- お役立ち記事
- Key Points of Precision Machining Technology Transforming Small-Lot Production
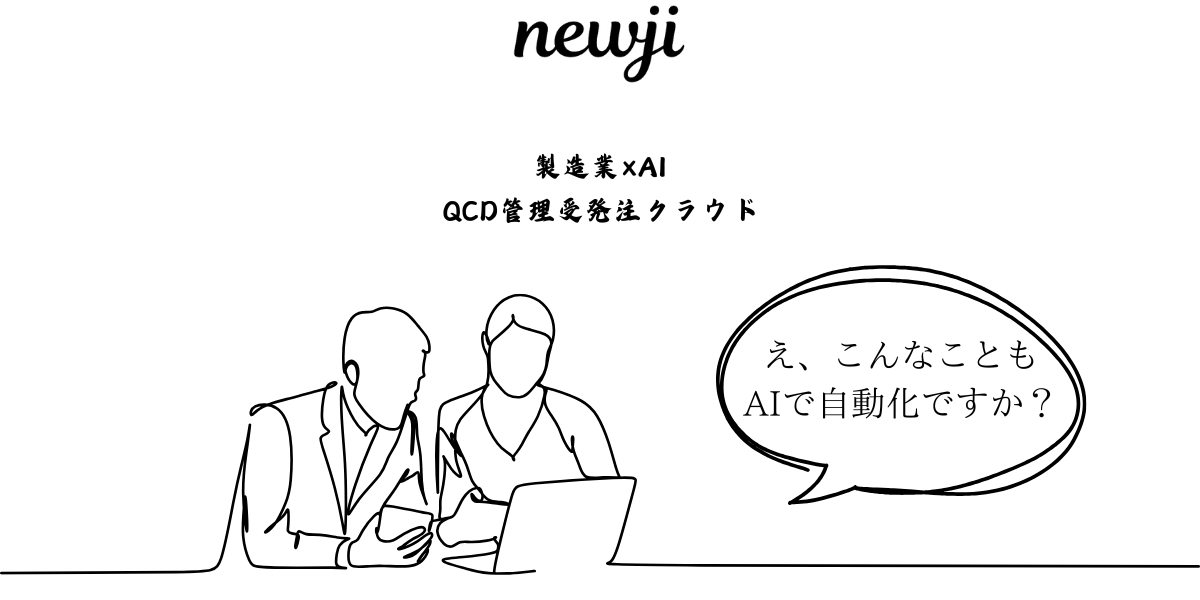
Key Points of Precision Machining Technology Transforming Small-Lot Production
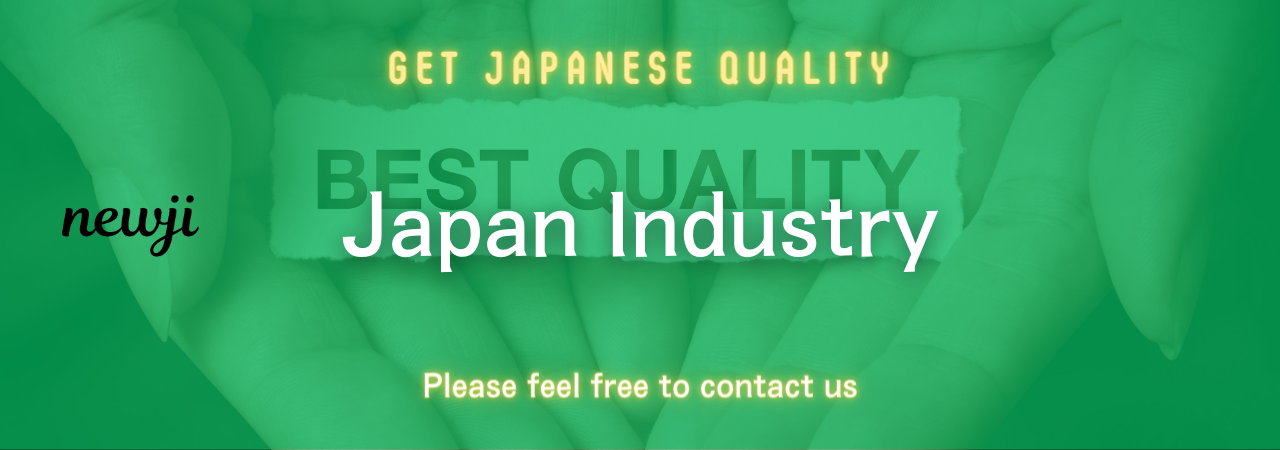
Precision machining technology has significantly transformed the way small-lot production is conducted.
With the advent of advanced machinery and innovative techniques, even small-scale productions can achieve high levels of accuracy and efficiency.
This is essential for industries where precision is non-negotiable, such as aerospace, medical devices, and automotive components.
Let’s delve into the key points of this groundbreaking technology.
目次
What Is Precision Machining?
Precision machining is a process used to produce complex parts and components with tight tolerances.
It involves the use of computer numerical control (CNC) machines, lasers, and other advanced tools to remove material from a workpiece.
The goal is to achieve a predetermined design that meets exact specifications.
Traditional machining methods often rely on manual operation, which can lead to errors and inconsistencies.
In contrast, precision machining automates the process, ensuring high accuracy and repeatability.
This is particularly beneficial in small-lot production, where each piece must meet stringent quality standards.
