- お役立ち記事
- Factory Simulation and Operational Optimization Using Digital Twin Technology
Factory Simulation and Operational Optimization Using Digital Twin Technology
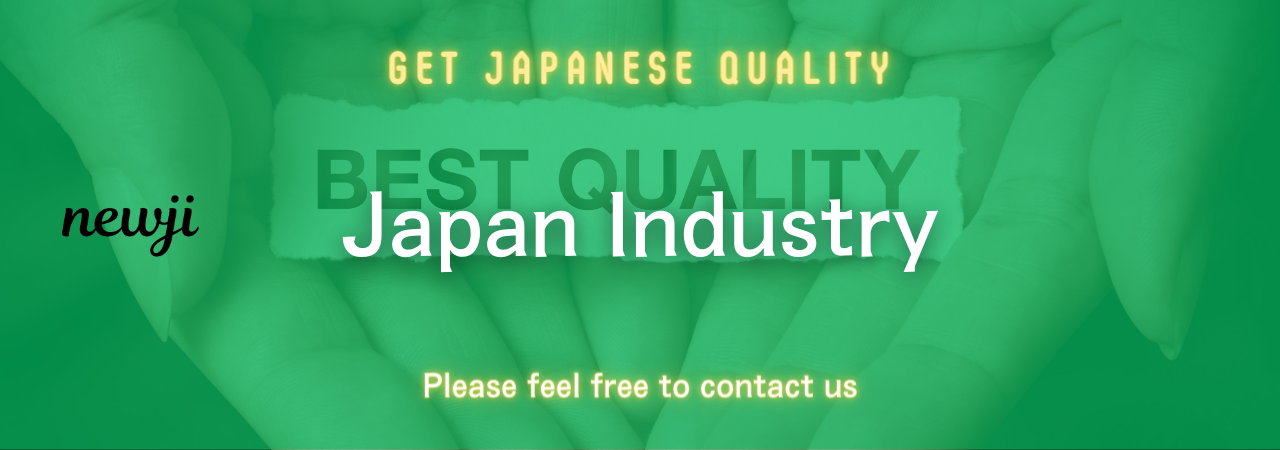
In recent years, digital twin technology has revolutionized various industries, including manufacturing.
It’s a powerful concept that helps companies create virtual models of their physical operations to simulate processes, identify inefficiencies, and optimize performance.
Digital twins, in simple terms, are digital replicas of physical assets, processes, systems, or entire facilities.
目次
Understanding Digital Twin Technology
Digital twin technology involves creating a digital counterpart that represents a real-world entity.
These digital models are typically updated in real-time with data collected from sensors embedded in the physical counterparts.
This replication allows organizations to analyze and optimize operations without interfering with actual production.
How Digital Twin Works
A digital twin integrates several technologies, including the Internet of Things (IoT), machine learning, and artificial intelligence.
IoT devices collect data from physical assets and transmit it to the digital twin.
Machine learning algorithms then analyze this data to predict outcomes and identify potential problems.
Meanwhile, artificial intelligence provides actionable insights for decision-making.
Benefits of Digital Twin Technology in Manufacturing
Manufacturers are increasingly adopting digital twin technology for its many advantages.
Here are some of the key benefits:
1. Improved Efficiency
Digital twins enable manufacturers to simulate production processes and identify bottlenecks or inefficiencies.
By addressing these issues virtually, companies can streamline operations and enhance overall efficiency.
This results in reduced downtime and increased productivity.
2. Predictive Maintenance
One of the most significant advantages of digital twin technology is its ability to predict equipment failures.
By continuously monitoring the condition of machinery, digital twins can forecast when maintenance is needed.
This predictive maintenance approach minimizes unplanned downtime and extends the lifespan of equipment.
3. Enhanced Product Quality
Manufacturers can use digital twins to test and refine product designs before actual production.
This allows them to detect and rectify potential flaws, ensuring higher quality products.
As a result, customers receive goods that meet or exceed their expectations.
4. Cost Reduction
Implementing digital twins can lead to significant cost savings.
By optimizing production processes and reducing waste, manufacturers can cut operating costs.
In addition, predictive maintenance prevents costly breakdowns, further reducing expenses.
