- お役立ち記事
- How SMEs Can Improve Efficiency and Quality in EDM
How SMEs Can Improve Efficiency and Quality in EDM
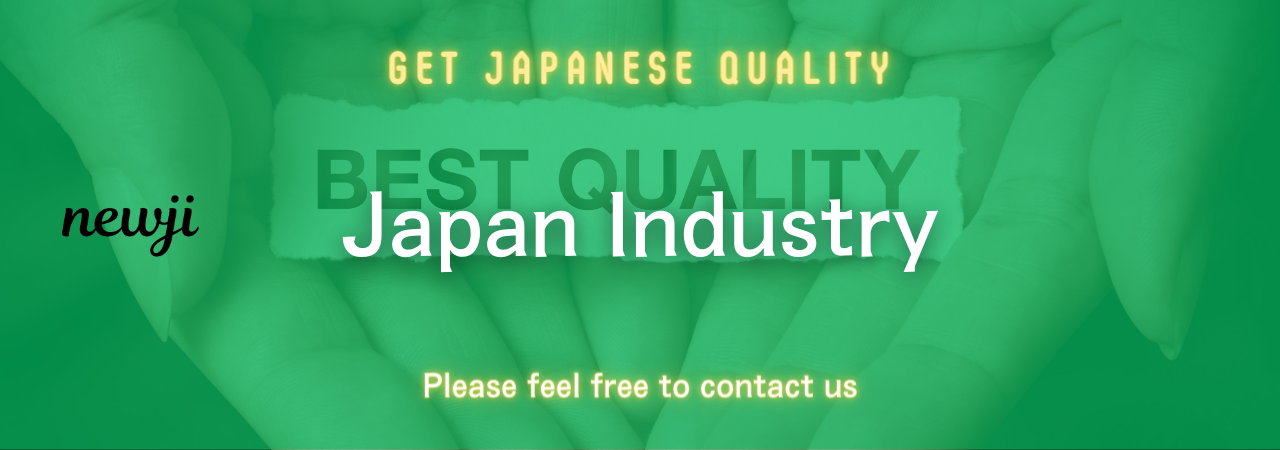
目次
Understanding EDM for Your SME
Electrical Discharge Machining, commonly known as EDM, is a technique used for shaping hard metals and conducting intricate electrics via controlled electric sparks.
For small and medium-sized enterprises (SMEs), mastering EDM can significantly improve both efficiency and product quality.
But what exactly is EDM, and how can SMEs harness its potential?
What is EDM?
EDM is a manufacturing process where electrical discharges or sparks are used to shape materials.
This method is particularly effective for materials that are difficult to cut using traditional machining methods.
EDM works by creating a series of rapid electrical discharges between an electrode and the workpiece.
These discharges generate heat, melting and vaporizing the material to create the desired shape.
There are two main types of EDM: wire EDM and sinker EDM.
Wire EDM uses a thin, electrically charged wire to cut the material, while sinker EDM utilizes a shaped electrode to form cavities in the workpiece.
Both methods offer high precision and the ability to produce intricate designs.
Why Should SMEs Consider EDM?
For SMEs, investing in EDM technology offers several compelling advantages.
By understanding these benefits, SMEs can make informed decisions on adopting EDM for their operations.
Precision and Accuracy
One of the primary benefits of EDM is its ability to produce highly precise and accurate results.
The controlled electrical discharges can achieve tolerances as tight as a few microns.
This level of precision is especially crucial for industries such as aerospace, automotive, and medical devices, where parts must meet stringent quality standards.
Complex Geometries
EDM is well-suited for creating complex and intricate shapes that would be challenging or impossible to achieve using traditional machining methods.
This capability allows SMEs to expand their offerings and cater to a broader range of customer needs.
Hard Material Machining
Many traditional machining methods struggle with hard or exotic materials.
EDM excels in machining hard materials such as titanium, tungsten, and hardened steels.
This ability allows SMEs to work with a wider variety of materials, offering greater versatility in their operations.
Reduced Tool Wear
EDM does not involve direct contact between the electrode and the material, resulting in minimal tool wear.
This extends the lifespan of the electrode and reduces the frequency of tool replacements, leading to lower production costs.
Implementing EDM in Your SME
Adopting EDM technology involves several steps to ensure a smooth transition and maximize the benefits.
Here are some key considerations for SMEs looking to implement EDM.
Assessing Your Needs
Before investing in EDM equipment, it’s essential to assess your specific needs and objectives.
