- お役立ち記事
- Case Studies and Benefits of Using the Seven QC Tools in Manufacturing Quality Control
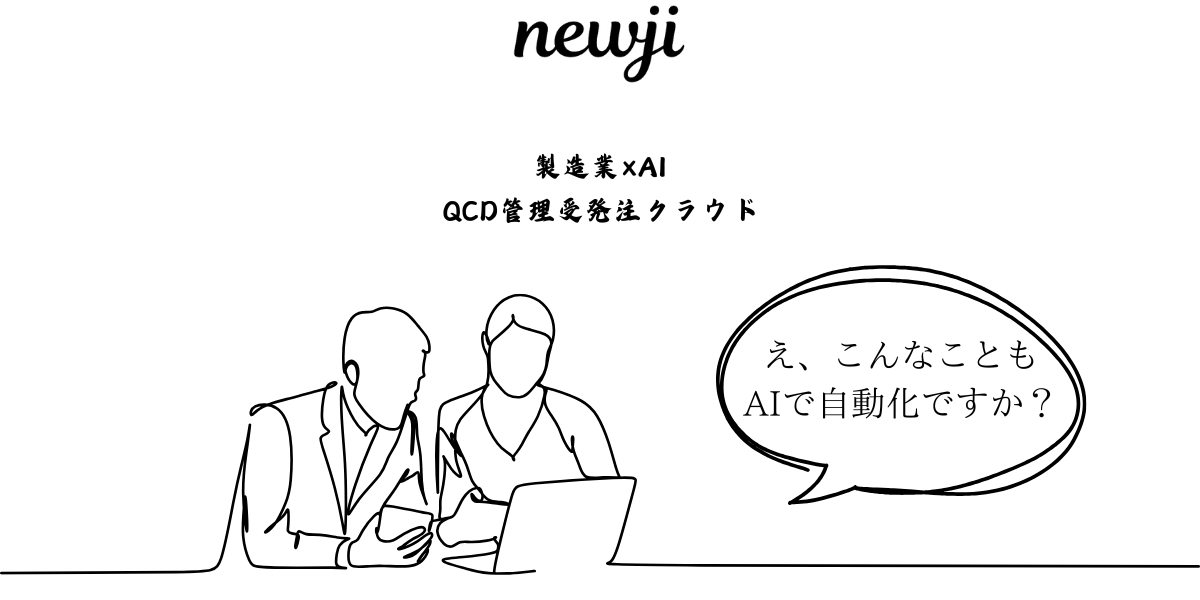
Case Studies and Benefits of Using the Seven QC Tools in Manufacturing Quality Control
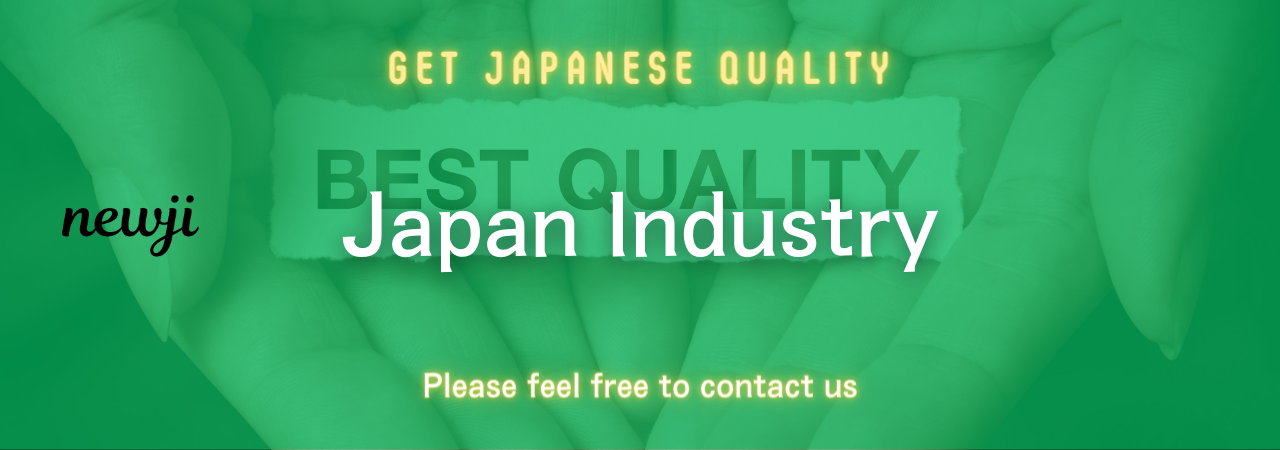
In the competitive world of manufacturing, ensuring high-quality products is essential.
One powerful way to achieve this is through the use of the Seven Quality Control (QC) Tools.
These tools are designed to help identify and solve problems, ensuring that the production process runs smoothly and efficiently.
In this article, we will explore various case studies and the benefits of using these QC tools in manufacturing quality control.
目次
What Are the Seven QC Tools?
The Seven QC Tools are simple but effective techniques used in quality management and process improvement.
They include:
1. **Cause-and-Effect Diagram (Ishikawa or Fishbone Diagram)**
2. **Check Sheet**
3. **Control Chart**
4. **Histogram**
5. **Pareto Chart**
6. **Scatter Diagram**
7. **Flowchart**
Each of these tools serves a unique purpose and, when used together, can give a comprehensive picture of a manufacturing process.
Case Studies of the Seven QC Tools in Action
Case Study 1: Reducing Defects in a Car Manufacturing Plant
A car manufacturing plant was facing issues with a high number of defects in its production line.
By implementing the Seven QC Tools, they managed to reduce these defects significantly.
**Step 1: Identifying the Problem**
They first used a **Check Sheet** to collect data on when and where defects were occurring.
