- お役立ち記事
- The Role and Strategy of Quality Assurance in Achieving Zero Defects in Manufacturing
The Role and Strategy of Quality Assurance in Achieving Zero Defects in Manufacturing
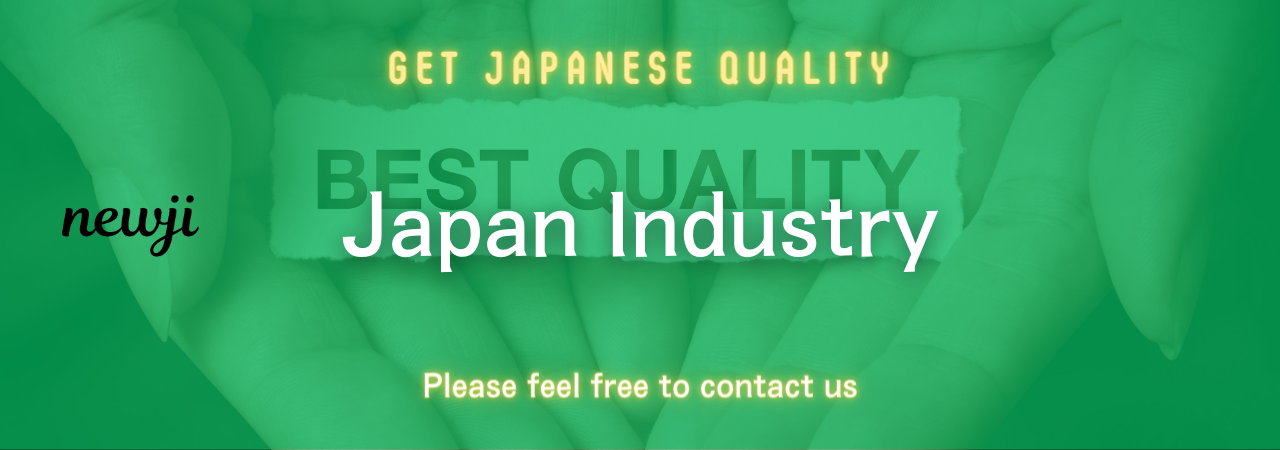
In the manufacturing industry, producing error-free products is crucial for ensuring customer satisfaction and maintaining a company’s reputation.
Quality assurance (QA) plays a pivotal role in achieving this goal.
By implementing effective QA strategies, manufacturers can aim for zero defects in their production processes.
目次
Understanding Quality Assurance
Quality assurance refers to the systematic processes and measures taken to ensure products meet specified standards and requirements.
Unlike quality control, which focuses on identifying defects in finished products, QA aims to prevent defects throughout the production process.
This proactive approach helps in detecting potential issues early on, saving time and resources.
The Importance of Quality Assurance in Manufacturing
In manufacturing, even minor defects can lead to significant consequences.
Faulty products can result in recalls, customer complaints, and financial losses.
Moreover, a compromised product quality can damage a brand’s reputation, leading to loss of customer trust.
Therefore, implementing robust QA strategies is vital for maintaining high product standards and achieving customer satisfaction.
Strategies for Effective Quality Assurance
To achieve zero defects in manufacturing, companies need to adopt a comprehensive QA strategy.
Here are some proven approaches:
1. Define Clear Quality Standards
First and foremost, it is essential to establish clear quality standards for all products.
These standards should be documented and communicated to all employees involved in the production process.
Having well-defined criteria ensures that everyone is aware of the quality expectations and works towards achieving them.
2. Implement Total Quality Management (TQM)
Total Quality Management (TQM) is a holistic approach to QA that involves all employees in the quest for quality improvement.
TQM emphasizes continuous improvement, customer focus, and employee involvement.
By fostering a culture of quality, companies can ensure that QA becomes an integral part of everyday operations.
3. Utilize Statistical Process Control (SPC)
Statistical Process Control (SPC) is a method of monitoring and controlling production processes using statistical techniques.
By analyzing data from the manufacturing process, companies can identify variations and trends that may indicate potential defects.
SPC helps in making data-driven decisions, enabling timely interventions to prevent defects.
4. Conduct Regular Audits and Inspections
Regular audits and inspections are crucial for maintaining quality standards.
These evaluations help in identifying any deviations from the set standards and implementing corrective actions promptly.
Audits and inspections should be conducted at different stages of the production process to ensure comprehensive coverage.
