- お役立ち記事
- Best Practices for SMEs to Improve Welding Quality
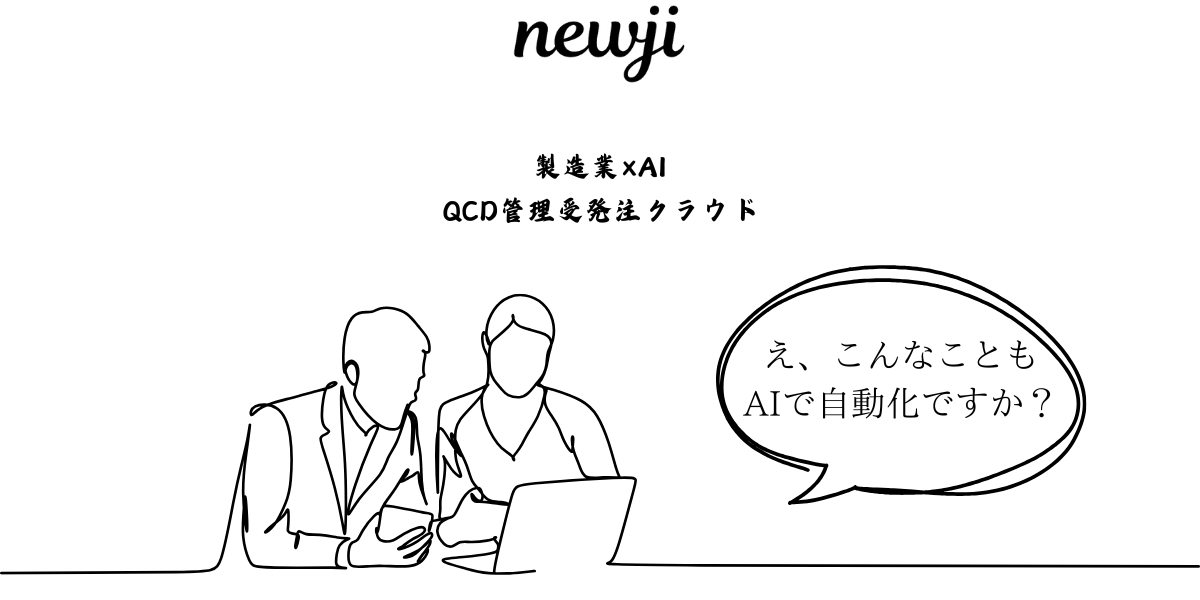
Best Practices for SMEs to Improve Welding Quality
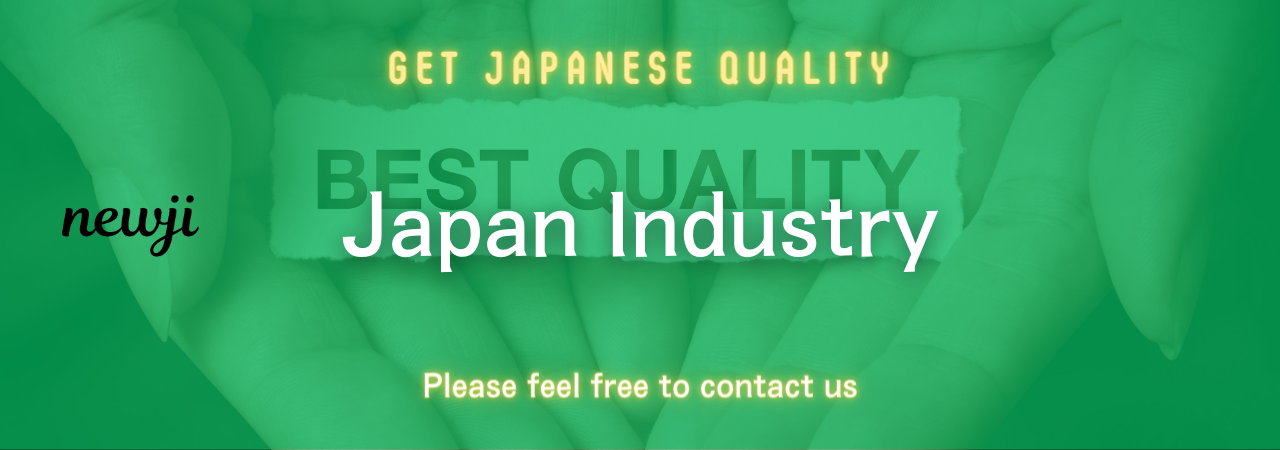
In today’s competitive market, ensuring high welding quality is essential for small and medium-sized enterprises (SMEs). Proper welding practices improve structural integrity and safety and enhance the longevity of your products. This article explores best practices for SMEs to improve welding quality, providing valuable insights and actionable steps to elevate your welding standards.
目次
Understanding Welding Quality
Welding quality refers to the condition of the weld in terms of its strength, appearance, and defect-free nature. High-quality welding ensures robust joints and contributes to the product’s overall durability. Achieving this requires a combination of skilled labor, appropriate materials, and stringent quality control measures.
Invest in Training and Certification
Regular Training Programs
One of the most crucial steps for SMEs to improve welding quality is to invest in regular training programs. Skilled welders are fundamental to producing high-quality welds. Training programs should cover the latest welding techniques, safety protocols, and equipment handling. Regularly updating your workforce’s skills ensures they are capable of performing to the highest standards.