This simple tool helped to record the frequency of production line defects over time.
**Step 2: Analyzing the Cause**
Next, they used a **Cause-and-Effect Diagram** to identify potential causes of these defects.
The team brainstormed various factors, such as materials, machinery, methods, and manpower, that could be contributing to the defects.
**Step 3: Monitoring and Controlling**
A **Control Chart** was then used to monitor the production process and identify any variations from the standard.
This chart helped in identifying trends and deviations that were not immediately obvious.
**Step 4: Prioritizing Issues**
A **Pareto Chart** was employed to prioritize the most critical issues.
This chart showed that a majority of defects were caused by a small number of factors, allowing the team to focus their efforts on these key areas.
**Step 5: Inspecting Data Distributions**
They also used a **Histogram** to view the distribution of the defects.
This helped in understanding the spread and central tendency of the defects, providing insight into the overall quality of the production process.
**Step 6: Investigating Relationships**
To dig deeper into the potential relationships between different variables, a **Scatter Diagram** was created.
This illustrated the correlation between machine age and the frequency of defects, leading to insights on machine maintenance practices.
**Step 7: Documenting the Process**
Finally, they used a **Flowchart** to map out the entire production process, from raw materials to finished product.
This visual representation helped in identifying bottlenecks and areas for further improvement.
Case Study 2: Improving Efficiency in an Electronics Manufacturing Company
An electronics manufacturing company was struggling with inefficiencies in its assembly line.
By applying the Seven QC Tools, they were able to optimize their processes and increase productivity.
**Step 1: Data Collection**
A **Check Sheet** was used to gather data on production times and identify where delays were occurring.
This simple form helped in quickly identifying the most time-consuming steps in the assembly line.
**Step 2: Root Cause Analysis**
A **Cause-and-Effect Diagram** was employed to brainstorm potential causes for these delays.
Factors such as staff skills, equipment performance, and material quality were all considered.
**Step 3: Monitoring Process Stability**
Using a **Control Chart**, the company monitored the consistency of production times.
This helped in identifying when and where variability and inefficiencies were happening.
**Step 4: Identifying Key Issues**
A **Pareto Chart** showed that a large portion of delays was due to a few specific steps in the assembly process.
By focusing on these steps, the team was able to make targeted improvements.
**Step 5: Understanding Process Variation**
A **Histogram** provided a visual representation of the variation in production times.
This helped in understanding the distribution and frequency of delays.
**Step 6: Exploring Variable Relationships**
A **Scatter Diagram** was used to examine the relationship between worker training hours and assembly time.
The diagram showed a clear correlation, leading to an increased focus on staff training.
**Step 7: Mapping the Process**
A detailed **Flowchart** was created to outline the assembly process, highlighting areas of redundancy and inefficiency.
This visual tool enabled the team to streamline the process and eliminate unnecessary steps.
Benefits of Using the Seven QC Tools
Identifying and Solving Problems Efficiently
One of the primary benefits of using the seven QC tools is the ability to identify and solve problems quickly and efficiently.
By using tools such as the Cause-and-Effect Diagram and Control Chart, issues can be pinpointed and addressed before they escalate.
Improving Product Quality
By systematically applying these tools, manufacturers can improve the quality of their products.
Histograms and Pareto Charts, for example, help in understanding the most common issues and focusing on quality improvement efforts.
Increasing Productivity
The Seven QC Tools can also help in optimizing manufacturing processes, leading to increased productivity.
Flowcharts and Check Sheets, in particular, assist in identifying bottlenecks and areas for improvement, enabling smoother and faster production lines.
Boosting Customer Satisfaction
With improved product quality and efficiency, customer satisfaction naturally increases.
Reliable and high-quality products are key to building a loyal customer base.
Cost Reduction
By identifying and eliminating waste and inefficiencies, companies can significantly reduce costs.
Tools like the Scatter Diagram can help in understanding the root causes of costly issues, leading to more effective solutions.
Enhancing Team Collaboration
The process of using the Seven QC Tools often involves team brainstorming and discussion.
This collaborative approach fosters better communication and teamwork, essential components of any successful manufacturing operation.
The Seven QC Tools offer a structured and effective approach to tackling quality control issues in manufacturing.
By systematically applying these tools, companies can reap numerous benefits, ranging from improved product quality to increased productivity and customer satisfaction.
As demonstrated by the case studies, the practical application of these tools can lead to significant improvements and long-term success in the manufacturing industry.
資料ダウンロード
QCD調達購買管理クラウド「newji」は、調達購買部門で必要なQCD管理全てを備えた、現場特化型兼クラウド型の今世紀最高の購買管理システムとなります。
ユーザー登録
調達購買業務の効率化だけでなく、システムを導入することで、コスト削減や製品・資材のステータス可視化のほか、属人化していた購買情報の共有化による内部不正防止や統制にも役立ちます。
NEWJI DX
製造業に特化したデジタルトランスフォーメーション(DX)の実現を目指す請負開発型のコンサルティングサービスです。AI、iPaaS、および先端の技術を駆使して、製造プロセスの効率化、業務効率化、チームワーク強化、コスト削減、品質向上を実現します。このサービスは、製造業の課題を深く理解し、それに対する最適なデジタルソリューションを提供することで、企業が持続的な成長とイノベーションを達成できるようサポートします。
オンライン講座
製造業、主に購買・調達部門にお勤めの方々に向けた情報を配信しております。
新任の方やベテランの方、管理職を対象とした幅広いコンテンツをご用意しております。
お問い合わせ
コストダウンが利益に直結する術だと理解していても、なかなか前に進めることができない状況。そんな時は、newjiのコストダウン自動化機能で大きく利益貢献しよう!
(Β版非公開)