Benefits of Precision Machining in Small-Lot Production
High Accuracy
One of the primary advantages of precision machining is its unparalleled accuracy.
Advanced CNC machines can achieve tolerances as tight as a few micrometers.
This level of precision is indispensable for industries that require exact specifications.
The ability to produce identical parts within these tolerances minimizes the risk of defects and enhances overall product quality.
Cost-Efficiency
While precision machining technology can be expensive to set up initially, it proves cost-effective in the long run.
Automated processes reduce the need for manual labor, thereby lowering production costs.
Additionally, the high accuracy of precision machining reduces the likelihood of costly errors and rework.
This is especially important in small-lot production, where the margin for error is minimal.
Flexibility
Precision machining offers a high degree of flexibility, making it ideal for small-lot production.
CNC machines can be easily programmed to execute various tasks, allowing for quick changes to design and production parameters.
This flexibility enables manufacturers to produce custom parts without significant downtime, thereby speeding up the production process.
Material Utilization
Efficient material utilization is another crucial benefit of precision machining.
Advanced machines are designed to minimize waste, ensuring that raw materials are used optimally.
This not only reduces material costs but also aligns with sustainable manufacturing practices.
Types of Precision Machining Technologies
CNC Machining
Computer Numerical Control (CNC) machining is one of the most widely-used precision machining technologies.
CNC machines are operated using pre-programmed software that dictates the movement and operation of the machinery.
They can perform a variety of tasks, including drilling, milling, and turning.
The result is highly accurate and repeatable parts, making CNC machining ideal for small-lot production.
Laser Machining
Laser machining uses focused light beams to cut, engrave, or etch materials.
The precision of laser technology allows for intricate designs and complex geometries that are difficult to achieve with traditional methods.
Laser machining is particularly useful for small components that require high levels of detail and accuracy.
Electrical Discharge Machining (EDM)
EDM involves using electrical sparks to erode material from a workpiece.
This method is highly effective for hard materials that are difficult to machine using traditional techniques.
EDM offers exceptionally high accuracy, making it suitable for producing complex shapes and fine details in small-lot production.
Challenges and Considerations
High Initial Costs
While precision machining offers numerous benefits, it does come with high initial costs.
The machinery and software required for precision machining can be expensive to acquire and maintain.
However, the long-term savings in labor and material costs often justify this initial investment.
Skilled Workforce
Operating advanced precision machining equipment requires a skilled workforce.
Training and retaining qualified personnel can be challenging but is crucial for achieving the desired level of accuracy and efficiency.
Investing in ongoing training programs is essential to keep the workforce updated with the latest technological advancements.
Complex Programming
Creating and managing the programs that run CNC and other precision machines can be complex.
Even small mistakes in the programming code can lead to significant errors in the final product.
Therefore, it is essential to have experienced programmers to ensure the process runs smoothly.
Future Trends in Precision Machining
Automation and AI
The integration of automation and Artificial Intelligence (AI) is set to revolutionize precision machining.
Automation will further reduce the need for manual intervention, while AI can optimize machining processes by analyzing data and making real-time adjustments.
These advancements will make small-lot production even more efficient and cost-effective.
Advanced Materials
The development of advanced materials, such as composites and high-performance alloys, will expand the possibilities for precision machining.
These materials offer superior properties, such as high strength-to-weight ratios, making them ideal for various applications.
Precision machining technologies will continue to evolve to accommodate these advanced materials, opening new avenues for innovation.
IoT Integration
The Internet of Things (IoT) is poised to play a significant role in the future of precision machining.
IoT-enabled machines can communicate with each other and with central monitoring systems, providing real-time data on machine performance and production status.
This connectivity will enhance operational efficiency and enable predictive maintenance, minimizing downtime.
In conclusion, precision machining technology has revolutionized small-lot production by offering high levels of accuracy, cost-efficiency, and flexibility.
Understanding its key benefits, challenges, and future trends can help manufacturers make informed decisions and remain competitive in an ever-evolving market.
As technology continues to advance, the possibilities for precision machining in small-lot production are virtually limitless.
資料ダウンロード
QCD調達購買管理クラウド「newji」は、調達購買部門で必要なQCD管理全てを備えた、現場特化型兼クラウド型の今世紀最高の購買管理システムとなります。
ユーザー登録
調達購買業務の効率化だけでなく、システムを導入することで、コスト削減や製品・資材のステータス可視化のほか、属人化していた購買情報の共有化による内部不正防止や統制にも役立ちます。
NEWJI DX
製造業に特化したデジタルトランスフォーメーション(DX)の実現を目指す請負開発型のコンサルティングサービスです。AI、iPaaS、および先端の技術を駆使して、製造プロセスの効率化、業務効率化、チームワーク強化、コスト削減、品質向上を実現します。このサービスは、製造業の課題を深く理解し、それに対する最適なデジタルソリューションを提供することで、企業が持続的な成長とイノベーションを達成できるようサポートします。
オンライン講座
製造業、主に購買・調達部門にお勤めの方々に向けた情報を配信しております。
新任の方やベテランの方、管理職を対象とした幅広いコンテンツをご用意しております。
お問い合わせ
コストダウンが利益に直結する術だと理解していても、なかなか前に進めることができない状況。そんな時は、newjiのコストダウン自動化機能で大きく利益貢献しよう!
(Β版非公開)