- お役立ち記事
- Improving Efficiency in Press Processing Through Feeder System Optimization
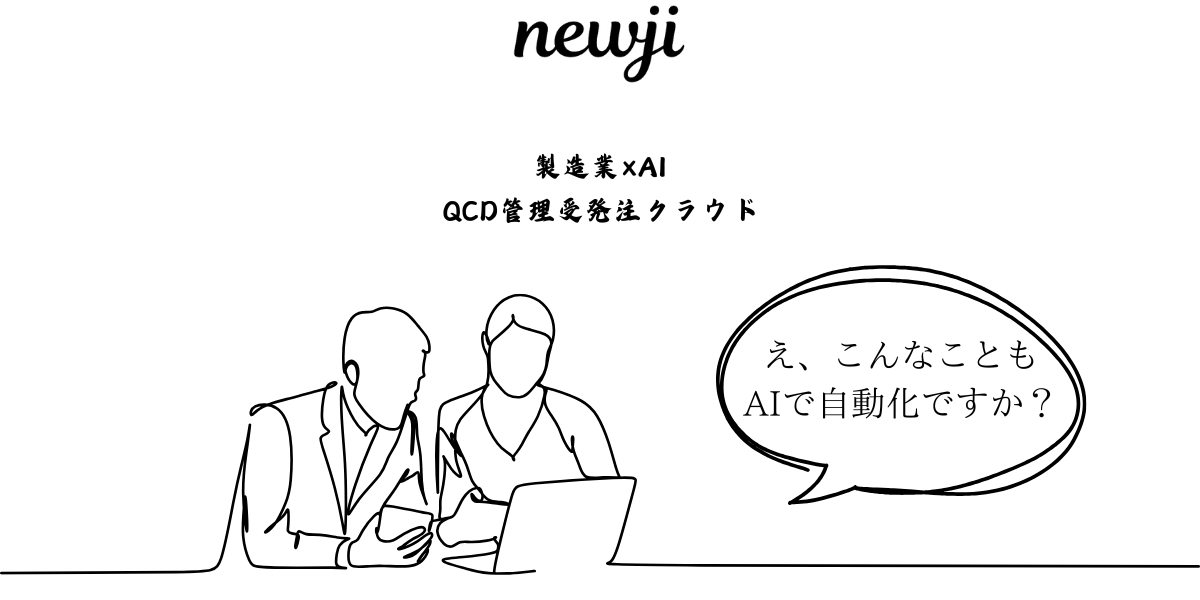
Improving Efficiency in Press Processing Through Feeder System Optimization
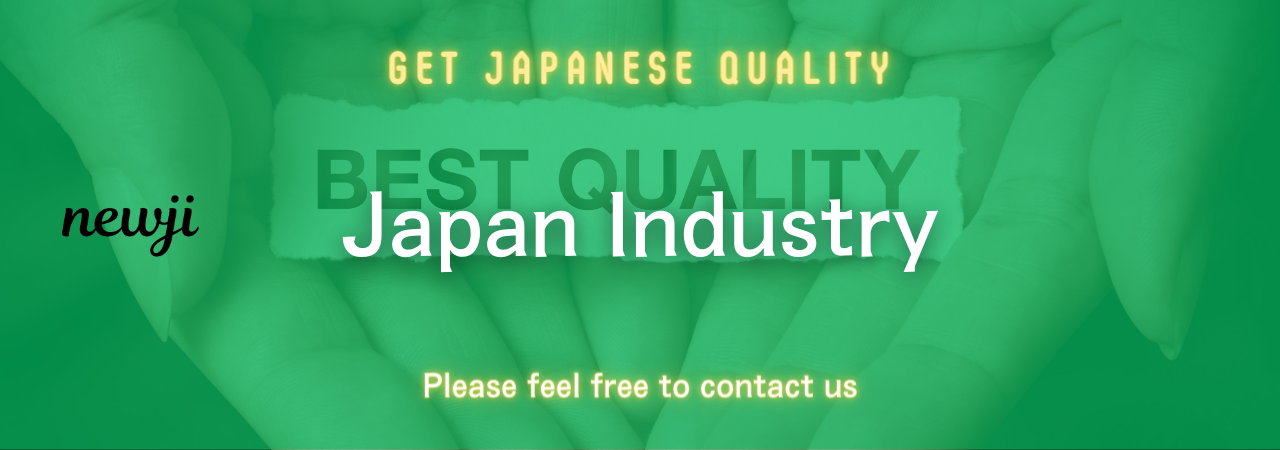
In the world of manufacturing, efficiency is king.
When it comes to press processing, nothing can accelerate productivity quite like the optimization of your feeder system.
Feeder systems ensure that materials are correctly positioned for pressing, a critical step in achieving high-quality results and maximizing throughput.
Let’s delve into how optimizing these systems can lead to remarkable improvements in press processing efficiency.
目次
Understanding Feeder Systems in Press Processing
Feeder systems are the lifelines of press machines.
