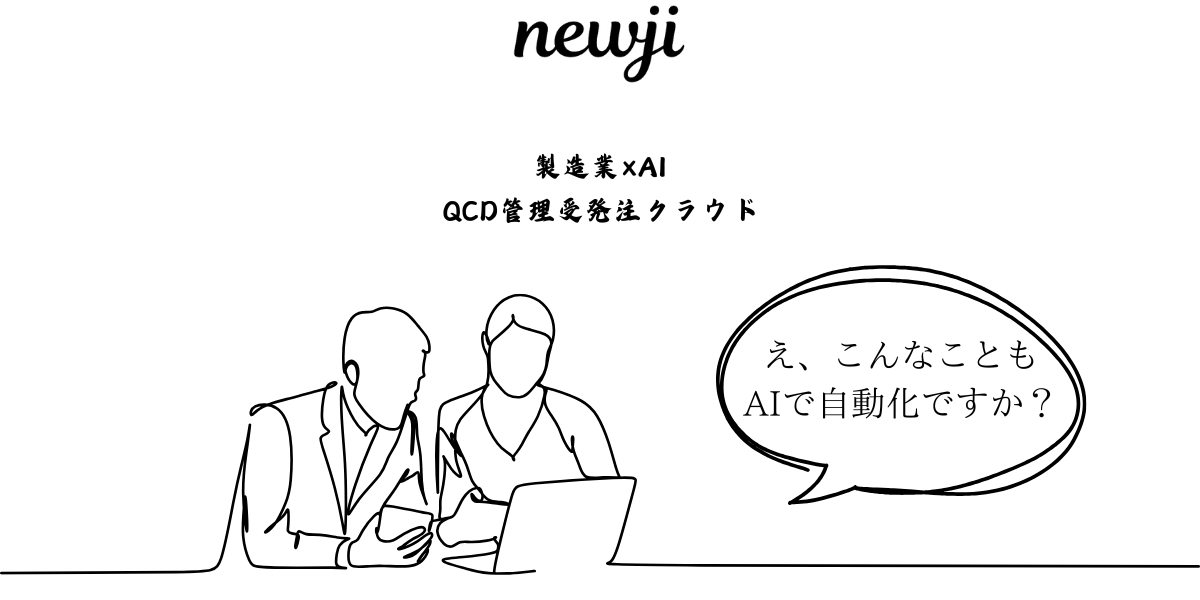
Challenges and Solutions for Quality Control in Global Procurement for Manufacturing
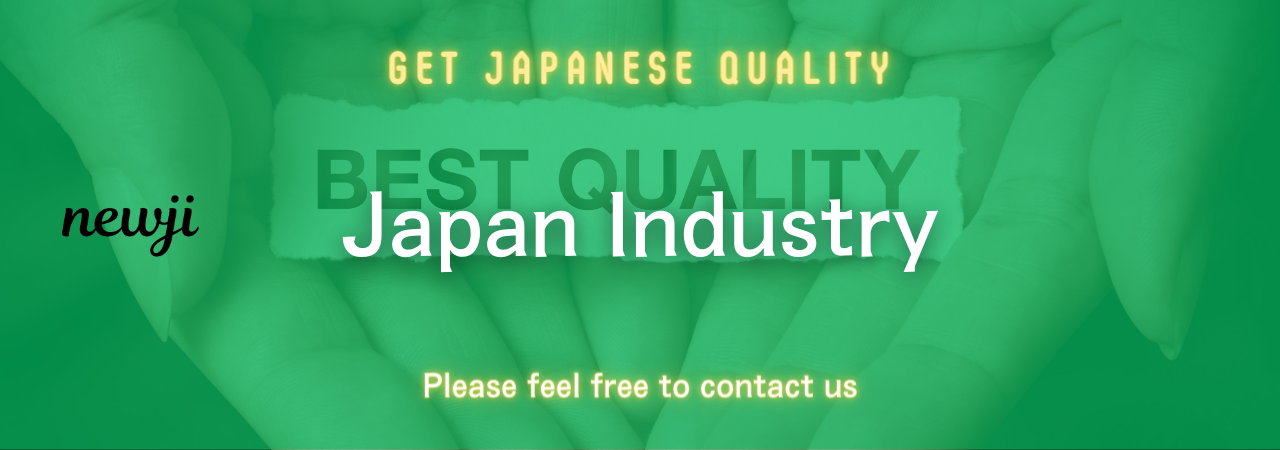
In today’s globalized world, manufacturing companies often source their materials and components from different countries.
While this can lead to cost savings and access to a wider range of resources, it also comes with unique challenges.
One of the most significant challenges is ensuring quality control in global procurement.
目次
Understanding the Challenges
Varying Standards
One of the biggest issues in global procurement is dealing with varying quality standards.
Different countries and regions may have their own set of standards and regulations, which can sometimes be inconsistent with each other.
For example, a part that meets the quality standards in one country may not meet the stricter standards in another.
These discrepancies can lead to issues in the manufacturing process and affect the final product’s quality.
Communication Barriers
Communication is crucial in maintaining quality control, but it can be severely hampered by language and cultural barriers.
