- お役立ち記事
- Addressing the Skills Gap: Digital Training Programs for the Manufacturing Industry
Addressing the Skills Gap: Digital Training Programs for the Manufacturing Industry
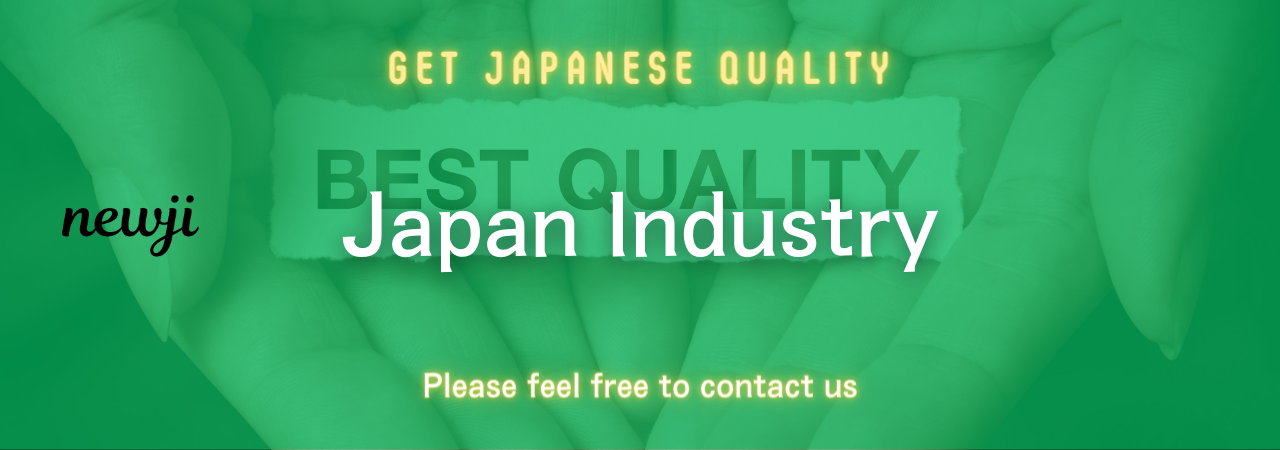
The manufacturing industry is rapidly evolving, with digital technologies reshaping the landscape.
However, the shift towards Industry 4.0 is not without challenges.
One of the most pressing issues is the widening skills gap.
As automation, robotics, and artificial intelligence become central to modern manufacturing, there is an urgent need to equip the workforce with the relevant skills.
This article explores how digital training programs can be a solution to bridge this skills gap and ensure the manufacturing sector remains competitive.
目次
Understanding the Skills Gap
The skills gap in the manufacturing industry is characterized by a mismatch between the skills required by employers and those possessed by the workforce.
This disparity is particularly evident in areas requiring advanced technical knowledge.
Traditional manufacturing skills are no longer sufficient as digital tools become integral to operations.
Employers are looking for workers who are proficient in data analysis, cybersecurity, and the operation of complex machinery.
The Impact on the Manufacturing Industry
The skills gap has significant implications for the manufacturing industry.
Companies struggle to fill critical positions, leading to decreased productivity and innovation.
Without a workforce adept in digital technologies, manufacturers risk falling behind global competitors.
Moreover, the inability to harness new technologies fully can lead to inefficient processes and increased operational costs.
Addressing this gap is crucial for sustaining growth and maintaining a competitive edge.
The Role of Digital Training Programs
Digital training programs are emerging as a vital tool to bridge the skills gap in manufacturing.
These programs leverage online platforms, virtual simulations, and interactive modules to deliver training.
They offer flexibility in learning, allowing employees to upskill at their own pace and convenience.
Furthermore, digital training can be tailored to meet the specific needs of the manufacturing industry, ensuring that workers gain the relevant knowledge and practical skills required.
Types of Digital Training Programs
Several types of digital training programs are particularly effective in the manufacturing sector:
1. Online Courses
Online courses offer comprehensive and structured learning paths.
They cover various topics, from basic digital literacy to advanced manufacturing technologies.
Platforms like Coursera, Udacity, and edX provide courses that are accessible and affordable, making them ideal for continuous learning.
2. Virtual Reality (VR) Training
Virtual Reality (VR) is another innovative way to deliver training.
VR allows employees to immerse themselves in realistic manufacturing environments, enabling hands-on practice without the risks associated with real-world operations.