5. Better Decision-Making
Digital twins provide valuable insights through real-time data analysis.
This information empowers manufacturers to make informed decisions quickly and accurately.
Whether it’s adjusting production schedules or reconfiguring machinery, decision-makers have the tools they need to respond effectively.
Operational Optimization with Digital Twins
Beyond improving efficiency and reducing costs, digital twin technology also plays a crucial role in operational optimization.
Simulation and Modeling
Digital twins enable manufacturers to create detailed simulations of their operations.
These models can replicate various scenarios to identify potential improvements.
For example, a factory can simulate different production line configurations to find the most efficient setup.
Resource Management
Effective resource management is essential for optimizing operations.
Digital twins help in tracking inventory levels, raw materials, and finished products.
By understanding resource usage patterns, manufacturers can plan more effectively and reduce waste.
Supply Chain Optimization
Supply chains are often complex and challenging to manage.
Digital twins can simulate the entire supply chain, from raw material procurement to product delivery.
This helps manufacturers identify and mitigate risks, ensuring a smoother and more reliable supply chain.
Energy Management
Energy consumption is a significant concern for many manufacturers.
Digital twins can monitor energy usage and identify areas where consumption can be reduced.
By implementing energy-saving measures, companies can lower their environmental impact and save costs.
Employee Training
Training employees effectively is critical for smooth operations.
Digital twins can create realistic training simulations, allowing workers to practice without real-world consequences.
This leads to better-prepared employees who can handle various scenarios efficiently.
Case Studies: Digital Twins in Action
Several companies have successfully implemented digital twins to optimize their operations.
General Electric (GE)
General Electric uses digital twin technology to monitor and maintain its industrial equipment.
By analyzing data from sensors, GE can predict when maintenance is needed, reducing downtime and maintenance costs.
Siemens
Siemens employs digital twins in its manufacturing processes to enhance product quality and efficiency.
The company uses virtual models to simulate production and optimize workflows.
Toyota
Toyota leverages digital twin technology to streamline its production lines.
By simulating different configurations, Toyota can identify the most efficient setups, leading to reduced waste and increased productivity.
Challenges and Future Outlook
While digital twin technology offers numerous benefits, it’s not without challenges.
Implementing and maintaining digital twins requires significant investment in technology and training.
Data security is also a concern, as digital twins rely on real-time data from physical assets.
Future Prospects
Despite these challenges, the future of digital twin technology is promising.
As technology continues to evolve, digital twins will become more sophisticated and accessible.
Advancements in IoT, AI, and machine learning will further enhance the capabilities of digital twins.
Conclusion
In conclusion, digital twin technology is transforming the manufacturing industry.
By creating virtual replicas of physical operations, manufacturers can optimize efficiency, reduce costs, and improve product quality.
While challenges exist, the benefits far outweigh them, making digital twins an essential tool for the future of manufacturing.
資料ダウンロード
QCD調達購買管理クラウド「newji」は、調達購買部門で必要なQCD管理全てを備えた、現場特化型兼クラウド型の今世紀最高の購買管理システムとなります。
ユーザー登録
調達購買業務の効率化だけでなく、システムを導入することで、コスト削減や製品・資材のステータス可視化のほか、属人化していた購買情報の共有化による内部不正防止や統制にも役立ちます。
NEWJI DX
製造業に特化したデジタルトランスフォーメーション(DX)の実現を目指す請負開発型のコンサルティングサービスです。AI、iPaaS、および先端の技術を駆使して、製造プロセスの効率化、業務効率化、チームワーク強化、コスト削減、品質向上を実現します。このサービスは、製造業の課題を深く理解し、それに対する最適なデジタルソリューションを提供することで、企業が持続的な成長とイノベーションを達成できるようサポートします。
オンライン講座
製造業、主に購買・調達部門にお勤めの方々に向けた情報を配信しております。
新任の方やベテランの方、管理職を対象とした幅広いコンテンツをご用意しております。
お問い合わせ
コストダウンが利益に直結する術だと理解していても、なかなか前に進めることができない状況。そんな時は、newjiのコストダウン自動化機能で大きく利益貢献しよう!
(Β版非公開)