- お役立ち記事
- Process Improvement Strategies for Differentiation in Injection Molding
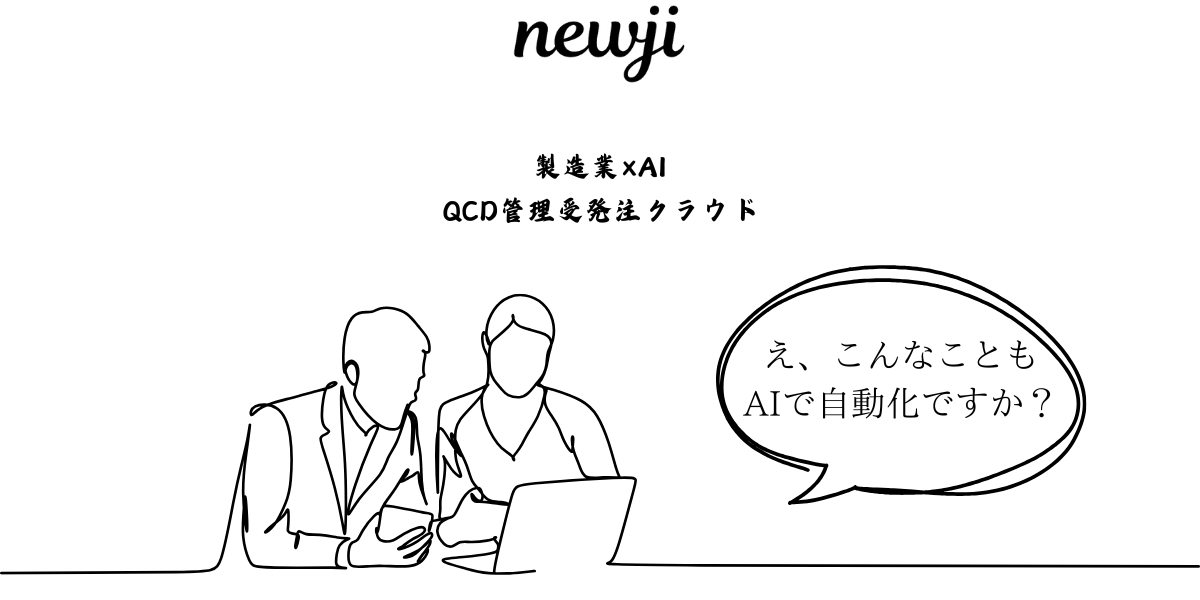
Process Improvement Strategies for Differentiation in Injection Molding
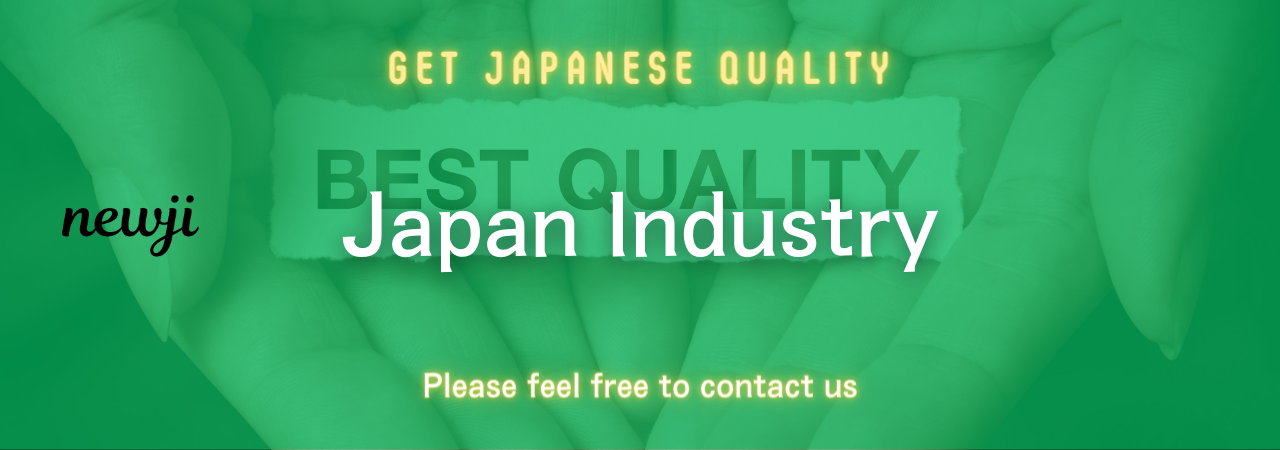
Injection molding is a manufacturing process that allows for the mass production of plastic parts by injecting molten plastic material into a mold.
In today’s competitive market, it’s crucial for companies to distinguish themselves through effective process improvement strategies.
Using advanced techniques and innovative methods, companies can ensure high-quality products, reduce costs, and stay ahead of their competitors.
目次
Understanding Injection Molding
Injection molding is a highly efficient and versatile manufacturing method used to produce a wide range of plastic products.
The process begins with the heating of plastic pellets until they melt.
This molten plastic is then injected into a mold, where it cools and solidifies into the desired shape.
The mold can be customized to produce parts of varying complexity and size, making injection molding suitable for diverse applications, from automotive components to consumer goods.
Importance of Process Improvement
To maintain a competitive edge, manufacturers must continuously seek ways to improve their injection molding processes.
Process improvement leads to several benefits, including increased efficiency, reduced waste, lower production costs, and better product quality.
Additionally, consistent improvements can help companies respond more quickly to market demands and adapt to new technologies.
