- お役立ち記事
- Basics of Improving Welded Joint Quality
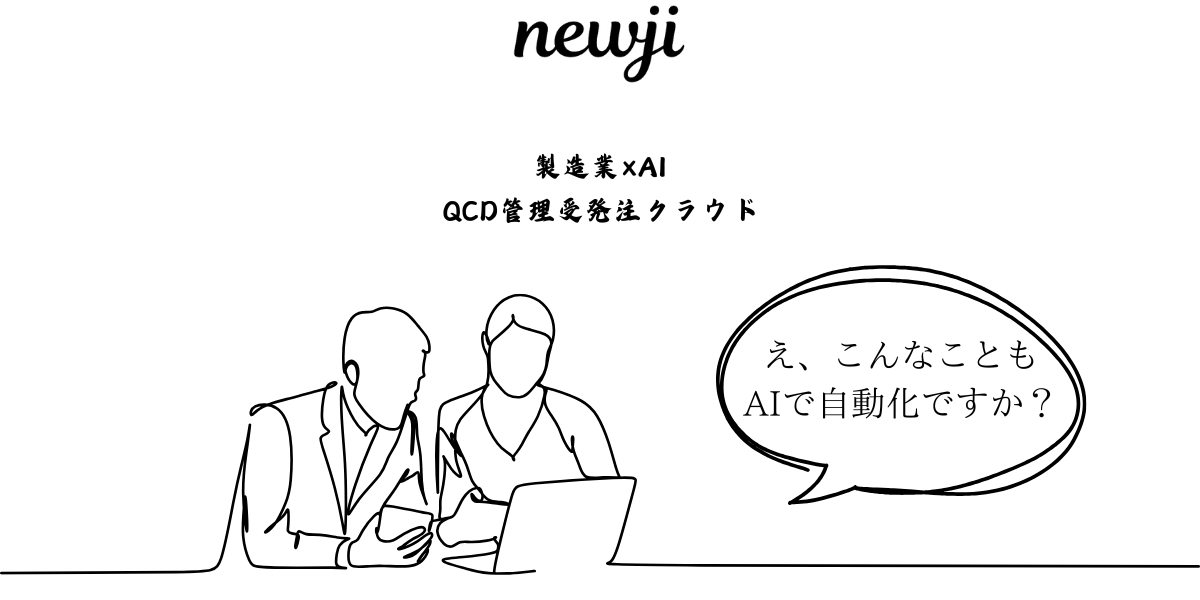
Basics of Improving Welded Joint Quality
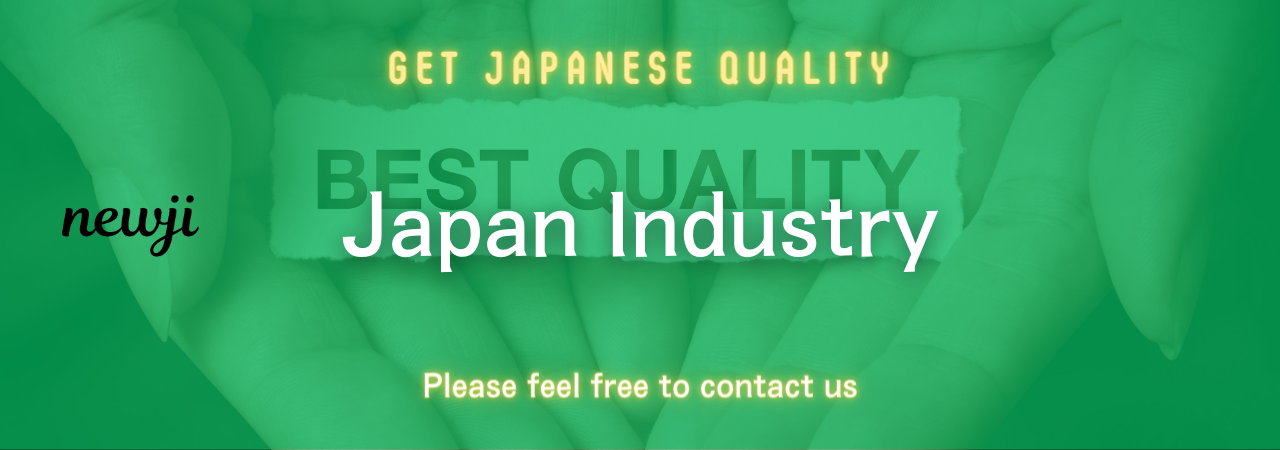
Welding is a critical process in many industries, forming the backbone of metal fabrication in construction, manufacturing, and even automotive sectors.
To ensure that welded joints are strong, reliable, and long-lasting, it is essential to focus on improving the quality of these joints.
Let’s dive into some of the fundamental aspects of enhancing welded joint quality.
目次
Understanding the Welding Process
Before delving into quality improvement techniques, it’s crucial to understand the basics of the welding process.
Welding joins two pieces of metal by melting their edges and adding a filler material to create a strong bond.
This process requires heat, pressure, or both, and can be carried out through various methods including MIG (Metal Inert Gas), TIG (Tungsten Inert Gas), and Stick welding.
Each technique has its unique advantages and applications.
Factors Affecting Weld Quality
Several factors influence the quality of a welded joint.
These include the choice of materials, the welding method, the skill of the welder, and the conditions under which the welding takes place.
Addressing these factors can significantly enhance the overall quality of the weld.
Material Selection
Choosing the right materials is the first step in ensuring a high-quality weld.