Identify the types of materials you will be working with, the level of precision required, and the complexity of the geometries you need to produce.
This evaluation will help you choose the right type of EDM equipment for your operations.
Choosing the Right Equipment
There are various EDM machines available on the market, each with its own features and capabilities.
Consider factors such as machine size, power capacity, and programming options.
It’s also important to select reliable manufacturers and suppliers who can provide quality equipment and ongoing support.
Training and Skill Development
EDM technology requires specialized knowledge and skills to operate effectively.
Investing in training and skill development for your employees is crucial to ensure they can use the equipment safely and efficiently.
Many equipment manufacturers offer training programs and resources to help your team get up to speed.
Maintenance and Upkeep
Regular maintenance is essential to keep your EDM equipment in optimal condition.
Develop a maintenance schedule that includes cleaning, lubrication, and inspection of critical components.
This proactive approach will help prevent unexpected breakdowns and extend the lifespan of your equipment.
Maximizing Efficiency with EDM
To fully leverage the benefits of EDM, it’s important to focus on maximizing efficiency in your operations.
Here are some strategies to enhance productivity and quality.
Automation and Integration
Integrating EDM machines with computer-aided design (CAD) and computer-aided manufacturing (CAM) software can streamline your workflow and reduce manual errors.
Automation can also improve cycle times and increase consistency in production.
Process Optimization
Continuously evaluate and optimize your EDM processes to identify areas for improvement.
Analyze factors such as electrode wear, discharge settings, and cooling methods to enhance efficiency and quality.
Implementing lean manufacturing principles can also help eliminate waste and improve overall productivity.
Quality Control
Implement robust quality control measures to ensure the final products meet the required specifications and standards.
Regularly inspect and test the output of your EDM processes to identify any deviations and address them promptly.
Utilize advanced inspection tools such as coordinate measuring machines (CMM) to verify the accuracy of your parts.
Future Trends in EDM Technology
EDM technology continues to evolve, with new advancements offering even greater potential for SMEs.
Staying informed about these trends can help your SME remain competitive and capitalize on emerging opportunities.
Micro-EDM
Micro-EDM is a specialized form of EDM that enables the machining of extremely small and delicate parts.
This technology is particularly valuable for industries such as electronics and medical devices, where precision at the microscopic level is required.
Electrode Materials
Advancements in electrode materials are enhancing the efficiency and performance of EDM processes.
Materials such as graphite, copper tungsten, and composite electrodes offer improved conductivity and durability, leading to higher quality outcomes.
Hybrid EDM Machines
Hybrid EDM machines combine EDM with other machining processes, such as milling or grinding, to offer a more versatile and efficient solution.
These machines enable SMEs to perform multiple operations in a single setup, reducing production times and costs.
Conclusion: Embrace the Power of EDM
Adopting EDM technology can offer significant benefits for SMEs, from improved precision and efficiency to the ability to work with complex geometries and hard materials.
By carefully assessing your needs, choosing the right equipment, and investing in training and maintenance, you can harness the full potential of EDM for your operations.
Stay informed about emerging trends and continuously optimize your processes to remain competitive in the dynamic manufacturing landscape.
With the power of EDM, your SME can achieve new levels of quality and efficiency, driving success and growth in your industry.
資料ダウンロード
QCD調達購買管理クラウド「newji」は、調達購買部門で必要なQCD管理全てを備えた、現場特化型兼クラウド型の今世紀最高の購買管理システムとなります。
ユーザー登録
調達購買業務の効率化だけでなく、システムを導入することで、コスト削減や製品・資材のステータス可視化のほか、属人化していた購買情報の共有化による内部不正防止や統制にも役立ちます。
NEWJI DX
製造業に特化したデジタルトランスフォーメーション(DX)の実現を目指す請負開発型のコンサルティングサービスです。AI、iPaaS、および先端の技術を駆使して、製造プロセスの効率化、業務効率化、チームワーク強化、コスト削減、品質向上を実現します。このサービスは、製造業の課題を深く理解し、それに対する最適なデジタルソリューションを提供することで、企業が持続的な成長とイノベーションを達成できるようサポートします。
オンライン講座
製造業、主に購買・調達部門にお勤めの方々に向けた情報を配信しております。
新任の方やベテランの方、管理職を対象とした幅広いコンテンツをご用意しております。
お問い合わせ
コストダウンが利益に直結する術だと理解していても、なかなか前に進めることができない状況。そんな時は、newjiのコストダウン自動化機能で大きく利益貢献しよう!
(Β版非公開)