This type of training is particularly beneficial for complex and hazardous tasks.
3. Simulation-Based Training
Simulation-based training uses computer-generated models to replicate manufacturing processes.
Employees can interact with these simulations to understand the intricacies of machinery and production lines.
This method helps in building practical skills and testing theoretical knowledge in a controlled setting.
4. Microlearning Modules
Microlearning breaks down complex subjects into bite-sized, easily digestible lessons.
These modules are usually short and focused, targeting specific skills or knowledge areas.
Microlearning is effective for busy professionals who need to fit learning into their tight schedules.
Benefits of Digital Training Programs
Digital training programs offer numerous benefits for both employees and employers in the manufacturing industry.
Enhanced Learning Experience
Digital training programs provide an interactive and engaging learning experience.
The use of multimedia elements, such as videos, animations, and interactive quizzes, makes learning more enjoyable and effective.
This approach can lead to better retention of knowledge and skills.
Accessibility and Convenience
One of the significant advantages of digital training is its accessibility.
Employees can access training materials from anywhere and at any time.
This flexibility is particularly beneficial for shift workers and those in remote locations.
It ensures that all employees have the opportunity to participate in training programs.
Cost-Effectiveness
Digital training programs are often more cost-effective compared to traditional training methods.
They eliminate the need for physical classrooms, travel expenses, and printed materials.
Moreover, once developed, digital training content can be reused and updated easily, providing long-term savings.
Tracking and Assessment
Digital training platforms typically come with built-in tracking and assessment tools.
These features allow employers to monitor the progress of their employees and evaluate the effectiveness of training programs.
Real-time feedback and performance analytics help in identifying areas for improvement and tailoring future training initiatives.
Implementing Digital Training Programs
For digital training programs to be successful, it is essential to have a strategic approach.
Manufacturers need to assess the skills requirements and identify gaps that need addressing.
Collaboration with educational institutions and technology providers can also be beneficial.
These partnerships can help in developing customized training content that meets industry standards.
Encouraging a Learning Culture
Creating a culture of continuous learning within the organization is crucial.
Employees should be encouraged to take ownership of their professional development.
Incentives, such as recognition and career advancement opportunities, can motivate employees to participate in training programs.
Utilizing Technology
Leveraging the latest technologies is vital in the effective delivery of digital training.
Manufacturers should invest in reliable and user-friendly platforms.
Ensuring seamless access to training materials and support services can enhance the overall learning experience.
Evaluating Effectiveness
Regular evaluation of training programs is necessary to ensure their effectiveness.
Feedback from employees can provide valuable insights into areas that need improvement.
Employers should continually update training content to keep pace with technological advancements and industry changes.
Digital training programs are a powerful solution to the skills gap in the manufacturing industry.
They offer flexibility, accessibility, and cost-effectiveness, making them an ideal tool for upskilling the workforce.
By investing in digital training, manufacturers can ensure their employees are equipped with the necessary skills to thrive in the digital era.
This proactive approach will help in maintaining competitiveness and driving innovation in the manufacturing sector.
資料ダウンロード
QCD調達購買管理クラウド「newji」は、調達購買部門で必要なQCD管理全てを備えた、現場特化型兼クラウド型の今世紀最高の購買管理システムとなります。
ユーザー登録
調達購買業務の効率化だけでなく、システムを導入することで、コスト削減や製品・資材のステータス可視化のほか、属人化していた購買情報の共有化による内部不正防止や統制にも役立ちます。
NEWJI DX
製造業に特化したデジタルトランスフォーメーション(DX)の実現を目指す請負開発型のコンサルティングサービスです。AI、iPaaS、および先端の技術を駆使して、製造プロセスの効率化、業務効率化、チームワーク強化、コスト削減、品質向上を実現します。このサービスは、製造業の課題を深く理解し、それに対する最適なデジタルソリューションを提供することで、企業が持続的な成長とイノベーションを達成できるようサポートします。
オンライン講座
製造業、主に購買・調達部門にお勤めの方々に向けた情報を配信しております。
新任の方やベテランの方、管理職を対象とした幅広いコンテンツをご用意しております。
お問い合わせ
コストダウンが利益に直結する術だと理解していても、なかなか前に進めることができない状況。そんな時は、newjiのコストダウン自動化機能で大きく利益貢献しよう!
(Β版非公開)