They transport materials to the press and position them accurately, ensuring consistent and quality products.
The higher the efficiency of this function, the better the performance of the entire press processing line.
Several types of feeder systems exist, including mechanical feeders, servo feeders, and pneumatic feeders, each with its own set of advantages.
Types of Feeder Systems
Mechanical feeders use a combination of mechanical components to control the feeding process.
They are reliable and often found in many standard applications.
Servo feeders, on the other hand, use servo motors for precise control, making them ideal for high-speed operations requiring exactness.
Lastly, pneumatic feeders utilize air pressure to move materials.
They are simpler but less precise compared to servo feeders.
The Role of Feeder System Optimization
Optimization involves fine-tuning and upgrading the feeder systems to enhance their performance.
This can be achieved through a variety of methods, such as improving speed, accuracy, and reliability.
Effective optimization minimizes downtime, reduces errors, and increases the overall throughput of the press processing line.
Benefits of Feeder System Optimization
1. **Increased Speed:** Optimized feeders can handle materials faster, reducing the cycle time.
2. **Enhanced Accuracy:** Improved precision in material positioning leads to higher quality and less wastage.
3. **Reduced Downtime:** Efficient feeders are less likely to experience breakdowns, ensuring continuous operation.
4. **Better Consistency:** Consistent material feeding means fewer errors and uniform product quality.
5. **Cost Savings:** By reducing waste and downtime, optimized feeder systems can lead to significant cost savings.
Strategies for Optimizing Feeder Systems
Several strategies can be employed to optimize feeder systems for press processing.
Let’s explore some of the most effective techniques.
Regular Maintenance and Upkeep
Regular maintenance is crucial for ensuring that feeder systems perform at their best.
This includes cleaning, lubrication, and inspecting parts for wear and tear.
Preventive maintenance can help identify and address potential issues before they escalate into major problems.
Upgrading to Advanced Feeder Systems
Sometimes, the best way to optimize is to upgrade.
Switching to advanced feeder systems like servo feeders can greatly enhance performance.
These feeders offer better control and precision, making them suitable for high-speed operations.
Implementing Automation
Automation can play a significant role in optimizing feeder systems.
Automated feeders can be programmed to handle multiple tasks, reducing the need for manual intervention.
This not only increases efficiency but also reduces the likelihood of human errors.
Using High-Quality Materials
The materials used in feeder systems can impact their durability and performance.
Using high-quality, wear-resistant materials can extend the lifespan of feeder components, reducing the frequency of replacements and downtime.
Training and Skill Development
Optimizing feeder systems isn’t just about the machines; it’s also about the people operating them.
Investing in training and skill development can ensure that operators are well-versed in best practices, leading to more efficient and accurate operations.
Case Study: Successful Feeder System Optimization
Let’s consider a real-world example of a manufacturing company that optimized its feeder systems to improve press processing efficiency.
A mid-sized automotive parts manufacturer was facing issues with inconsistent product quality and frequent downtime.
After conducting a thorough analysis, the company decided to upgrade from mechanical feeders to servo feeders.
They also implemented a preventive maintenance schedule and trained their operators on the new system.
The results were impressive.
The company saw a 20% increase in throughput, a 15% reduction in waste, and a significant decrease in downtime.
The investment in optimizing their feeder systems paid off with improved product quality and overall efficiency.
Conclusion
Optimizing feeder systems for press processing is not just about making adjustments.
It’s a comprehensive approach that includes upgrading technology, maintaining equipment, using quality materials, and training personnel.
The benefits of such optimization are manifold, from increased speed and accuracy to reduced downtime and cost savings.
By focusing on these critical aspects, manufacturers can achieve significant improvements in efficiency and productivity.
資料ダウンロード
QCD調達購買管理クラウド「newji」は、調達購買部門で必要なQCD管理全てを備えた、現場特化型兼クラウド型の今世紀最高の購買管理システムとなります。
ユーザー登録
調達購買業務の効率化だけでなく、システムを導入することで、コスト削減や製品・資材のステータス可視化のほか、属人化していた購買情報の共有化による内部不正防止や統制にも役立ちます。
NEWJI DX
製造業に特化したデジタルトランスフォーメーション(DX)の実現を目指す請負開発型のコンサルティングサービスです。AI、iPaaS、および先端の技術を駆使して、製造プロセスの効率化、業務効率化、チームワーク強化、コスト削減、品質向上を実現します。このサービスは、製造業の課題を深く理解し、それに対する最適なデジタルソリューションを提供することで、企業が持続的な成長とイノベーションを達成できるようサポートします。
オンライン講座
製造業、主に購買・調達部門にお勤めの方々に向けた情報を配信しております。
新任の方やベテランの方、管理職を対象とした幅広いコンテンツをご用意しております。
お問い合わせ
コストダウンが利益に直結する術だと理解していても、なかなか前に進めることができない状況。そんな時は、newjiのコストダウン自動化機能で大きく利益貢献しよう!
(Β版非公開)