Certification
Encourage your welders to obtain certifications from recognized institutions. Certification programs, such as those offered by the American Welding Society (AWS), provide standard guidelines and validate the skills of your welders. Certified welders are more likely to produce consistent and reliable welds, significantly improving overall weld quality.
Utilize High-Quality Materials
Choosing the Right Filler Materials
The selection of appropriate filler materials is essential for achieving high-quality welds. Depending on the base metals being welded, the filler material must have compatible properties to ensure a strong bond. Consider factors such as tensile strength, corrosion resistance, and thermal expansion when choosing filler materials.
Quality of Base Metals
Using high-quality base metals is just as important as using the correct filler material. Impurities and inconsistencies in base metals can lead to welding defects, compromising the weld’s integrity. Source your base metals from reputable suppliers to ensure consistency and reliability in your welding operations.
Maintain Equipment and Infrastructure
Regular Equipment Maintenance
Well-maintained welding equipment is critical for achieving high-quality welds. Regular maintenance checks and servicing ensure that your machines operate at optimal efficiency. Calibrate your welding machines periodically and replace worn-out parts to prevent any disruptions during the welding process.
Updated Welding Technology
Investing in modern welding technology can drastically improve weld quality. Advanced welding machines offer better control, precision, and versatility over traditional equipment. Technologies such as automated welding systems and advanced welding software can enhance productivity and ensure consistent weld quality.
Implement Stringent Quality Control Measures
Pre-Weld Inspection
Implementing a robust pre-weld inspection process ensures that all materials and equipment are ready for the job. Inspect the base metals for any impurities or defects, verify the specifications of filler materials, and ensure that the welding environment is adequately prepared. Pre-weld inspections prevent potential issues and set the stage for successful welding operations.
Post-Weld Inspection
Post-weld inspections are equally important for maintaining high-quality welds. Inspect welds for any visible defects such as cracks, porosity, or incomplete fusion. Non-destructive testing methods, such as ultrasonic testing and radiographic testing, can be employed to identify hidden defects within the welds. Implementing post-weld inspections helps in identifying issues early and preventing product failures.
Optimize Welding Processes
Standardized Welding Procedures
Standardizing welding procedures is an effective way to improve weld quality. Develop detailed welding procedure specifications (WPS) tailored to your projects. These specifications should outline the necessary parameters, including voltage, amperage, travel speed, and welding position. Enforcing standardized procedures ensures consistency across all welding operations.
Proper Joint Design
Effective joint design plays a crucial role in the success of your welding operations. Poorly designed joints can lead to weak welds and structural failures. To optimize joint design, consider factors such as joint geometry, fit-up, and access for welding. Collaborate with your engineering team to design joints that are conducive to high-quality welding.
Focus on Safety
Protective Gear
Safety should always be a priority in any welding operation. Providing appropriate protective gear, such as welding helmets, gloves, and aprons, is essential to safeguard your workers. Proper safety gear not only protects welders from hazards but also enables them to perform their tasks more effectively.
Safe Working Environment
Creating a safe working environment is vital for maintaining high welding quality. Ensure your welding area is well-ventilated and free from flammable materials. Implement safety protocols and conduct regular safety drills to keep your workforce prepared for emergencies. A safe environment fosters better focus and concentration, leading to higher quality welds.
Conclusion
Improving welding quality is a multifaceted challenge that requires commitment, investment, and continuous improvement. By focusing on training and certification, utilizing high-quality materials, maintaining equipment, implementing strict quality control measures, optimizing welding processes, and prioritizing safety, SMEs can significantly enhance their welding standards. High-quality welds not only ensure the durability and reliability of your products but also contribute to customer satisfaction and business success.
Incorporating these best practices will set your enterprise on the path to achieving exceptional welding quality, resulting in better products and a stronger market position.
資料ダウンロード
QCD調達購買管理クラウド「newji」は、調達購買部門で必要なQCD管理全てを備えた、現場特化型兼クラウド型の今世紀最高の購買管理システムとなります。
ユーザー登録
調達購買業務の効率化だけでなく、システムを導入することで、コスト削減や製品・資材のステータス可視化のほか、属人化していた購買情報の共有化による内部不正防止や統制にも役立ちます。
NEWJI DX
製造業に特化したデジタルトランスフォーメーション(DX)の実現を目指す請負開発型のコンサルティングサービスです。AI、iPaaS、および先端の技術を駆使して、製造プロセスの効率化、業務効率化、チームワーク強化、コスト削減、品質向上を実現します。このサービスは、製造業の課題を深く理解し、それに対する最適なデジタルソリューションを提供することで、企業が持続的な成長とイノベーションを達成できるようサポートします。
オンライン講座
製造業、主に購買・調達部門にお勤めの方々に向けた情報を配信しております。
新任の方やベテランの方、管理職を対象とした幅広いコンテンツをご用意しております。
お問い合わせ
コストダウンが利益に直結する術だと理解していても、なかなか前に進めることができない状況。そんな時は、newjiのコストダウン自動化機能で大きく利益貢献しよう!
(Β版非公開)