Misunderstandings and misinterpretations of requirements and specifications can lead to errors.
Moreover, time zone differences can delay communication, making it harder to address issues promptly.
Logistical Issues
Logistics play a critical role in procurement.
Delays in shipping, customs clearance, and other logistical hurdles can impede the timely delivery of materials and components.
These delays can disrupt the production schedule and compromise the quality of the final product.
Additionally, long shipping times can affect the quality of perishable or sensitive materials.
Supplier Reliability
Another challenge is ensuring the reliability of suppliers.
Not all suppliers maintain consistent quality standards.
Some may cut corners to reduce costs or fail to meet deadlines.
Establishing trust and reliability with new suppliers can be challenging, especially when they are located in different parts of the world.
Effective Solutions
Setting Clear Standards
One of the first steps in addressing quality control issues is to set clear, consistent quality standards.
These should be well-documented and communicated to all suppliers.
Having a universal standard that all suppliers must adhere to can help minimize inconsistencies and ensure that all materials and components meet the required quality levels.
Regular Communication
Maintaining regular communication with suppliers is essential.
Regular updates and check-ins can help catch potential issues before they become major problems.
Using technology like video conferencing, instant messaging, and collaborative platforms can facilitate better communication despite language and time zone barriers.
Thorough Supplier Evaluation
Before engaging with new suppliers, conducting a thorough evaluation is crucial.
This can include quality audits, site visits, and reviewing their past performance and reputation.
An established evaluation process helps ensure that the chosen suppliers are reliable and capable of meeting your quality standards.
Implementation of Quality Control Systems
Implementing robust quality control systems within both your organization and your supplier’s operations is vital.
This could include regular quality checks, standardized testing procedures, and comprehensive quality management systems.
Automation and AI-driven quality control tools can also help monitor and maintain standards more efficiently.
Training and Development
Investing in training and development for both your team and your suppliers can significantly improve quality control.
Training programs on quality standards, best practices, and new technologies can help ensure everyone involved is competent and aligned in their objectives.
This creates a culture focused on quality and continuous improvement.
Developing Strong Relationships
Building strong, long-term relationships with suppliers can lead to better quality control.
When suppliers feel valued and part of your business ecosystem, they are more likely to invest in maintaining high standards.
Regular meetings, fair contract terms, and mutual trust can foster strong partnerships that benefit both parties.
Leveraging Technology
Technology plays a significant role in modern quality control.
Advanced software solutions can track and analyze every aspect of the supply chain, providing real-time data and insights.
Blockchain technology, for instance, can provide transparency and traceability, making it easier to track the origin and quality of materials.
Additionally, IoT devices can monitor the condition of goods during transit, ensuring they remain within the required quality parameters.
Case Studies and Real-World Examples
Case Study: Automaker Success Through Supplier Collaboration
One leading automaker faced challenges in maintaining quality due to its diverse global suppliers.
By implementing a comprehensive supplier evaluation process and establishing clear communication channels, they built stronger relationships with their suppliers.
Regular audits and site visits ensured adherence to their stringent quality standards, leading to improved product quality and customer satisfaction.
Example: Tech Giant Using Blockchain for Transparency
A major tech company faced issues with counterfeit components infiltrating their supply chain.
They adopted blockchain technology to track every component from the point of origin to the final product.
This transparent and immutable record helped ensure the authenticity and quality of all components used in their manufacturing process.
Conclusion
Quality control in global procurement is a complex but manageable challenge.
By setting clear standards, maintaining regular communication, thoroughly evaluating suppliers, implementing quality control systems, investing in training, and leveraging technology, companies can overcome these challenges.
Building strong relationships with suppliers will also play a critical role in ensuring consistent quality.
Ultimately, a structured and proactive approach to quality control can lead to better products, improved customer satisfaction, and a stronger competitive edge in the global marketplace.
資料ダウンロード
QCD調達購買管理クラウド「newji」は、調達購買部門で必要なQCD管理全てを備えた、現場特化型兼クラウド型の今世紀最高の購買管理システムとなります。
ユーザー登録
調達購買業務の効率化だけでなく、システムを導入することで、コスト削減や製品・資材のステータス可視化のほか、属人化していた購買情報の共有化による内部不正防止や統制にも役立ちます。
NEWJI DX
製造業に特化したデジタルトランスフォーメーション(DX)の実現を目指す請負開発型のコンサルティングサービスです。AI、iPaaS、および先端の技術を駆使して、製造プロセスの効率化、業務効率化、チームワーク強化、コスト削減、品質向上を実現します。このサービスは、製造業の課題を深く理解し、それに対する最適なデジタルソリューションを提供することで、企業が持続的な成長とイノベーションを達成できるようサポートします。
オンライン講座
製造業、主に購買・調達部門にお勤めの方々に向けた情報を配信しております。
新任の方やベテランの方、管理職を対象とした幅広いコンテンツをご用意しております。
お問い合わせ
コストダウンが利益に直結する術だと理解していても、なかなか前に進めることができない状況。そんな時は、newjiのコストダウン自動化機能で大きく利益貢献しよう!
(Β版非公開)