- お役立ち記事
- QC Practices
QC Practices
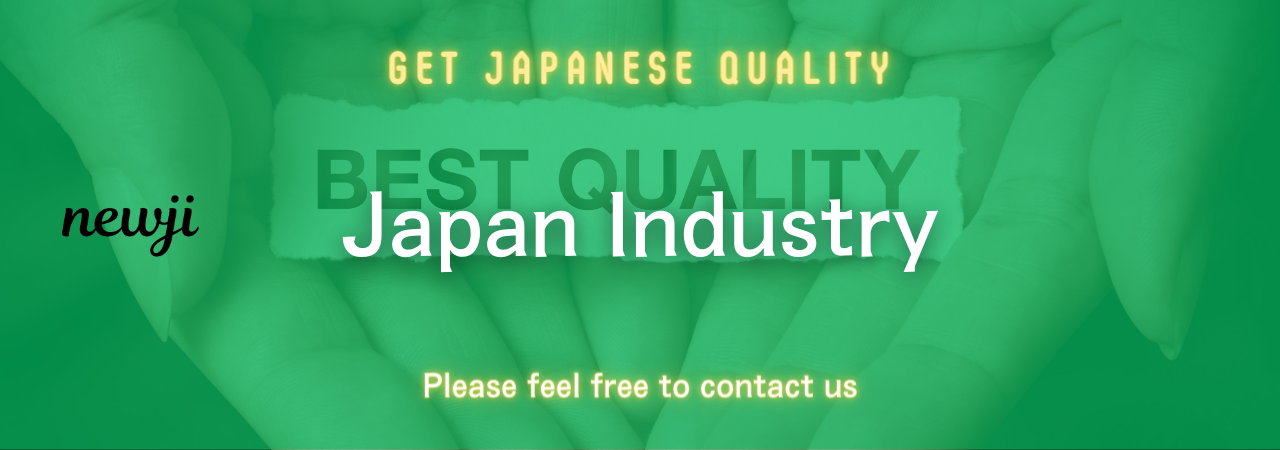
Quality control (QC) practices are essential in ensuring that products and services meet certain standards and specifications. Maintaining stringent QC practices helps businesses deliver superior quality, boosting customer satisfaction and trust. Proper implementation of quality control can also lead to cost savings by minimizing waste and reducing the need for rework or correction of faulty products.
目次
Understanding Quality Control
Quality control refers to the processes and methodologies used to ensure that a product or service adheres to a predefined set of quality criteria. These criteria can include company standards, industry regulations, or customer requirements. QC typically involves various procedures such as inspection, testing, and reviewing to determine if a product or service meets the desired level of quality.
Companies across different industries employ quality control measures. For example, in manufacturing, QC might involve the inspection of raw materials, in-process checks, and finished product testing. In the software industry, QC could involve thorough testing of software applications before release to ensure functionality and performance.
Key Components of Quality Control
Effective QC practices are built upon several key components. These include:
1. Setting Quality Standards
Establishing clear, measurable quality standards is critical for effective QC. These standards provide a benchmark against which products or services can be evaluated. Companies should develop standards based on customer expectations, industry regulations, and their quality goals.
2. Regular Inspections
Regular inspections help identify defects or issues early in the production process. Inspections can be conducted at various stages, from raw material receipt to final product ready for shipment. Conducting routine checks ensures that any deviations from the standards are identified and rectified promptly.
3. Comprehensive Testing
In addition to inspections, comprehensive testing of products or services is necessary. Testing can be functional, performance-based, or involve stress testing to determine reliability. For instance, in the food industry, testing might include assessing microbial contamination and nutritional value.
4. Use of Control Charts and Statistical Methods
Control charts and statistical methods are valuable tools in QC. By analyzing data trends and variation, companies can determine if a process is in control or if corrective actions are needed. These methods help in predicting and preventing issues before they become significant problems.
Implementing Quality Control
Implementing QC involves several steps:
1. Define Objectives and Standards
Clearly defining what needs to be achieved is the first step. This includes setting the quality standards and identifying the critical points where QC will be implemented. Objectives should align with the broader business goals and customer expectations.
2. Training and Development
Staff should be adequately trained in QC procedures and the importance of maintaining quality. Regular training ensures that employees are up-to-date with the latest QC practices and techniques.
3. Use of Technology
Leveraging technology can enhance QC processes. For example, automated inspection systems can detect defects more accurately and efficiently than manual checks. Software tools can be used to analyze data and generate control charts, providing valuable insights into the production process.
4. Continuous Improvement
QC should not be a static process. Continuous improvement involves regularly reviewing QC practices and making necessary adjustments to enhance quality. This could include updating standards, adopting new technologies, or refining procedures to address emerging challenges.
Benefits of Effective Quality Control
Effective QC practices offer several benefits:
1. Enhanced Customer Satisfaction
Delivering high-quality products and services consistently leads to satisfied customers. Satisfied customers are more likely to become repeat buyers, provide positive feedback, and refer your business to others.
2. Reduced Costs
Implementing QC helps in identifying defects early, reducing waste and avoiding costly rework. By addressing issues before products reach the market, businesses can save significant resources.
3. Improved Reputation
A strong commitment to quality can enhance a company’s reputation. Companies known for their quality control are seen as reliable and trustworthy, which can be a significant competitive advantage.
4. Compliance and Risk Management
QC ensures compliance with industry regulations and standards, reducing the risk of penalties or legal issues. It also helps in managing potential risks by identifying and addressing issues before they escalate.
Challenges in Quality Control
Despite its benefits, implementing QC can pose several challenges:
1. High Initial Costs
Setting up QC systems and procedures can be expensive. The cost of equipment, technology, and training can be significant, especially for small businesses with limited resources.
2. Resistance to Change
Employees may resist changes to established processes. Introducing new QC practices requires effective communication and sometimes, a cultural shift within the organization.
3. Complexity of Processes
Some production processes are highly complex, making it difficult to implement consistent QC. This is particularly true in industries where products are customized or highly variable.
Conclusion
Quality control is a critical component of any successful business. By setting clear standards, conducting regular inspections and testing, and leveraging technology, companies can ensure their products and services meet the highest quality criteria. Despite the challenges, the benefits of effective QC practices are substantial, ranging from enhanced customer satisfaction to cost savings and improved reputation. As industries evolve, continuous improvement in QC practices will remain essential for maintaining high standards and driving business success.
資料ダウンロード
QCD調達購買管理クラウド「newji」は、調達購買部門で必要なQCD管理全てを備えた、現場特化型兼クラウド型の今世紀最高の購買管理システムとなります。
ユーザー登録
調達購買業務の効率化だけでなく、システムを導入することで、コスト削減や製品・資材のステータス可視化のほか、属人化していた購買情報の共有化による内部不正防止や統制にも役立ちます。
NEWJI DX
製造業に特化したデジタルトランスフォーメーション(DX)の実現を目指す請負開発型のコンサルティングサービスです。AI、iPaaS、および先端の技術を駆使して、製造プロセスの効率化、業務効率化、チームワーク強化、コスト削減、品質向上を実現します。このサービスは、製造業の課題を深く理解し、それに対する最適なデジタルソリューションを提供することで、企業が持続的な成長とイノベーションを達成できるようサポートします。
オンライン講座
製造業、主に購買・調達部門にお勤めの方々に向けた情報を配信しております。
新任の方やベテランの方、管理職を対象とした幅広いコンテンツをご用意しております。
お問い合わせ
コストダウンが利益に直結する術だと理解していても、なかなか前に進めることができない状況。そんな時は、newjiのコストダウン自動化機能で大きく利益貢献しよう!
(Β版非公開)