- お役立ち記事
- Improving Energy Efficiency in Blow Molding: Practical Approaches
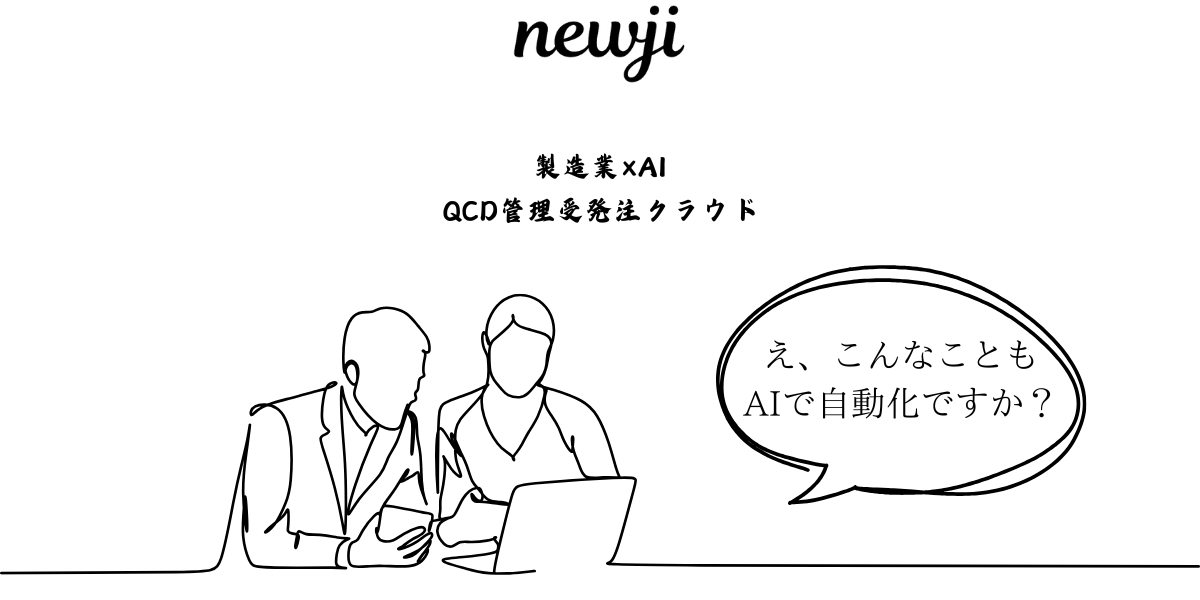
Improving Energy Efficiency in Blow Molding: Practical Approaches
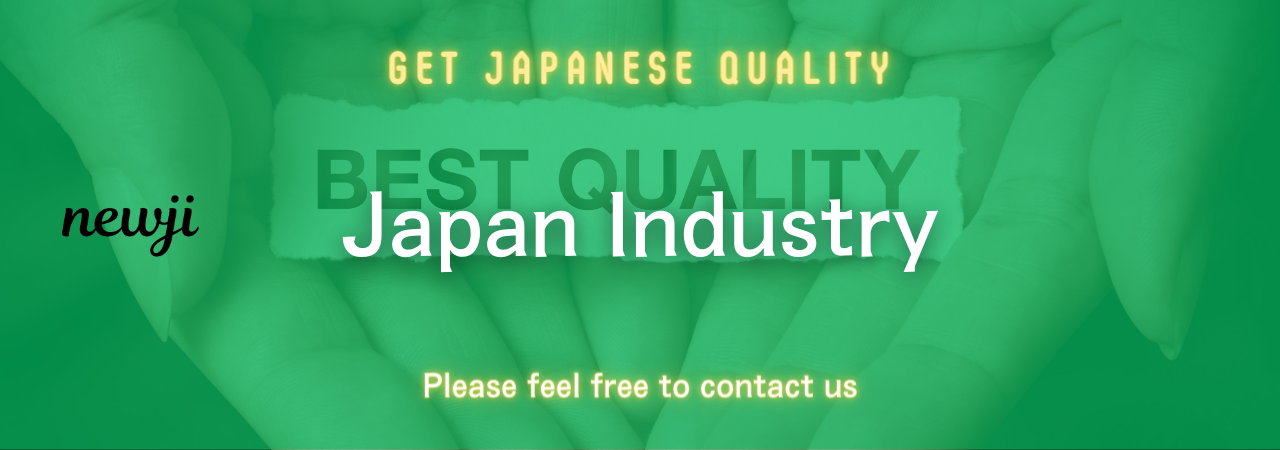
Blow molding is a widely used manufacturing process for creating hollow plastic parts, such as bottles and containers.
However, despite its popularity, blow molding can be quite energy-intensive.
Improving energy efficiency in blow molding is crucial not only for reducing production costs but also for minimizing environmental impact.
目次
Understanding Energy Usage in Blow Molding
Blow molding involves several stages, each requiring a significant amount of energy.
The primary stages include melting the plastic material, forming it into a parison (a tube-like piece of plastic), and then blowing it into the desired shape within a mold.
Heating the plastic to a molten state is one of the most energy-consuming steps.
Moreover, maintaining optimal temperatures throughout the process is crucial for ensuring product quality.
Heating Elements
The heating elements used in blow molding machines play a significant role in energy consumption.
Traditional electric resistance heaters are commonly used, but they are not the most energy-efficient option.
Induction heating, on the other hand, provides a more energy-efficient alternative.
Induction heaters use electromagnetic fields to heat the plastic directly, resulting in faster and more efficient heating.
Extrusion Process
The extrusion process, where plastic is melted and formed into a parison, also demands a considerable amount of energy.
