- お役立ち記事
- “Revolutionizing Japanese Manufacturing with RFID Devices: The Future of Smart Factories”
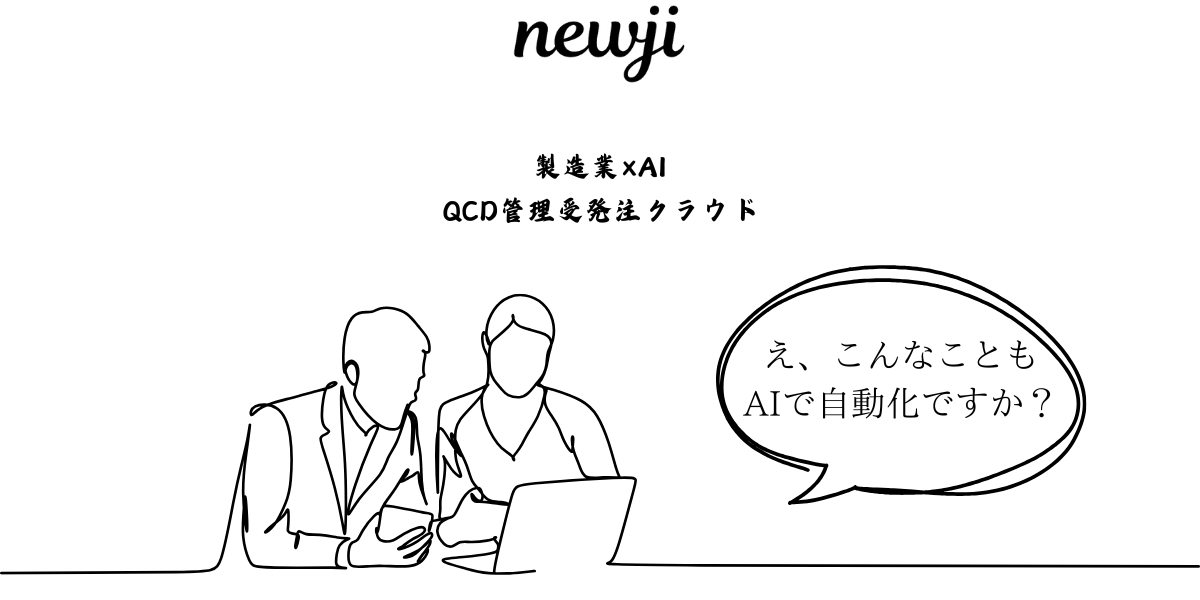
“Revolutionizing Japanese Manufacturing with RFID Devices: The Future of Smart Factories”
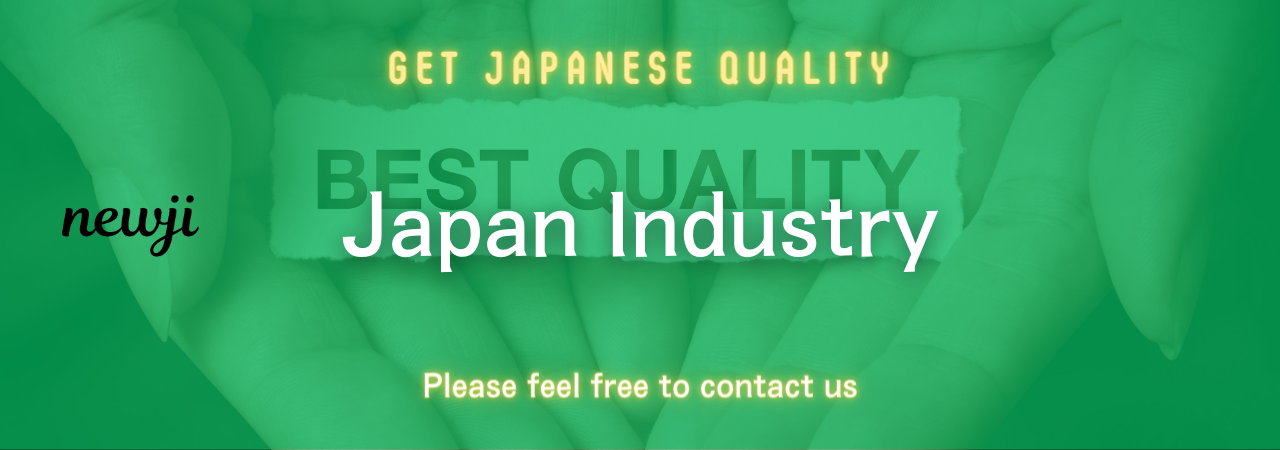
目次
Introduction
The landscape of global manufacturing is rapidly transforming, with technological advancements driving substantial changes.
