- お役立ち記事
- How to Create QC Process Sheets & Work Standards and Prevent Quality Defects: Training and Development Techniques
How to Create QC Process Sheets & Work Standards and Prevent Quality Defects: Training and Development Techniques
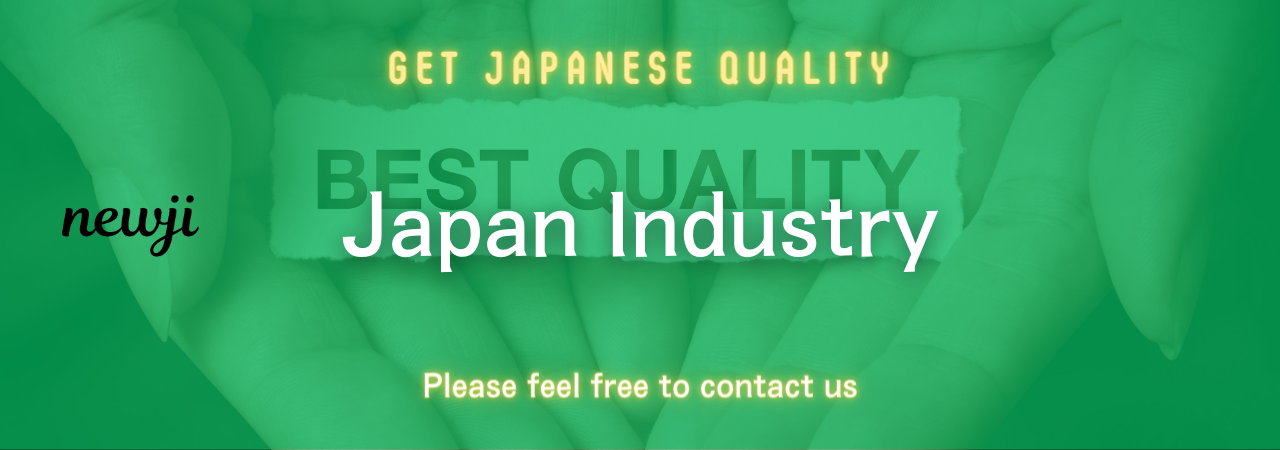
Creating a successful Quality Control (QC) process and work standards is crucial for ensuring consistent product quality and preventing defects.
In this article, we will break down everything you need to know about how to develop effective QC process sheets and work standards, along with training and development techniques to minimize quality defects.
目次
Why Quality Control is Crucial
Quality control ensures that products meet the required standards before reaching consumers.
Without a robust QC process, defects could occur, leading to customer dissatisfaction and potential financial losses.
A well-designed QC process emphasizes consistency, reliability, and customer satisfaction.
Understanding QC Process Sheets
QC process sheets serve as guidelines for quality inspections.
They outline the steps to be followed and criteria to be checked.
Having detailed and clear QC process sheets ensures that inspections are conducted systematically and uniformly.
The Components of QC Process Sheets
An effective QC process sheet should include the following components:
– **Inspection Criteria**: List the quality parameters that need to be checked.
– **Inspection Tools**: Mention any tools or equipment required for inspections.
– **Acceptance Standards**: Define what is considered acceptable or unacceptable.
– **Step-by-Step Instructions**: Give detailed instructions for each inspection step.
– **Documentation Requirements**: Specify what needs to be documented during inspections.
Developing Work Standards
Work standards are the set guidelines and procedures that employees should follow to ensure quality.
These serve as the backbone of a consistent and efficient production process.
Steps to Create Work Standards
1. **Analyze Current Processes**: Review existing procedures and identify areas for improvement.
2. **Define Objectives**: Clearly outline the goals of the work standards, such as reducing defects or improving efficiency.
3. **Collaborate with Team Members**: Involve those who will be implementing the work standards to gain valuable insights.
4. **Document Procedures**: Write detailed instructions for each process to ensure clarity.
5. **Review and Revise**: Periodically review the work standards to ensure they are still effective and make adjustments as needed.
Training and Development Techniques
Training and development are critical for ensuring that employees understand and can effectively implement QC process sheets and work standards.
Initial Training
Start with comprehensive training sessions that cover the basics of QC, inspection criteria, and work standards.
Use a mix of theoretical and practical training to give employees a well-rounded understanding.
On-the-Job Training
On-the-job training allows employees to apply what they’ve learned in a real-world setting.
Pair new employees with experienced ones to mentor them through the process.
Continuous Development
Quality control is not a one-time task; it requires continuous improvement.
Regularly schedule refresher courses and advanced training sessions to keep employees up-to-date on best practices and new developments in the field.
Feedback Mechanisms
Establish mechanisms for employees to provide feedback.
Encourage them to share any challenges they face in following QC process sheets or work standards.
This feedback can be invaluable for making necessary adjustments.
Preventing Quality Defects
Prevention is always better than cure.
By implementing robust QC process sheets and work standards, you can significantly reduce the likelihood of defects.
Proactive Measures
– **Regular Audits**: Conduct frequent audits to ensure compliance with established standards.
– **Root Cause Analysis**: When a defect is identified, perform a root cause analysis to determine the underlying issue.
– **Preventive Maintenance**: Regularly maintain equipment to prevent malfunctions that could lead to defects.
Employee Involvement
Encourage employees to take ownership of quality control.
Involving them in the development and review of QC process sheets and work standards can lead to better adherence and proactive problem solving.
Use Technology
Leverage technology to streamline quality control processes.
Digital QC process sheets can be easily updated and accessed, ensuring that everyone is always working with the latest information.
Conclusion
Creating effective QC process sheets and work standards is integral to maintaining high-quality products and preventing defects.
Through careful planning, employee training, and continuous improvement, you can achieve consistent product quality and enhance customer satisfaction.
Implement these strategies in your organization to see substantial improvements in your quality control processes.
資料ダウンロード
QCD調達購買管理クラウド「newji」は、調達購買部門で必要なQCD管理全てを備えた、現場特化型兼クラウド型の今世紀最高の購買管理システムとなります。
ユーザー登録
調達購買業務の効率化だけでなく、システムを導入することで、コスト削減や製品・資材のステータス可視化のほか、属人化していた購買情報の共有化による内部不正防止や統制にも役立ちます。
NEWJI DX
製造業に特化したデジタルトランスフォーメーション(DX)の実現を目指す請負開発型のコンサルティングサービスです。AI、iPaaS、および先端の技術を駆使して、製造プロセスの効率化、業務効率化、チームワーク強化、コスト削減、品質向上を実現します。このサービスは、製造業の課題を深く理解し、それに対する最適なデジタルソリューションを提供することで、企業が持続的な成長とイノベーションを達成できるようサポートします。
オンライン講座
製造業、主に購買・調達部門にお勤めの方々に向けた情報を配信しております。
新任の方やベテランの方、管理職を対象とした幅広いコンテンツをご用意しております。
お問い合わせ
コストダウンが利益に直結する術だと理解していても、なかなか前に進めることができない状況。そんな時は、newjiのコストダウン自動化機能で大きく利益貢献しよう!
(Β版非公開)