- お役立ち記事
- Initiatives by Quality Assurance Departments to Prevent Defective Products in Manufacturing
Initiatives by Quality Assurance Departments to Prevent Defective Products in Manufacturing
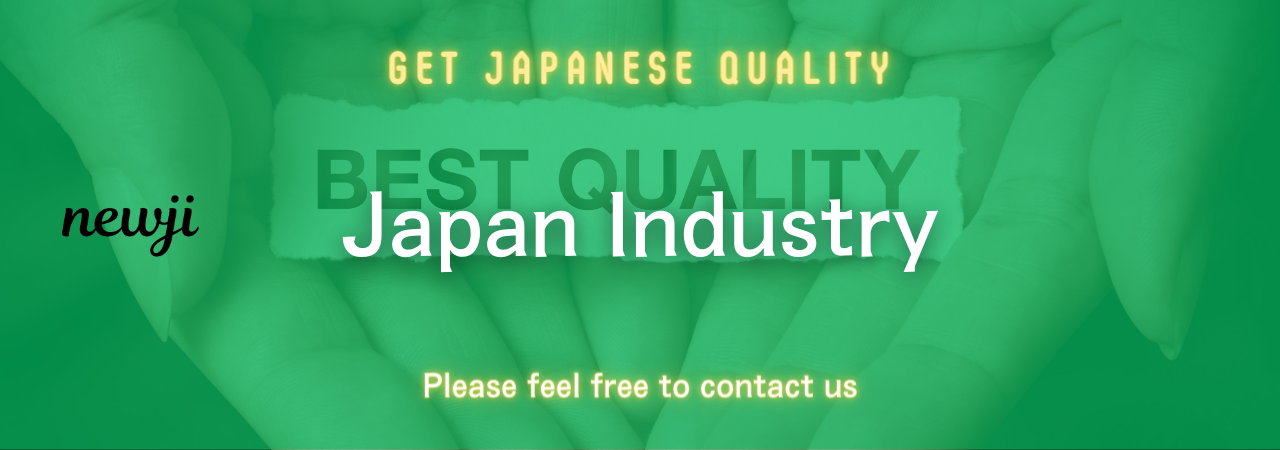
In the world of manufacturing, ensuring that products are of high quality and free from defects is a top priority.
Quality assurance (QA) departments play a crucial role in making sure that everything produced meets strict standards.
But how do these departments go about preventing defective products?
Let’s explore several key initiatives that QA departments undertake to maintain product quality and reliability.
目次
Understanding the Role of Quality Assurance
What is Quality Assurance?
Quality assurance is a process-focused approach to ensuring that a company’s products meet the set quality standards.
It includes the systematic monitoring and evaluation of various aspects of a project, service, or facility to maximize the probability of defect-free outputs.
QA is proactive, aiming to prevent problems before they occur.
Why is QA Important?
QA is essential for maintaining customer satisfaction and loyalty.
Defective products can lead to returns, complaints, and even loss of business.
By implementing thorough QA processes, companies can build trust with their customers, minimize waste, and increase efficiency.
Key Initiatives by Quality Assurance Departments
Establishing Standards and Guidelines
One of the first steps QA departments take is to establish clear quality standards and guidelines.
These are based on industry norms, customer requirements, and regulatory conditions.
Having well-defined standards helps to ensure consistency and clarity in production.
Everyone involved in the manufacturing process knows what is expected and strives to meet those expectations.
Implementing Rigorous Testing Protocols
QA departments often implement rigorous testing protocols to identify potential issues in the production process.
These tests can include stress tests, functionality tests, and performance tests.
By testing products under various conditions, QA teams can identify weaknesses or potential failure points.
Regular testing helps catch defects early, preventing defective products from reaching customers.
Conducting Quality Audits
Regular quality audits are another crucial initiative.
These audits involve systematically reviewing all processes, materials, and products to ensure they meet established quality standards.
Audits can be internal or conducted by external bodies.
They provide an objective assessment of the quality control measures in place, highlighting areas that need improvement.
Employee Training and Development
Employees must be well-trained and knowledgeable about quality standards and procedures.
QA departments often hold regular training sessions and workshops to keep staff updated on the latest quality control techniques and standards.
Continuous training helps employees understand the importance of quality assurance and equips them with the skills necessary to identify and address potential issues.