The base metals should possess compatible physical and chemical properties to form a strong bond.
Selecting metals with similar melting points and thermal expansion coefficients is crucial to avoid potential issues like cracking or distortion.
Proper Welding Technique
Selecting the appropriate welding technique for the job is equally important.
For example, MIG welding is ideal for welding thin sheets of metal quickly and efficiently, while TIG welding provides high precision for intricate tasks.
Stick welding, on the other hand, is versatile and suitable for outdoor work.
Skilled Welders
The skill level of the welder plays a significant role in determining the quality of the weld.
A well-trained and experienced welder can handle complex welds and adapt to varying conditions, ensuring that the weld is strong and free from defects.
Environmental Conditions
Environmental conditions can also impact weld quality.
Factors such as temperature, humidity, and wind can affect the welding process.
To mitigate these issues, it’s important to work in controlled environments or use protective equipment like welding tents and screens.
Preparing for Welding
Proper preparation is key to achieving a high-quality weld.
This stage involves several critical steps that lay the groundwork for a successful welding process.
Cleaning the Metals
Cleanliness is paramount when it comes to welding.
Any contamination, such as dirt, grease, or rust, can lead to weak welds and potential failure.
Use a wire brush, grinder, or chemical cleaners to ensure that the surfaces are free from impurities before starting the welding process.
Joint Design
Designing the joint correctly is another essential aspect.
Different joints, such as butt, lap, or T-joints, have specific applications and require different welding techniques.
Proper joint design ensures that the weld will be strong and durable, with good load-bearing capacity.
Aligning the Pieces
Proper alignment of the pieces to be welded is crucial.
Misaligned joints can lead to poor weld quality and potential structural issues.
Use clamps, jigs, or fixtures to hold the pieces securely in place during the welding process.
Executing the Weld
Once everything is prepared, executing the weld becomes the focus.
Attention to detail and adherence to best practices during this phase can make a significant difference in the final quality of the welded joint.
Controlling Heat Input
Controlling the heat input is vital to achieving a strong weld.
Excessive heat can cause warping, while insufficient heat can result in weak bonds.
Use the appropriate settings on your welding equipment to ensure that the heat is evenly distributed and maintained at optimal levels.
Tack Welding
Tack welding involves placing small welds at intervals to hold the pieces in place before completing the final weld.
This technique prevents the pieces from shifting during welding and helps maintain proper alignment.
Ensure that the tacks are strong enough to hold the pieces but small enough to avoid interference with the final weld.
Welding Speed and Technique
The speed and technique used during welding also affect the quality of the weld.
Moving too quickly can cause incomplete fusion, while moving too slowly can lead to overheating.
Maintain a steady pace and use consistent welding techniques to ensure a uniform and strong weld.
Post-Weld Considerations
After completing the weld, several post-weld considerations can further enhance the quality and longevity of the joint.
Inspection and Testing
Inspect the welded joint for any visible defects such as cracks, porosity, or incomplete fusion.
Non-destructive testing methods like ultrasonic testing or X-rays can help identify hidden flaws.
Addressing these issues promptly ensures that the weld meets safety and quality standards.
Cleaning and Finishing
Clean the welded area to remove any slag, spatter, or flux residues.
A smooth and clean finish not only improves the appearance but also helps prevent corrosion.
Use grinders, brushes, or chemical solutions to achieve the desired finish.
Stress Relief
Welding induces residual stresses in the metal, which can lead to issues like warping or cracking.
Stress-relief techniques such as post-weld heat treatment (PWHT) help alleviate these stresses, ensuring that the weld remains robust and stable over time.
Continuous Improvement
Improving weld quality is an ongoing process.
Continually evaluate and refine your techniques, stay updated with the latest advancements in welding technology, and invest in continuous training for welders.
By fostering a culture of continuous improvement, you can consistently achieve high-quality welded joints.
In conclusion, the quality of welded joints is influenced by various factors, from material selection and welding technique to environmental conditions and post-weld treatments.
By understanding these factors and implementing best practices, you can significantly enhance the strength, durability, and overall quality of your welded joints.
Emphasize preparation, precision, and continuous learning to achieve the best possible results in your welding projects.
資料ダウンロード
QCD調達購買管理クラウド「newji」は、調達購買部門で必要なQCD管理全てを備えた、現場特化型兼クラウド型の今世紀最高の購買管理システムとなります。
ユーザー登録
調達購買業務の効率化だけでなく、システムを導入することで、コスト削減や製品・資材のステータス可視化のほか、属人化していた購買情報の共有化による内部不正防止や統制にも役立ちます。
NEWJI DX
製造業に特化したデジタルトランスフォーメーション(DX)の実現を目指す請負開発型のコンサルティングサービスです。AI、iPaaS、および先端の技術を駆使して、製造プロセスの効率化、業務効率化、チームワーク強化、コスト削減、品質向上を実現します。このサービスは、製造業の課題を深く理解し、それに対する最適なデジタルソリューションを提供することで、企業が持続的な成長とイノベーションを達成できるようサポートします。
オンライン講座
製造業、主に購買・調達部門にお勤めの方々に向けた情報を配信しております。
新任の方やベテランの方、管理職を対象とした幅広いコンテンツをご用意しております。
お問い合わせ
コストダウンが利益に直結する術だと理解していても、なかなか前に進めることができない状況。そんな時は、newjiのコストダウン自動化機能で大きく利益貢献しよう!
(Β版非公開)