Optimizing the extrusion process can lead to significant energy savings.
Using energy-efficient extruders and ensuring proper maintenance can reduce energy usage.
Additionally, minimizing the residence time (the time plastic spends in the extruder) can prevent unnecessary energy expenditure.
Implementing Energy-Efficient Technologies
Modern advancements in technology have introduced several energy-efficient solutions for the blow molding industry.
By adopting these technologies, manufacturers can enhance their energy efficiency and reduce overall production costs.
Variable Frequency Drives (VFDs)
Variable Frequency Drives (VFDs) are devices that control the speed of electric motors.
By using VFDs in blow molding machines, manufacturers can adjust the motor speed based on the specific requirements of the process.
This results in reduced energy consumption and increased efficiency.
VFDs are particularly effective in applications with fluctuating load demands, as they prevent motors from operating at full speed when not necessary.
Insulation and Heat Recovery
Proper insulation of blow molding machinery can significantly reduce heat loss and energy consumption.
Insulating components such as barrels, molds, and heating zones can maintain optimal temperatures more efficiently.
Additionally, heat recovery systems can capture and reuse waste heat generated during the process.
This recovered heat can be used for preheating the plastic material or other auxiliary processes, further improving energy efficiency.
Advanced Control Systems
Implementing advanced control systems can optimize various parameters of the blow molding process, leading to improved energy efficiency.
These systems can monitor and adjust factors such as temperature, pressure, and cycle times in real-time.
By maintaining precise control over these variables, manufacturers can minimize energy wastage and ensure consistent product quality.
Material Selection and Optimization
The choice of plastic material and its preparation can also impact the energy efficiency of the blow molding process.
Selecting the right material and optimizing its usage can lead to significant energy savings.
Lightweight Materials
Using lightweight plastic materials can reduce the energy required for the blow molding process.
Lightweight materials typically require less energy to heat and form into the desired shape.
Moreover, these materials can help reduce the overall weight of the final product, leading to further energy savings during transportation and handling.
Recycled Materials
Incorporating recycled plastic materials into the blow molding process can contribute to energy efficiency.
Recycled materials often require less energy to process compared to virgin plastics.
By using recycled materials, manufacturers can reduce their energy consumption and environmental footprint.
Material Preparation
Proper preparation of plastic materials before processing is essential for improving energy efficiency.
Pre-drying the plastic pellets to remove moisture can prevent energy wastage during the heating process.
Additionally, using granulators and crushers to reduce the size of plastic waste can make it easier to reprocess and reduce energy consumption.
Optimizing Production Processes
Streamlining and optimizing production processes can significantly enhance energy efficiency in blow molding.
By focusing on process improvements, manufacturers can minimize energy wastage and maximize productivity.
Process Automation
Automation can play a crucial role in improving energy efficiency.
Automated systems can monitor and control various aspects of the blow molding process with precision.
This reduces the likelihood of human error and ensures optimal operation.
Automated processes are often more consistent and efficient, leading to reduced energy consumption.
Regular Maintenance
Maintaining blow molding equipment in good condition is vital for energy efficiency.
Regular inspections and maintenance can identify and address issues that may lead to energy wastage.
Lubricating moving parts, cleaning filters, and checking for leaks are essential maintenance tasks that can improve overall efficiency.
Cycle Time Reduction
Reducing cycle times in blow molding can lead to significant energy savings.
Shorter cycle times mean that the equipment operates for less time, consuming less energy.
Optimizing cooling times, mold design, and other process parameters can help achieve faster cycle times without compromising product quality.
Training and Awareness
Educating and training employees about energy-efficient practices is crucial for achieving long-term improvements in energy efficiency.
Creating a culture of energy awareness within the organization can lead to more sustainable practices.
Employee Training
Providing training programs for employees can enhance their understanding of energy-efficient practices.
Training should cover topics such as proper equipment operation, maintenance procedures, and energy-saving techniques.
Well-informed employees are more likely to adopt energy-efficient behaviors and contribute to overall efficiency improvements.
Energy Audits
Conducting regular energy audits can help identify areas of improvement in blow molding operations.
Energy audits involve assessing energy usage, identifying inefficiencies, and recommending actionable solutions.
By implementing the recommendations from energy audits, manufacturers can achieve significant energy savings and productivity improvements.
By focusing on these practical approaches, manufacturers can achieve significant energy savings and contribute to a more sustainable future.
資料ダウンロード
QCD調達購買管理クラウド「newji」は、調達購買部門で必要なQCD管理全てを備えた、現場特化型兼クラウド型の今世紀最高の購買管理システムとなります。
ユーザー登録
調達購買業務の効率化だけでなく、システムを導入することで、コスト削減や製品・資材のステータス可視化のほか、属人化していた購買情報の共有化による内部不正防止や統制にも役立ちます。
NEWJI DX
製造業に特化したデジタルトランスフォーメーション(DX)の実現を目指す請負開発型のコンサルティングサービスです。AI、iPaaS、および先端の技術を駆使して、製造プロセスの効率化、業務効率化、チームワーク強化、コスト削減、品質向上を実現します。このサービスは、製造業の課題を深く理解し、それに対する最適なデジタルソリューションを提供することで、企業が持続的な成長とイノベーションを達成できるようサポートします。
オンライン講座
製造業、主に購買・調達部門にお勤めの方々に向けた情報を配信しております。
新任の方やベテランの方、管理職を対象とした幅広いコンテンツをご用意しております。
お問い合わせ
コストダウンが利益に直結する術だと理解していても、なかなか前に進めることができない状況。そんな時は、newjiのコストダウン自動化機能で大きく利益貢献しよう!
(Β版非公開)