Reducing Cycle Time
Cycle time is the amount of time it takes to complete one injection molding process cycle, from the injection of molten plastic to the ejection of the finished part.
Reducing cycle time is a primary goal for process improvement, as shorter cycles increase production rates and reduce manufacturing costs.
To achieve this, manufacturers can optimize various parameters, such as injection speed, cooling time, and material flow.
Enhancing Material Efficiency
Material efficiency is another crucial aspect of process improvement.
By selecting high-quality, durable materials and using them efficiently, manufacturers can minimize waste and lower costs.
Implementing techniques such as regrinding and reusing scrap materials can further enhance material efficiency.
Additionally, advancements in material science, like the development of new polymers and composites, offer opportunities for improved performance and sustainability.
Implementing Advanced Technologies
The integration of advanced technologies in injection molding offers numerous possibilities for process improvement.
These technologies enable manufacturers to achieve higher precision, better control, and more consistent quality.
Automation and Robotics
Automation and robotics play a significant role in modern injection molding.
Automated systems can perform repetitive tasks with high accuracy and speed, reducing the need for manual labor and minimizing the risk of human error.
Robots can handle tasks such as part removal, quality inspection, and assembly, leading to more efficient and consistent production processes.
By integrating automation, manufacturers can also free up human workers to focus on more complex and value-added activities.
Use of Simulation Software
Simulation software allows manufacturers to model and analyze the injection molding process before actual production begins.
By simulating the flow of molten plastic, cooling patterns, and potential defects, manufacturers can identify and address issues early in the design phase.
This proactive approach reduces the need for costly trial-and-error adjustments during production.
Simulation software also helps optimize mold designs and process parameters, ensuring the best possible outcomes.
Industry 4.0 and IoT
Industry 4.0 refers to the fourth industrial revolution, characterized by the integration of digital technologies into manufacturing.
In the context of injection molding, Industry 4.0 technologies such as the Internet of Things (IoT) enable real-time monitoring and data collection.
Sensors integrated into machines can provide valuable insights into the performance of the injection molding process, allowing for predictive maintenance and instant troubleshooting.
By leveraging IoT, manufacturers can enhance efficiency, minimize downtime, and ensure consistent product quality.
Quality Control and Assurance
Ensuring consistent quality is paramount for manufacturers aiming to differentiate themselves in the market.
Implementing robust quality control and assurance measures helps maintain high standards and build customer trust.
Statistical Process Control (SPC)
Statistical Process Control (SPC) involves monitoring and controlling the injection molding process using statistical methods.
By collecting and analyzing data from production runs, manufacturers can identify trends, detect variations, and implement corrective actions promptly.
SPC helps in maintaining process stability, reducing defects, and improving overall product quality.
Regular Maintenance of Equipment
Equipment maintenance is crucial for ensuring the longevity and optimal performance of injection molding machines.
Regularly scheduled maintenance, including cleaning, lubrication, and inspection, helps prevent unexpected breakdowns and ensures consistent operation.
Implementing a preventive maintenance program can reduce downtime, lower repair costs, and enhance the reliability of the manufacturing process.
Employee Training and Development
The success of process improvement strategies heavily relies on the skills and knowledge of the workforce.
Investing in employee training and development is essential for fostering a culture of continuous improvement.
Skills Enhancement
Providing ongoing training programs for employees helps them stay up-to-date with the latest industry trends, technologies, and best practices.
Training sessions can cover various aspects of injection molding, such as machine operation, mold design, troubleshooting, and quality control.
Enhancing employees’ skills not only improves process efficiency but also empowers workers to contribute to innovation and problem-solving.
Encouraging Collaboration
Fostering a collaborative work environment encourages employees to share ideas, insights, and best practices.
Cross-functional teams can work together to identify process inefficiencies, brainstorm solutions, and implement improvements.
By encouraging open communication and knowledge-sharing, manufacturers can harness the collective expertise of their workforce.
Conclusion
Process improvement strategies are vital for achieving differentiation in injection molding.
By focusing on reducing cycle time, enhancing material efficiency, implementing advanced technologies, and ensuring robust quality control, manufacturers can produce high-quality products more efficiently and cost-effectively.
Investing in employee training and fostering a collaborative work environment further supports continuous improvement.
With these strategies in place, companies can stay ahead of the competition and meet the evolving demands of the market.
資料ダウンロード
QCD調達購買管理クラウド「newji」は、調達購買部門で必要なQCD管理全てを備えた、現場特化型兼クラウド型の今世紀最高の購買管理システムとなります。
ユーザー登録
調達購買業務の効率化だけでなく、システムを導入することで、コスト削減や製品・資材のステータス可視化のほか、属人化していた購買情報の共有化による内部不正防止や統制にも役立ちます。
NEWJI DX
製造業に特化したデジタルトランスフォーメーション(DX)の実現を目指す請負開発型のコンサルティングサービスです。AI、iPaaS、および先端の技術を駆使して、製造プロセスの効率化、業務効率化、チームワーク強化、コスト削減、品質向上を実現します。このサービスは、製造業の課題を深く理解し、それに対する最適なデジタルソリューションを提供することで、企業が持続的な成長とイノベーションを達成できるようサポートします。
オンライン講座
製造業、主に購買・調達部門にお勤めの方々に向けた情報を配信しております。
新任の方やベテランの方、管理職を対象とした幅広いコンテンツをご用意しております。
お問い合わせ
コストダウンが利益に直結する術だと理解していても、なかなか前に進めることができない状況。そんな時は、newjiのコストダウン自動化機能で大きく利益貢献しよう!
(Β版非公開)