5. Train and Educate Employees
Employee training is a fundamental aspect of QA.
Providing adequate training and education to employees ensures that they possess the necessary skills and knowledge to perform their tasks effectively.
Well-trained employees are more likely to identify and rectify potential issues before they escalate into defects.
6. Foster a Culture of Continuous Improvement
Continuous improvement is the cornerstone of effective QA.
Encouraging employees to participate in improvement initiatives and providing them with the tools and resources to do so is vital.
Companies can use techniques like Kaizen, Six Sigma, and Lean Manufacturing to drive ongoing improvements in quality and efficiency.
Leveraging Technology for Quality Assurance
In today’s digital age, technology plays a significant role in enhancing QA processes.
Advanced technologies like Artificial Intelligence (AI), Machine Learning (ML), and the Internet of Things (IoT) offer new opportunities for improving quality assurance.
AI and Machine Learning for Predictive Quality
AI and ML can analyze vast amounts of data generated during the manufacturing process to identify patterns and predict potential defects.
These technologies can detect anomalies that may not be visible to the human eye, allowing for early interventions.
By leveraging AI and ML, companies can achieve predictive quality, reducing the chances of defects.
IoT for Real-Time Monitoring
The Internet of Things enables real-time monitoring of production processes.
IoT devices can collect data from various stages of manufacturing, providing insights into machine performance, environmental conditions, and product quality.
This real-time data allows for immediate adjustments, ensuring that any deviations are corrected promptly.
Automation for Consistency
Automation plays a crucial role in achieving consistency and precision in manufacturing.
Automated systems can perform repetitive tasks with high accuracy, reducing the likelihood of human errors.
Additionally, automation ensures that products are manufactured to exact specifications, meeting the defined quality standards.
Case Studies: Successful Implementation of QA Strategies
Several companies have successfully implemented QA strategies to achieve zero defects in manufacturing.
These case studies highlight the practical application of QA principles and the resulting benefits.
Toyota: Pioneering Quality Through Kaizen
Toyota, a global leader in the automotive industry, is renowned for its commitment to quality.
The company adopts the Kaizen philosophy, which emphasizes continuous improvement in all aspects of operations.
By involving all employees in quality initiatives and implementing rigorous quality control measures, Toyota consistently delivers high-quality vehicles with minimal defects.
General Electric: Embracing Six Sigma
General Electric (GE) is another example of a company that has successfully leveraged QA strategies.
GE implemented Six Sigma, a data-driven methodology focused on reducing defects and variability in processes.
Through Six Sigma projects, GE achieved significant improvements in product quality and operational efficiency.
Conclusion
Quality assurance is indispensable in the pursuit of zero defects in manufacturing.
By defining clear quality standards, implementing comprehensive QA strategies, and leveraging advanced technologies, companies can achieve excellence in their production processes.
The commitment to continuous improvement and employee involvement further strengthens QA efforts.
Ultimately, a robust QA framework ensures that manufacturers deliver products that meet or exceed customer expectations, safeguarding their brand reputation and achieving long-term success.
資料ダウンロード
QCD調達購買管理クラウド「newji」は、調達購買部門で必要なQCD管理全てを備えた、現場特化型兼クラウド型の今世紀最高の購買管理システムとなります。
ユーザー登録
調達購買業務の効率化だけでなく、システムを導入することで、コスト削減や製品・資材のステータス可視化のほか、属人化していた購買情報の共有化による内部不正防止や統制にも役立ちます。
NEWJI DX
製造業に特化したデジタルトランスフォーメーション(DX)の実現を目指す請負開発型のコンサルティングサービスです。AI、iPaaS、および先端の技術を駆使して、製造プロセスの効率化、業務効率化、チームワーク強化、コスト削減、品質向上を実現します。このサービスは、製造業の課題を深く理解し、それに対する最適なデジタルソリューションを提供することで、企業が持続的な成長とイノベーションを達成できるようサポートします。
オンライン講座
製造業、主に購買・調達部門にお勤めの方々に向けた情報を配信しております。
新任の方やベテランの方、管理職を対象とした幅広いコンテンツをご用意しております。
お問い合わせ
コストダウンが利益に直結する術だと理解していても、なかなか前に進めることができない状況。そんな時は、newjiのコストダウン自動化機能で大きく利益貢献しよう!
(Β版非公開)