One pivotal innovation redefining manufacturing dynamics is Radio Frequency Identification (RFID) technology.
In particular, Japanese companies are leveraging RFID devices to create smart factories, optimizing efficiency, improving quality control, and enhancing supply chain visibility.
This article delves into how RFID technology is revolutionizing Japanese manufacturing, creating smart factories for the future, and offers insights into best practices, procurement strategies, and market conditions.
Understanding RFID and Its Importance
RFID technology uses electromagnetic fields to automatically identify and track tags attached to objects.
These tags contain electronically stored information that can be read from several meters away, eliminating the need for direct line-of-sight scanning, unlike barcodes.
RFID enables real-time data acquisition, providing an unprecedented level of visibility and control over manufacturing processes.
Advantages of RFID in Manufacturing
One of the most significant benefits of RFID in manufacturing is the ability to track inventory and assets in real-time.
This leads to improved accuracy in inventory management, reduced labor costs, and minimized human error.
Furthermore, RFID enhances traceability, essential for quality control and regulatory compliance.
RFID also streamlines production processes.
With real-time tracking, manufacturers can monitor the movement of raw materials and components through the production line.
This reduces bottlenecks, shortens cycle times, and optimizes resource utilization.
Another advantage is enhancing automation.
RFID technology seamlessly integrates with automated systems, creating truly smart factories where machines and systems communicate and operate autonomously.
This results in significant improvements in factory efficiency and productivity.
Challenges and Disadvantages
Despite its numerous advantages, adopting RFID technology in manufacturing is not without challenges.
One major obstacle is the initial cost of implementation.
RFID tags, readers, and the required infrastructure can be expensive, posing a financial barrier for smaller manufacturers.
Another challenge is the potential for signal interference and data security concerns.
RFID systems may face issues such as interference from metal objects or other electronic devices, which can impair performance.
Additionally, the data transmitted via RFID is susceptible to unauthorized access and tampering, necessitating robust security measures.
Finally, integrating RFID technology with existing systems and processes can be complex and require significant effort, potentially disrupting ongoing operations.
Best Practices for Implementing RFID in Japanese Manufacturing
Japanese manufacturing companies are renowned for their meticulous attention to detail and quality.
To successfully implement RFID technology and realize its full potential, adhering to best practices is crucial.
Comprehensive Planning and Assessment
Before implementing RFID, conduct a thorough assessment of current processes and identify areas where RFID can provide the most significant benefits.
Engage stakeholders from various departments, including procurement, production, and IT, to ensure a holistic approach.
Pilot Testing
Start with a pilot project to test the feasibility and effectiveness of RFID in your manufacturing environment.
Choose a specific area or process to implement RFID on a small scale, monitor performance, and gather data.
Use insights from the pilot to refine your strategy before full-scale deployment.
Custom Solutions
Every manufacturing operation is unique.
Customized RFID solutions, tailored to your specific requirements, will yield the best results.
Work closely with RFID suppliers to design and implement a system that aligns with your operational needs and goals.
Training and Change Management
Proper training is essential to ensure that employees understand how to use RFID technology effectively.
Invest in comprehensive training programs and develop a change management strategy to facilitate a smooth transition.
Address any resistance to change and highlight the benefits of RFID to gain employee buy-in.
Supplier Negotiation Techniques for RFID Devices
When procuring RFID devices from Japanese suppliers, effective negotiation techniques are crucial to securing the best deals and ensuring successful implementation.
Research and Selection
Conduct thorough research to identify reputable RFID suppliers in Japan.
Assess their track record, technological expertise, and customer reviews.
Shortlist suppliers with a proven history of successful implementations in similar industries.
Clear Specifications
Clearly define your requirements, including the type of RFID tags and readers, data management software, and support services.
Provide detailed specifications to suppliers to ensure they understand your needs and can offer the most suitable solutions.
Quality and Reliability
Japanese manufacturers are renowned for their high-quality products.
Emphasize the importance of quality and reliability during negotiations.
Request samples and conduct rigorous testing to ensure the RFID devices meet your standards.
Price and Payment Terms
While cost is an important consideration, it should not be the sole factor.
Negotiate a fair price that reflects the quality and reliability of the RFID devices.