Using Technology for Quality Assurance
Automated Inspection Systems
Modern manufacturing heavily relies on technology to enhance quality assurance.
Automated inspection systems, such as machine vision, use cameras and computer algorithms to inspect products quickly and accurately.
These systems can detect flaws that might be missed by the human eye, ensuring a higher level of precision in quality control.
Data Analytics and Predictive Maintenance
Data analytics is becoming a critical tool in quality assurance.
By collecting and analyzing data from various stages of production, QA departments can identify patterns and trends that may indicate potential quality issues.
Predictive maintenance uses this data to forecast when equipment might fail, allowing for preemptive maintenance and reducing the likelihood of defective products.
Real-Time Monitoring Systems
Implementing real-time monitoring systems allows for continuous observation of the manufacturing process.
These systems can provide instantaneous feedback and alerts if any deviation from the set standards occurs.
By catching issues in real-time, QA teams can address them immediately, preventing defects from developing further down the line.
The Continuous Improvement Cycle
Implementing the PDCA Cycle
Quality assurance is not a one-time effort but a continuous process.
The Plan-Do-Check-Act (PDCA) cycle is a widely adopted methodology for continuous improvement.
In the planning phase, QA teams identify potential areas for improvement and develop strategies.
During the doing phase, these strategies are implemented.
The checking phase involves evaluating the effectiveness of the implemented strategies.
Finally, in the acting phase, successful strategies are standardized, and unsuccessful ones are revised.
Encouraging a Culture of Quality
Building a culture of quality within the organization is vital.
When every employee, from management to the production floor, values quality and takes responsibility for it, the overall standard of production improves.
QA departments often lead by example, displaying a commitment to quality that motivates the entire workforce.
Challenges and Solutions in Quality Assurance
Overcoming Resistance to Change
One of the challenges in implementing quality assurance initiatives is resistance to change.
Employees may be accustomed to certain processes and hesitate to adopt new methods.
QA departments can overcome this by communicating the benefits of the new initiatives clearly and providing adequate training and support.
Managing Costs
Implementing QA initiatives often involves costs, which can be a concern for companies.
However, the long-term benefits of reducing defects, enhancing customer satisfaction, and minimizing waste often outweigh the initial investment.
Cost management can include prioritizing initiatives that offer the highest return on investment and seeking funding or support from stakeholders.
Ensuring Compliance
Meeting regulatory and industry standards is critical, especially in sectors like pharmaceuticals, automotive, and electronics.
QA departments must stay updated on changing regulations and ensure that all processes comply.
Non-compliance can lead to legal issues, fines, and reputational damage.
Preventing defective products in manufacturing is a multifaceted effort involving meticulous planning, advanced technology, and a culture of quality.
Quality assurance departments are at the forefront of these efforts, driving initiatives that ensure every product meets the highest standards.
Through continuous improvement, rigorous testing, and a commitment to excellence, QA departments help build trust with customers and uphold the company’s reputation for quality.
資料ダウンロード
QCD調達購買管理クラウド「newji」は、調達購買部門で必要なQCD管理全てを備えた、現場特化型兼クラウド型の今世紀最高の購買管理システムとなります。
ユーザー登録
調達購買業務の効率化だけでなく、システムを導入することで、コスト削減や製品・資材のステータス可視化のほか、属人化していた購買情報の共有化による内部不正防止や統制にも役立ちます。
NEWJI DX
製造業に特化したデジタルトランスフォーメーション(DX)の実現を目指す請負開発型のコンサルティングサービスです。AI、iPaaS、および先端の技術を駆使して、製造プロセスの効率化、業務効率化、チームワーク強化、コスト削減、品質向上を実現します。このサービスは、製造業の課題を深く理解し、それに対する最適なデジタルソリューションを提供することで、企業が持続的な成長とイノベーションを達成できるようサポートします。
オンライン講座
製造業、主に購買・調達部門にお勤めの方々に向けた情報を配信しております。
新任の方やベテランの方、管理職を対象とした幅広いコンテンツをご用意しております。
お問い合わせ
コストダウンが利益に直結する術だと理解していても、なかなか前に進めることができない状況。そんな時は、newjiのコストダウン自動化機能で大きく利益貢献しよう!
(Β版非公開)