Explore flexible payment terms to manage cash flow effectively.
Long-Term Partnership
Build a long-term partnership with your RFID supplier.
A collaborative relationship fosters mutual understanding and facilitates continuous improvement and support.
Negotiate service agreements that cover maintenance, software updates, and ongoing technical support.
Market Conditions in Japan for RFID Technology
The Japanese market for RFID technology is dynamic and evolving.
Numerous factors influence market conditions, including technological advancements, regulatory changes, and economic trends.
Technological Advancements
Japan is at the forefront of technological innovation.
Continuous advancements in RFID technology, such as improved tag durability, increased read distances, and enhanced data security, drive market growth.
Manufacturers are keen to adopt the latest RFID solutions to stay competitive.
Regulatory Environment
The Japanese government supports the adoption of advanced technologies in manufacturing.
Policies and initiatives aim to promote smart factories and Industry 4.0.
Compliance with regulatory standards is essential for manufacturers and RFID suppliers, ensuring safety and reliability.
Economic Trends
Japan’s economy significantly impacts the RFID market.
Economic stability and growth foster increased investments in manufacturing technology.
Conversely, economic downturns may lead to budget constraints and reduced spending on new technologies.
The Future of Smart Factories in Japan
The integration of RFID technology is a cornerstone of smart factories.
In Japan, the future of smart factories is promising, characterized by increased automation, enhanced connectivity, and data-driven decision-making.
Increased Automation
RFID technology enables greater automation by providing real-time data and facilitating machine-to-machine communication.
Automated systems can optimize production schedules, reduce downtime, and enhance overall efficiency.
Enhanced Connectivity
Smart factories rely on the seamless integration of various technologies.
RFID devices connect with the Internet of Things (IoT) and other digital systems, creating an interconnected ecosystem.
This connectivity enables manufacturers to monitor and control production processes remotely.
Data-Driven Decision Making
The real-time data generated by RFID devices provides valuable insights into production performance, inventory levels, and supply chain dynamics.
Manufacturers can use this data to make informed decisions, improve processes, and respond swiftly to market changes.
Customized Production
Smart factories equipped with RFID technology can achieve customized production efficiently.
Real-time data allows for dynamic adjustments in production lines, accommodating varying customer demands and reducing lead times.
Conclusion
RFID technology is revolutionizing Japanese manufacturing, paving the way for smart factories of the future.
By enhancing visibility, improving efficiency, and enabling automation, RFID devices offer significant benefits.
However, successful implementation requires comprehensive planning, careful supplier selection, and adherence to best practices.
As the Japanese market for RFID technology continues to evolve, manufacturers must stay abreast of technological advancements, regulatory changes, and economic trends.
By embracing RFID and other cutting-edge technologies, Japan’s manufacturing sector can maintain its global competitiveness and continue to deliver high-quality products.
Incorporating RFID into your manufacturing process is not just an investment in technology; it is an investment in the future.
The journey towards becoming a smart factory, though challenging, promises substantial returns in efficiency, quality, and profitability.
Japanese manufacturers, with their emphasis on quality and innovation, are well-positioned to lead this revolution and set new benchmarks in the industry.
資料ダウンロード
QCD調達購買管理クラウド「newji」は、調達購買部門で必要なQCD管理全てを備えた、現場特化型兼クラウド型の今世紀最高の購買管理システムとなります。
ユーザー登録
調達購買業務の効率化だけでなく、システムを導入することで、コスト削減や製品・資材のステータス可視化のほか、属人化していた購買情報の共有化による内部不正防止や統制にも役立ちます。
NEWJI DX
製造業に特化したデジタルトランスフォーメーション(DX)の実現を目指す請負開発型のコンサルティングサービスです。AI、iPaaS、および先端の技術を駆使して、製造プロセスの効率化、業務効率化、チームワーク強化、コスト削減、品質向上を実現します。このサービスは、製造業の課題を深く理解し、それに対する最適なデジタルソリューションを提供することで、企業が持続的な成長とイノベーションを達成できるようサポートします。
オンライン講座
製造業、主に購買・調達部門にお勤めの方々に向けた情報を配信しております。
新任の方やベテランの方、管理職を対象とした幅広いコンテンツをご用意しております。
お問い合わせ
コストダウンが利益に直結する術だと理解していても、なかなか前に進めることができない状況。そんな時は、newjiのコストダウン自動化機能で大きく利益貢献しよう!
(Β版非公開)